How does an architect become an experimental footwear designer? For Sara González de Ubieta Oliveros, it was curiosity about materials which led her from architecture school and into fashion and product design, researching how non-conventional substances and fabrication techniques might be incorporated to produce new varieties of shoes.
Correspondent Lara Álvarez talked with Ms. de Ubieta Oliveros about several of her projects which investigate the deeper relationships between objects, materials, design, and craft.
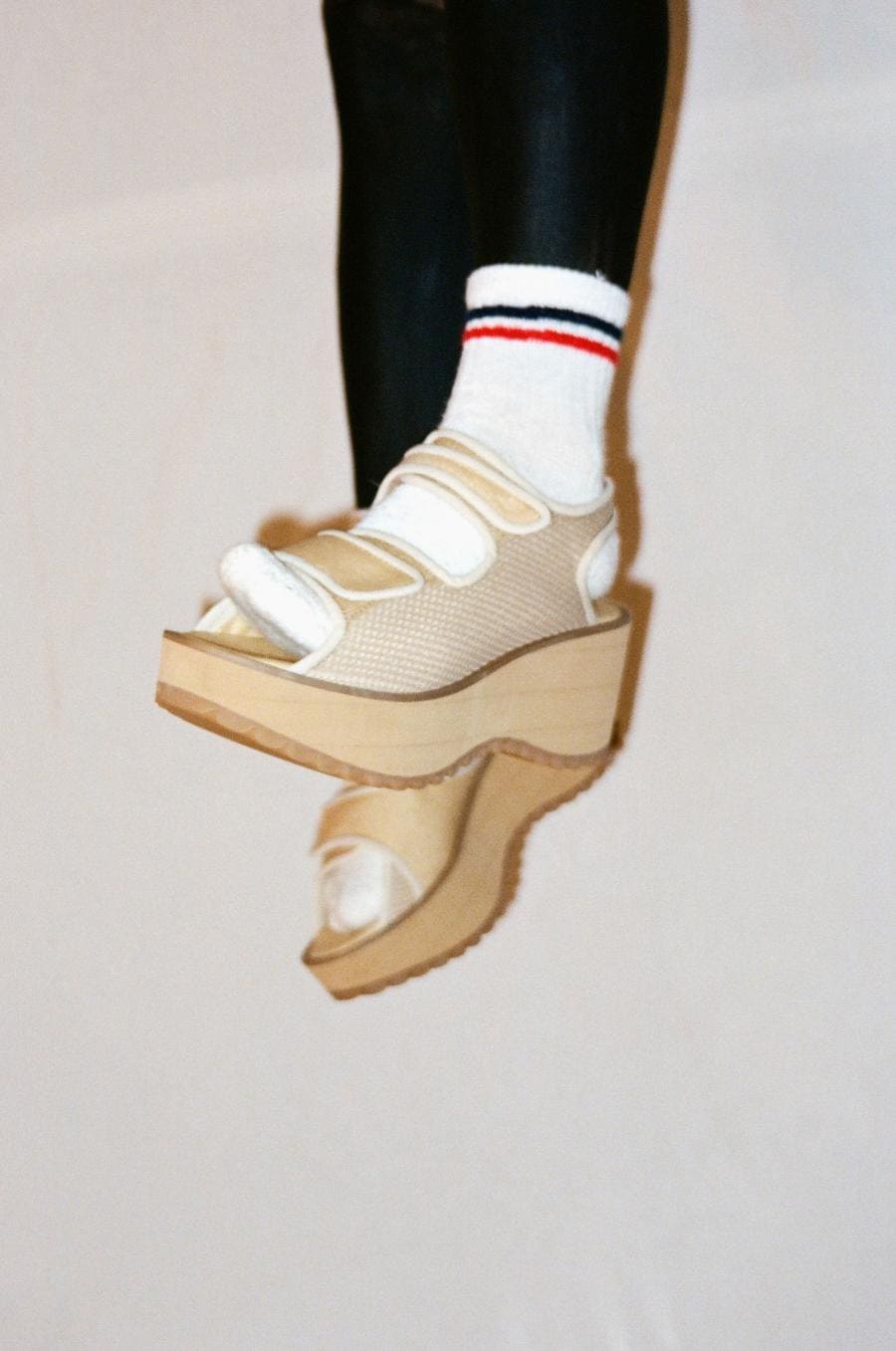
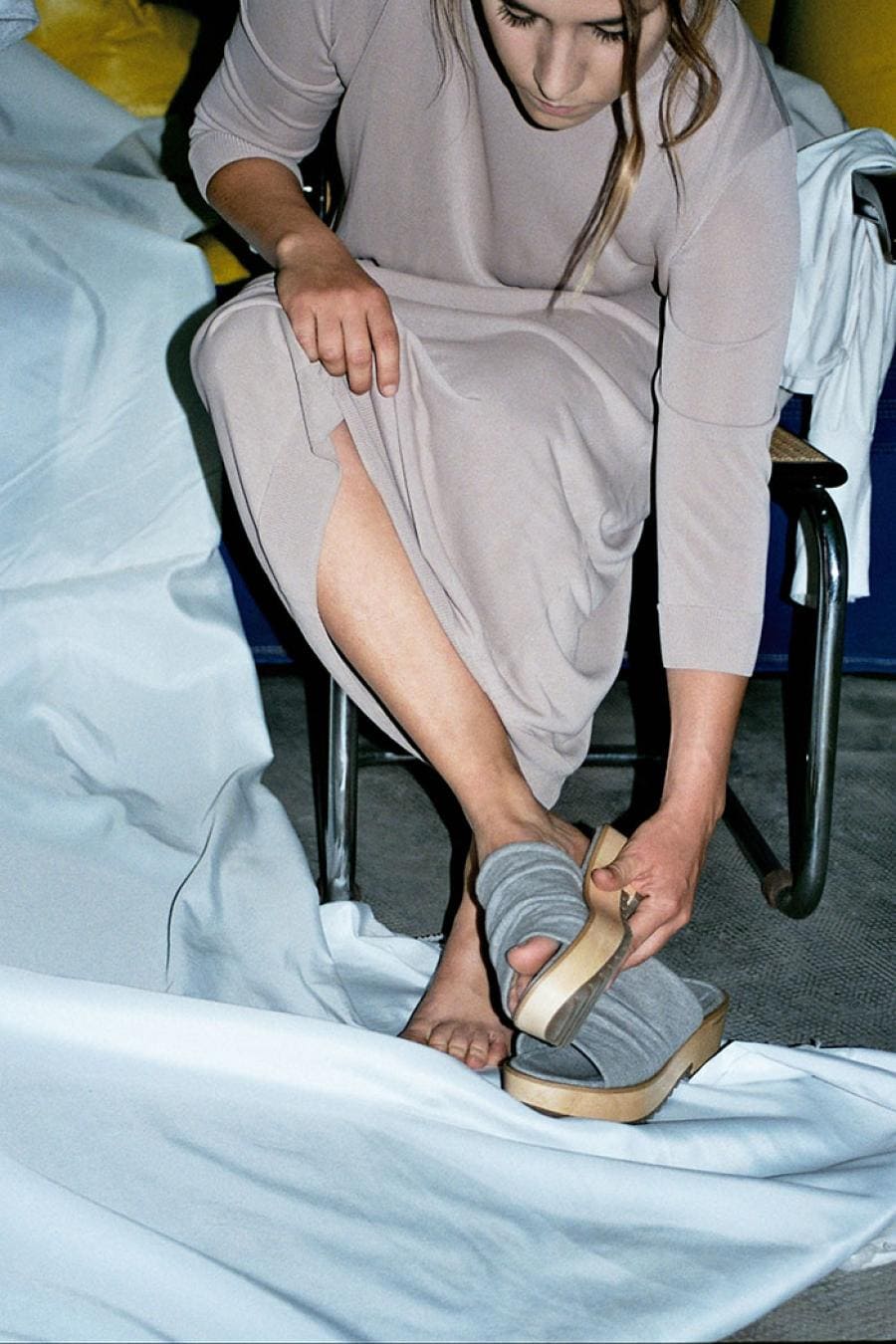
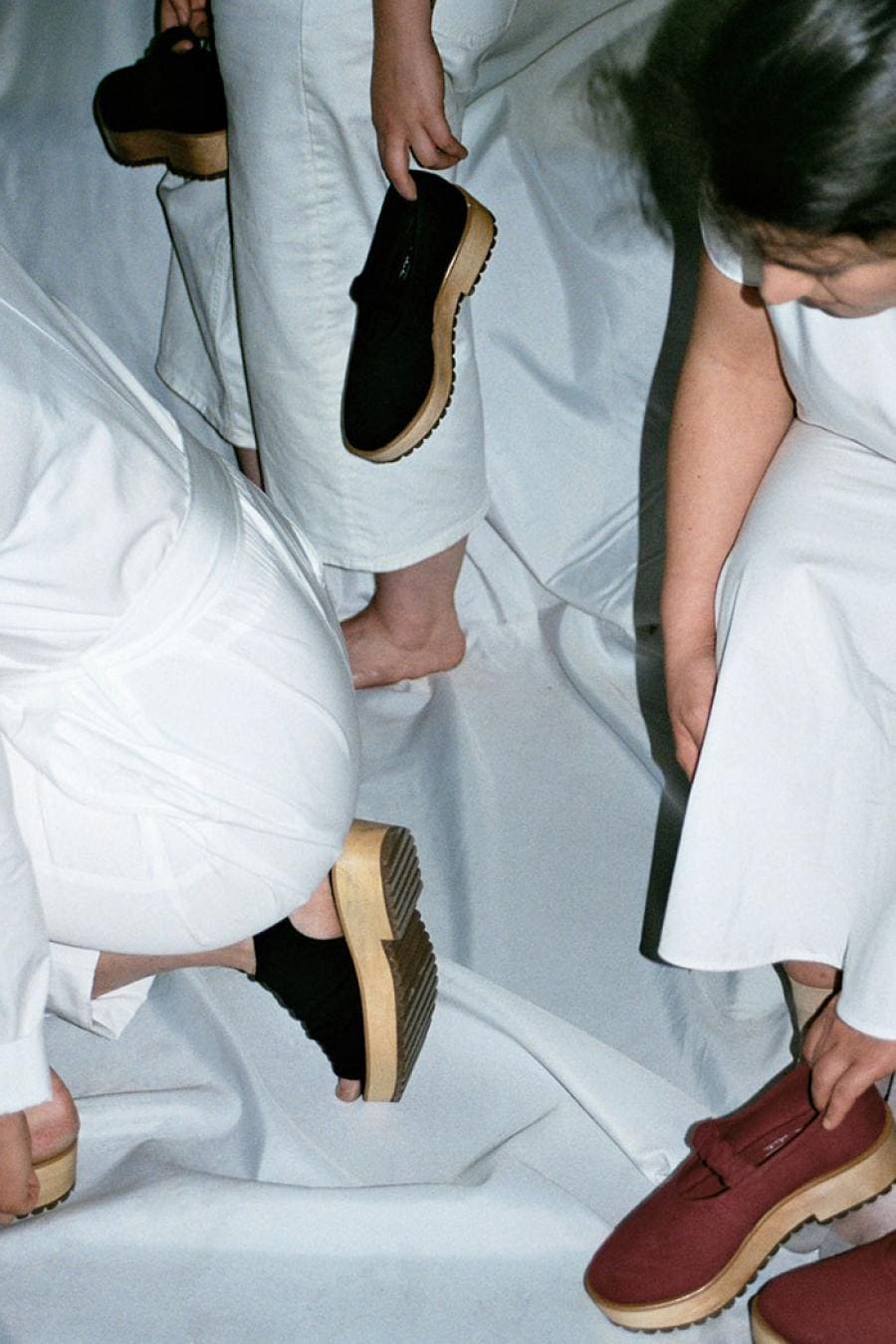
THE KINDCRAFT
How did your experimental footwear projects start?
Sara González de Ubieta Oliveros
I was restless about the use of leather in footwear since shoes had historically been mostly made in this material. If you work with it, you understand why: It’s a super noble material, very adaptable to the complicated shapes of the foot. It’s waterproof and breathable… it makes sense.
But when there's only one material in use, you notice the intense relationship between shape and the substance. If a new material appears, new shapes come with it. It doesn’t make any sense using old shapes on the new material because each one has a particular personality. That is something that happens a lot. For example, when cotton canvas started to be used in new designs, [designers] were using the old leather patterns. That blew my mind.
THE KIBDCRAFT
How did your first projects come to life?
Sara González de Ubieta Oliveros
After a couple of years learning with the master and doing small projects, I had an opportunity to create a collection with a Portuguese company. It was so enriching. The cool thing is that you understand the things that you can do on your own—with your hands, tools, machines—and the ones you can do in a factory. They have another technology and way of thinking.
Industrial production versus craftsmanship—where does each start and finish? Both of them use technology and machines. Take a look at the new digital craftsmen and actual makers. So, is it about quantities? Do we have to redefine the word "crafts"?
THE KINDCRAFT
