Dutch Design Week (DDW) is the largest design event in Northern Europe, showcasing the work of over 2,600 Dutch and international designers. Held in locations throughout Eindhoven, the event reflects the industrial makeup of the city — a place where experimentation in process is very much at the heart of the creative journey. The theme of the 2019 edition of DDW (October 19th–27th), “If not now, then when?”, felt particularly relevant, echoing a growing urgency for consideration of the environment in design and production.
Contributor Fiona Coleman attended DDW for THE KINDCRAFT and has selected her top ten projects of 2019. She saw a number of trends at this year’s show: A focus on natural materials from the Earth, agricultural by-products being put forward as an answer to eco-problems, alchemical combinations of resources used for burning and heating, and self-care — both reflection and play — explored as a means of escape.
The Growing Pavilion
The Growing Pavilion housed projects with bio-based material innovation. The space was covered in mycelium and the floor, together with most of the furniture, was made entirely from bio-laminated cattail, harvested in northern Netherlands. On display within the Pavilion were products made from flax, algae, horse manure, and mycelium. The humble mushroom’s powers of regeneration were also celebrated with a daily harvest of the growing display when, every day at 3pm, visitors could try, take home, or eat them from the on-site food truck.
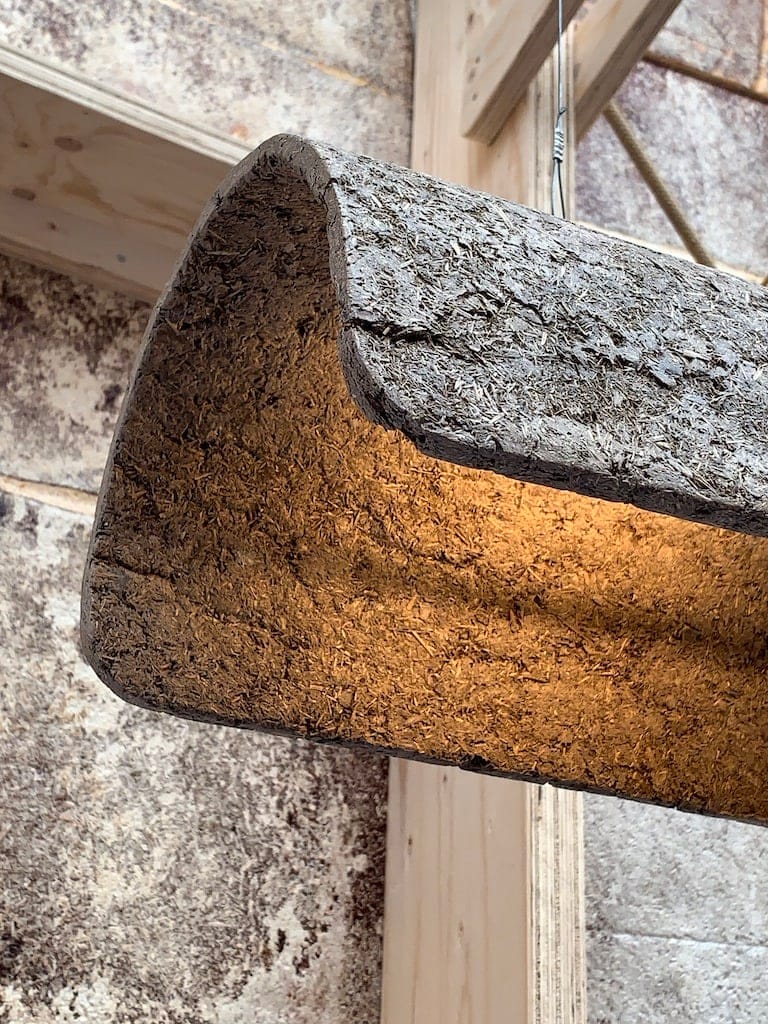
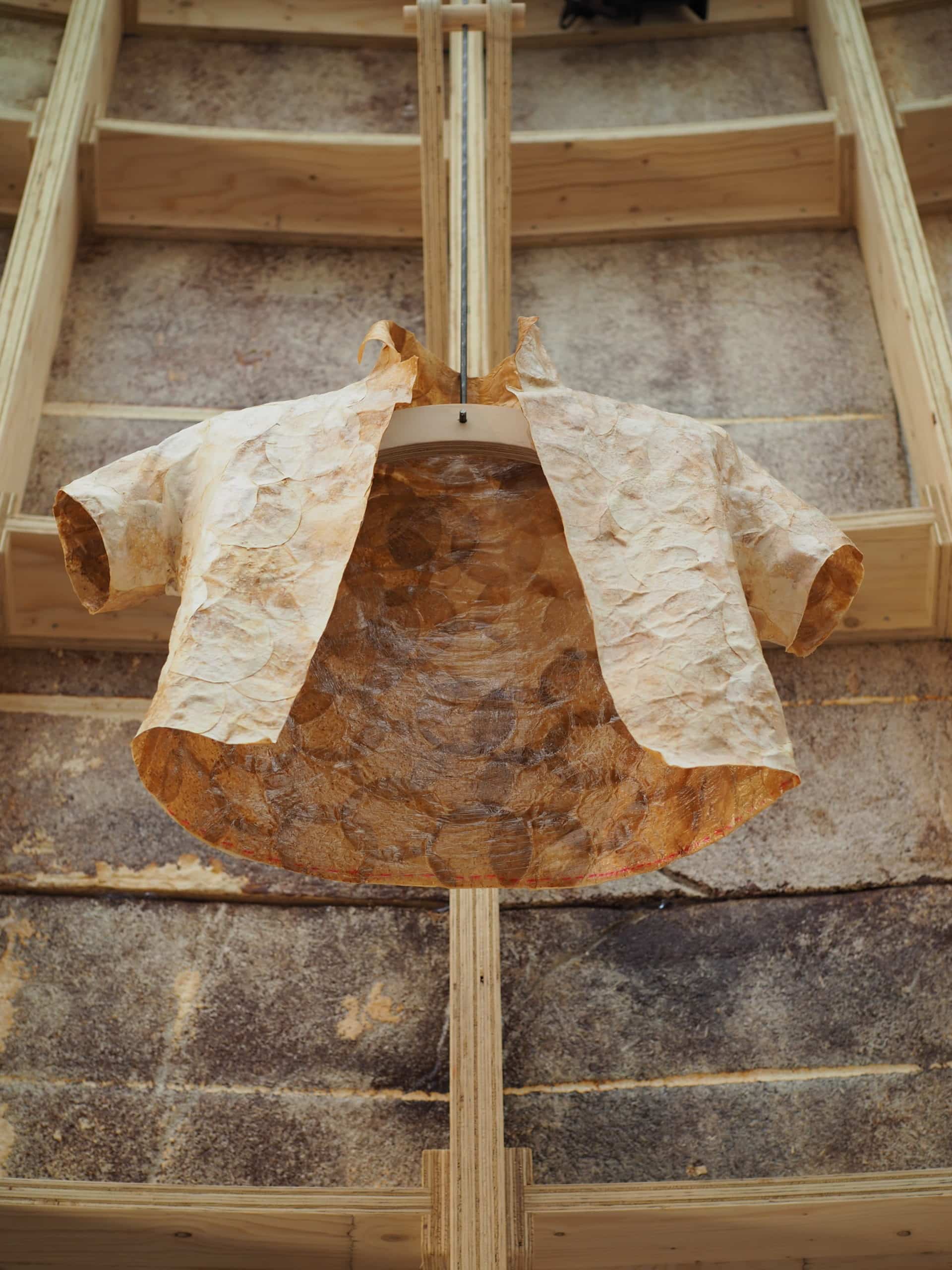
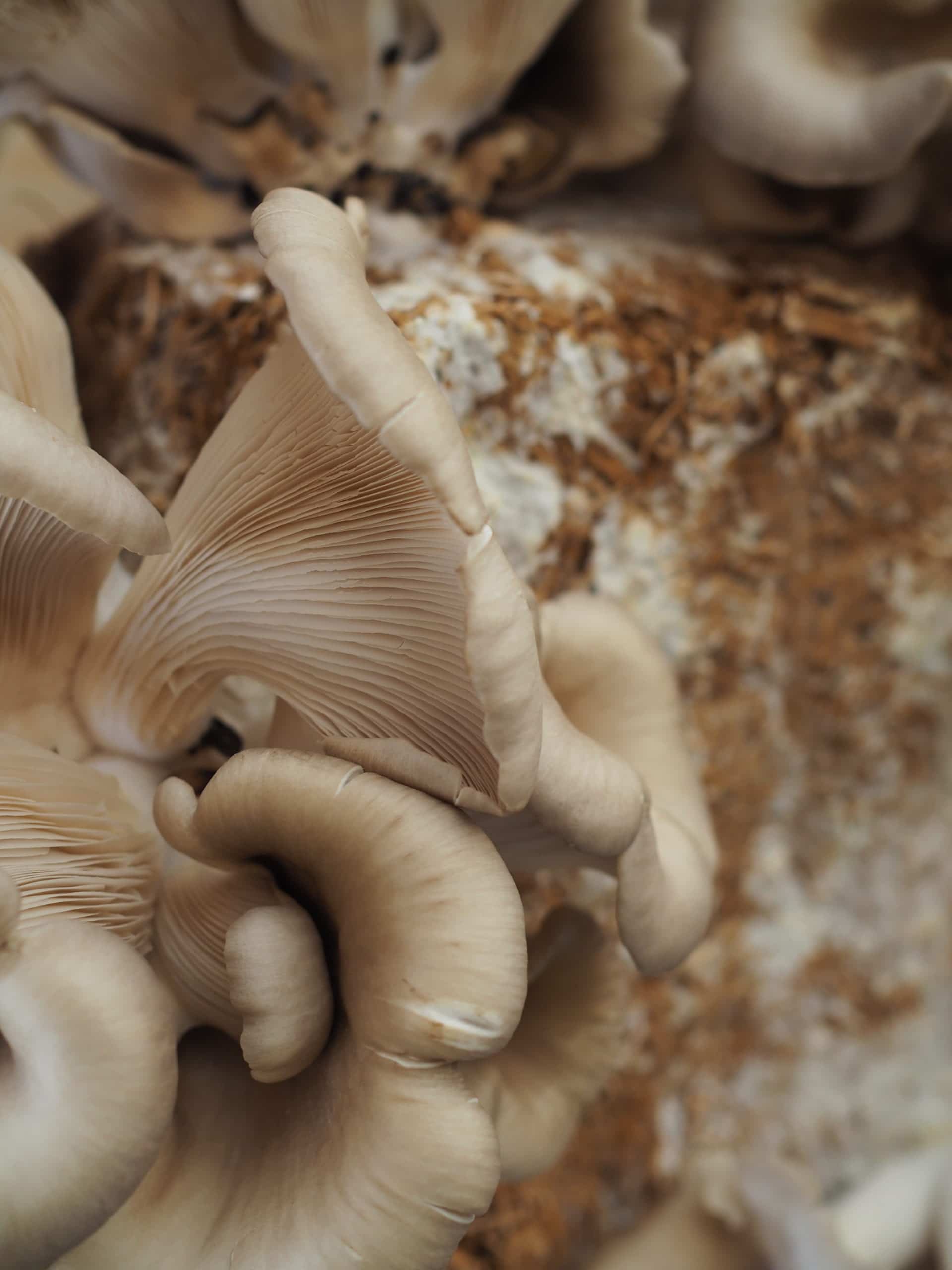
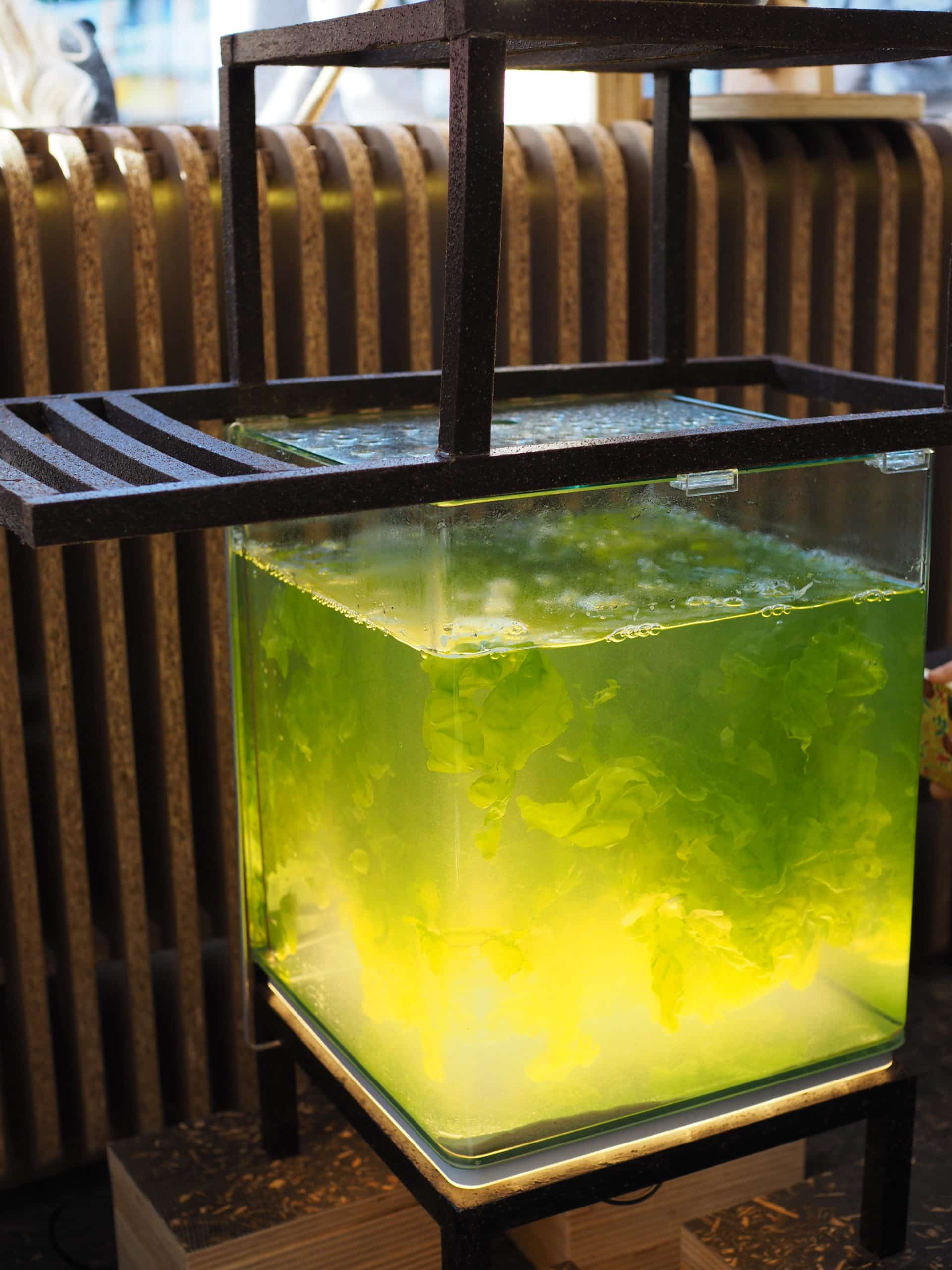
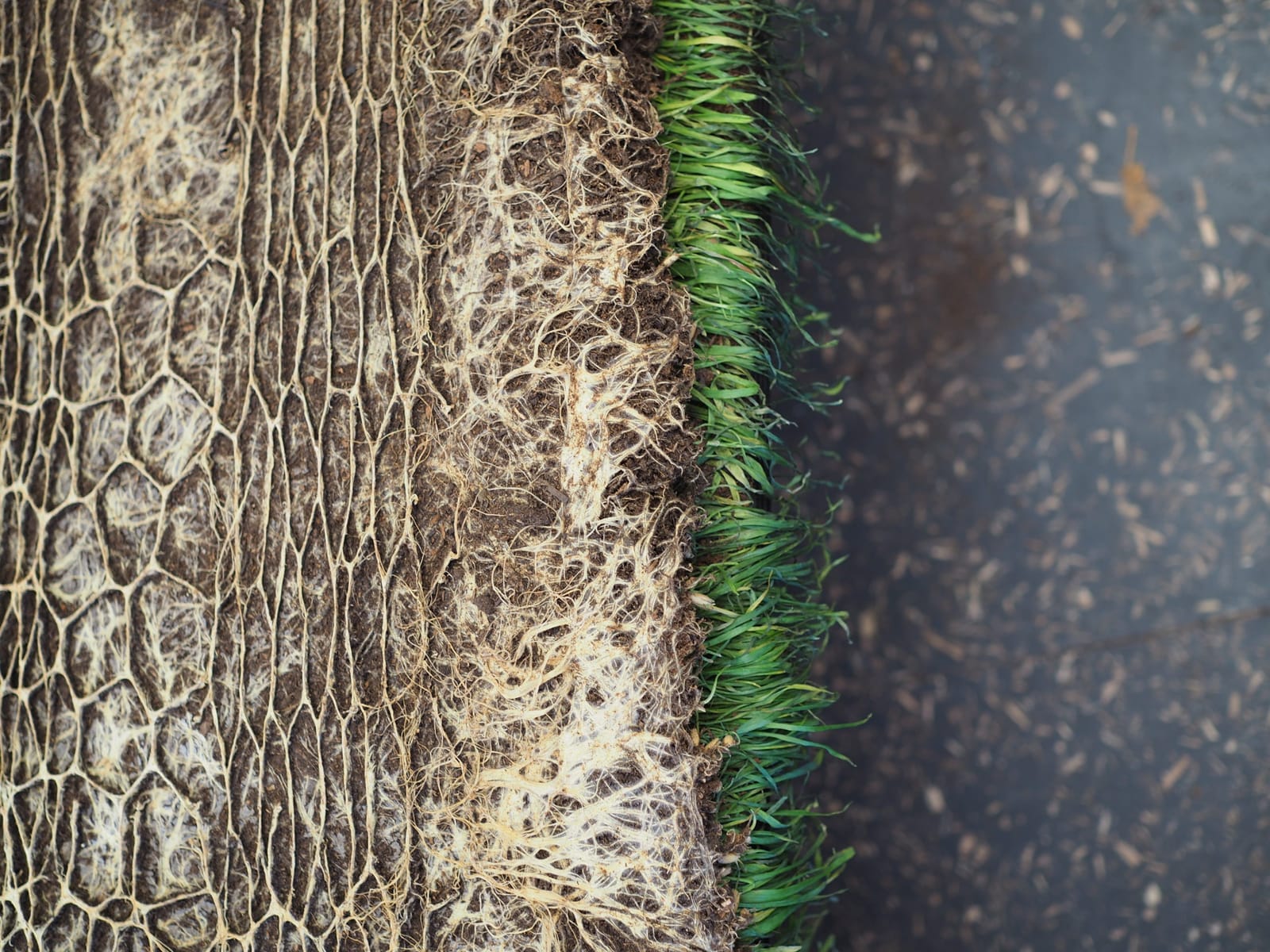
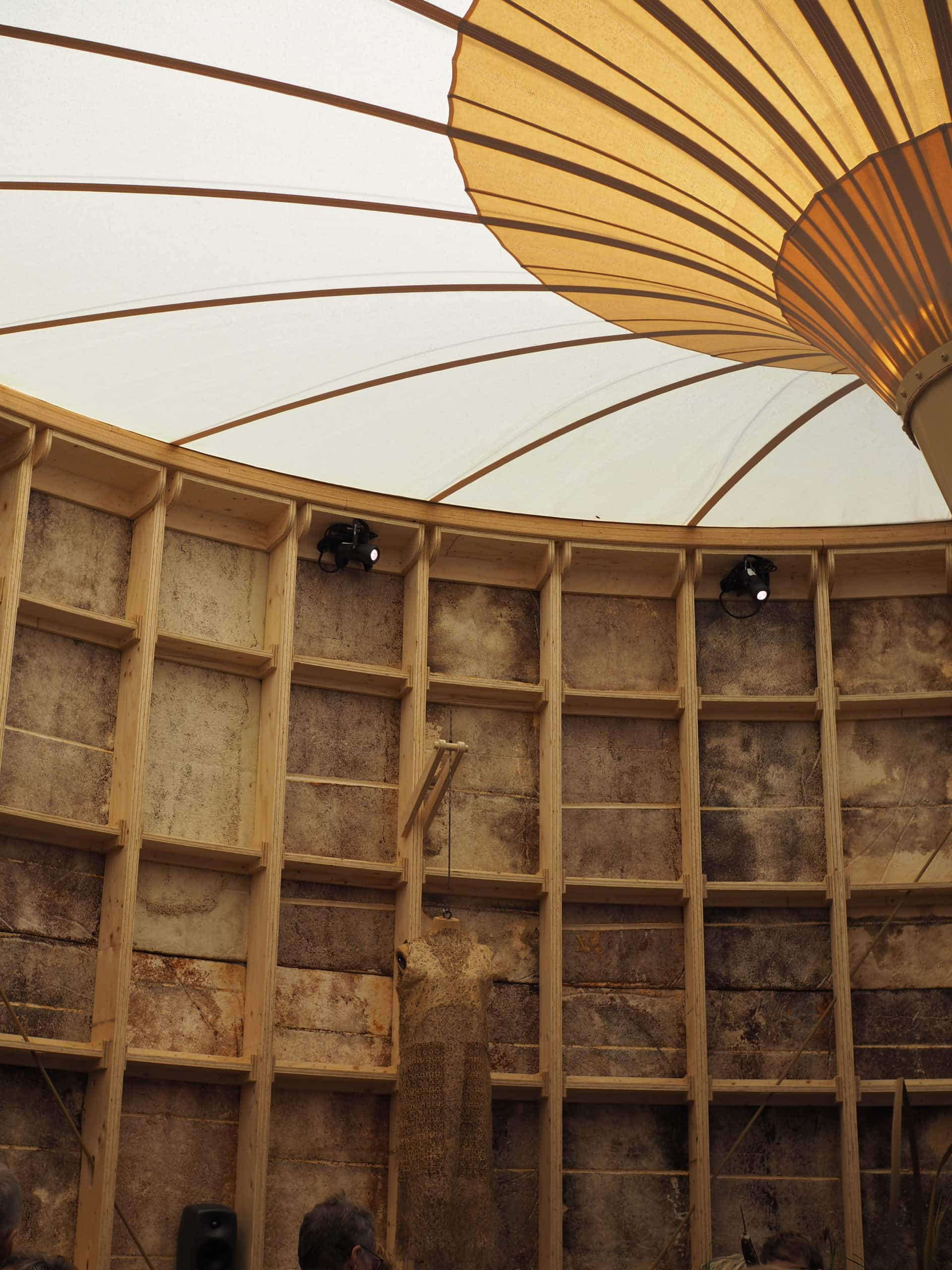
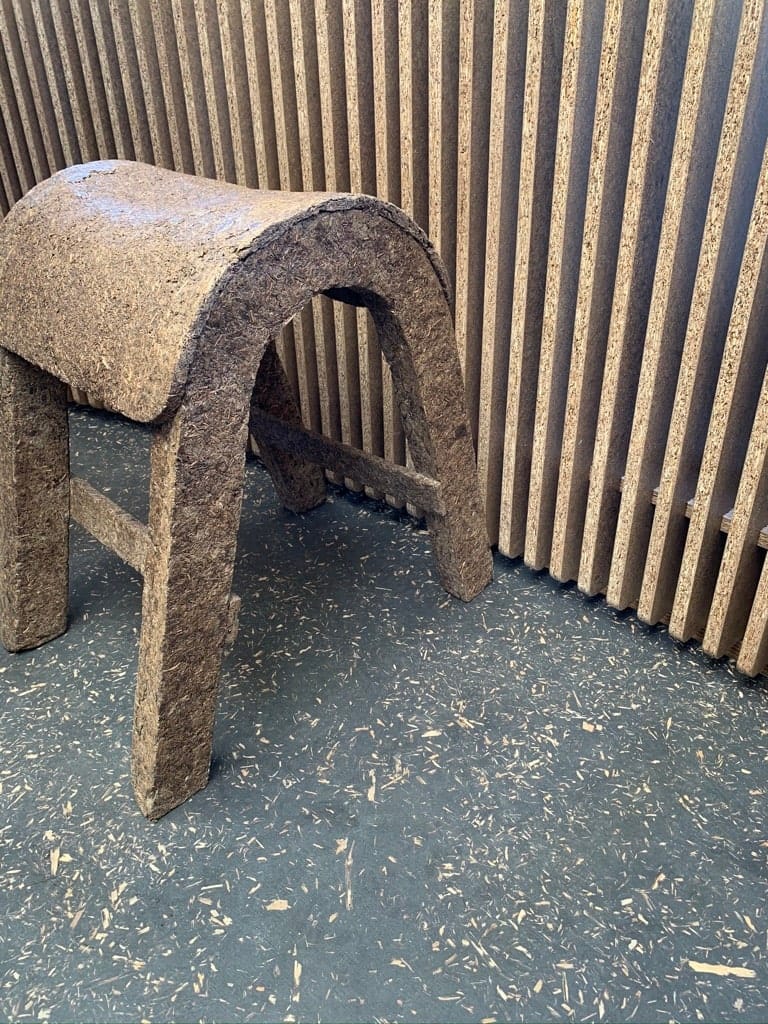
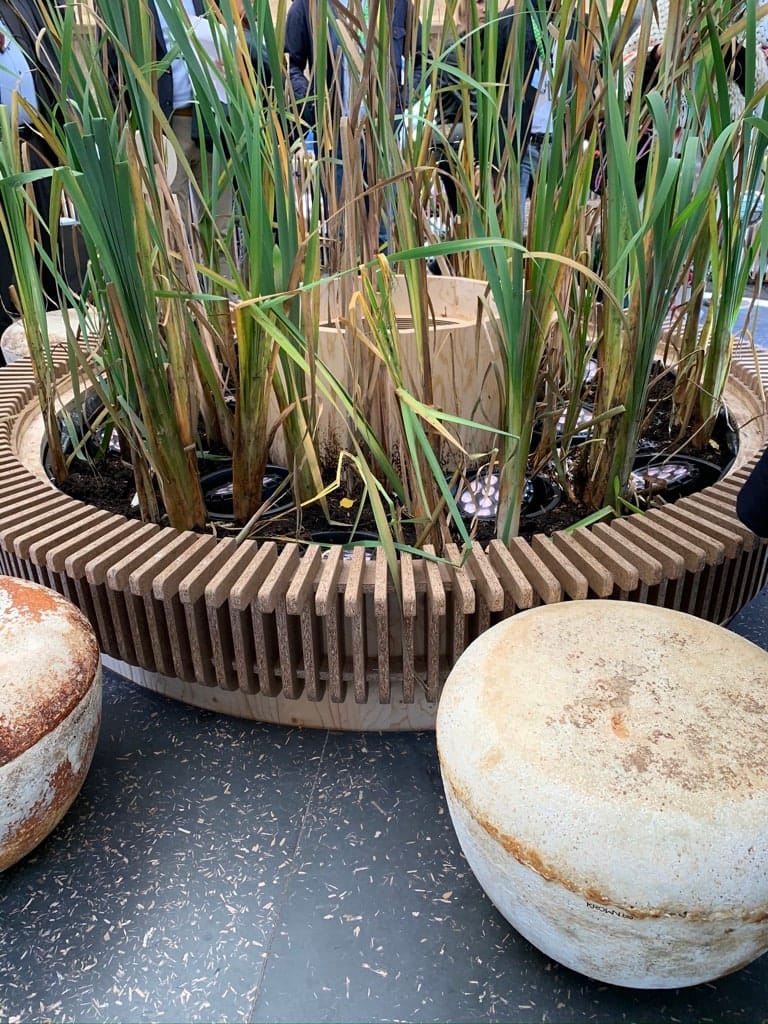
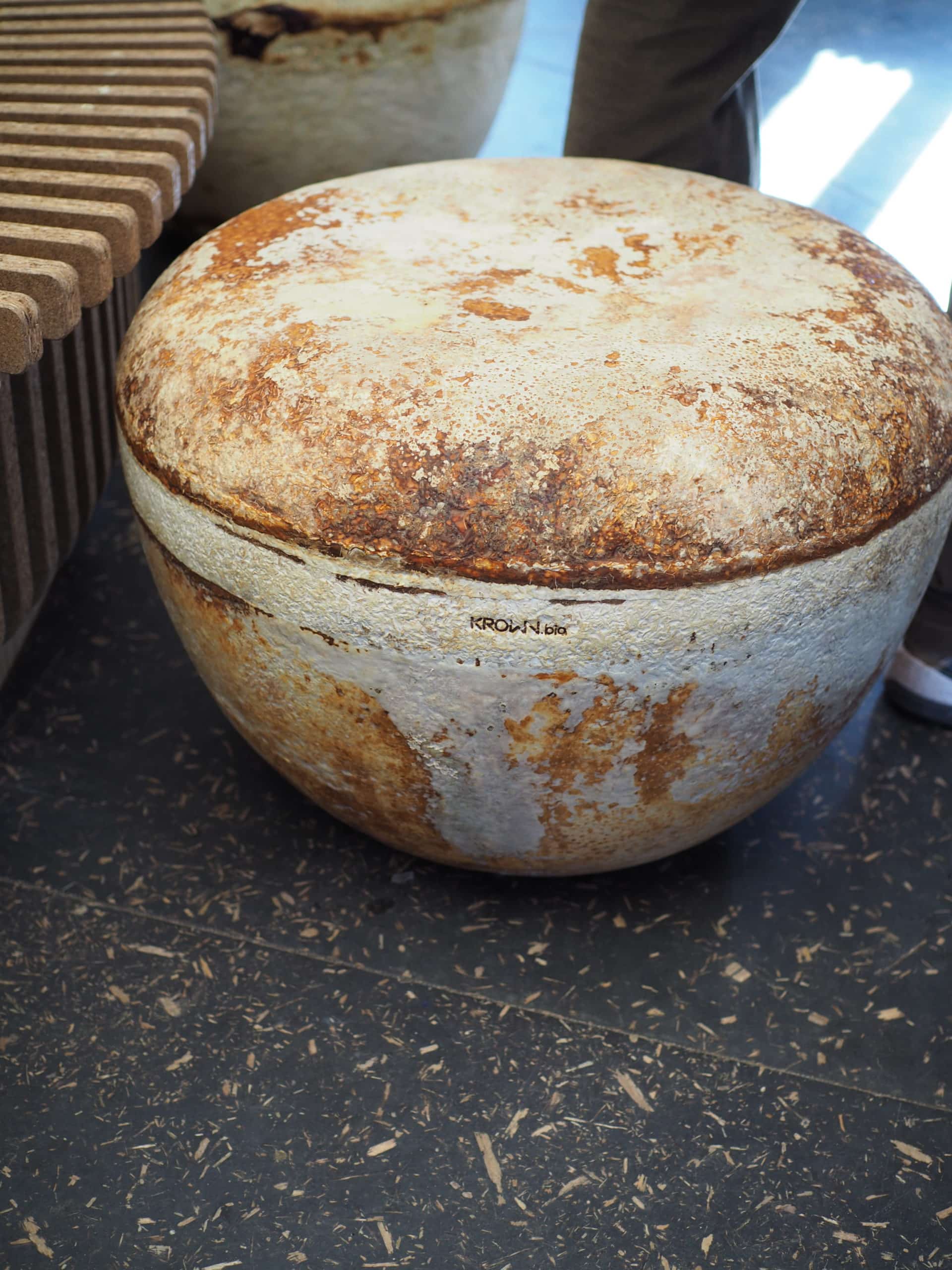
Featured designers included Aniela Hoitink, whose "Living Skin" investigates new materials, focusing on the behavior of mycelium, kombucha and algae when worn next to the human body. For the project ‘interwoven’, Diana Scherer shifts between disciplines—from design and art, to craft and science—while collaborating with biologists, engineers and designers to make her visions come to life. Christien Meindertsma’s Flax Chair is made of a new composite material, created using four layers of an existing woven flax textile and five layers of a newly developed dry needle felted flax. The soft pile of fabrics is heat pressed, melting the flax and PLA (a biodegradable plastic) into the shape of a rigid chair. In October 2018, Klarenbeek & Dros won the “New Materials Award” with their five-year research into biopolymers from algae and seaweed. The seaweed in The Seaweed Cabinet serves as a food source and as an air filter, with the end product being recyclable, compostable, and circular.
Scraped Earth by Rino Claessens
For his Design Academy Eindhoven graduation project, Rino Claessens used his own production method and tools to create five ceramic stoneware stools in five textures using five different clay types. After researching how ceramics are produced, Claessens discovered that the applications were limited to a certain size. So he devised a way to increase the size of production and expand the limits of the material. As a result, his designs make a physical connection with the body, offering a tactile experience. By reversing the usual technique of slip casting around and scraping clay over an inside mold instead of pouring onto an outside mold, he discovered new possibilities.
