Shibori — one of Japan's oldest indigo dyeing techniques — has seen its cool blue and white palette transformed into a red-hot global trend in recent years. But though this burgeoning worldwide market has helped to launch and to grow new communities of traditional dyers and artists, it has sometimes made it difficult for their individual work to be seen within what can sometimes feel like a rising tide of tie-dye.
One artisan shibori label, Slowstitch Studio, has decided to chart a distinctive course. Formed in 2015 by Kanchalee "Ann" Ngamdamronk and Sergey "Serge" Tishkin, Slowstitch creates colorful—and intricate—designs through a carefully controlled process of dyeing and stitching. Their aesthetics are, as you'd expect, grounded in traditional shibori techniques — but they also arose from a shared desire to find a slower pace of life that might allow deeper focus on details.
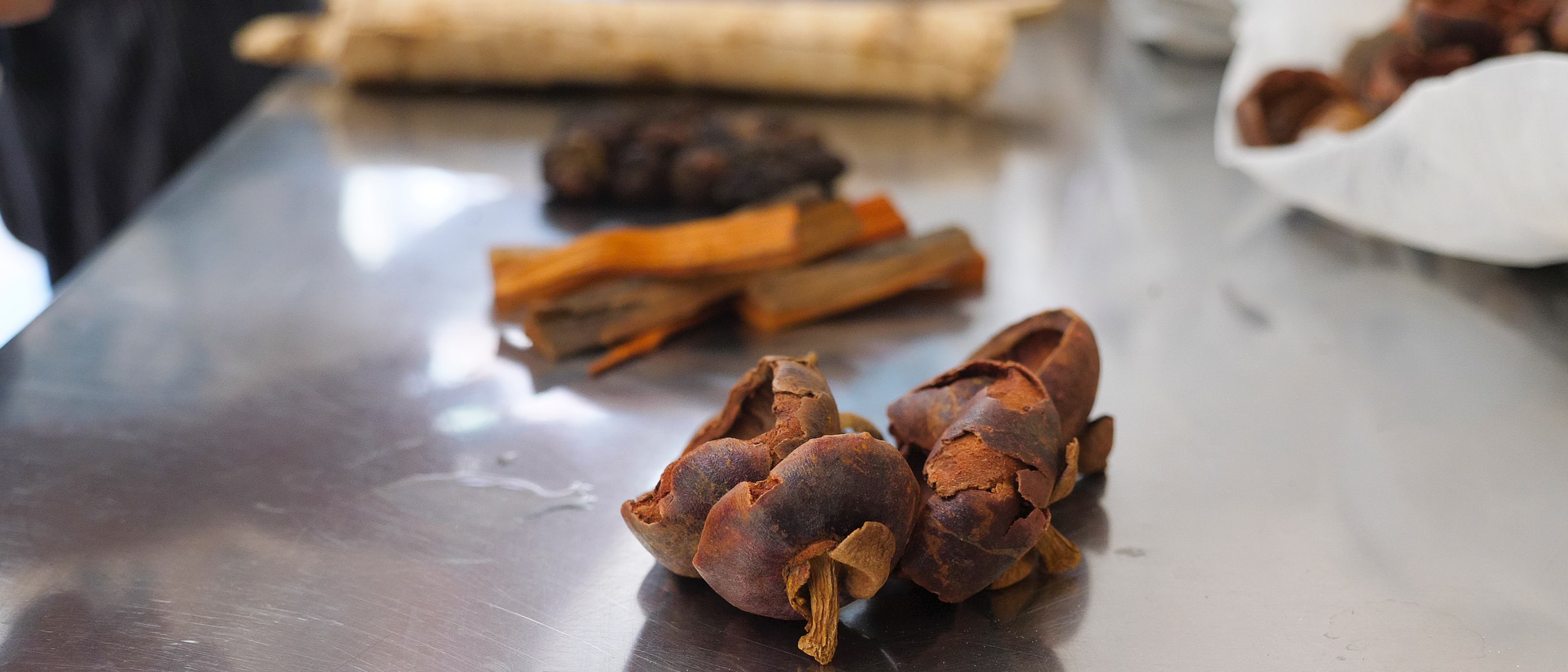
Slowstitch Origins
Ann Ngamdamronk recalls the beginnings of what would later become Slowstitch Studio. "I was browsing through the Internet and found this Canadian man who had a blog called "Japanese Textile Workshops" and who'd been living outside of Tokyo on a mountain for 25 years — farming silk, doing hand weaving, and teaching workshops in his farmhouse about shibori and indigo dying. And I thought 'This is interesting...'".