How would you define it?
Sara González de Ubieta Oliveros
Technical knowledge that arises from materials. The craftsman have technical knowledge of a discipline—but they’re always expanding it by working with the materials: their command of wood, of leather. They have to understand both the materiality and the technique.
There's another interesting element in "crafts": The transmission of knowledge through master vs apprentice, a workspace, schools — and now even open source (commons). A designer works in a different way than a ceramist, for example. It doesn't matter if it's worked by hand or 3D printing; In both cases, it's worked by using matter and knowledge of a technique's discipline.
It is true, though, that nowadays the market is demanding crossover skills from designers and craftsmen.
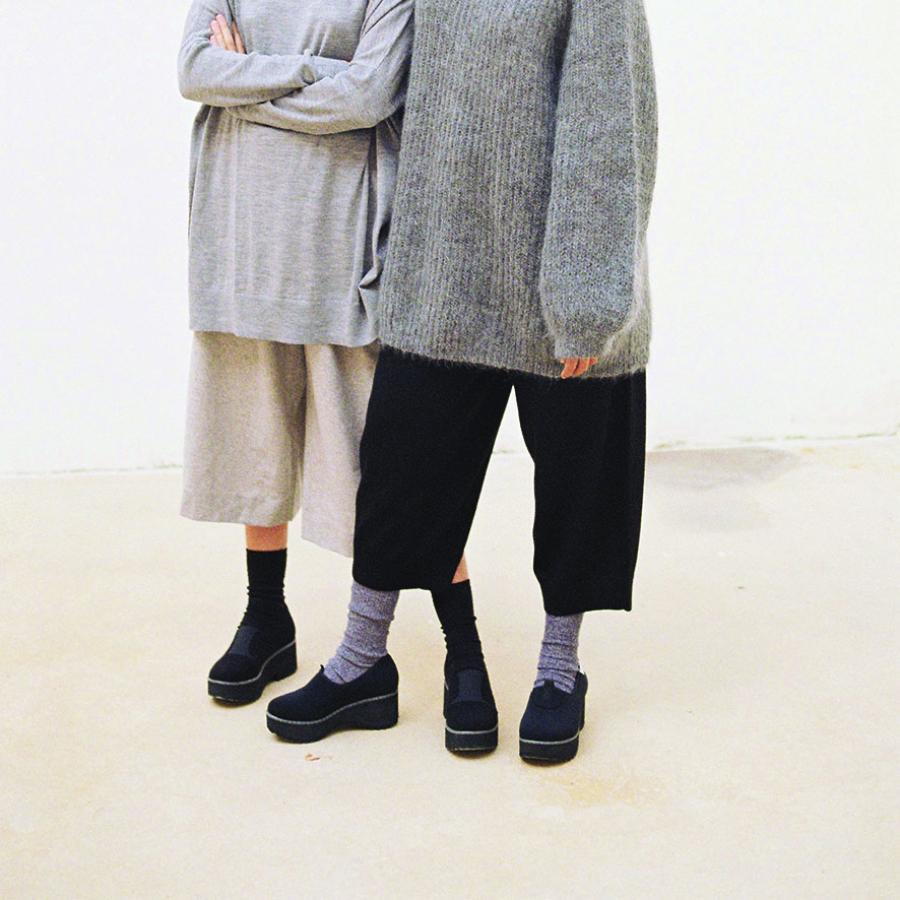
THE KINDCRAFT
What was the first material that you used in footwear?
Sara González de Ubieta Oliveros
During my first handmade collection, I worked with leather because I wasn’t brave enough to propose new materials. Later, I did a collection with leather but I did it without using the main patterns—just with the leather stratification, taking in account the layers of the skin like we have: dermis, epidermis, etc. On other collections I worked at the factory, I started using very simple ones like neoprene, or spacer. There I noticed that working with manufacturers means basically producing, not experimenting, unless if you are Adidas and have AdidasLab. That’s why I always had my workshop where I try to innovate with materials on my own. Since 2016, the projects that have come to me are basically related to formal and matter experimentation.
THE KINDCRAFT
Can you tell us about some of them?
Sara González de Ubieta Oliveros
I did a project called “Matter as a Shape” for BCN Producciò with MaterFad, a materials library in Barcelona. What I was doing was looking for materials from other industries, mainly the building sector, and trying them in experimental footwear. So I contacted several providers. They lent me some samples and, after trying to understand their behavior, I tested the possibility to do any kind of shoes with thos properties.