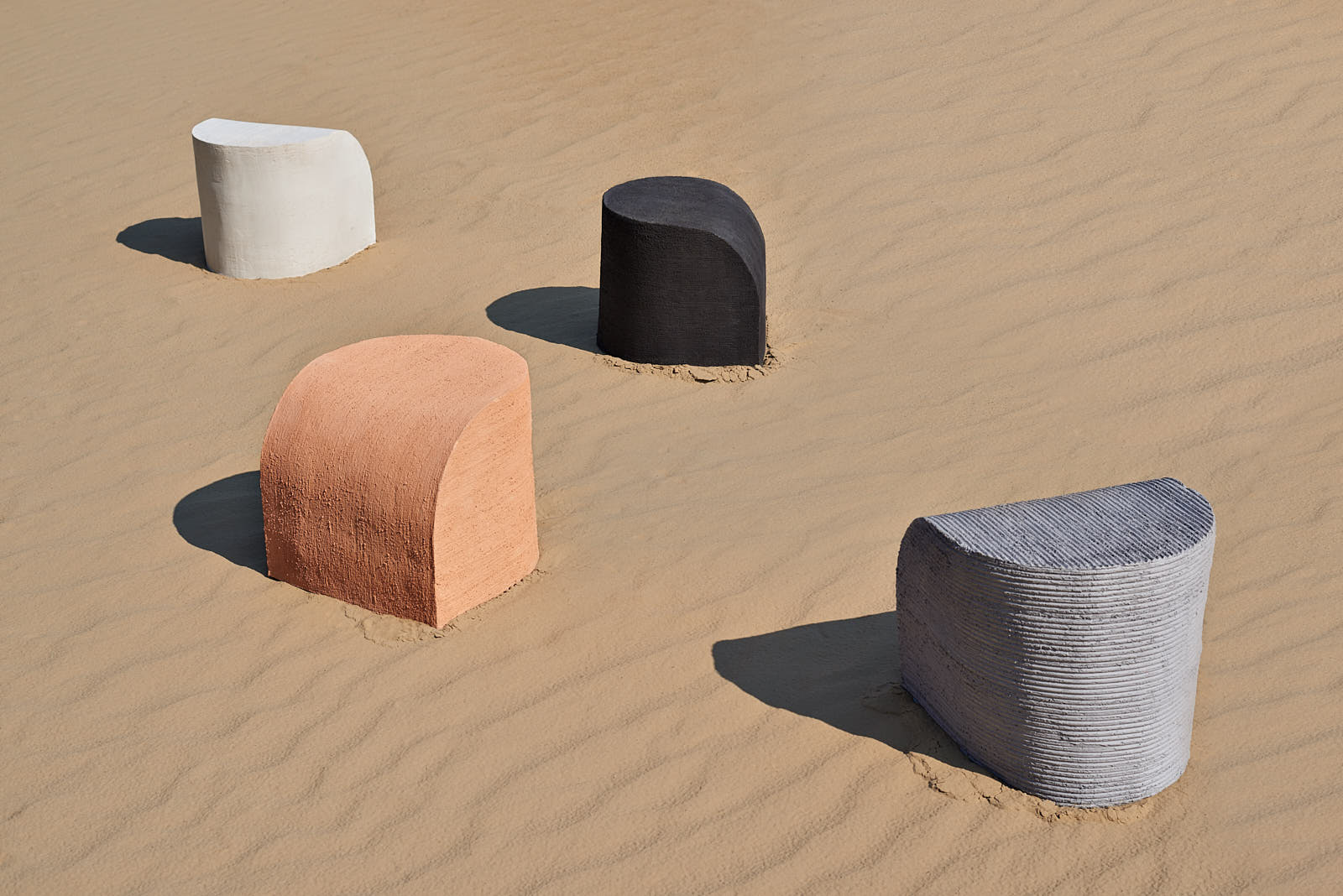
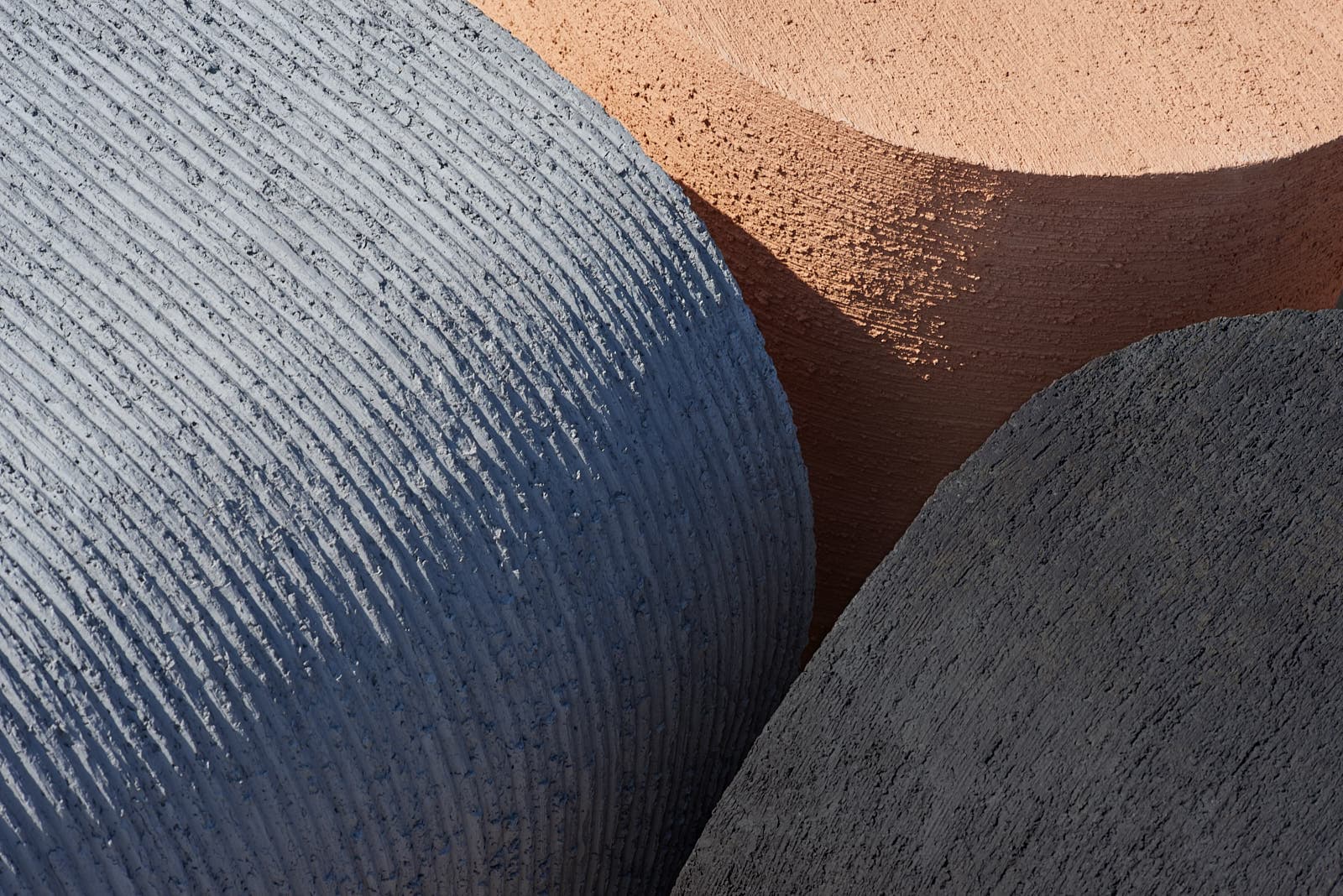
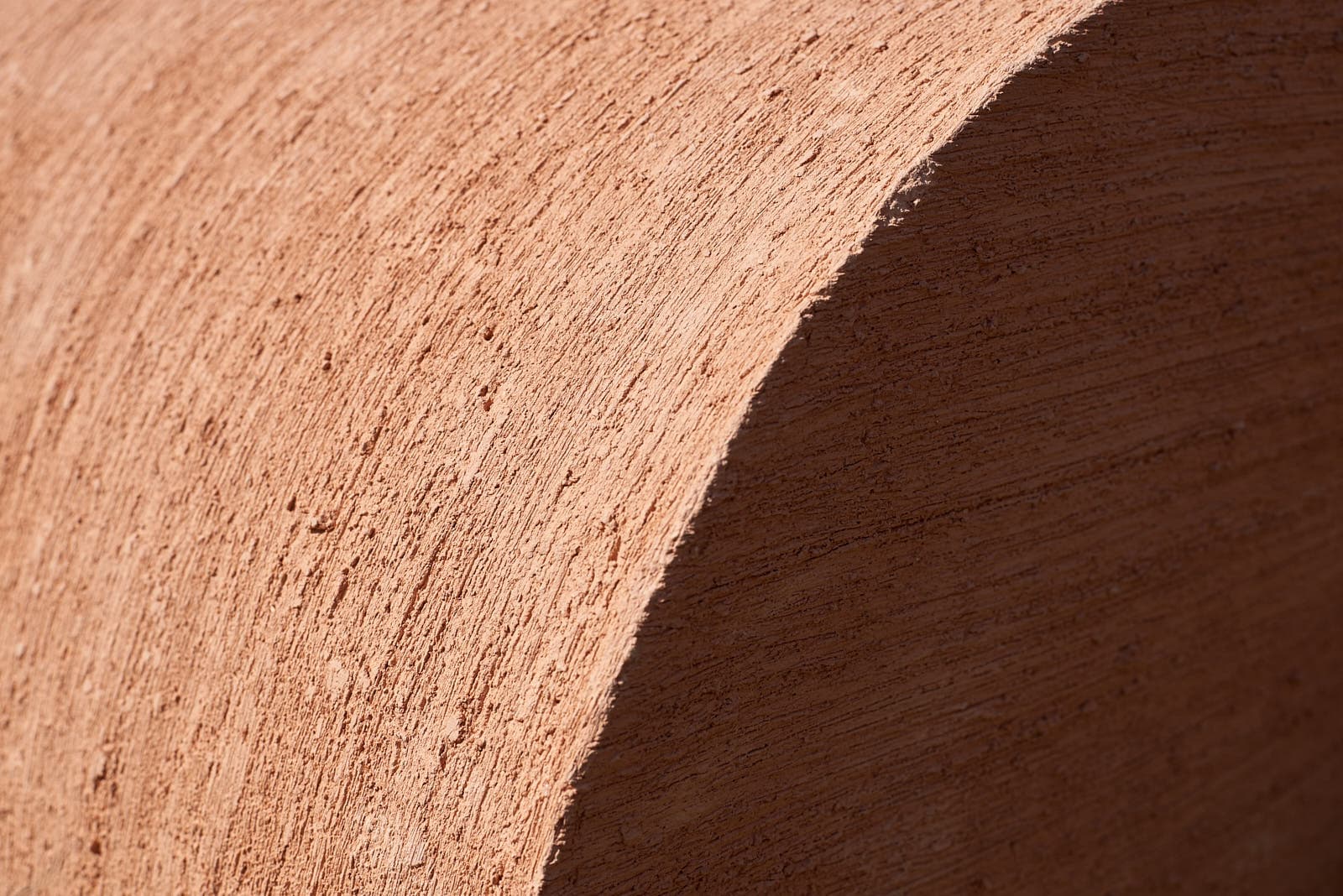
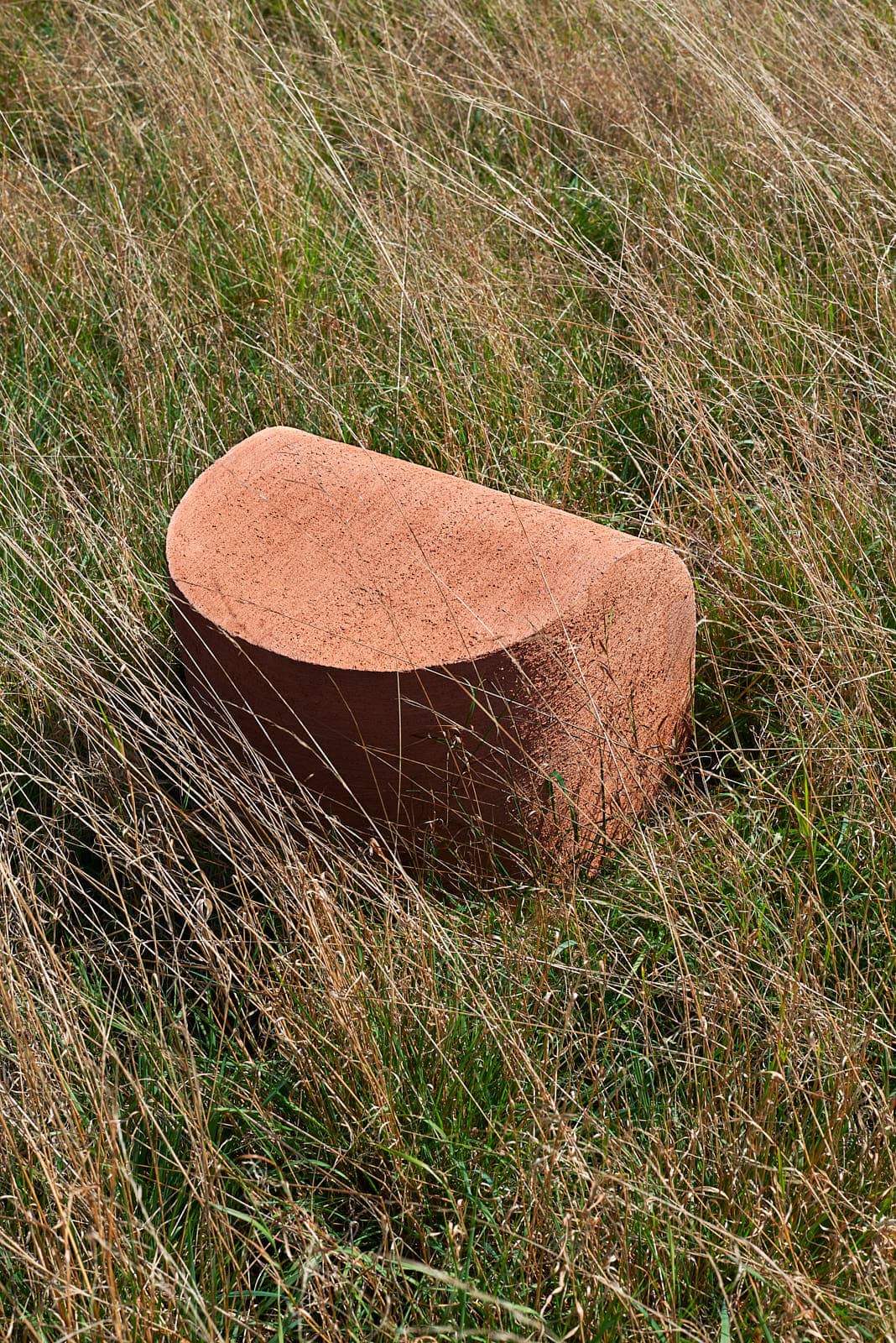
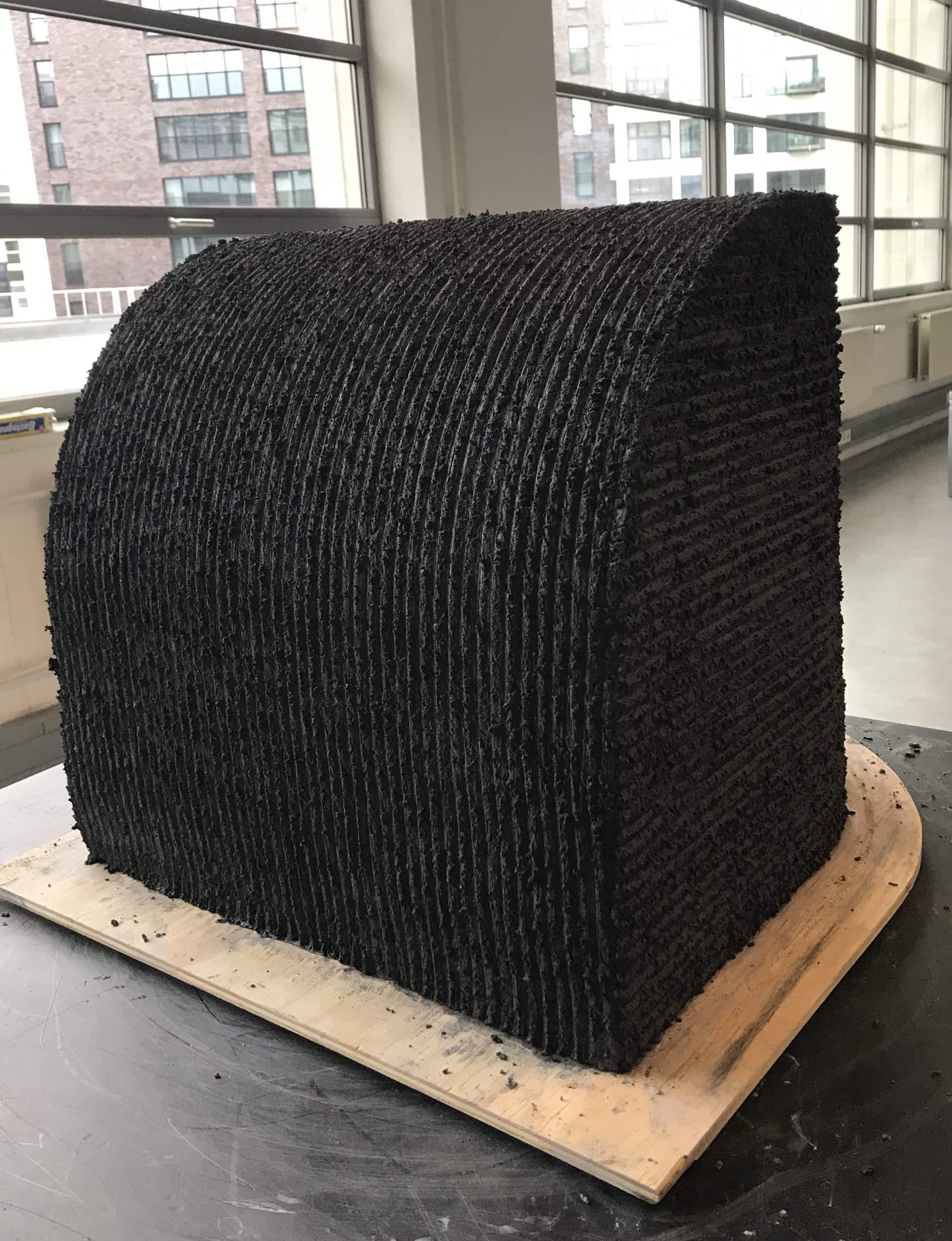
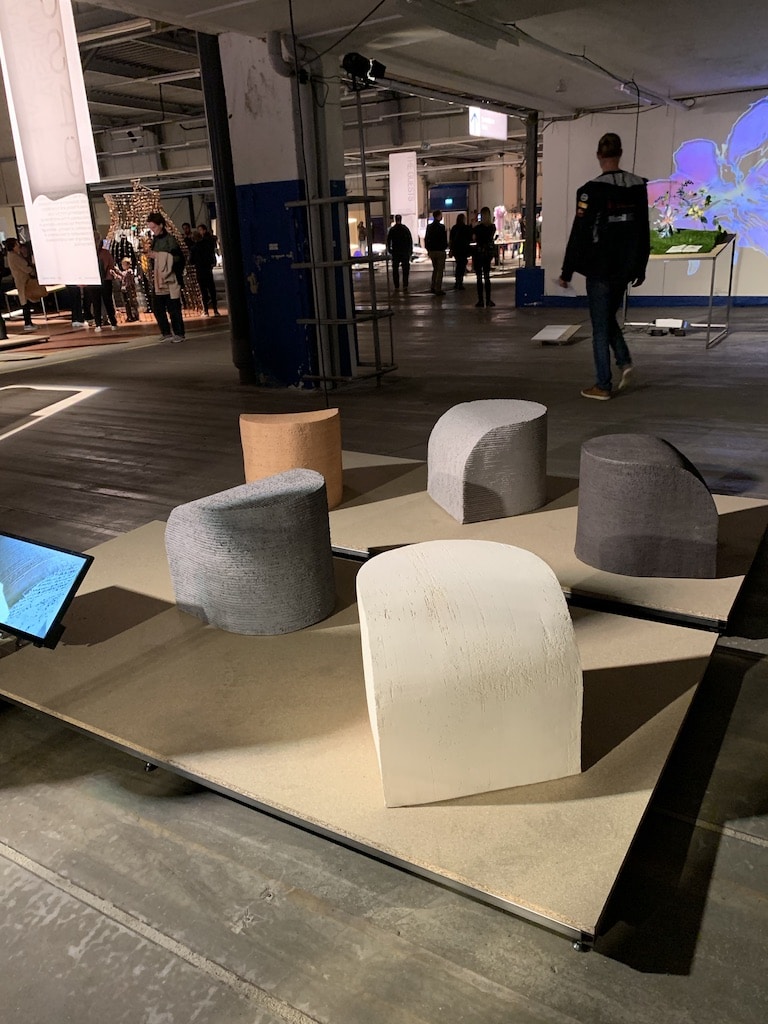
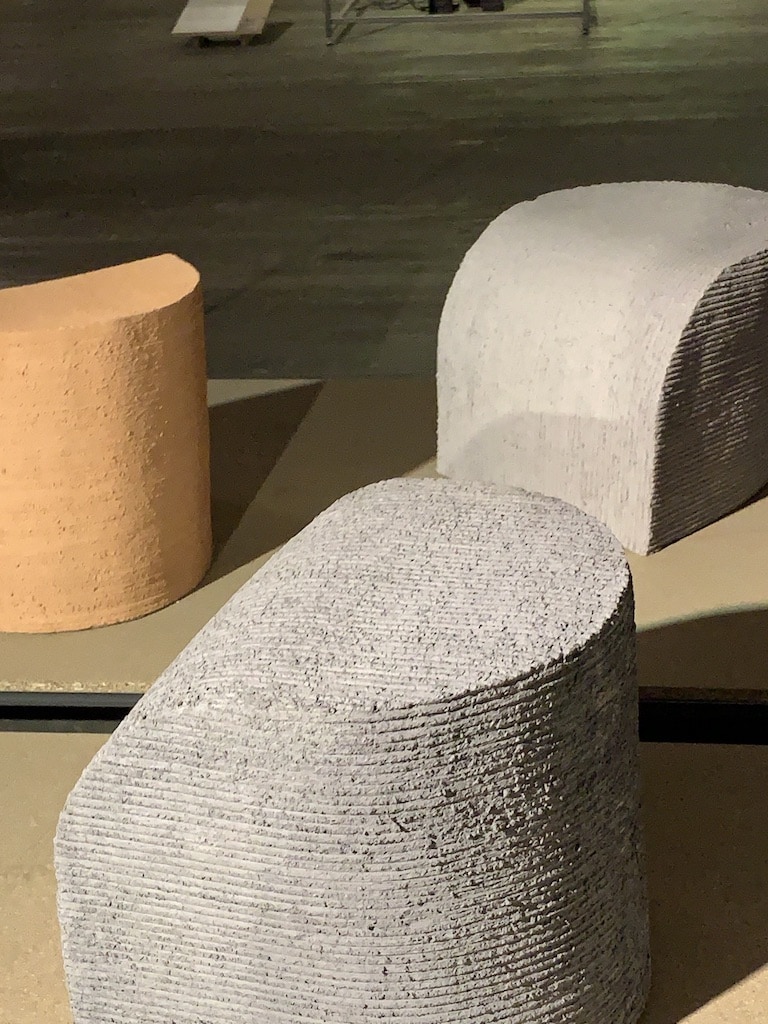
H.E.R.B.S. by Studio Nienke Hoogvliet
Nienke Hoogvliet started the H.E.R.B.S. project (Healthier Environment, Remedy for Body and Skin) to raise awareness of harmful chemicals used in clothing production processes — often still present when clothes are taken home by the buyer. Her question: If textiles can release harmful toxins, couldn't they also release substances beneficial to our health and skin?
As herbs are known for their medicinal effects, Hoogvliet wondered if they'd have a similar effect when used as a textile dye. Hoogvliet dyed textile samples later tested in a laboratory, where it was proven that essential oils can be transferred to textiles during the dyeing process.
