Made from natural elements - clay, fire, air, and human hands - the ceramic process is unpredictable.
"When all of these factors become one process, and each step is naturally difficult to control, the individuality of each product becomes visible. This is the most special thing about handmade ceramics," said Thai artist Jirawong Wongtrangan of InClay Studio.
Despite these challenges, Jirawong successfully makes one-of-a-kind bowls and cups in his Chiang Mai studio using his even-handed skill, patience, and creativity.
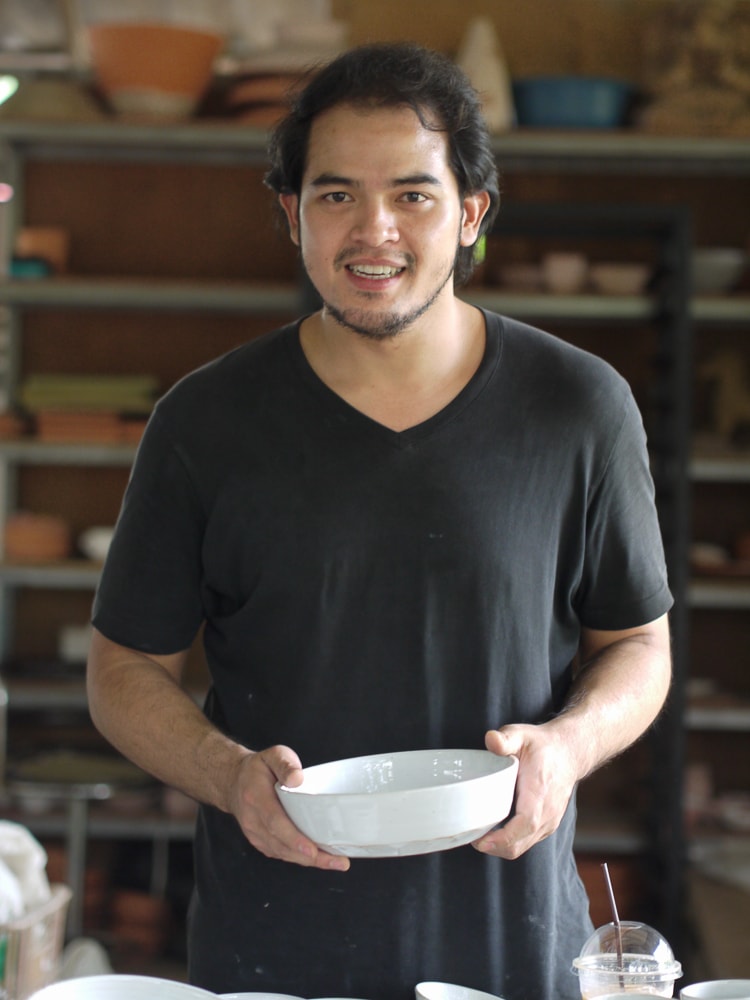
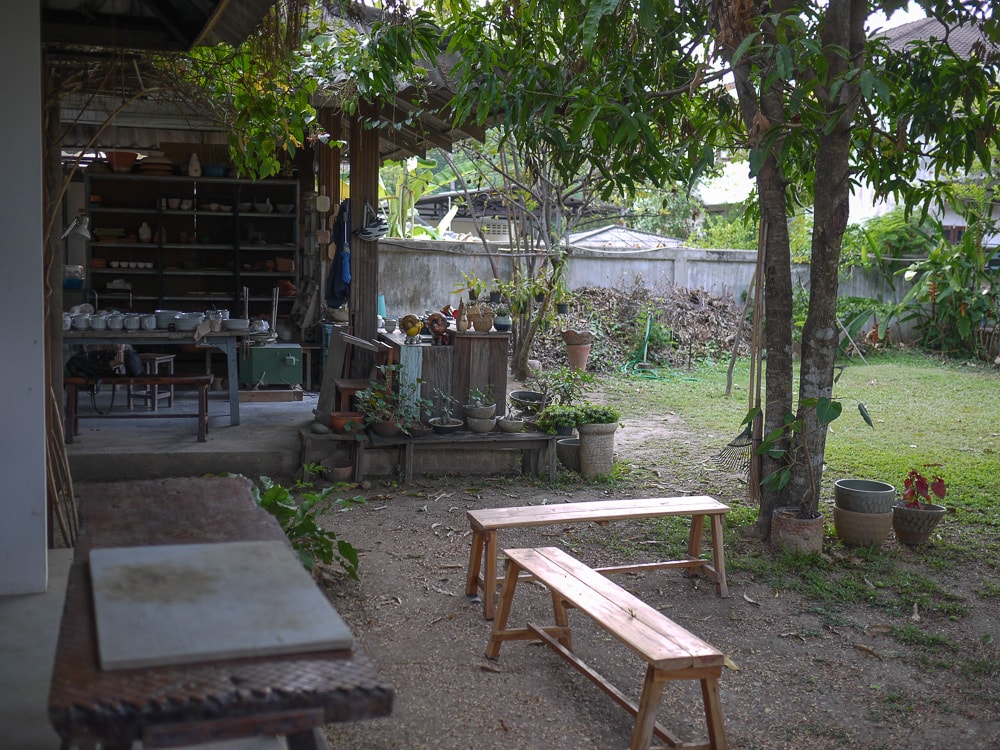
I first visited InClay's open-air workspace situated in the garden of Jirawong's family home near Chiang Mai's Wat Suan Dok Buddhist temple in 2013. The studio is located in a central section of the city, yet I arrived in a round-about way with the driver of a red truck taxi unique to Chiang Mai. I was later warmly greeted in Jirawong's gentle manner near the gate of his house. Before long, I became a weekly regular at InClay where pet chickens and roosters roam and peck at the tropical grounds. Artist friends of Jirawong's drop by and have a snack, play the guitar, and work on ceramic projects.
Two years after our initial meeting, Jirawong and I created a minimalist milk-white collection of handmade ceramics for THE KINDCRAFT x InClay Collaboration. Read below to see the making process behind our collaboration and learn about Jirawong's Northern Thai culture and his inspiration.
Tradition & Inspiration
While ceramics are a traditional art in Jirawong's culture, his functional pottery is more contemporary than the pieces the region is known for:
"In Chiang Mai, Chiang Rai, and Lampang, there are several kinds of traditional arts that are popular; textiles, silver-work, and ceramics which we call sa-kul- chang," he said, referring to heritage crafts that are passed from generation to generation. "Here in the Northern region, people feel more calm than other areas. And there is cooler weather and a nice environment. People are living simply, far from the modern city."
A graduate of Chiang Mai University who worked in a ceramics factory before opening InClay Studio Pottery in 2010, Jirawong's modern style is based around repetition of patterns found in nature: "Like leaves, textile motifs, stones, and dots," he said, "My inspiration is from everything around me. I’m focused on processes and throwing techniques more than on conceptual design."