It was this rural Japanese lifestyle which Ngamdamronk says was especially enticing to someone like her who grew up in Bangkok: "I was a city kid. I studied in London. I was 24, working as a freelance textile designer, and tired of being stuck in traffic for three hours a day. I didn't really think about what to expect. It was just this strange urge to go and learn something new."
She signed up for a 10 day course and traveled to the Japanese farmhouse she first saw online. It was there where she met Serge Tishkin, who was already knew the teacher and was helping at the workshop. "I thought 'He's a calm, cool person' and so we spent quite a lot of time together. Ngamdamronk asked to stay another two months after the course was complete to learn more about shibori and, she says, "because I like sitting and stitching so much".
By the time she was to return to Thailand, it was clear the seeds of a new career — and a new personal connection — had been planted. "I remember telling Serge: 'I don't know what I'm going to do when I go back yet. But it would be nice if I could maybe do something from what I learned here and make a business.'"
EARLY EXPERIMENTS
Back in Bangkok, Ngamdamronk says she used her free time to practice shibori and develop her own patterns. She also kept in contact with Tishkin. "We would talk about shibori and developing things together, but it was quite difficult when we weren't in the same place. So Serge would come and visit for a month and then... we just learned together and experimented on natural dyeing and indigo together in the backyard at my house."