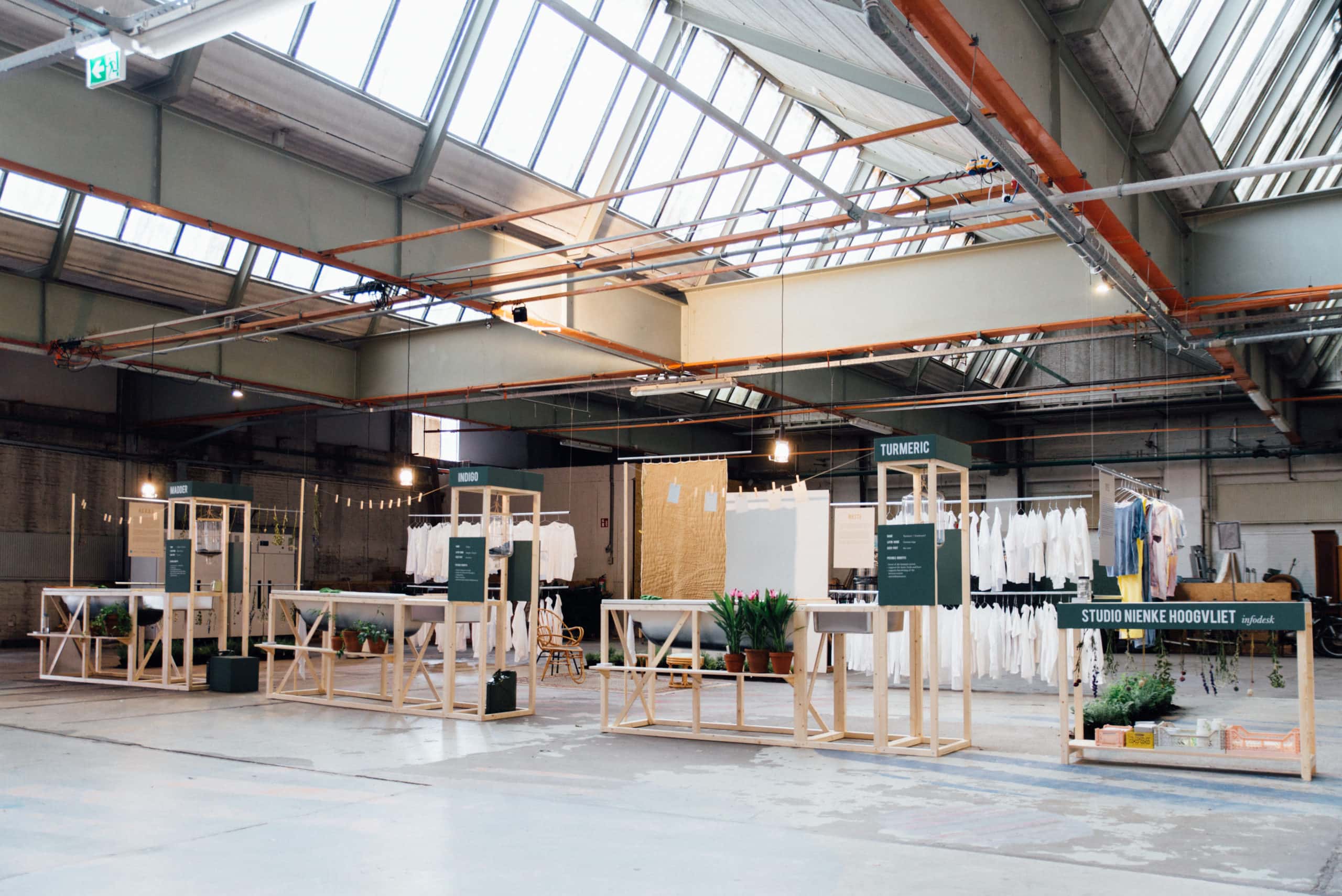
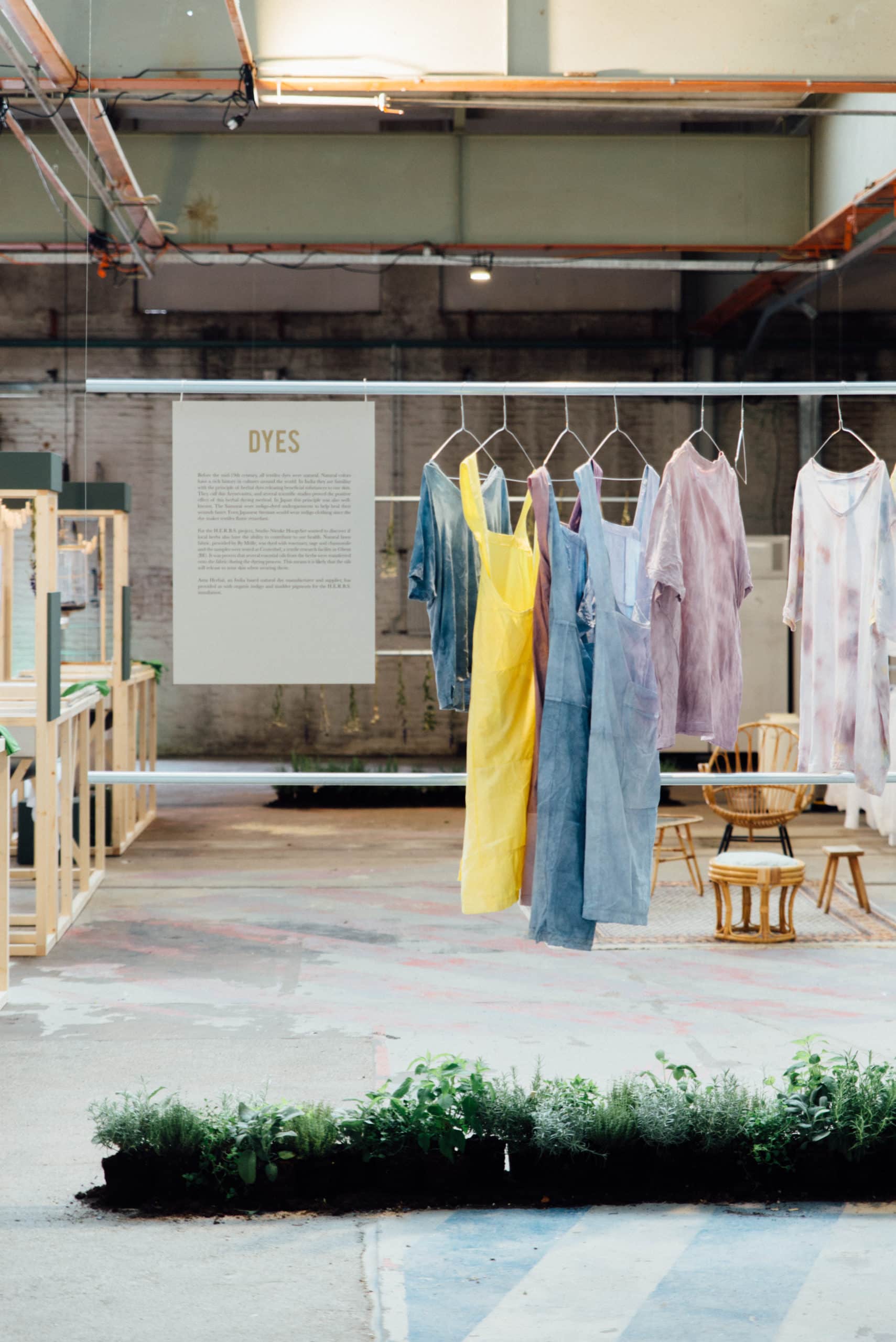
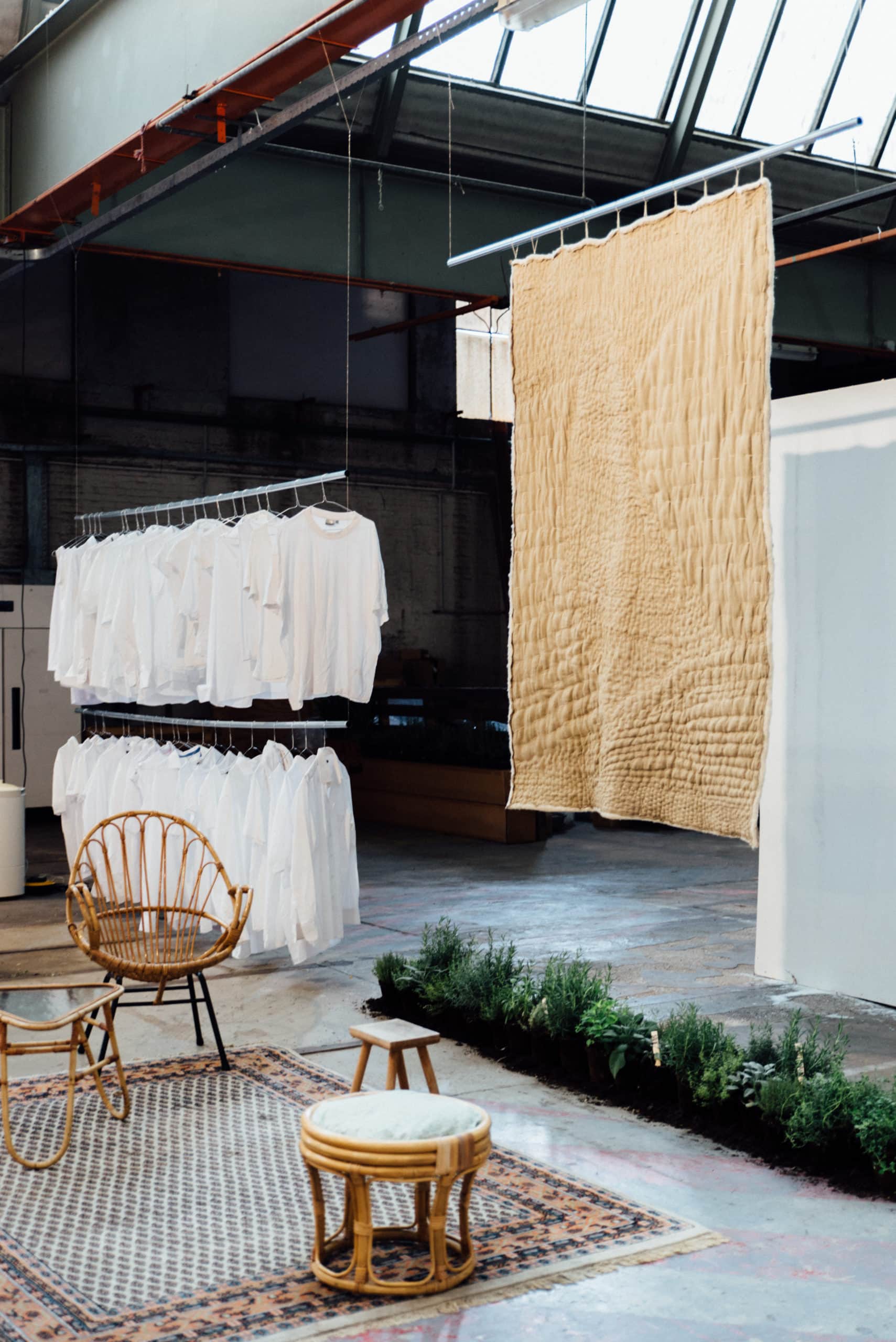
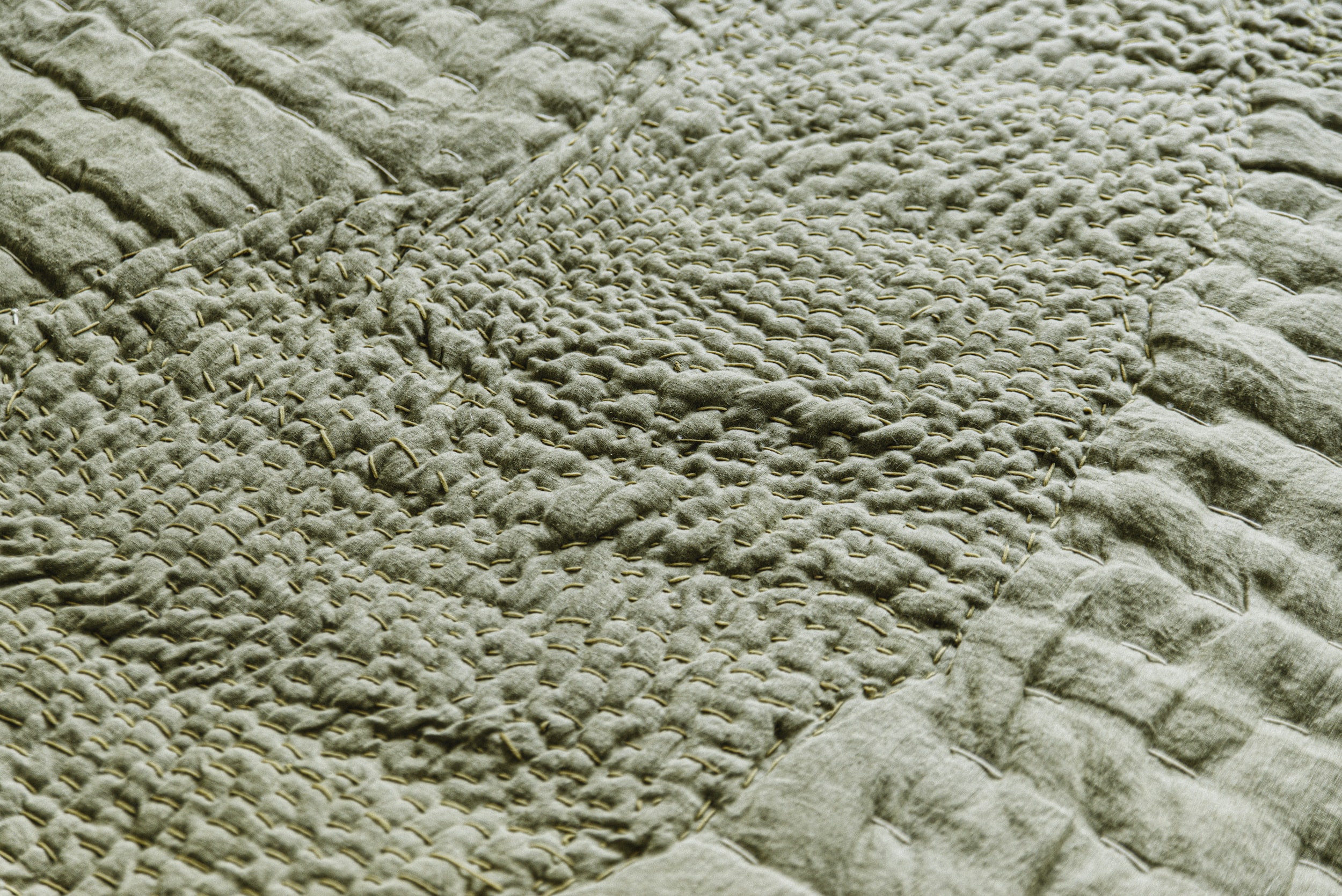
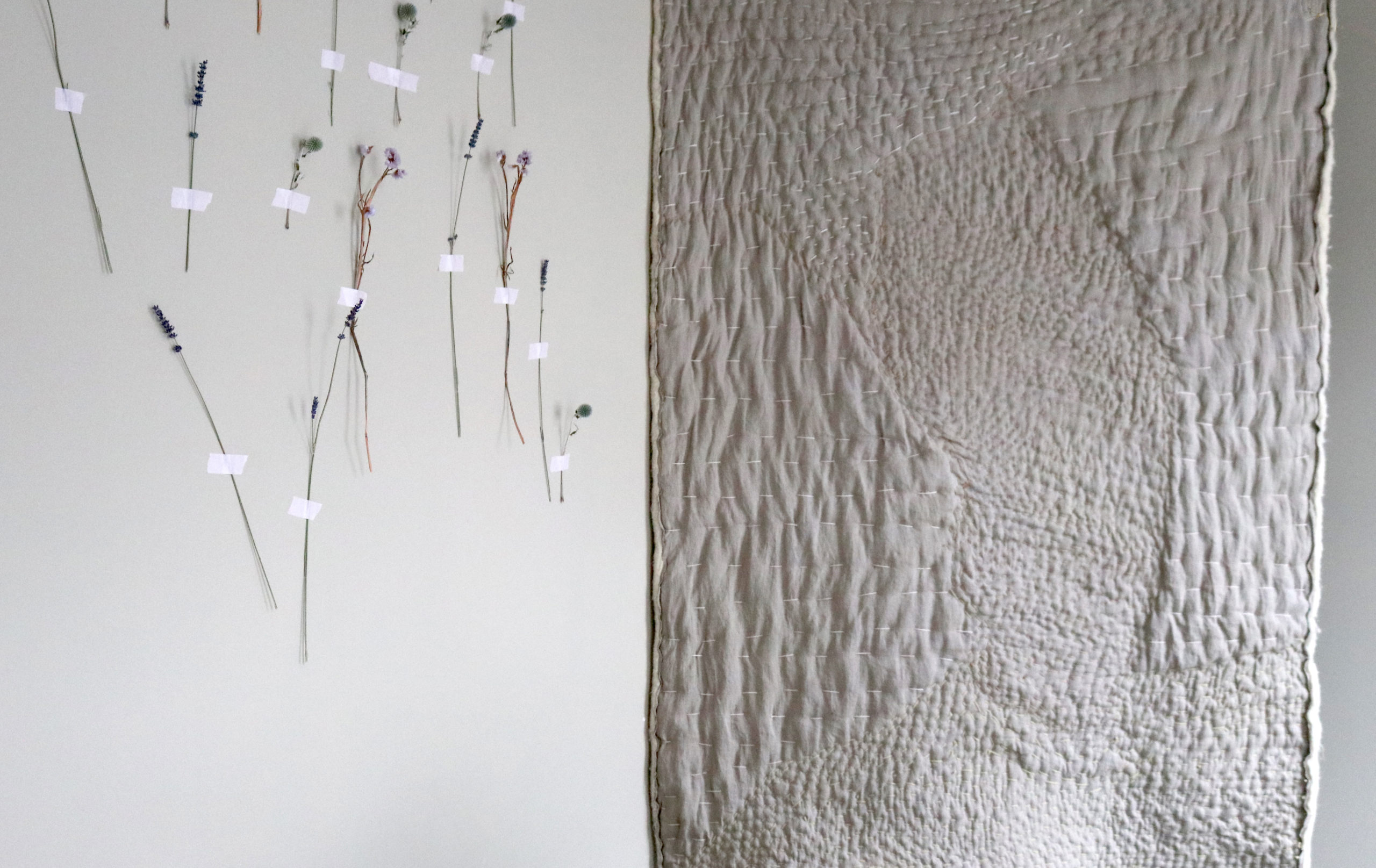
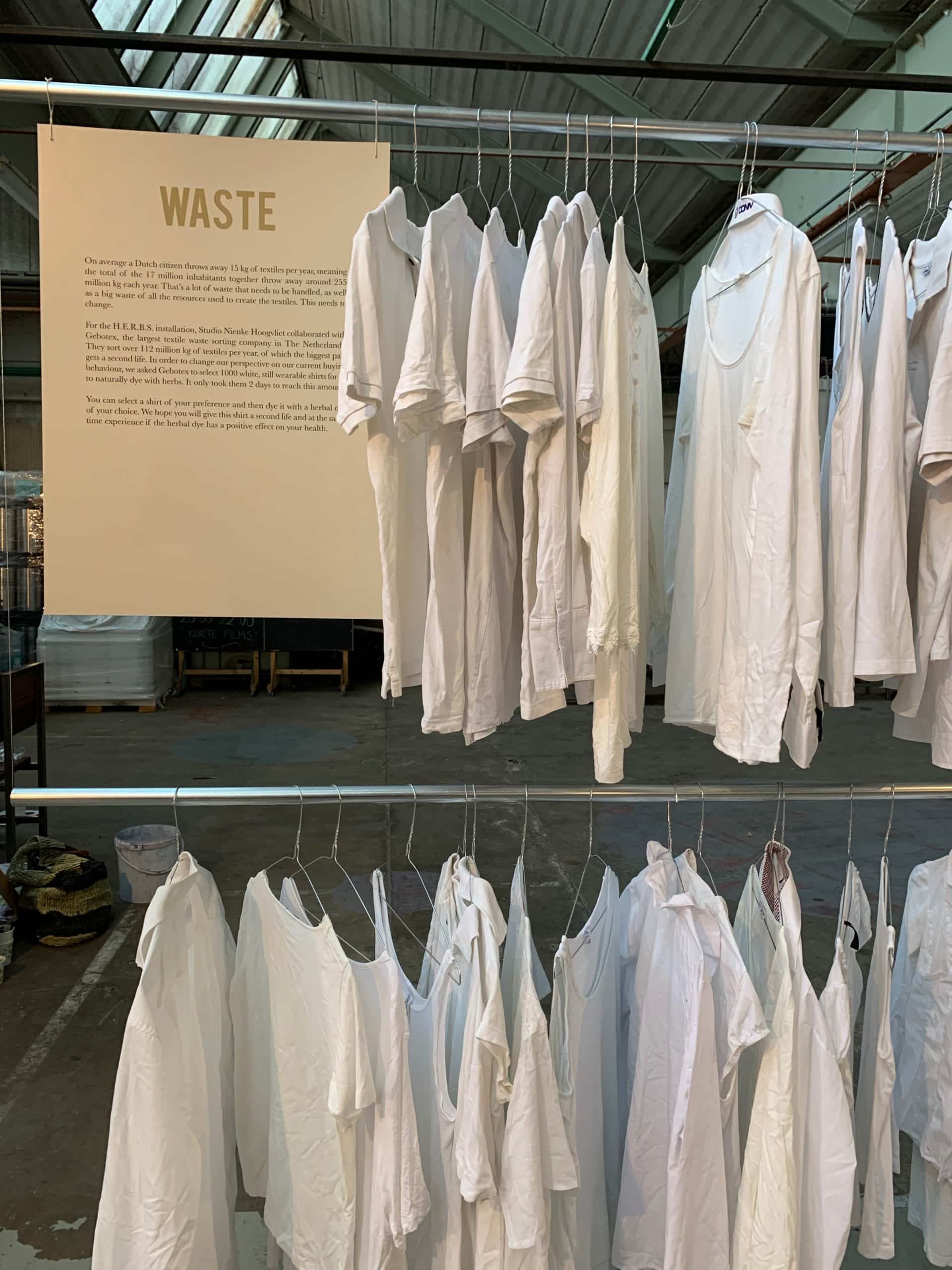
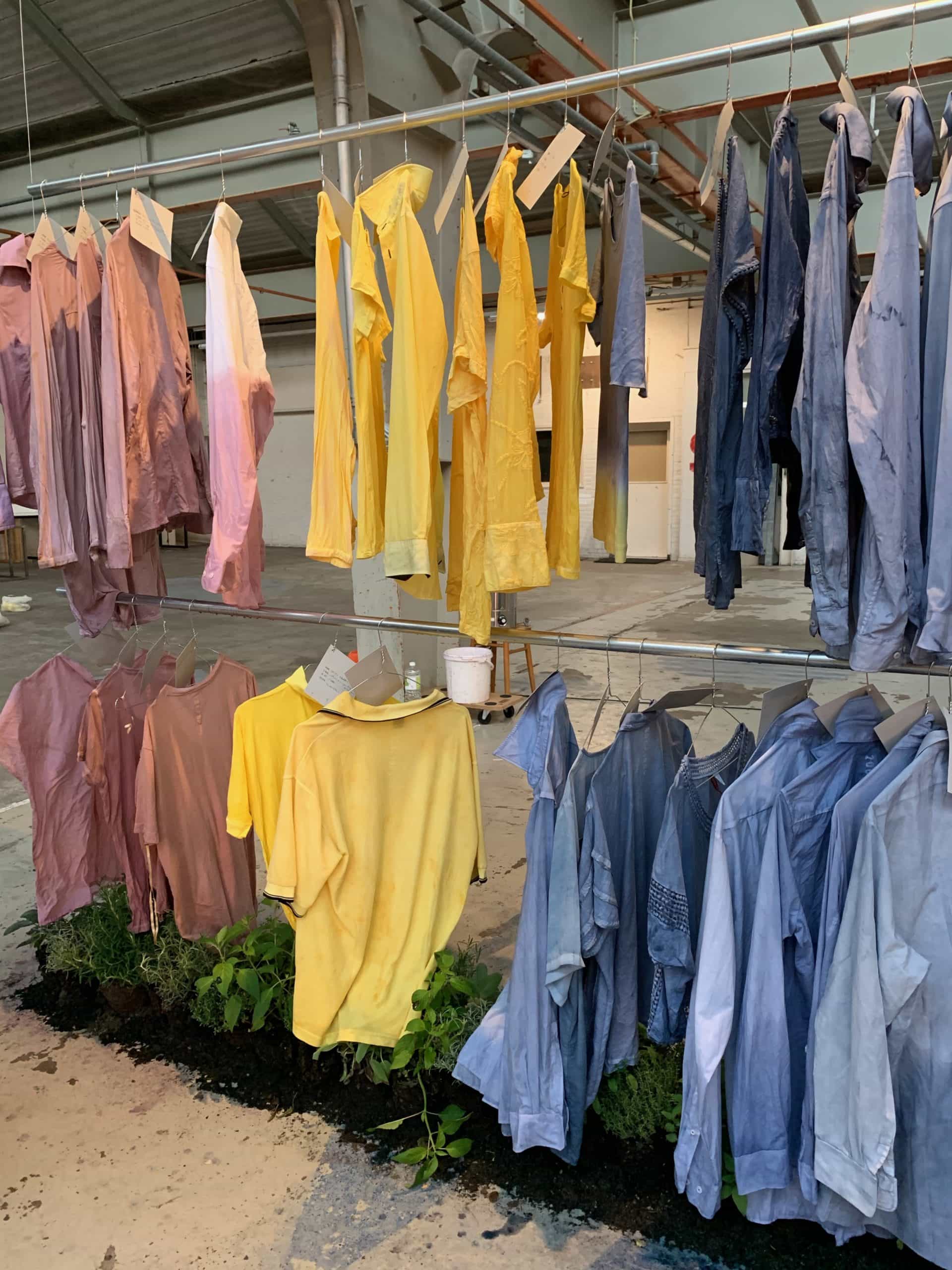
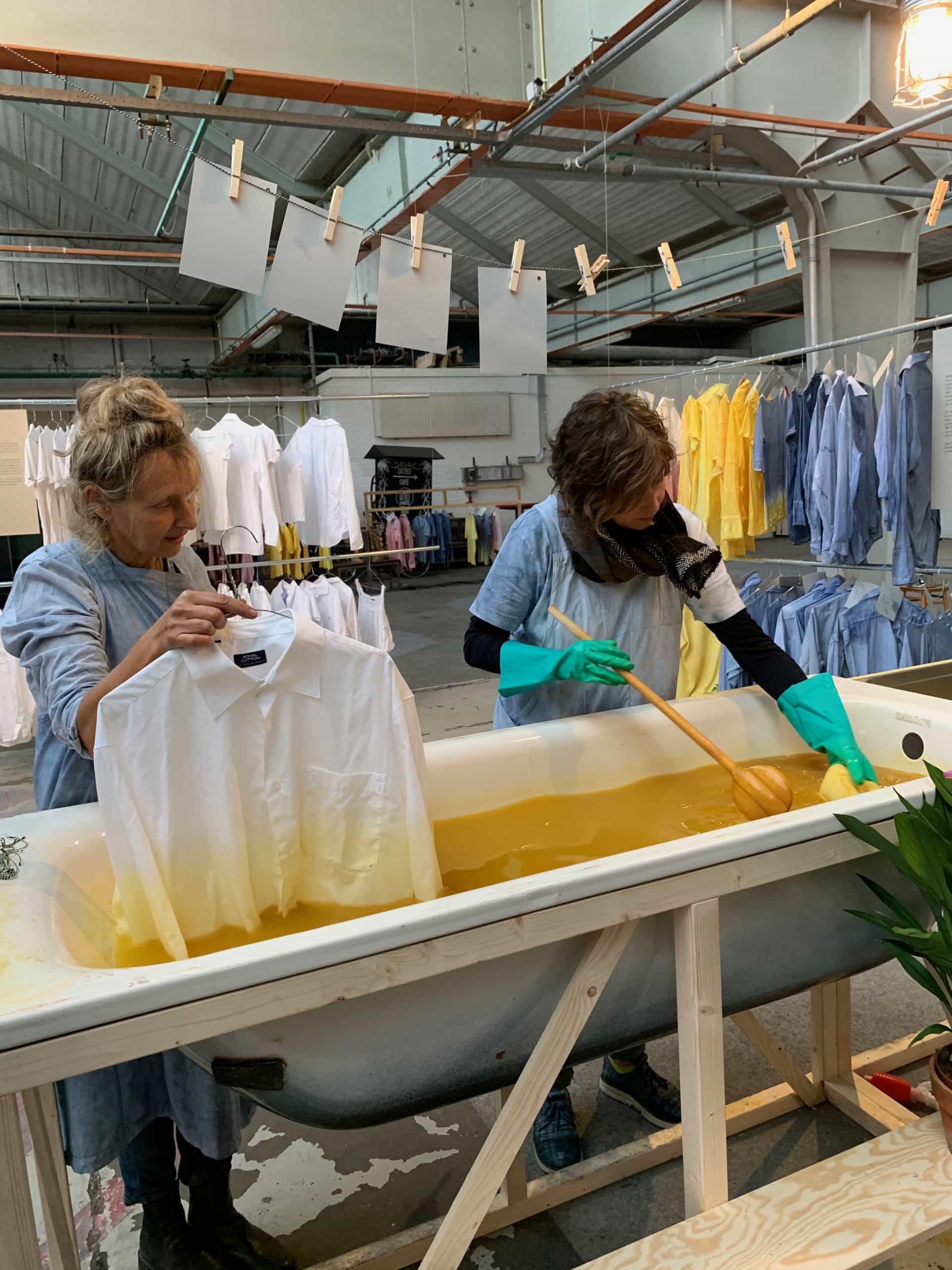
Blurred Objects by UAU Project
Blurred Objects are designed by UAU Project in their studio and manufactured