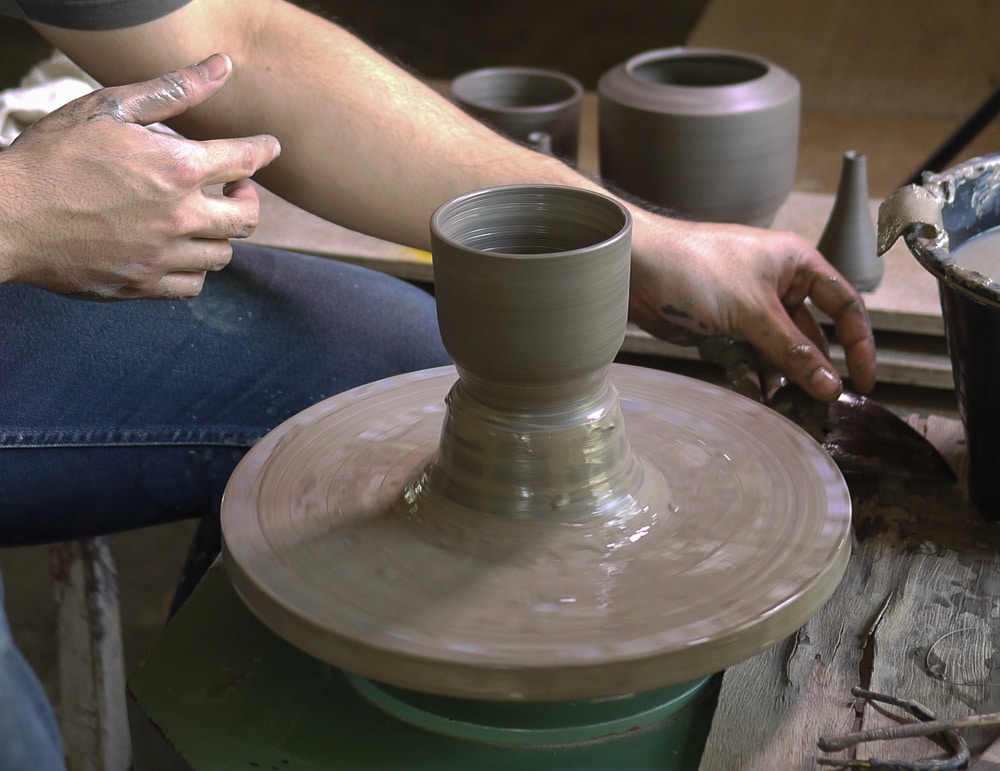
The Process: The Pottery Wheel
For Jirawong, the ceramic process begins with sourcing quality clay in Chiang Mai and the surrounding area. Once he has the clay in hand, he filters out small rocks and sand, then he submerges it in the water. After a month-long soak, the clay is the right texture for wheel-throwing.
He wedges the clay in rhythmic kneading motions before sitting down to his motorized pottery wheel. Expertly centering the clay, dipping his hands in and out of a water bucket, he works the clay up and down before he sinks his thumb into the middle creating an opening. Slowly, he pulls the clay up along the sides as the piece begins to takes shape.
"The thickness of the cup or bowl should be the same from top to bottom. If the bottom is thicker than the top, the piece will feel heavy. This is the good thing about my work - they are balanced. That’s why my ceramics are lighter than others," Jirawong said.
Once he's happy with the shape, he slices it off of the clay mound centered on the wheel and moves the finished piece to a wood board to dry for a day or two.
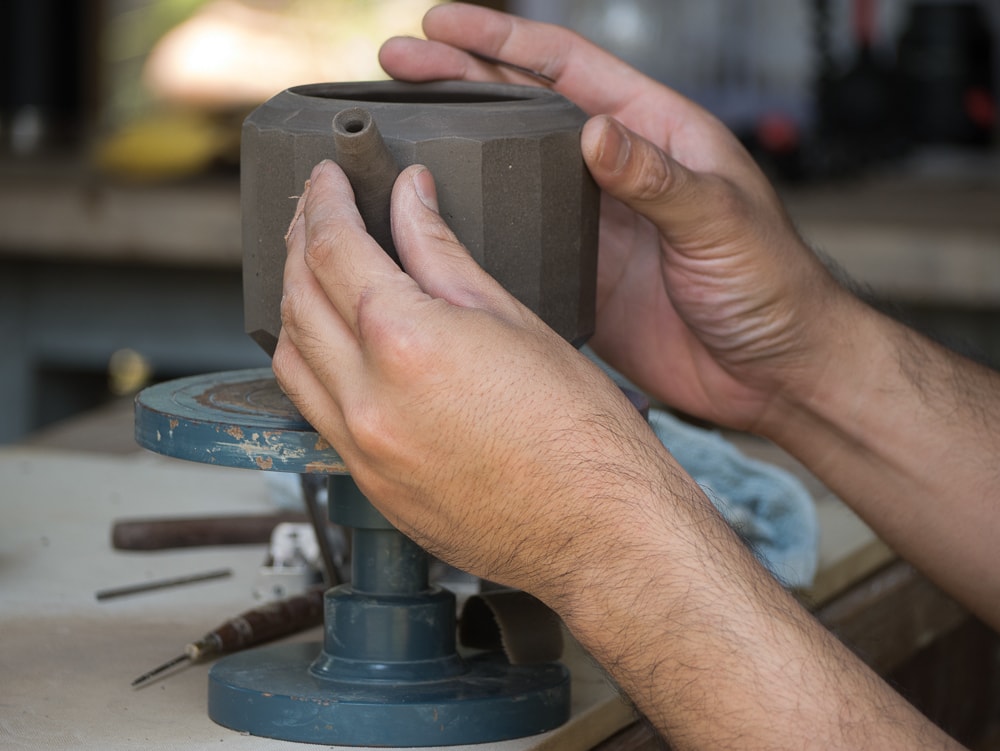