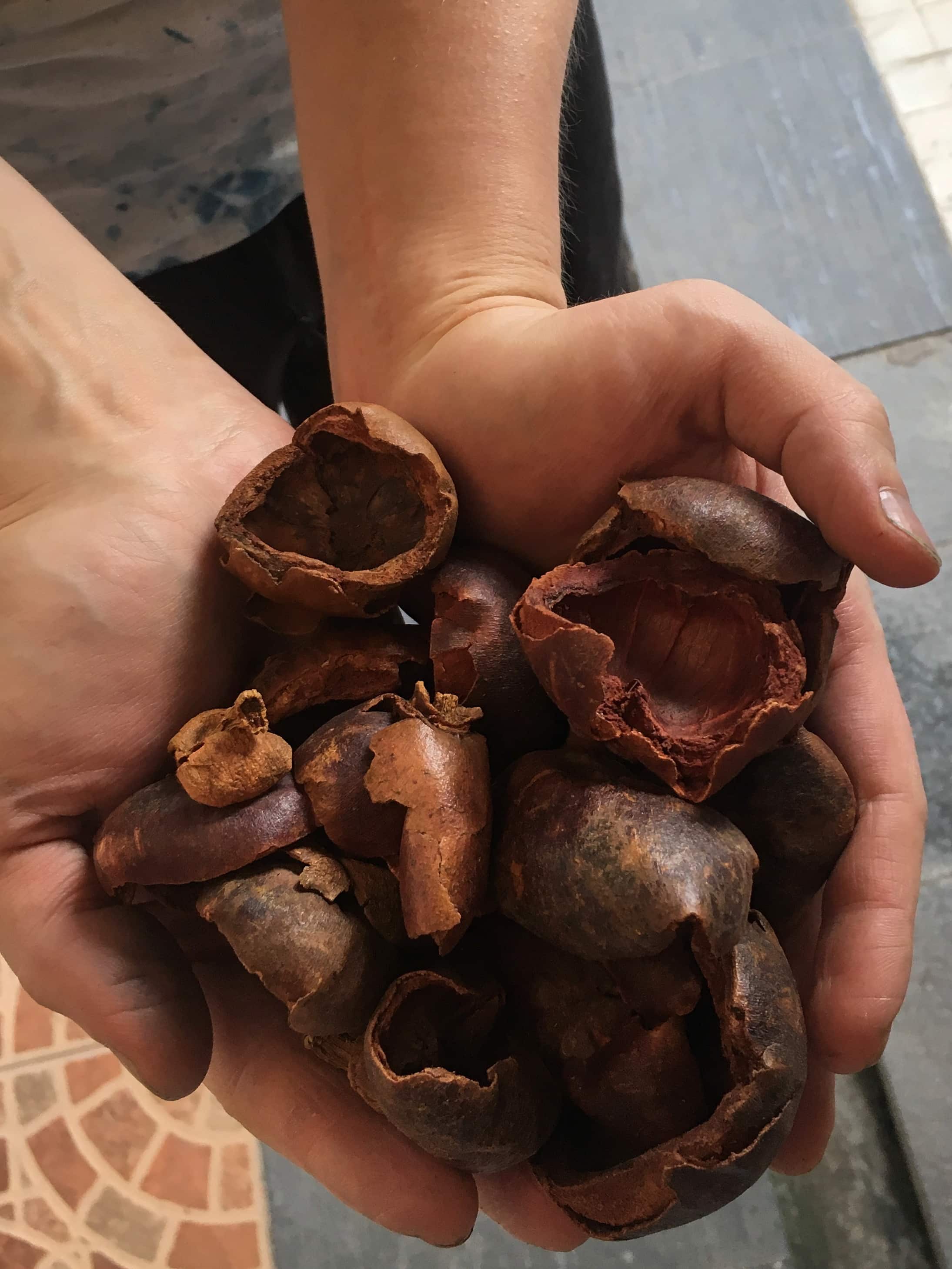
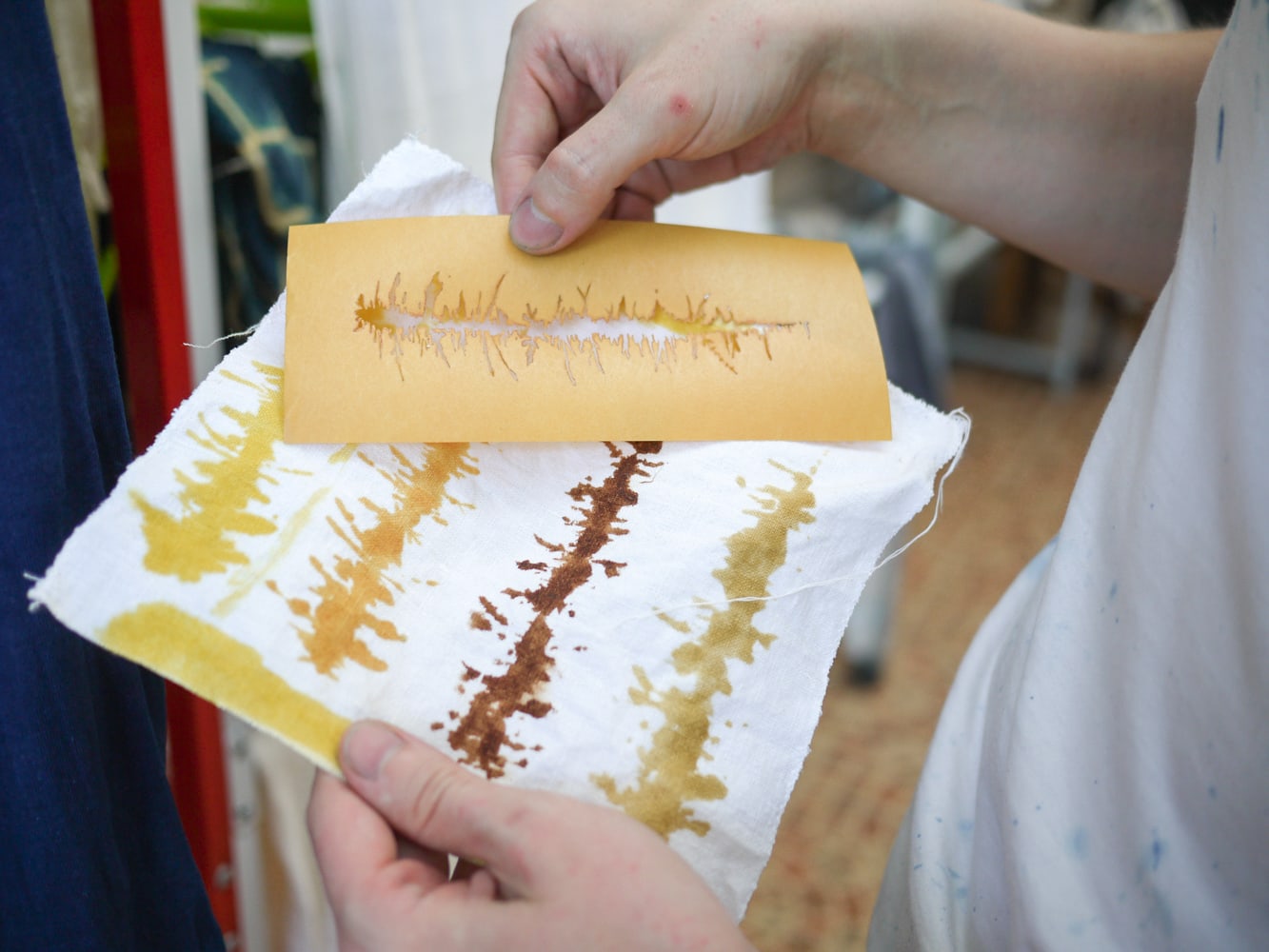
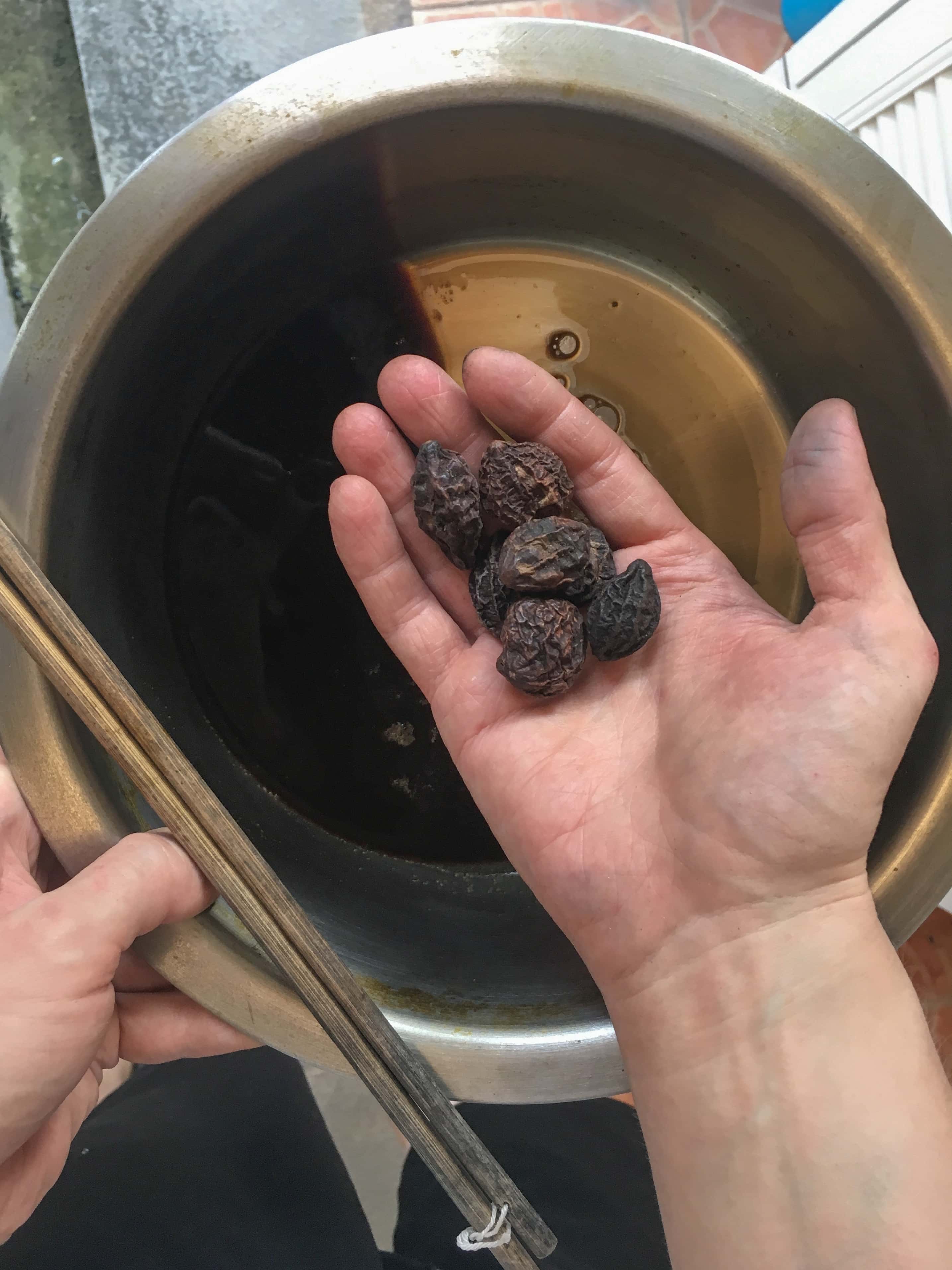
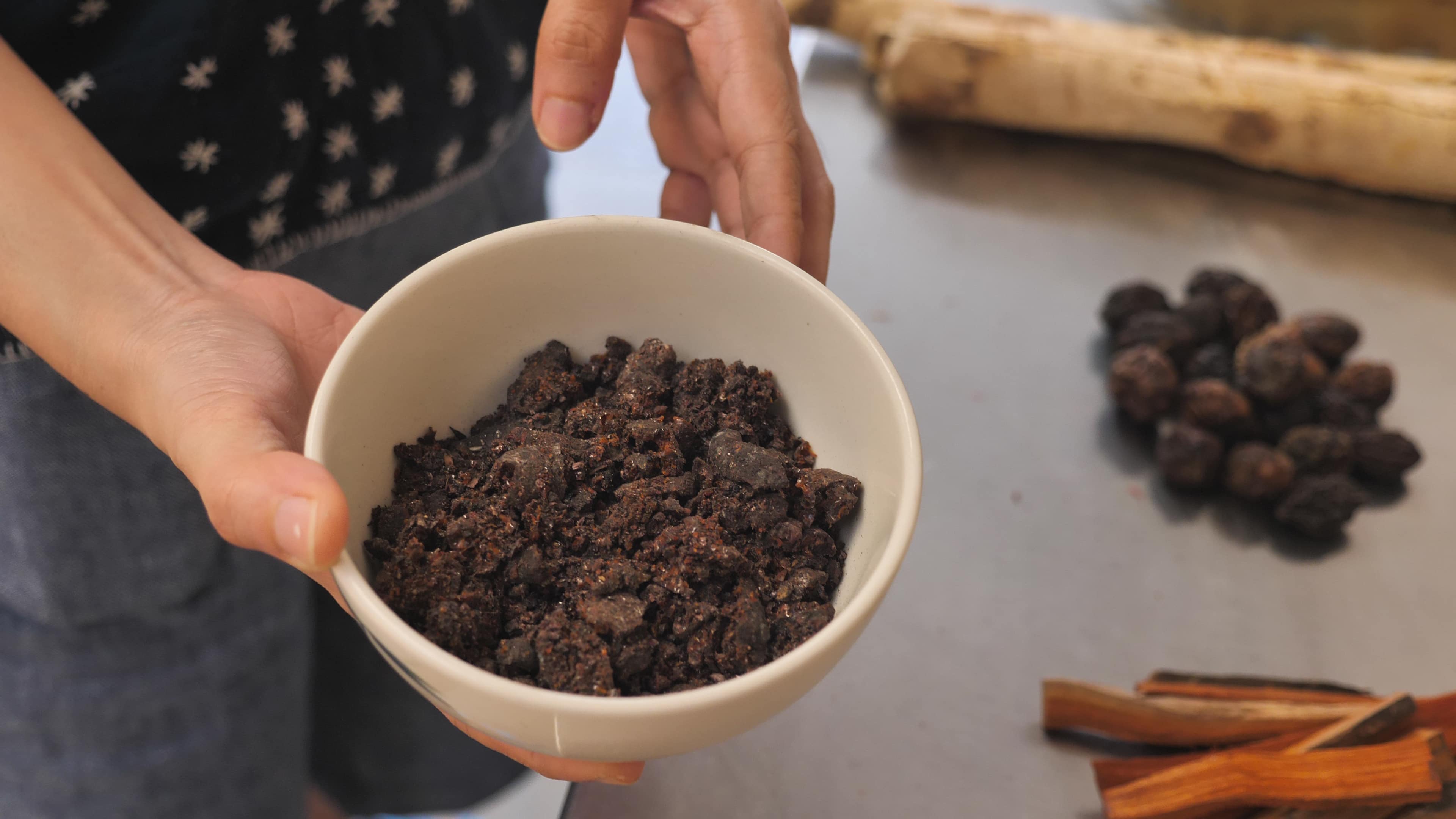
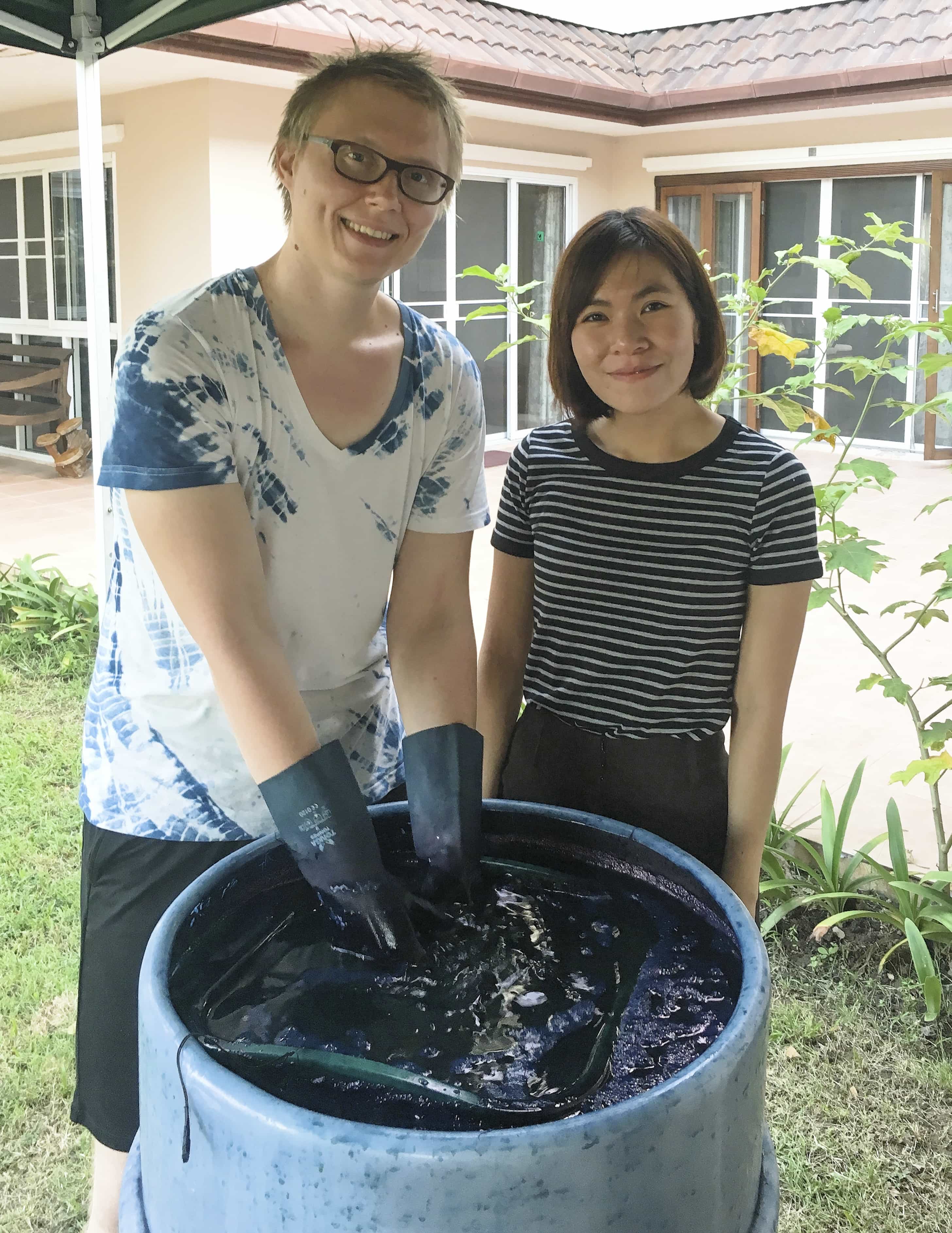
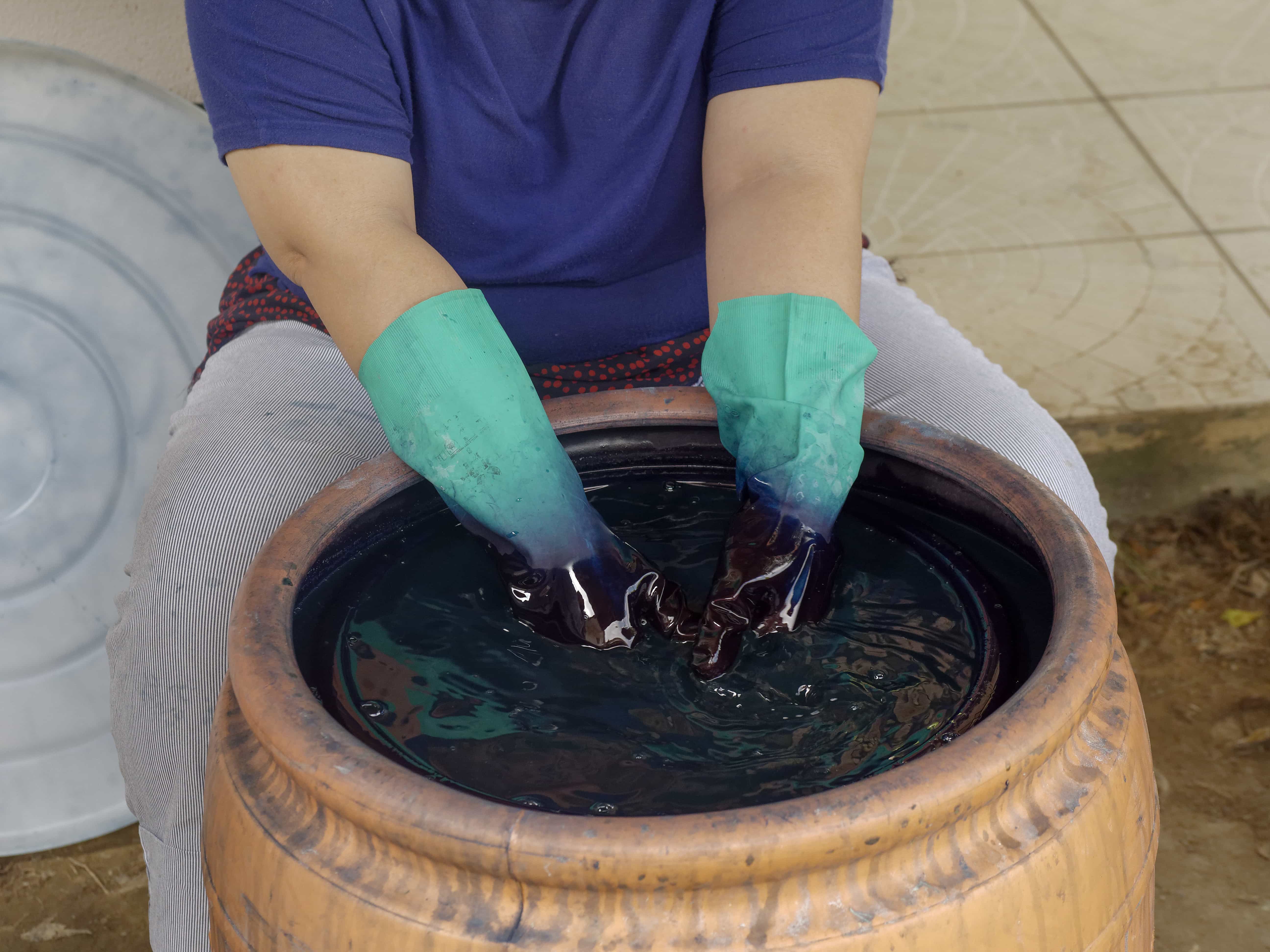
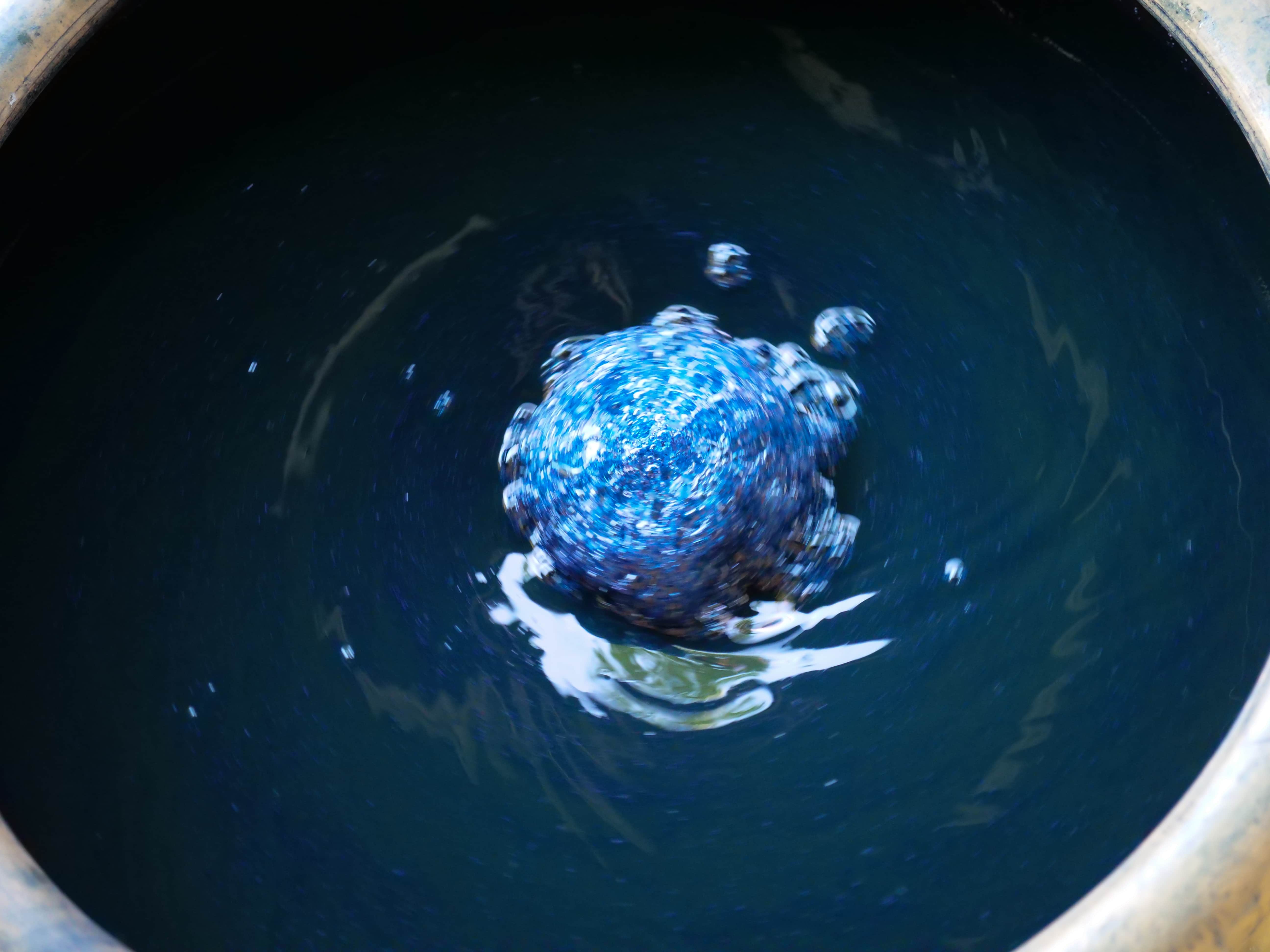
Adapting Japanese indigo techniques to Thailand proved to be a process of trial and error, says Serge Tishkin. "I think our first four vats did not go so well. The Japanese can be pretty specific with details of how things like vats have to be made — in a conical shape so that, when you stir the sediment, the shape of the vat creates a specific kind of vortex that redistributes all the Indigo. And so, one of Ann and my first purchases for our company were these antique Burmese water baths which were just the size and shape we needed, but which were not cheap."
There was only one problem, Tishkin discovered. "They all leaked."
FINDING A UNIQUE STYLE
Pushing past the initial difficulties, he says the pair decided to actively embrace a process of adaptation. "We've thrown out so many of the old rules that we had to follow — to just retrofit things to what we need here and now". This process of continual improvement put Slowstich on a road to finding their own unique style and, over time, the pair began to push things further with color and pattern.