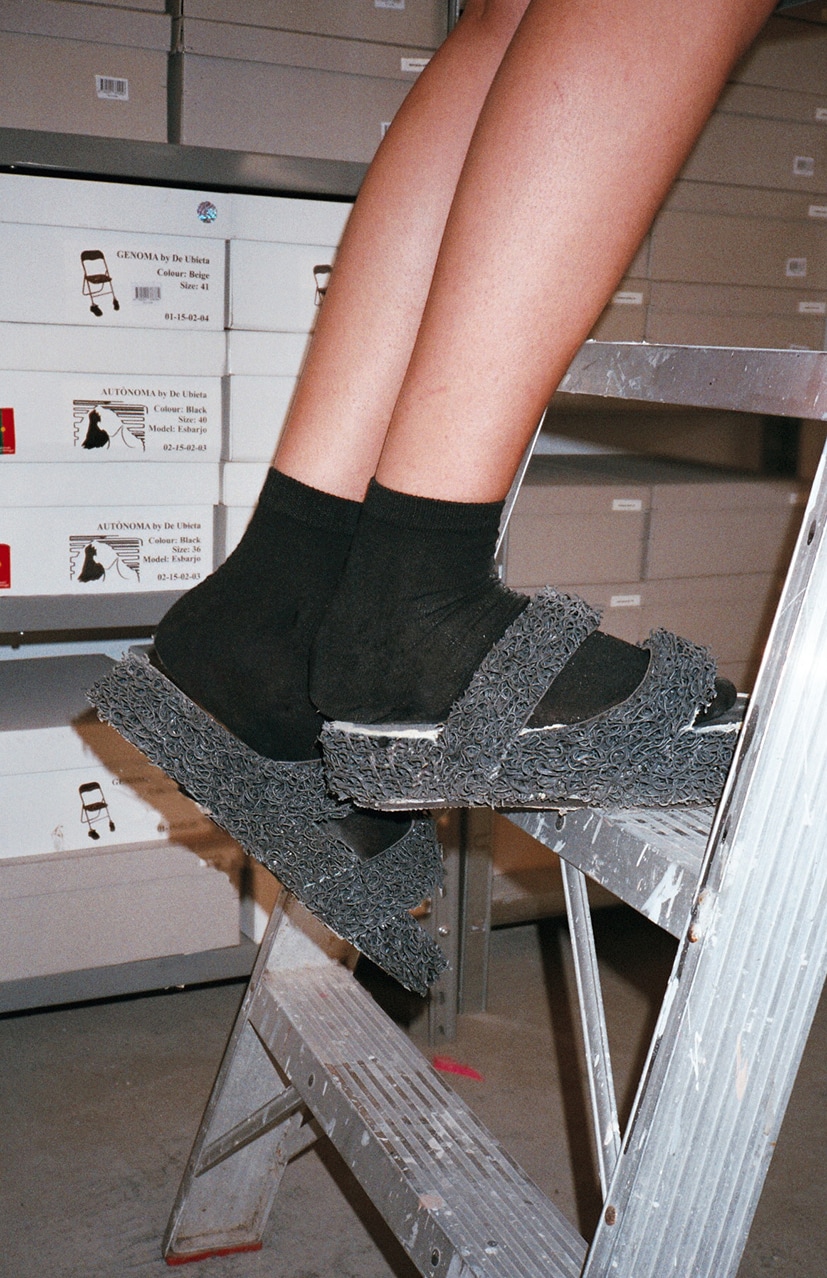
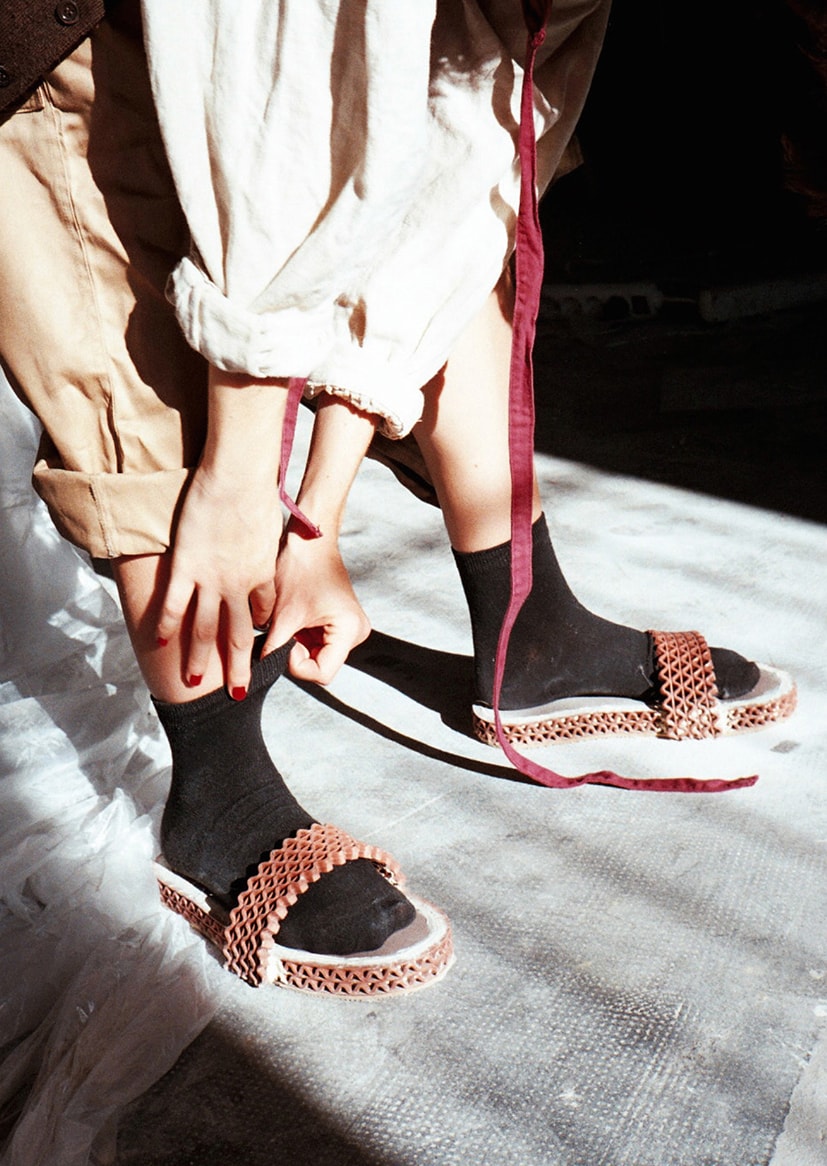
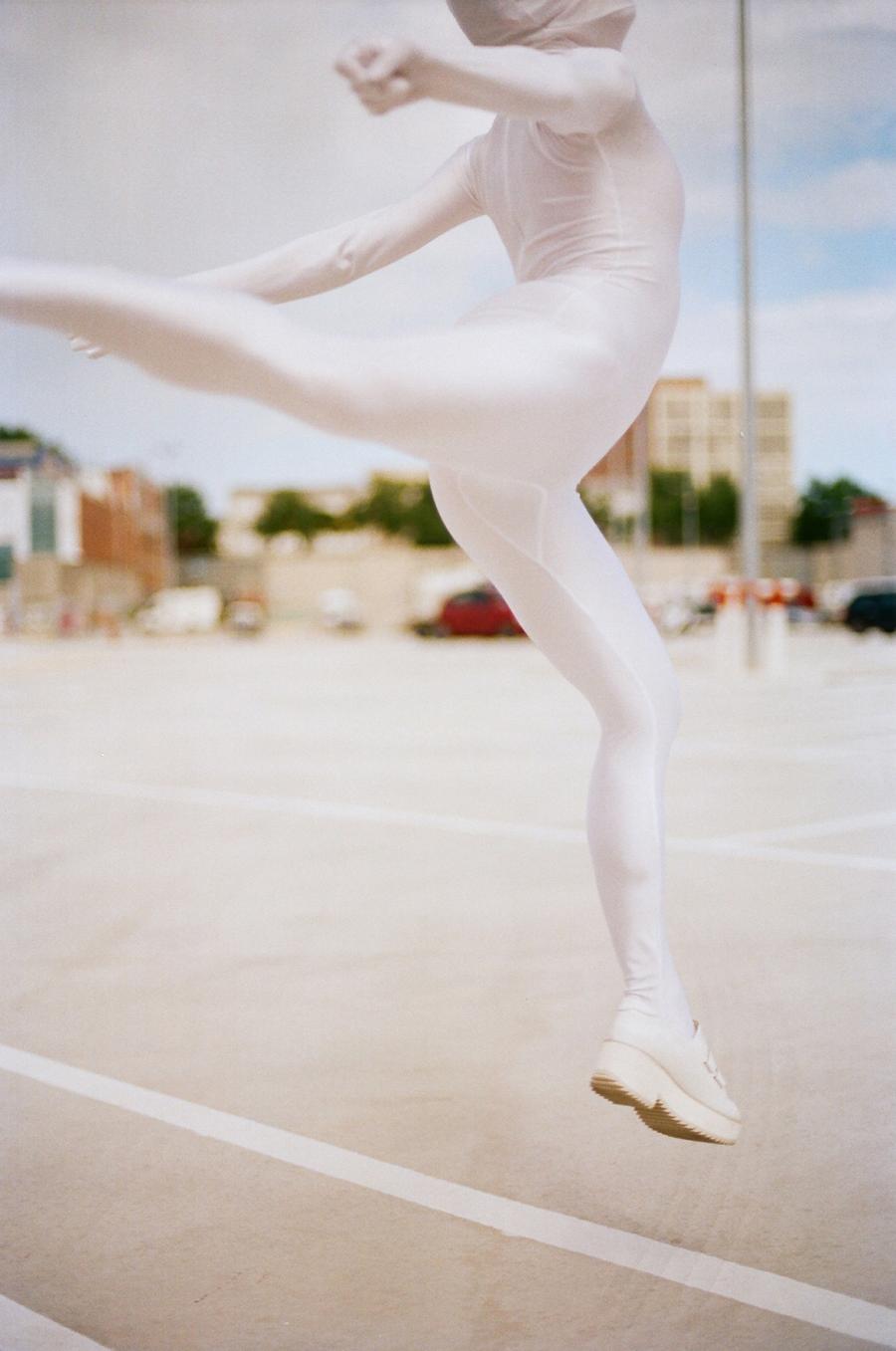
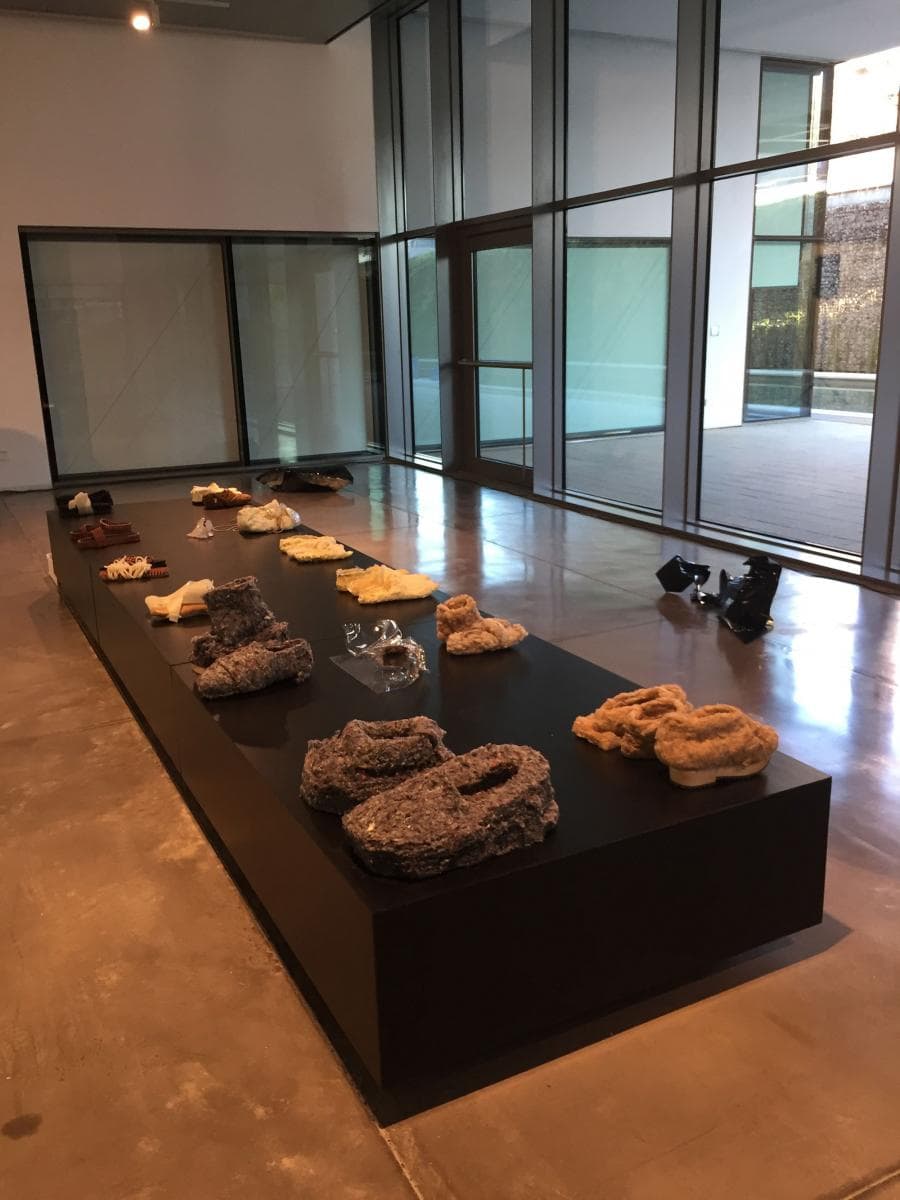
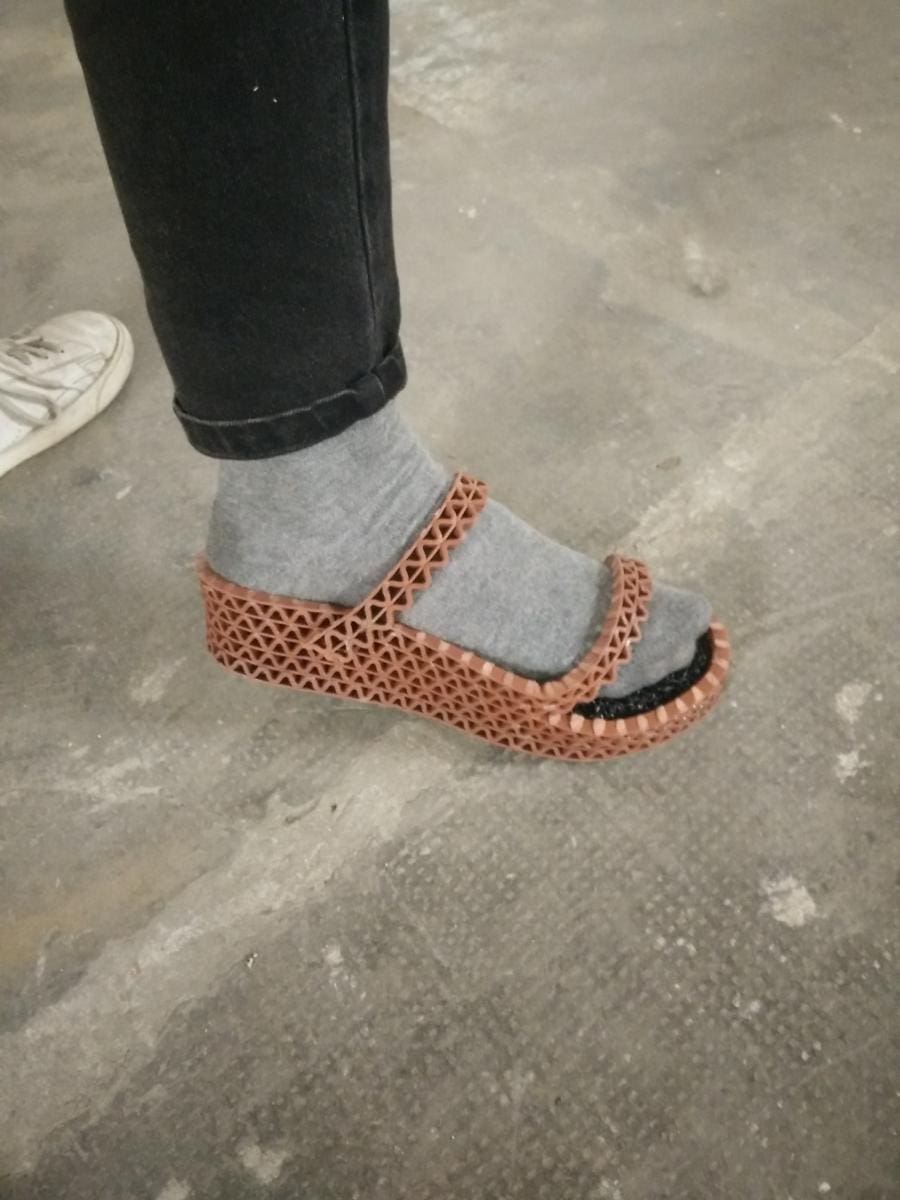
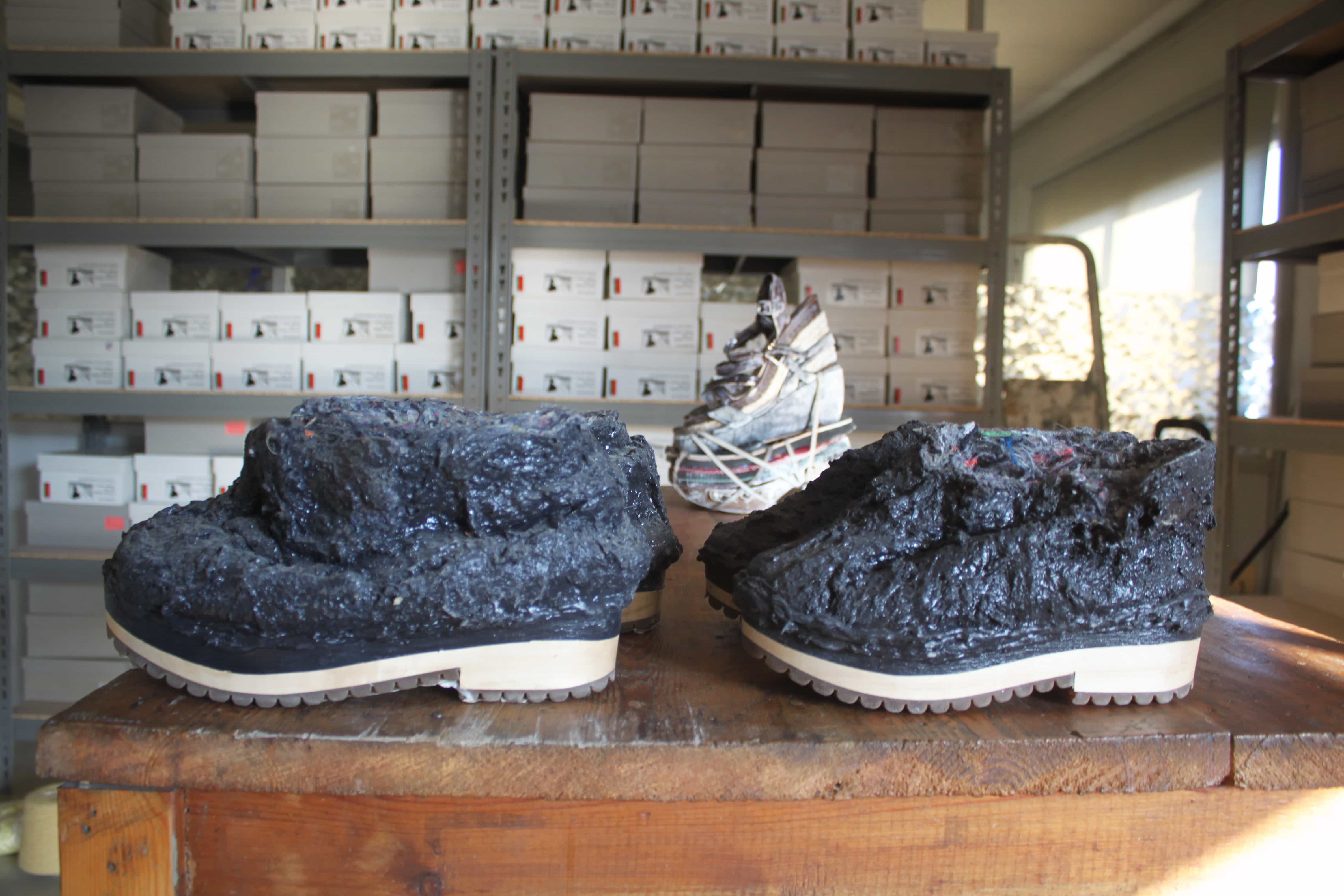
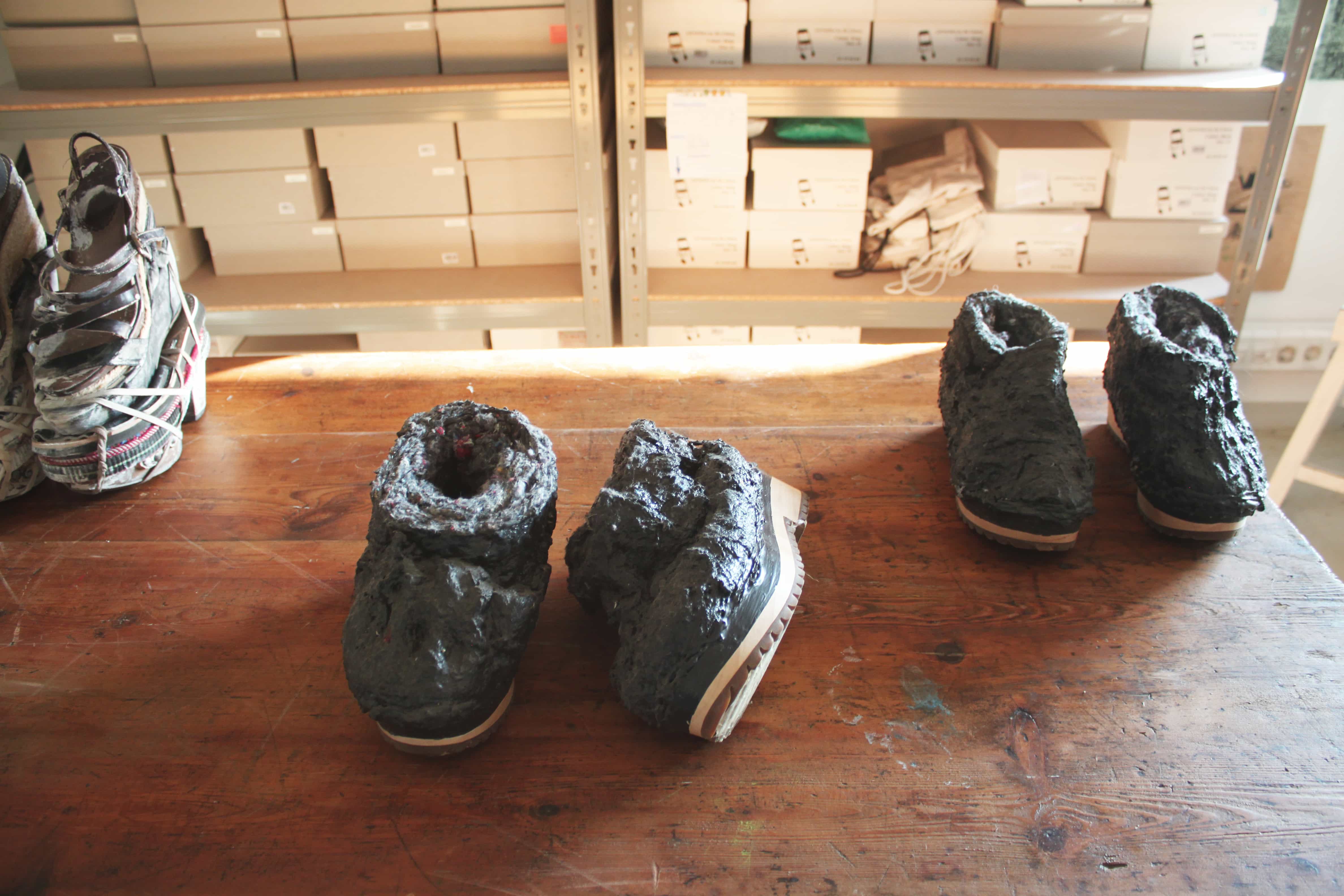
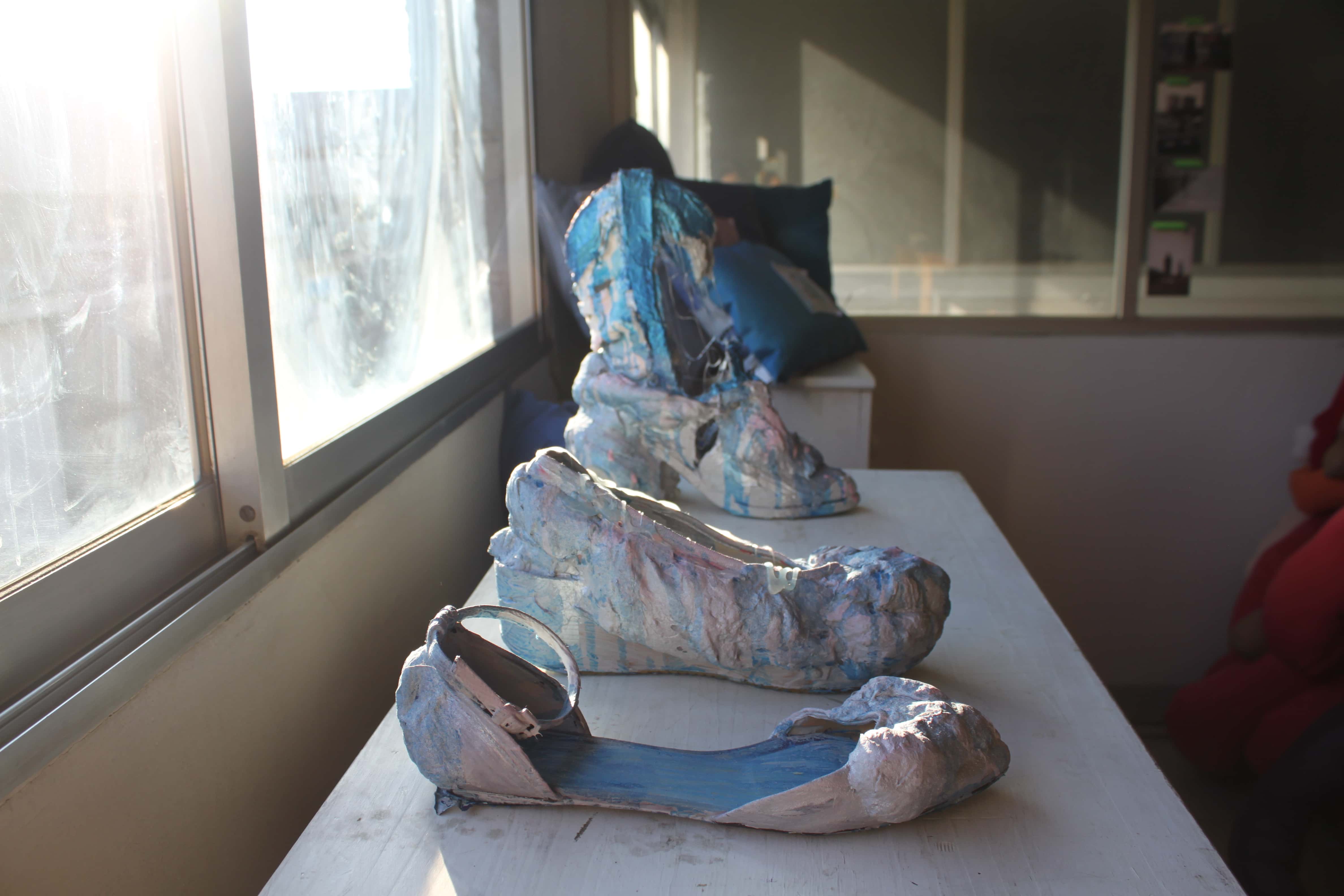
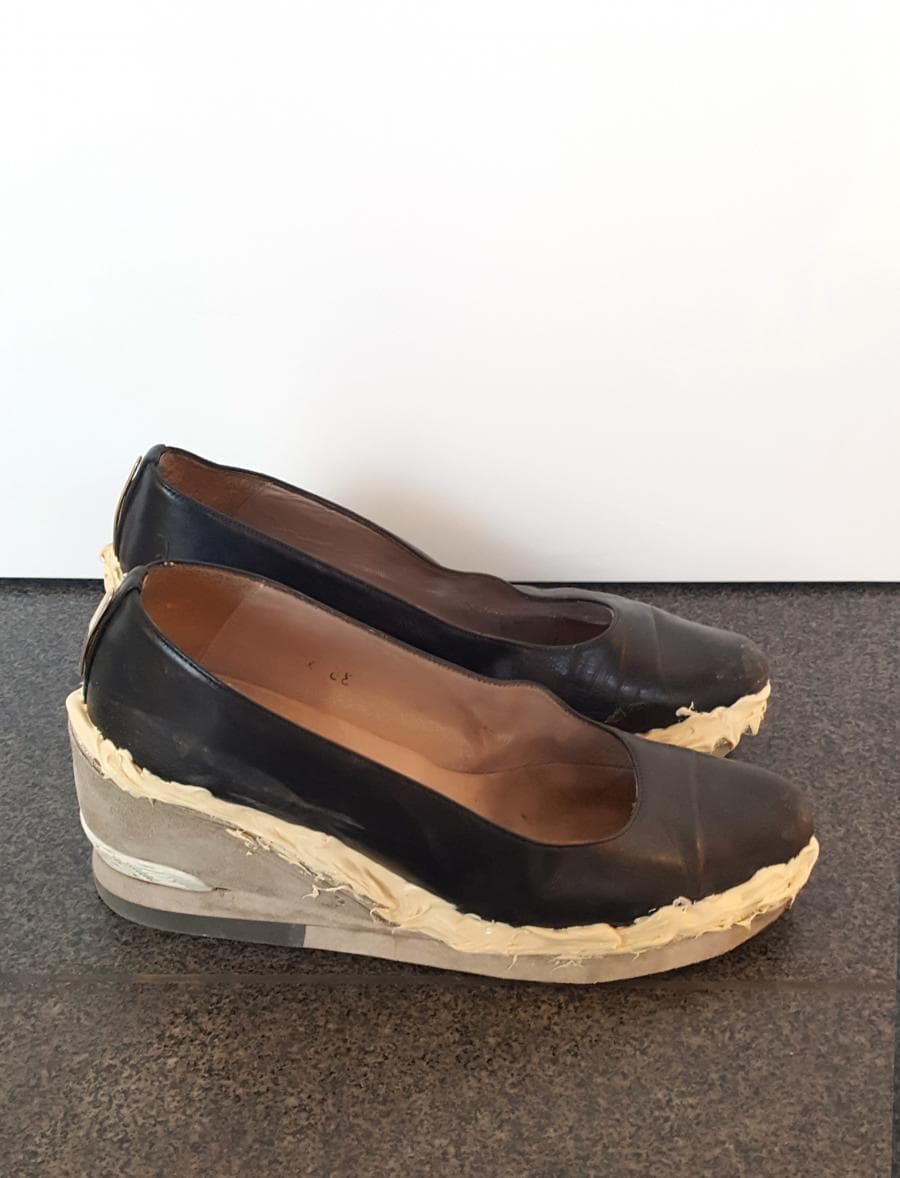
For example, I made some with pavement, with insulators... with scraps of Aramida, a commonly-used material in the military industry. The cool thing about Aramida is that you can recycle it and turn it into pulp. It has a very long life. I'm very interested in circular economies, taking the scraps and wastes from one industry to introduce them in another one.
THE KINDCRAFT
How was the process of testing with providers?
Sara González de Ubieta Oliveros