During the leather-hard stage when clay is almost dry but still malleable, Jirawong trims a cup or bowl with a loop tool as the wheel spins, removing excess clay. He then makes a foot, or base, using a different set of tools. Decorative handiwork and the application of handles and tea spouts also happen at this stage.
After further drying, it's time for the first firing - known as the bisque firing - at around 800 degrees Celsius. The mud-colored clay is baked to an orangey terra-cotta in Jirawong's kiln during this first firing. Fragile bisque pieces are often smoothed-over using sandpaper before they're dipped in glaze.
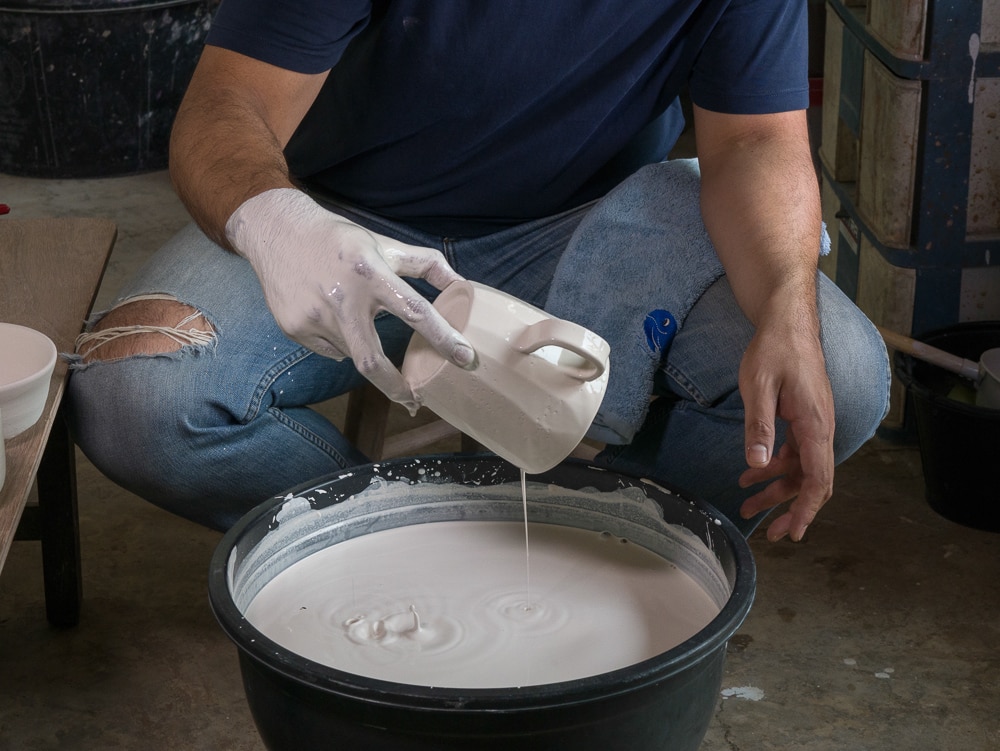
The Process: Glazing
Jirawong makes most of his own natural glazes, especially when materials such as white clay and natural ash aren't available in the local markets. The type of wood used for ash will determine the color of the glaze:
"Longan wood can make a green glaze. And teak wood can make a cream-colored glaze. The age of the wood effects the color of the glaze - old wood creates a different color of green than young wood does." Jirawong said. "Each time I make glaze, the color is different. It's not always exactly the same."