"We wanted to bring in other colors into our work and that's not really seen much in shibori," says Ngamdamronk. "We'd like to develop something that is quite unique in the [shibori] process itself. It's the stitching — the stitching technique and combining other colors into the work — that we think is pushing the boundaries."
The base for these colorful explorations is, of course, the famous shibori palette. "I love blue and white," Ngamdamronk says with a smile, "and, though I've been working with it for quite a few years, I'm still not bored of it." Slowstitch also uses a number of natural dyestuffs in conjunction with their semi-natural indigo: Sappanwood, the bark of maphuut (a tropical fruit tree native to Southeast Asia), mangosteen and pomegranate skins, Eucalyptus leaves, coffee, pods from the myrobalan tree — even onion skins sourced from a family restaurant are sometimes used to create a golden brown hue, Ngamdamronk says.
THE PROCESS
But it's how these colors are incorporated into their designs which sets their work apart. "We like to spend time developing patterns that are quite complicated," she says, "not because it's complicated, but because the process and the time that you spend on a piece can result in some beautiful work. "
"To make one scarf, you get a piece of white fabric and then you scour it to get rid of any impurities which would stop natural dyes from sticking to the fabric properly." Once washed and dried, Ngamdamronk says, it's time to start drawing patterns on the fabric. "Different designs require different techniques, but mostly we start with dotting out the patterns and then drawing lines."
After the pattern is drawn on the fabric, it's stitched by hand with thread and needle. This is the longest part of the process — taking from one day to a week, depending upon the complexity of the design. "Once everything is stitched, we pull all the threads to compress the fabric in a very small bundle and then we tie all the knots to make