It wasn't easy at all but, in the end, it depends a lot on the person that you find on the other side. Some are really kind and, from others, I didn’t even get an answer. For example, these shoes were made with a thermic and acoustic insulator for dwelling. The provider had grated used fabrics of cotton from different garments and had it as raw material, giving it then fireproof and antibacterial properties. It was amazing to see how they had created the recycling process, the specific machines for deleting the buttons, the metal pieces, the trimmings… It was really cool. The final material was a non-woven that I used without patterns since the material works as a whole.
But the best thing was discovering this small industrial factory and its process that they were not publicizing not even on their website
THE KINDCRAFT
You said that circular economies and upcycling interest you. Apart from this research project, where else did you apply it?
Sara González de Ubieta Oliveros
In a project called “Amorf Etern” with the Massana School of Arts & Crafts. I bought 30 kg of used shoes and I analyzed which parts were worn away, deleting the ones in bad condition. It was really interesting because, at the end, I was exploring a small sample of a community. I studied the functional parts and the ornamental ones and I mixed them up. For example, I mixed a sneaker and a sandal, deleting all the damaged parts of one and another and joining them in a way that the structural parts of the new sandal were the ornamental parts of the old sneaker.

Later on, I was called to make a workshop at The Marathon event held by Elisava School. Did you know that it's possible to spray cork? When I learned about it, I realized that the spray process had a lot of possibilities! Spray is normally used only as a recovery, but then I realized I could pulverize this table, for example, and transform it in something totally new. It is a mix between density and granulometry. I decided to make a workshop to explore this.
From this idea, I came up with another project called “The Rebellion of Objects”. Several artists were taking part of the project in order to create an event with different results. The idea of the project was thinking about objectuality, taking in account several considerations like the use of waste and the life of the objects. I wanted to create a machine since at that time I had been working with several makers. My concept was to reflect on the machine as an object and the love for the machines. So I contacted a printing house, collected all their wasted papers used for making printing tests, and transformed into something nice. Because if you just change the shape of a waste, it can become a desired material — like confetti.