After a careful dip into the glaze bucket, the ceramic pieces are fired at 1,280 degrees Celsius which melts the glaze creating a smooth covering.
"For THE KINDCRAFT collaboration, Lauren and I decided to use white glaze which is made from white clay with no ashes," he said.
Collaboration
THE KINDCRAFT x InClay Maker Collaboration happened organically: Jirawong and I discussed ideas for our project before we began in earnest. "Handmade works are more delicate than industrial pieces, and they are good for small projects which require unique details. We can control the handmade process piece by piece giving them special character," he said.
As a designer, I gathered inspiration and gave Jirawong a mood board. One image featured a painted scalloped shape which Jirawong cleverly made his own with the use of a clay-slicer. He cut scallop-like sections from the clay at the base of each mug, cup, bowl and teapot giving this otherwise minimalist collection a distinctive handworked feel.
"The purpose of my ceramics is not for decoration, but to be used. If no one used my ceramics, I would not feel successful— as if the last part of the process was missing," Jirawong said.
"When I see people using my ceramics, I feel happy."
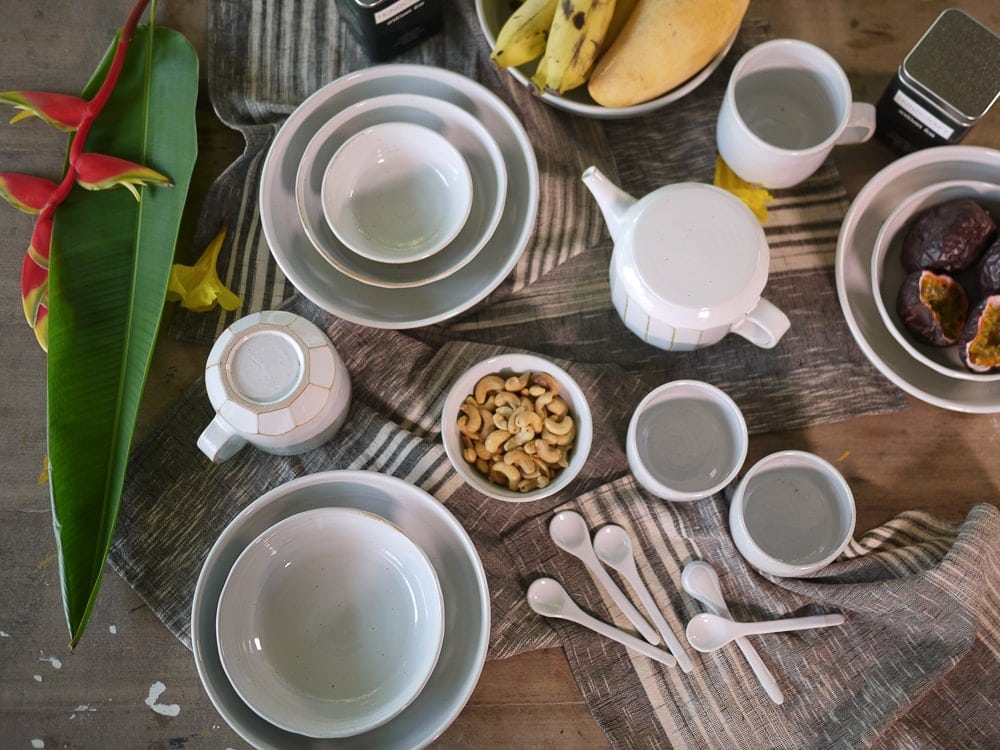