it really tight. We soak it in water and then it's ready to be dyed." If it's a traditional shibori design, this is the point when Slowstitch begins the dip-dyeing process in the indigo vat — often repeating the process up to 10 times in order to give the fabric a dark color.
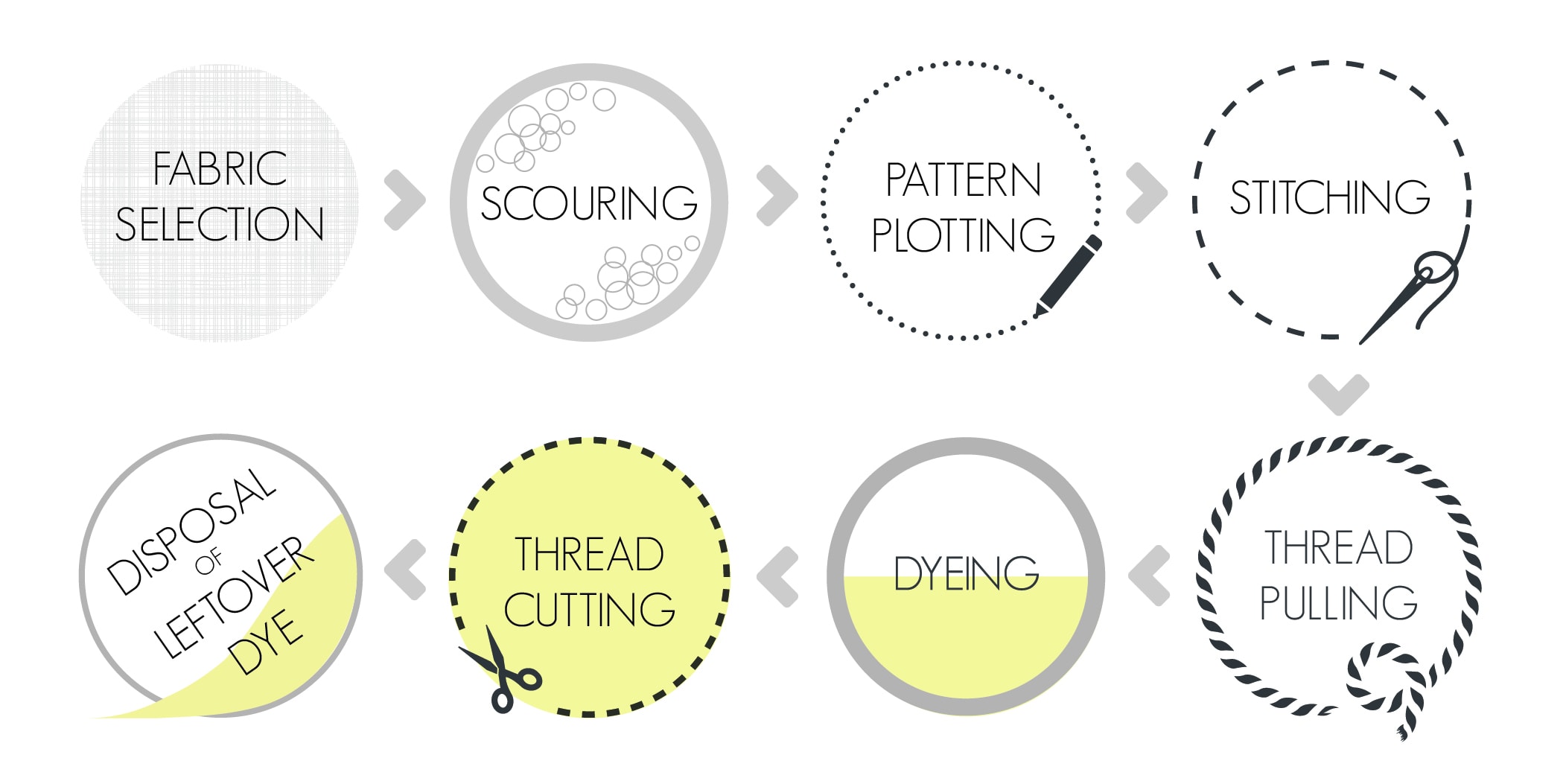
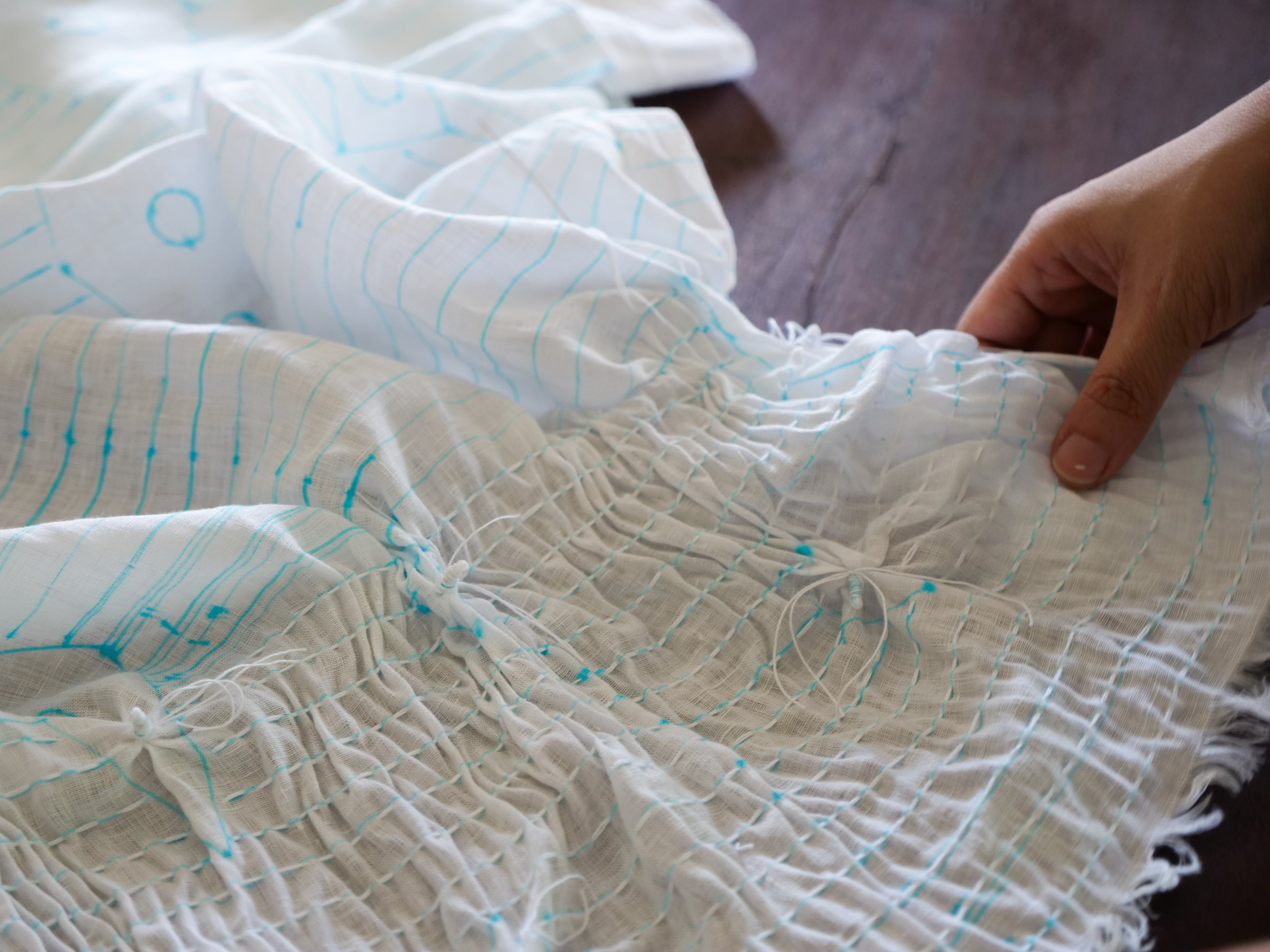
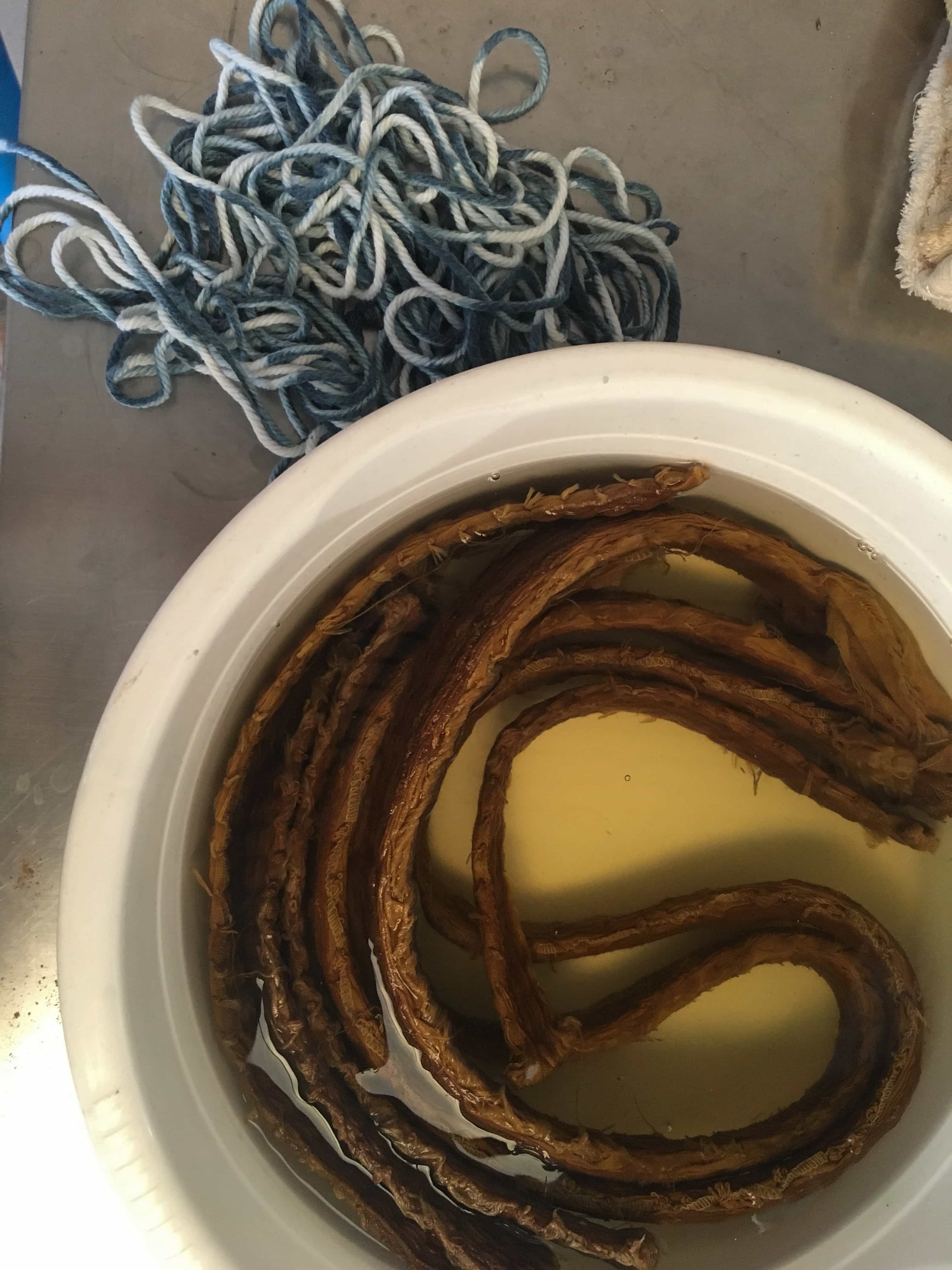
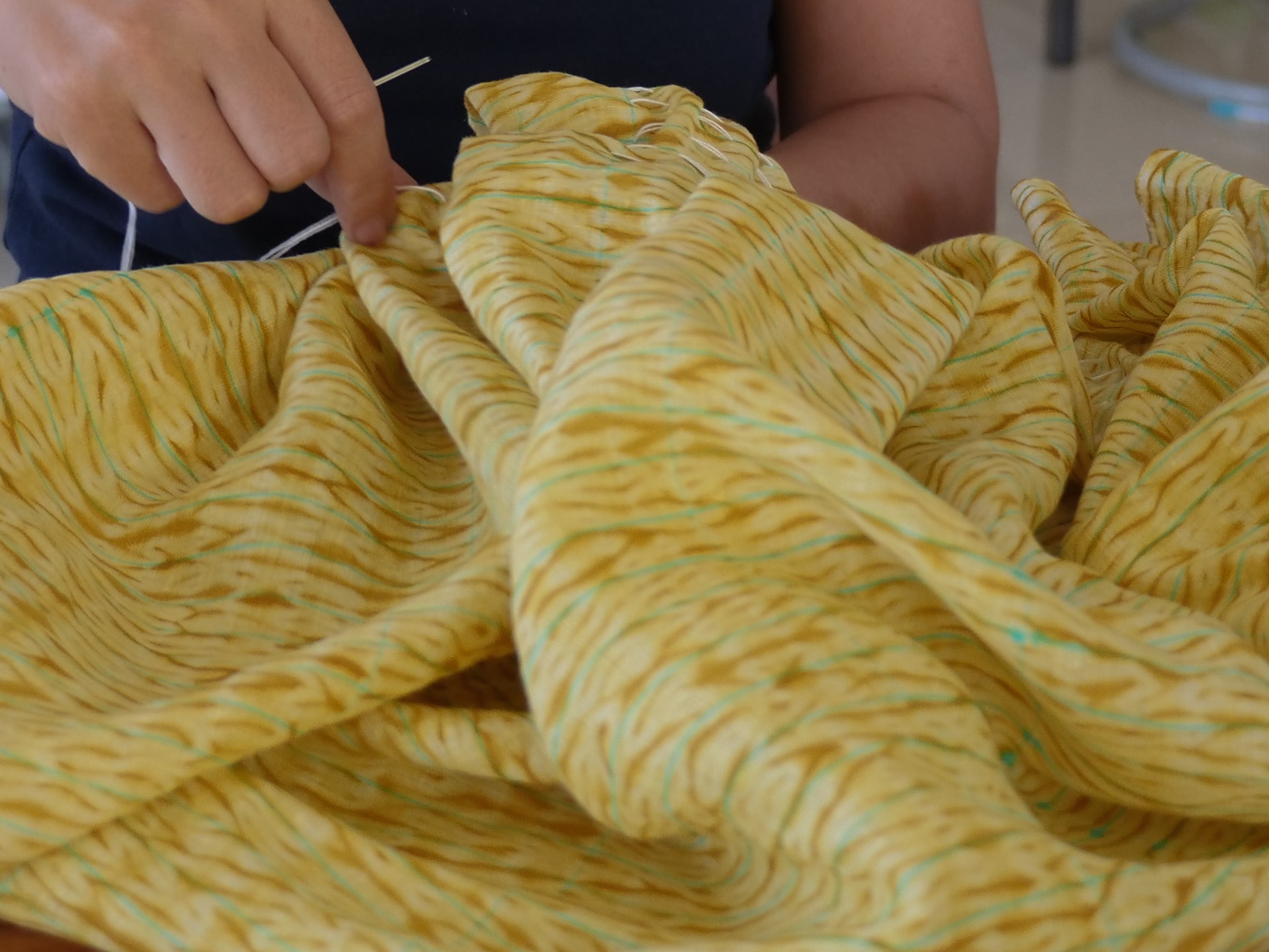
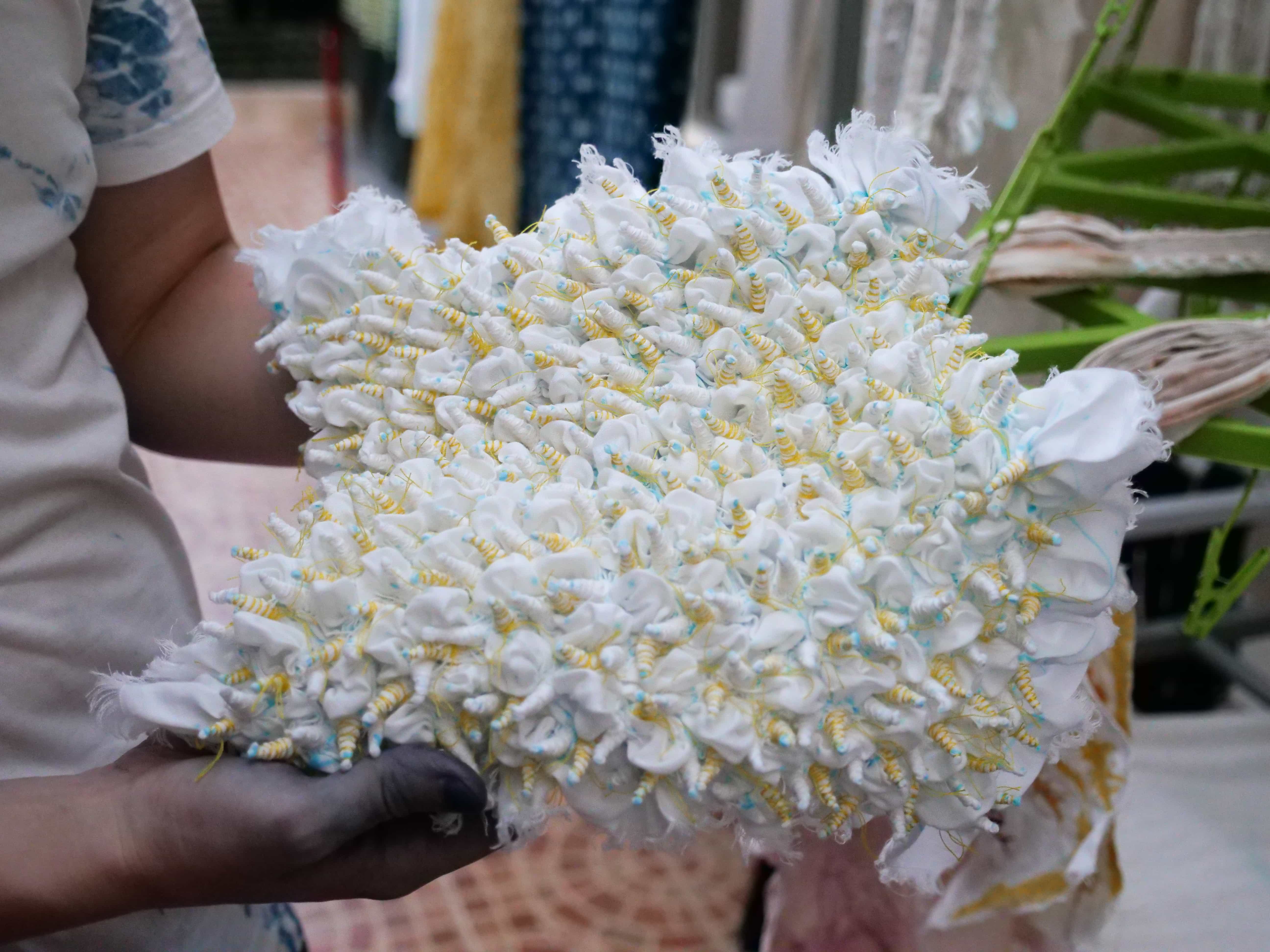
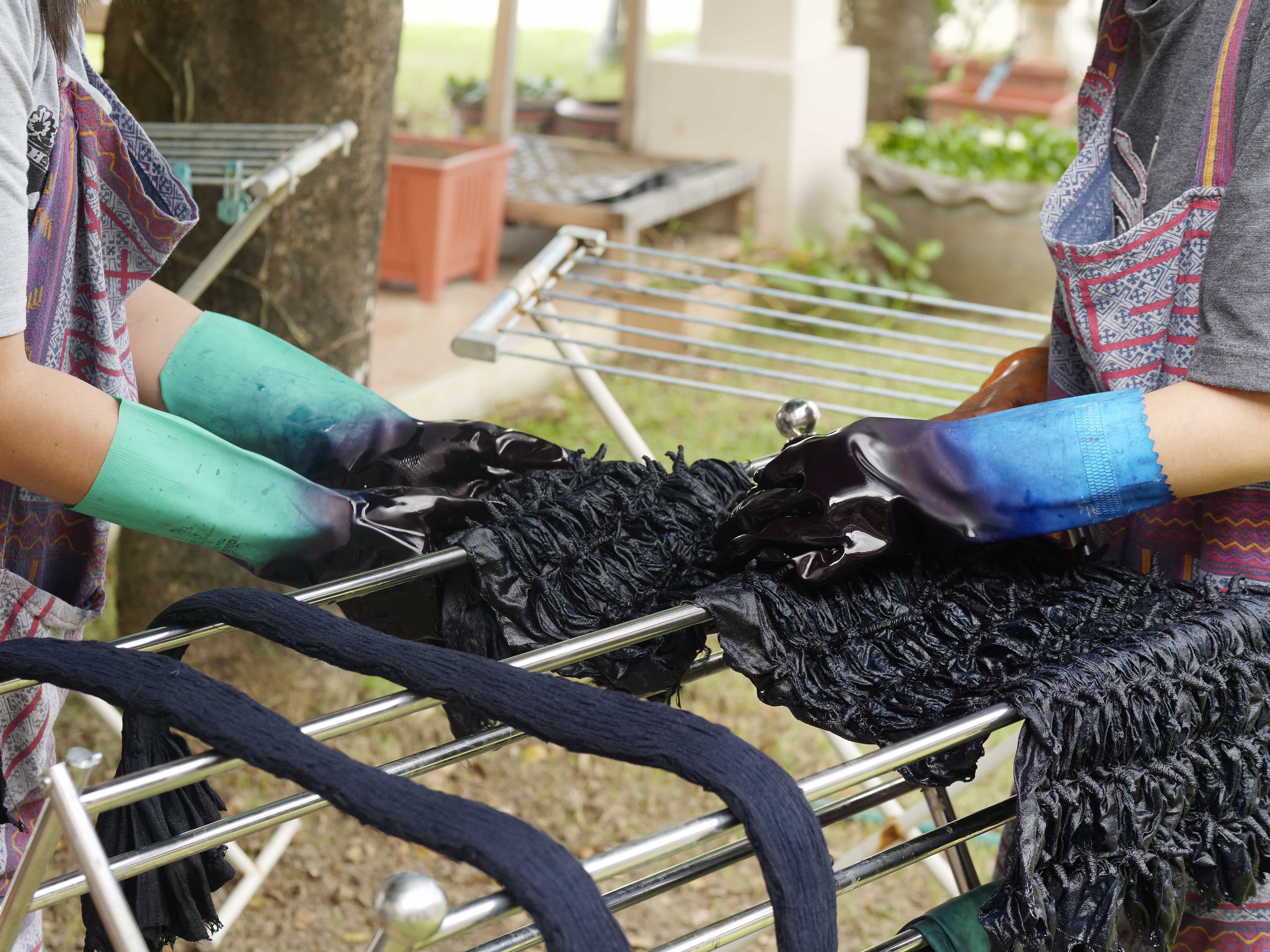
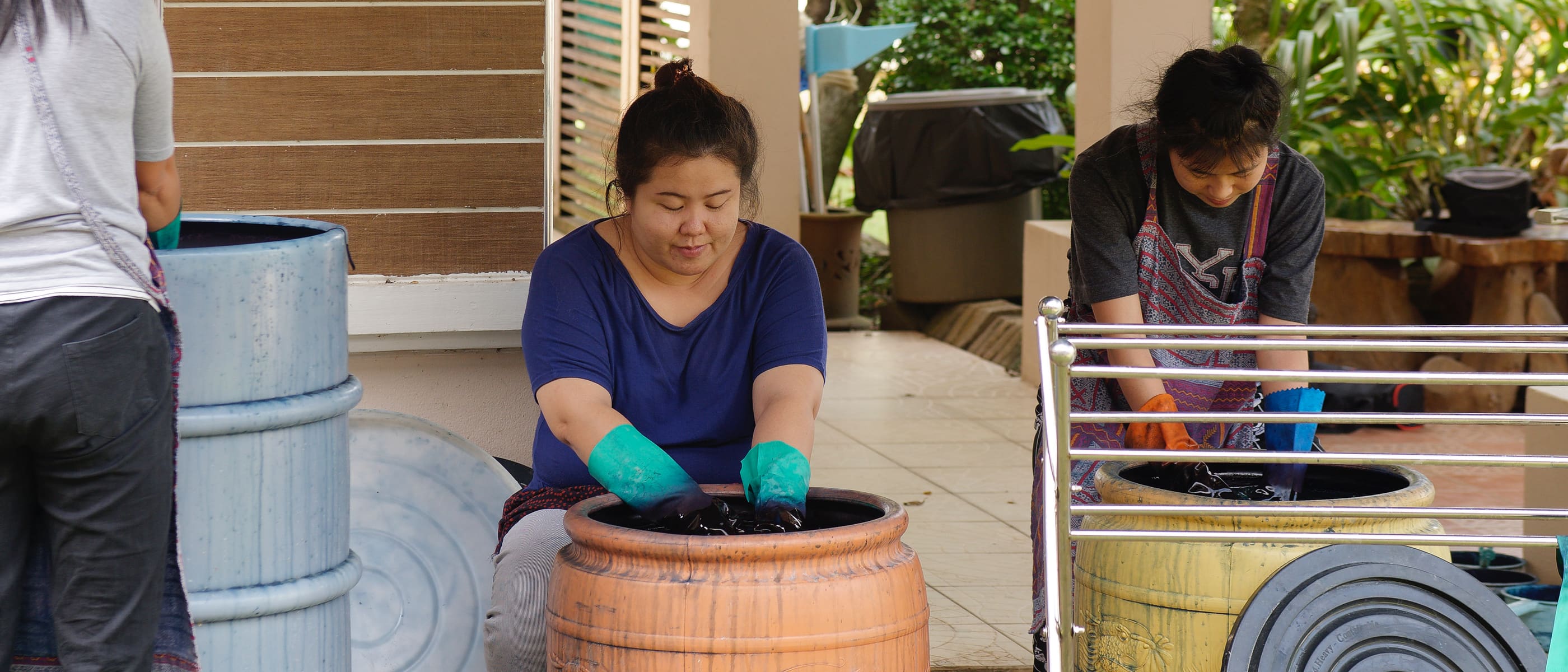
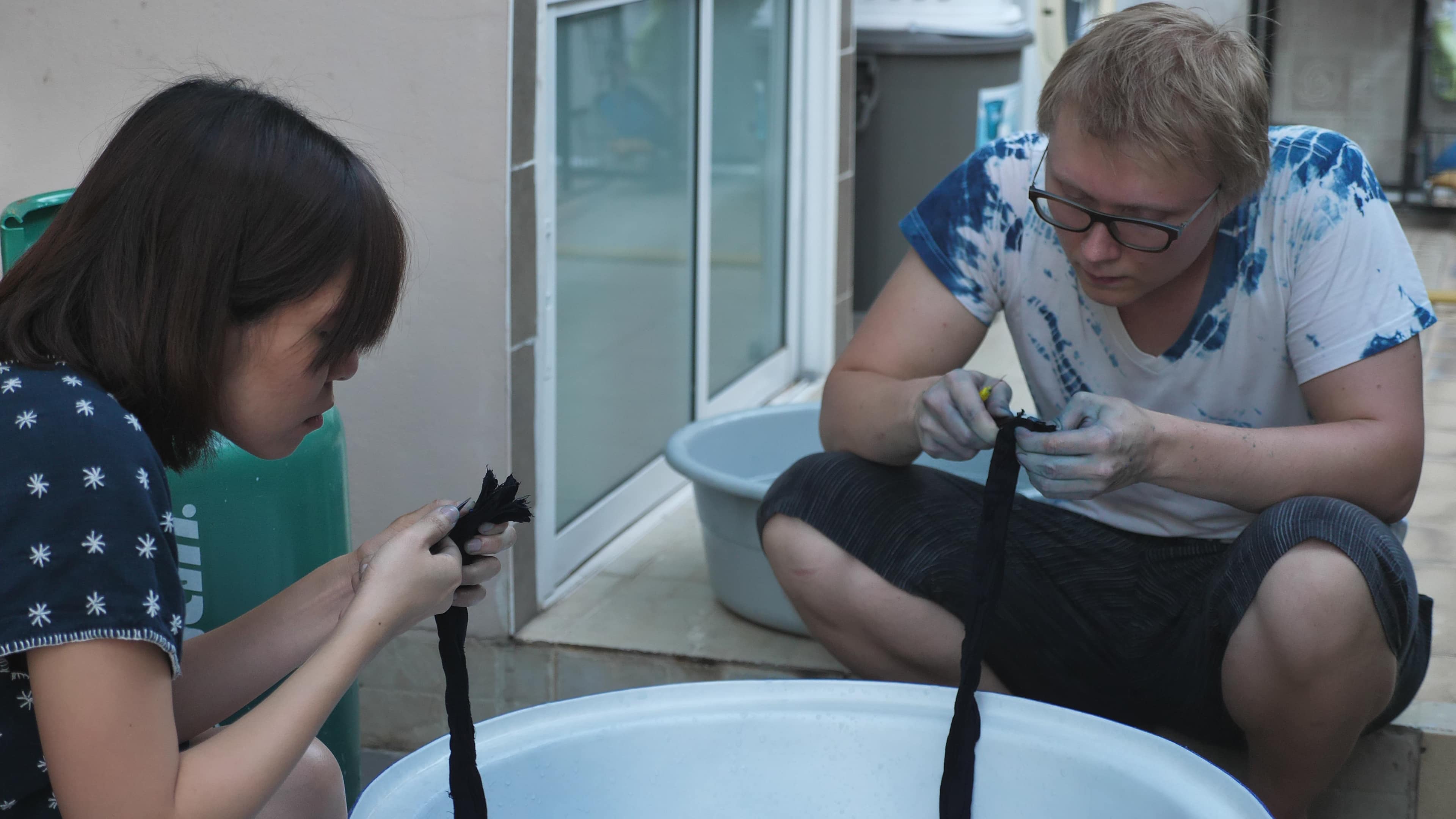
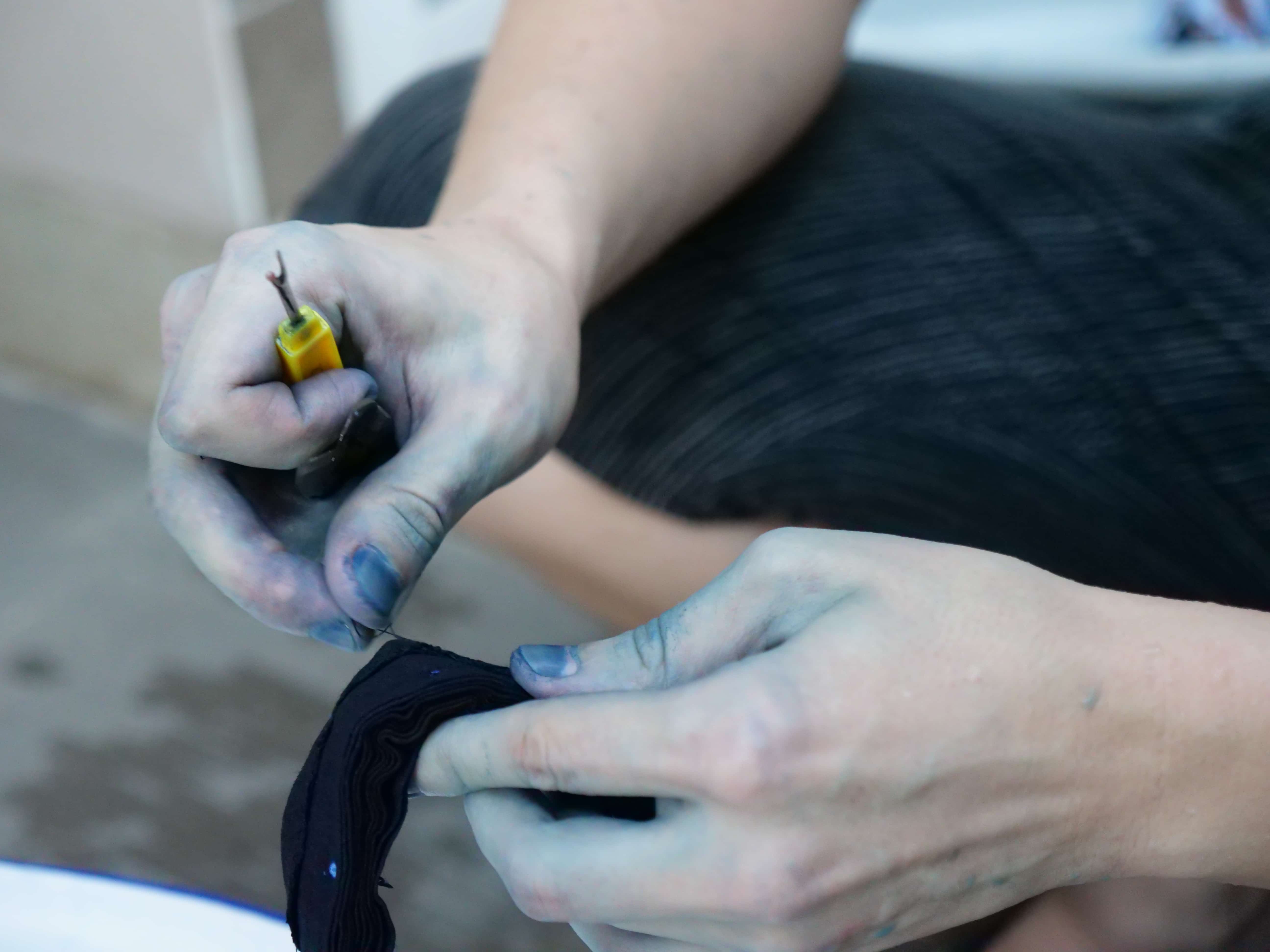
But many of their products have multi-layered designs and color palettes, sometimes laying patterns on top of one another to give deeper dimensions or more interesting qualities. This, incredibly, requires that the fabric first be dyed in another color and then have its stitching completely reworked before it is ready for the indigo dyeing process.