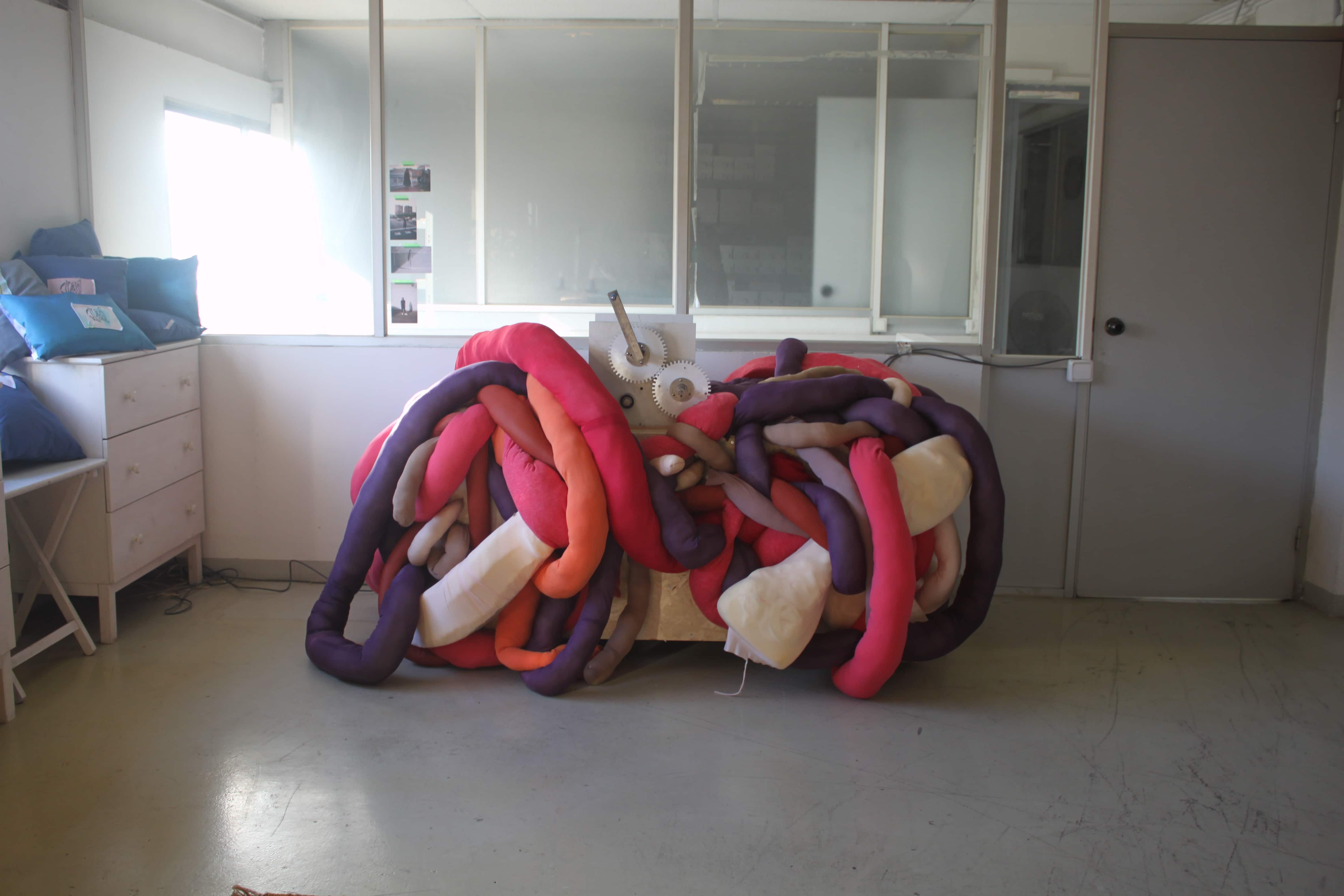
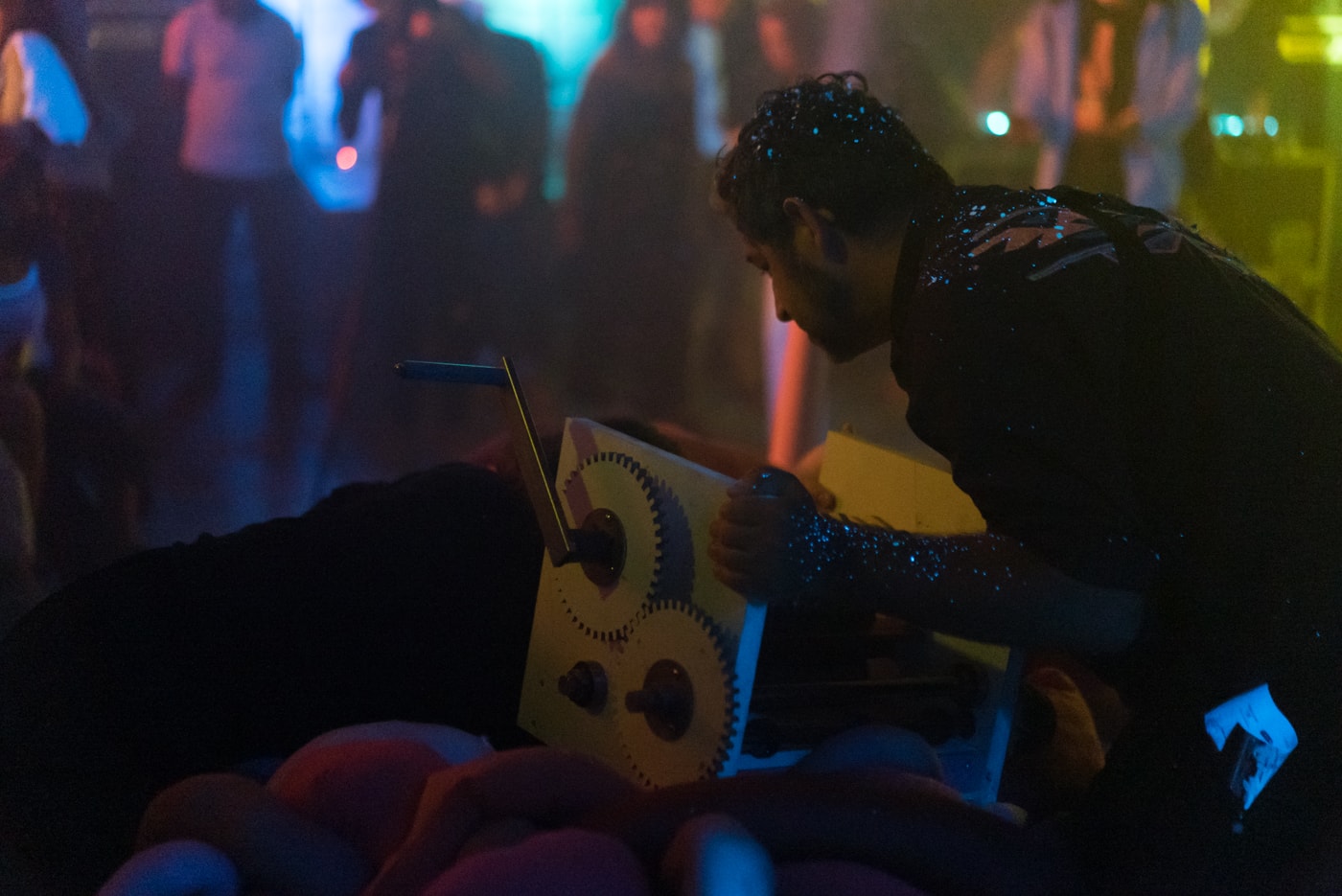
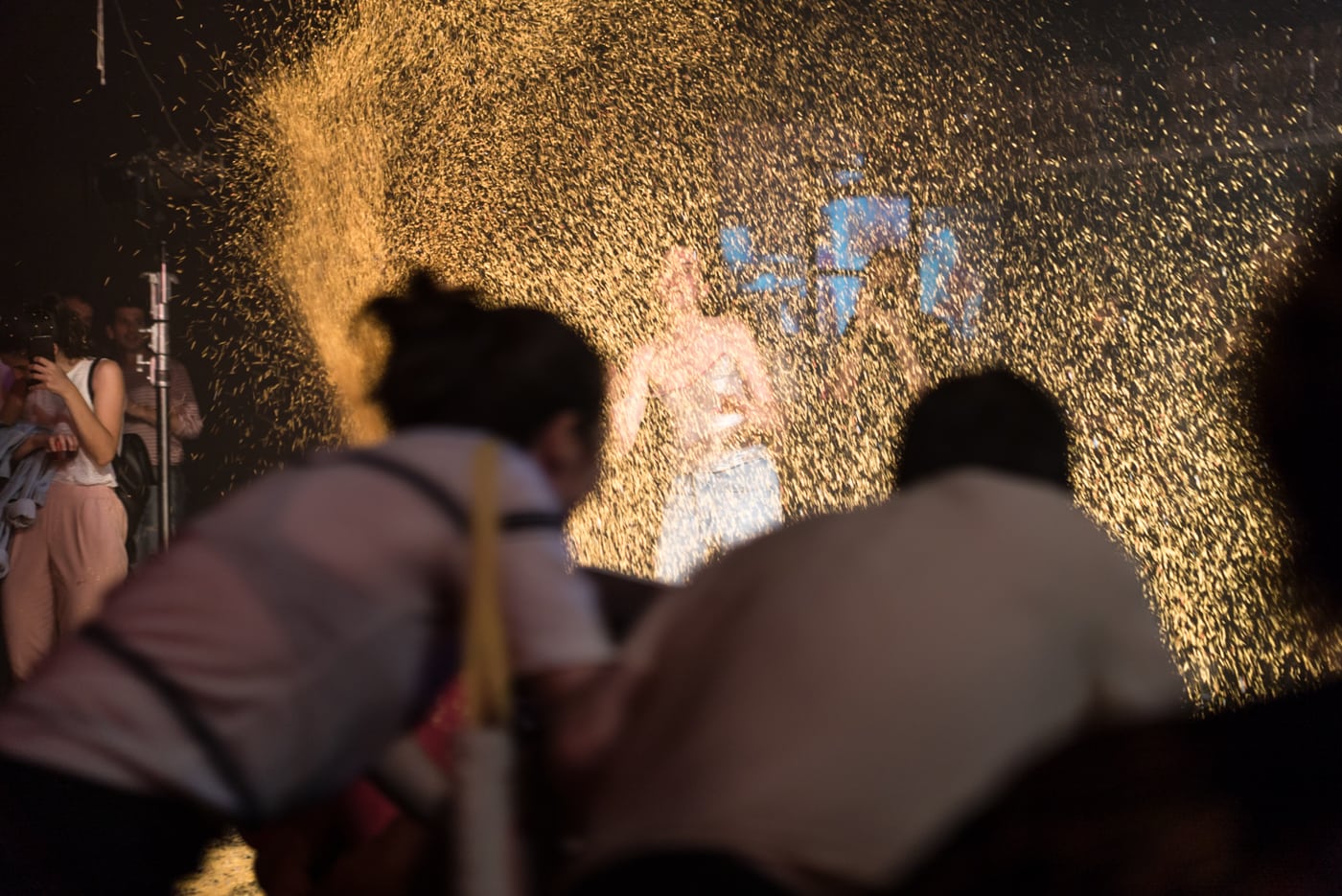
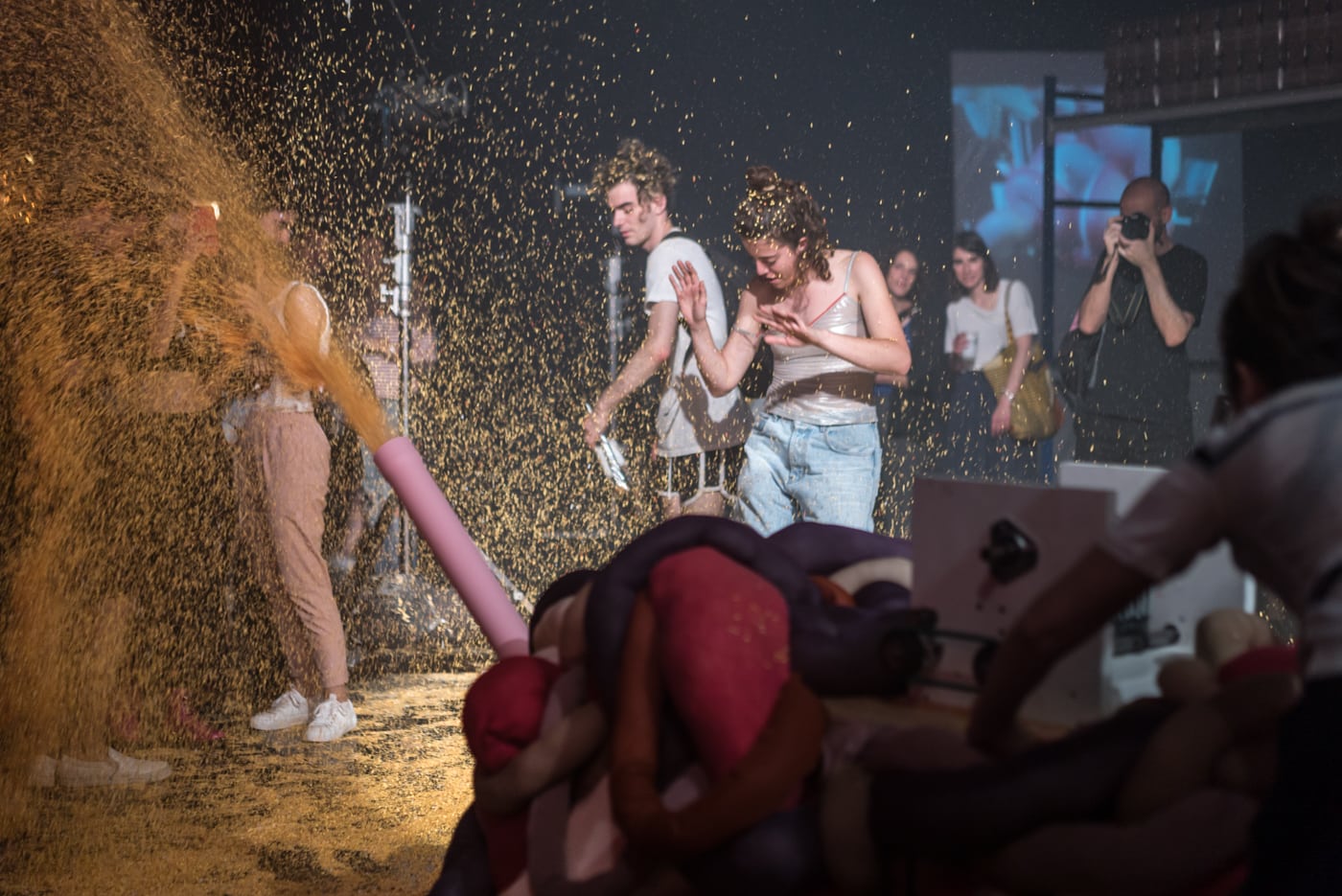
In another situation, I used waste wood beams from Portugal to make the soles in a shoe collection.
THE KINDCRAFT
Have you ever worked with natural materials?
Sara González de Ubieta Oliveros
I made shoes with fungi, but the actual problem is that they are working with it as a leather—as a substitute—but it doesn’t behave like that.
We should see it from a different angle: Look at the matter’s personality and create from there. I understand that usually you look for the solution of a problem, so substitutes appear: The problem of plastics, of leather… but you cannot apply the wisdom of the original material to the new one. If you use new materials, you [can] find awesome formal results.