"There's one scarf which has a kind of wood grain pattern for the background, so we would work on that pattern first," explains Ngamdamronk. "We would stitch it first and then tie it, dye it in the yellow color, and then we would take apart all the stitching. We then rework the fabric by drawing and stitching the stripe patterns, pull it, tie it again, and dye it in indigo."
The result feels both totally organic and meticulously planned which, in the end, might be the best way to describe the Slowstitch approach to modern shibori.
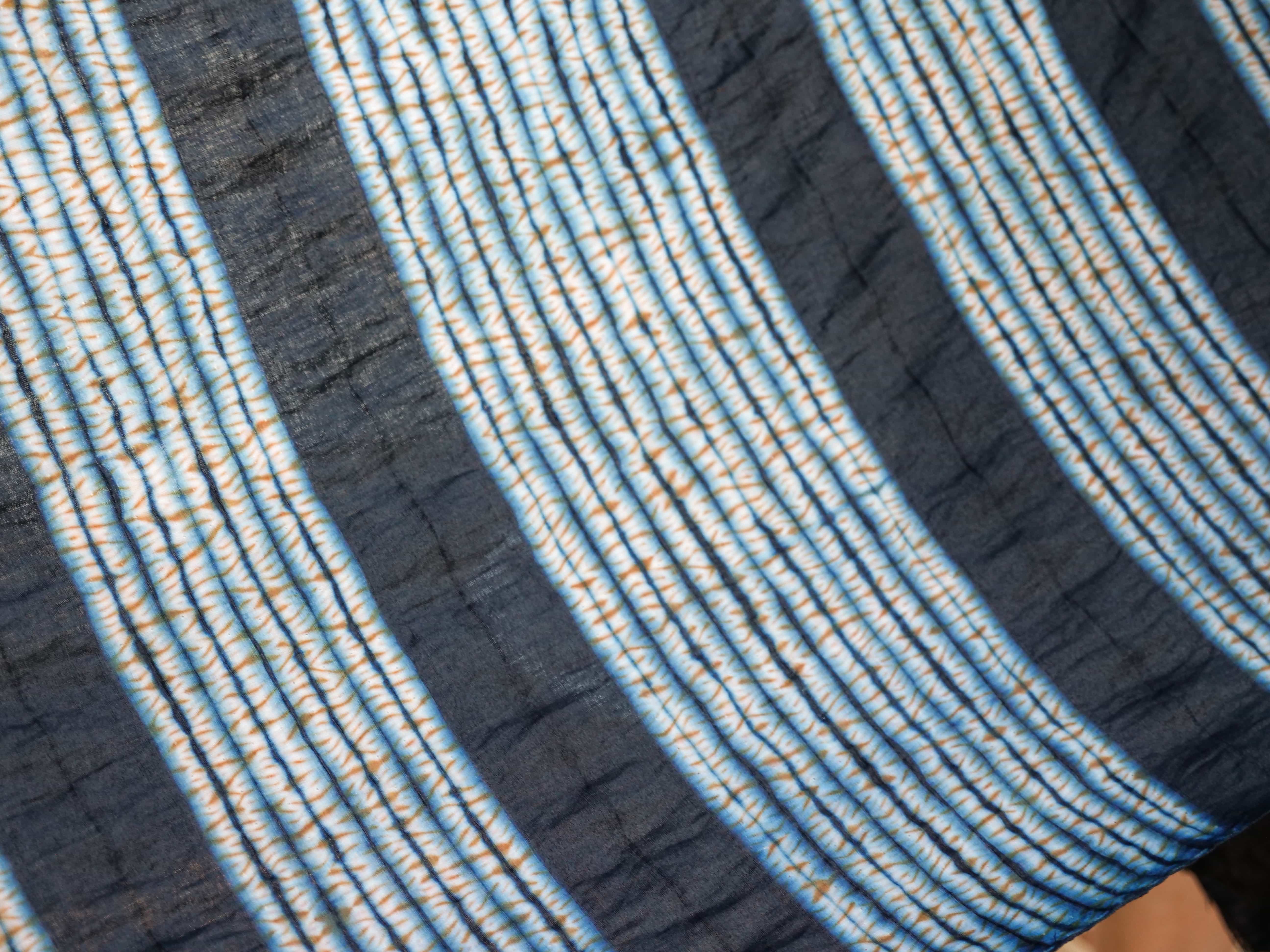
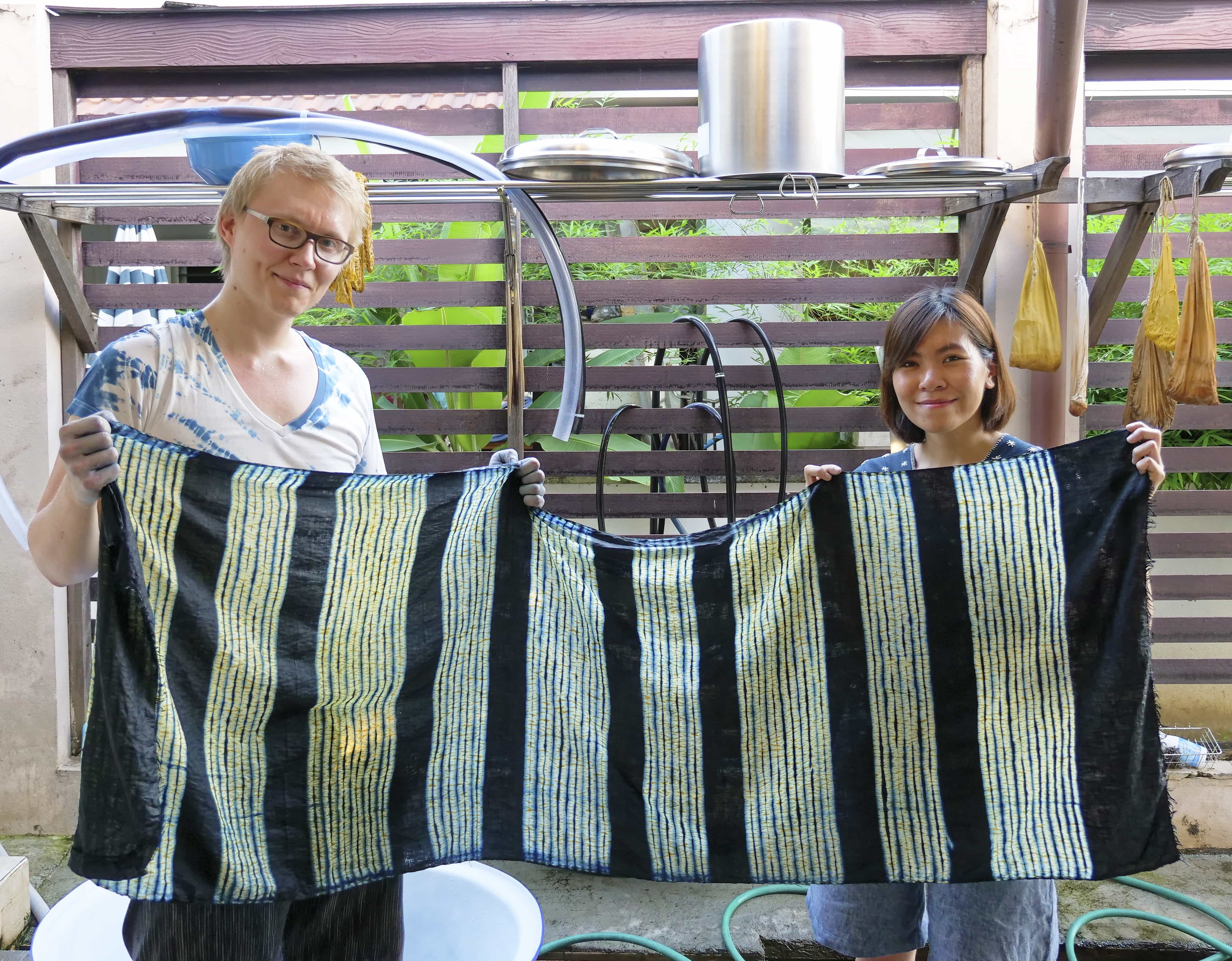
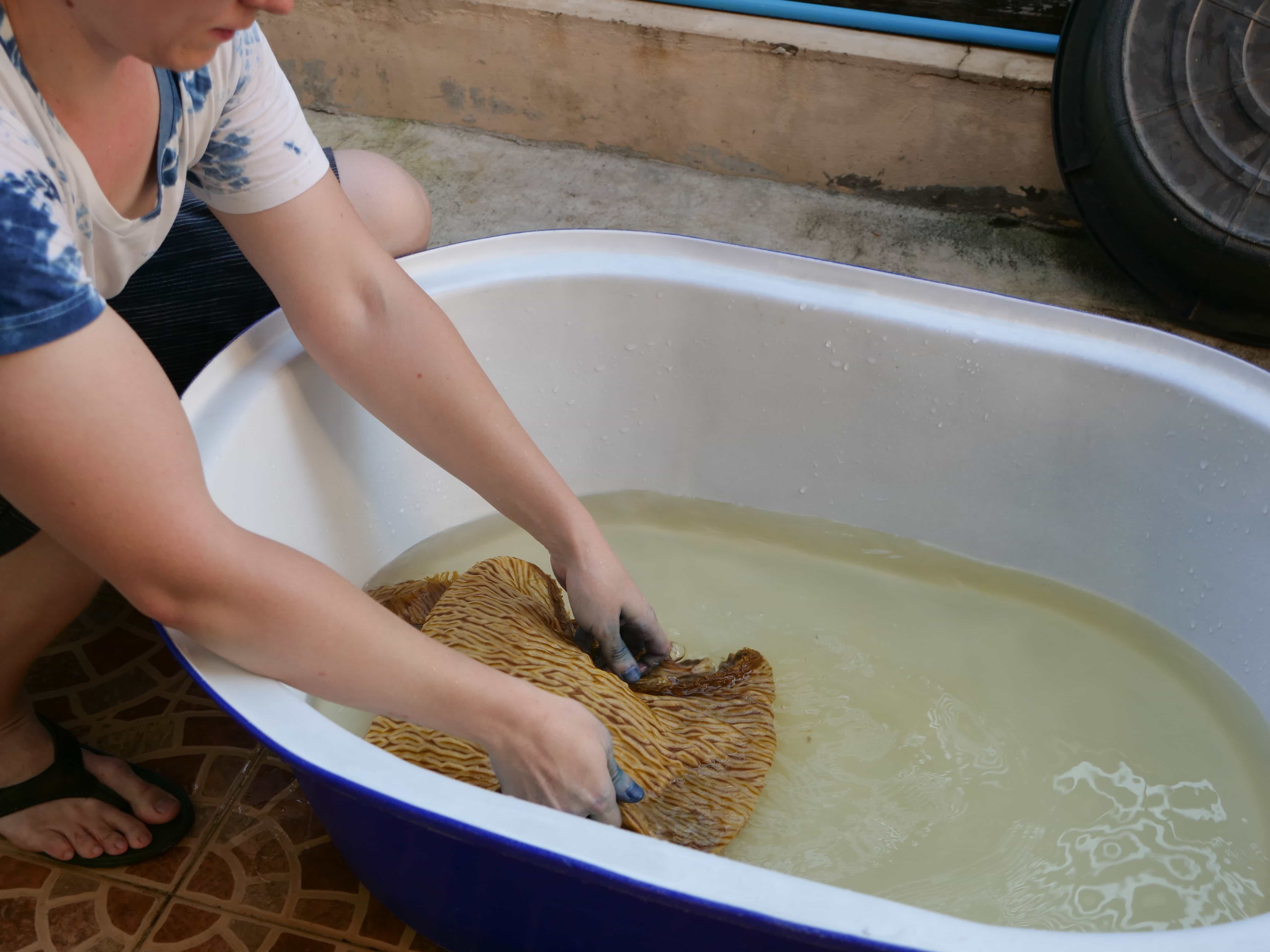
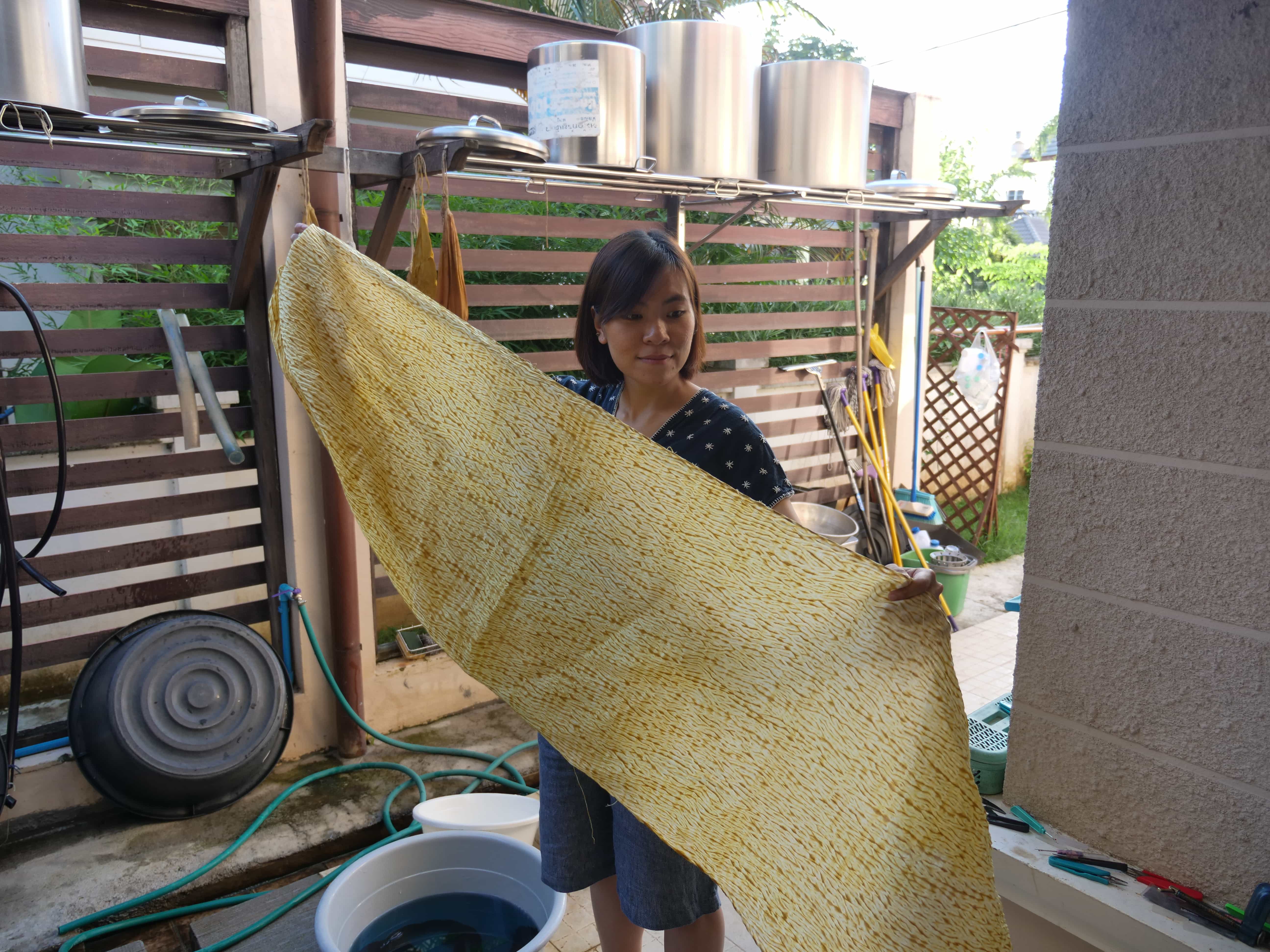
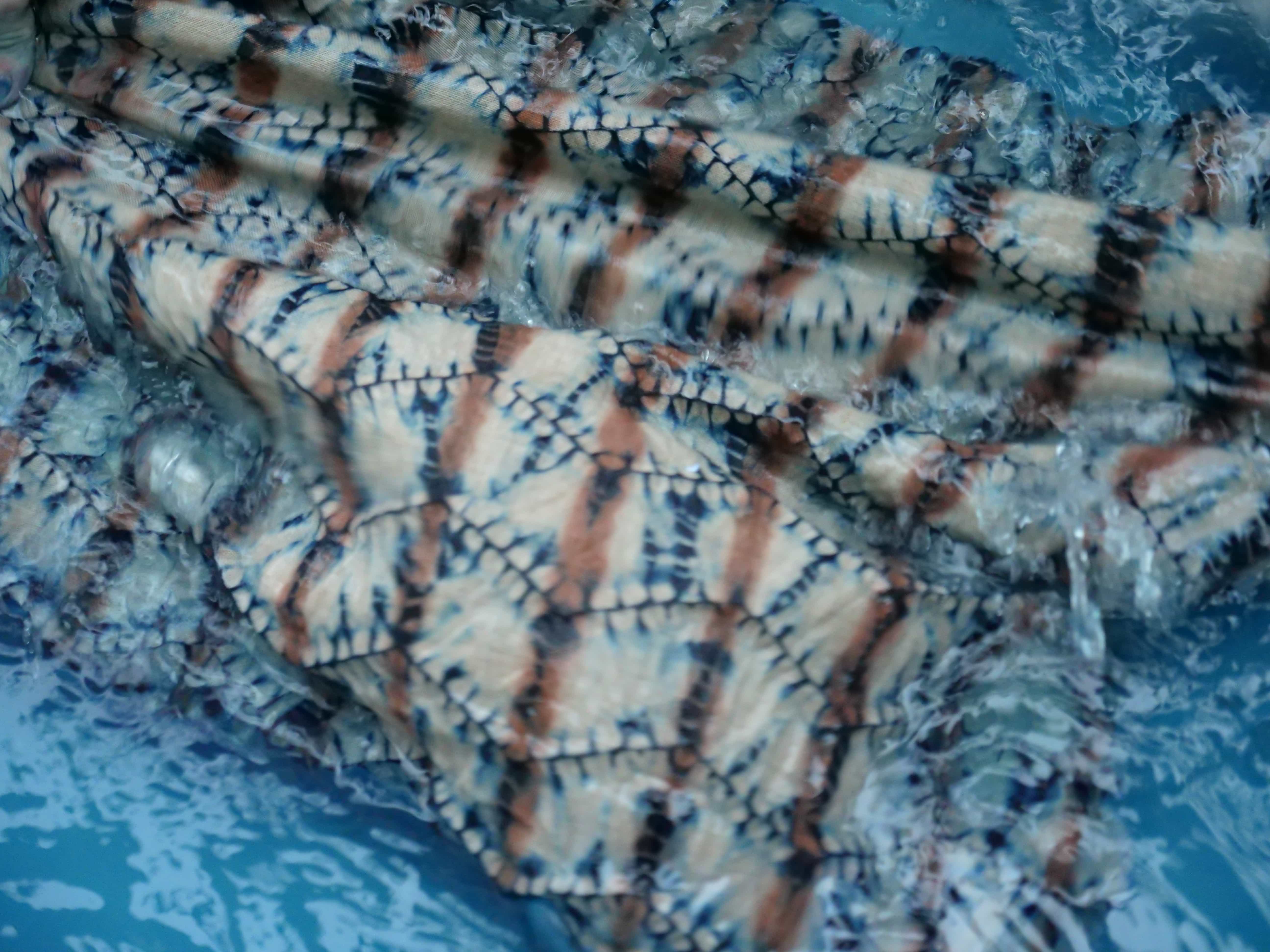