THE KINDCRAFT
Between your experimentation and diverse projects, what would you call yourself?
Sara González de Ubieta Oliveros
A craftsman, though I am interested in matter research. The shoe technique was just a means for testing. Sometimes there is a very thin line between the art and the design. Not everything must be product… there’s always other people interested in producing. I really enjoy the first phase of the creation.
THE KINDCRAFT
What do you see for yourself in the future?
Sara González de Ubieta Oliveros
Just to keep on trying, researching. Jumping between crafts, art and design.
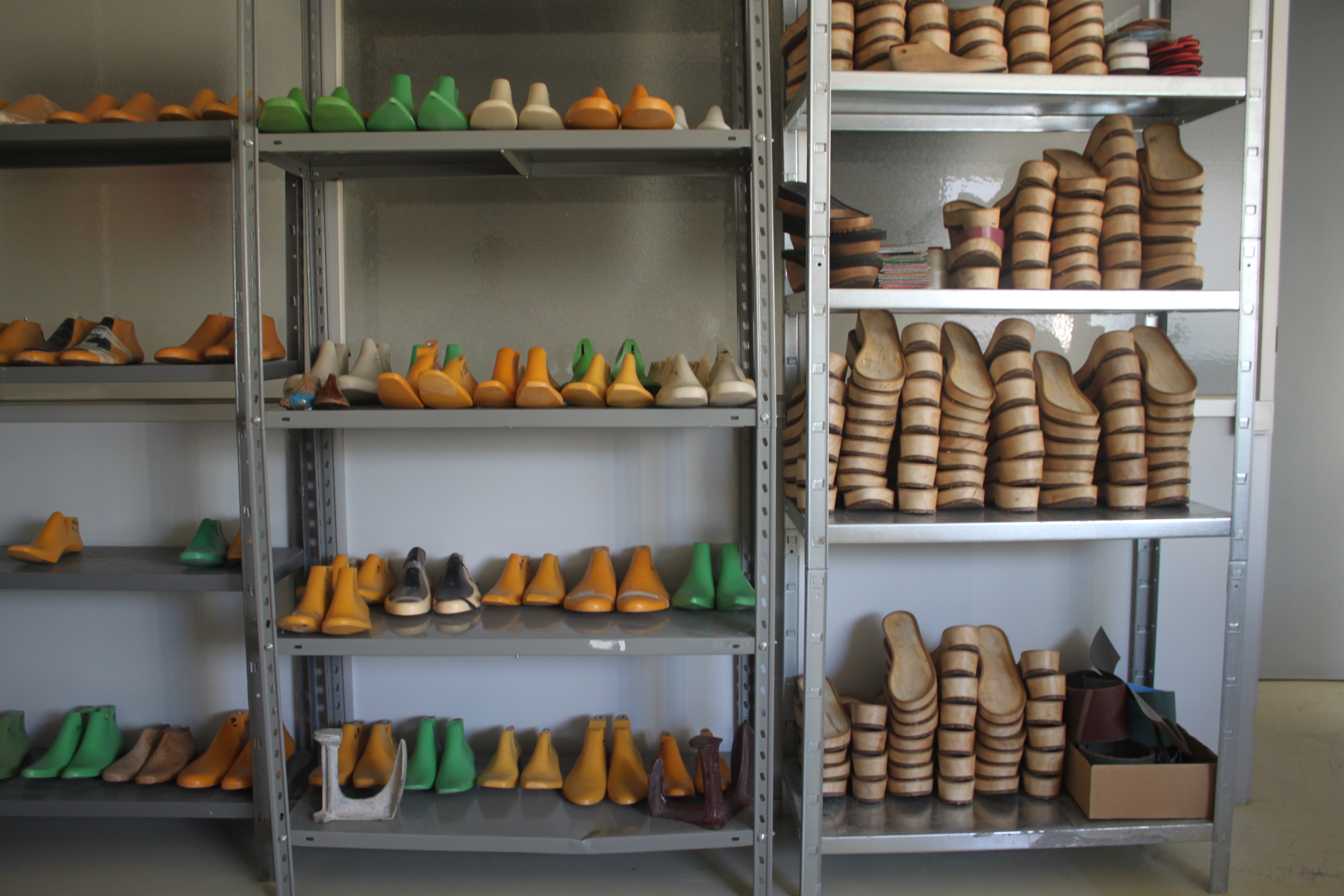