locally in each market to reduce shipping to a minimum. Founded by Justyna Fałdzińska & Miłosz Dąbrowski (graduates from Warsaw Academy of Fine Arts's Industrial Design Faculty), this 3D-printed collection is produced with two materials: PLA, a production waste from cleaning the machine between two filament colors and custom recycled PET filament made in cooperation with REFLOW. Produced with quality plastic materials—either bio-based or sourced from recycling—the duo is working to consider all elements of the process from an eco standpoint. Using additive technology in manufacturing allows zero waste production (even failed prints are shredded into new material). As products are made to order, there isn’t overstock and shipping leaves a smaller carbon footprint as their durable designs are still very light.
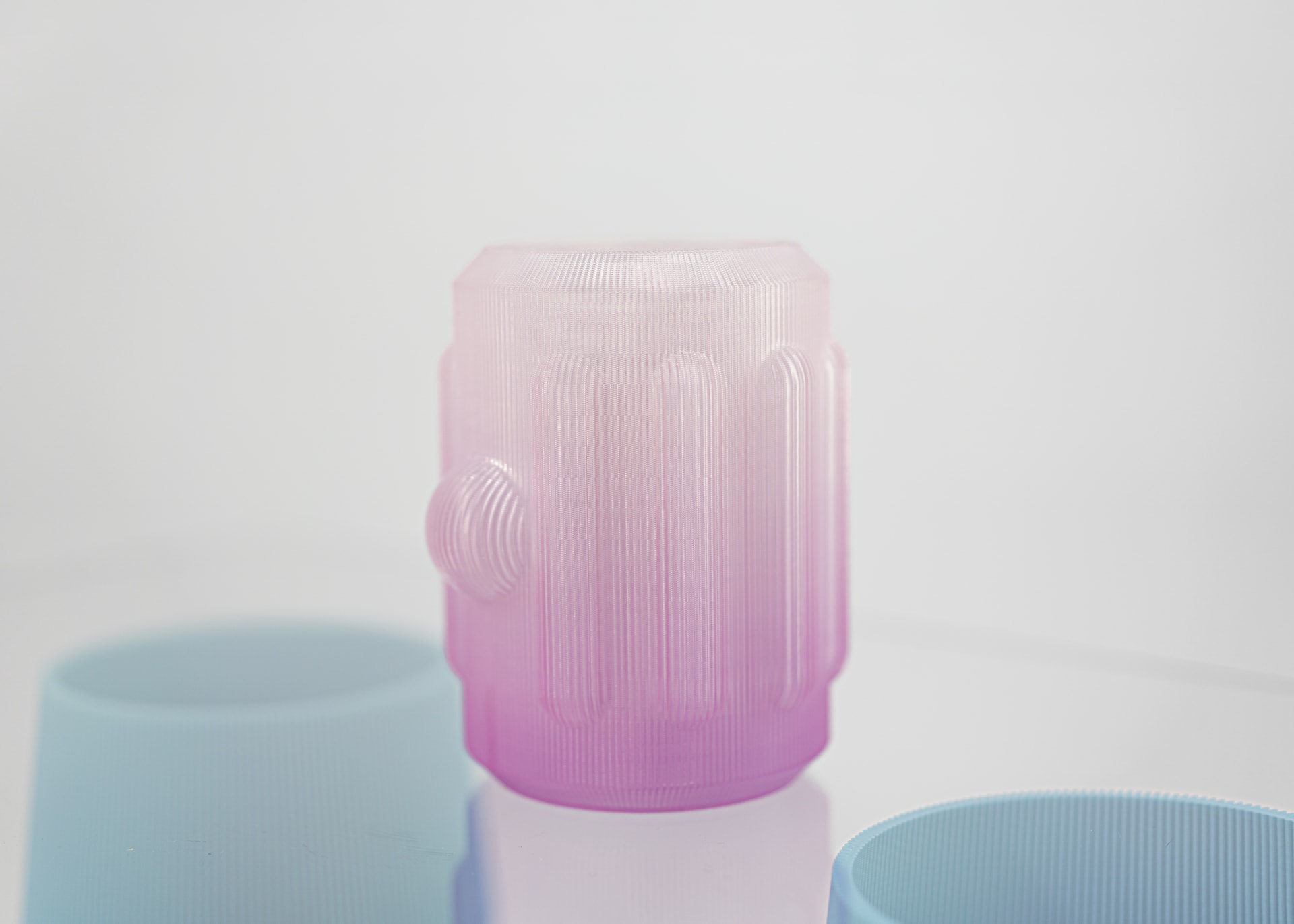

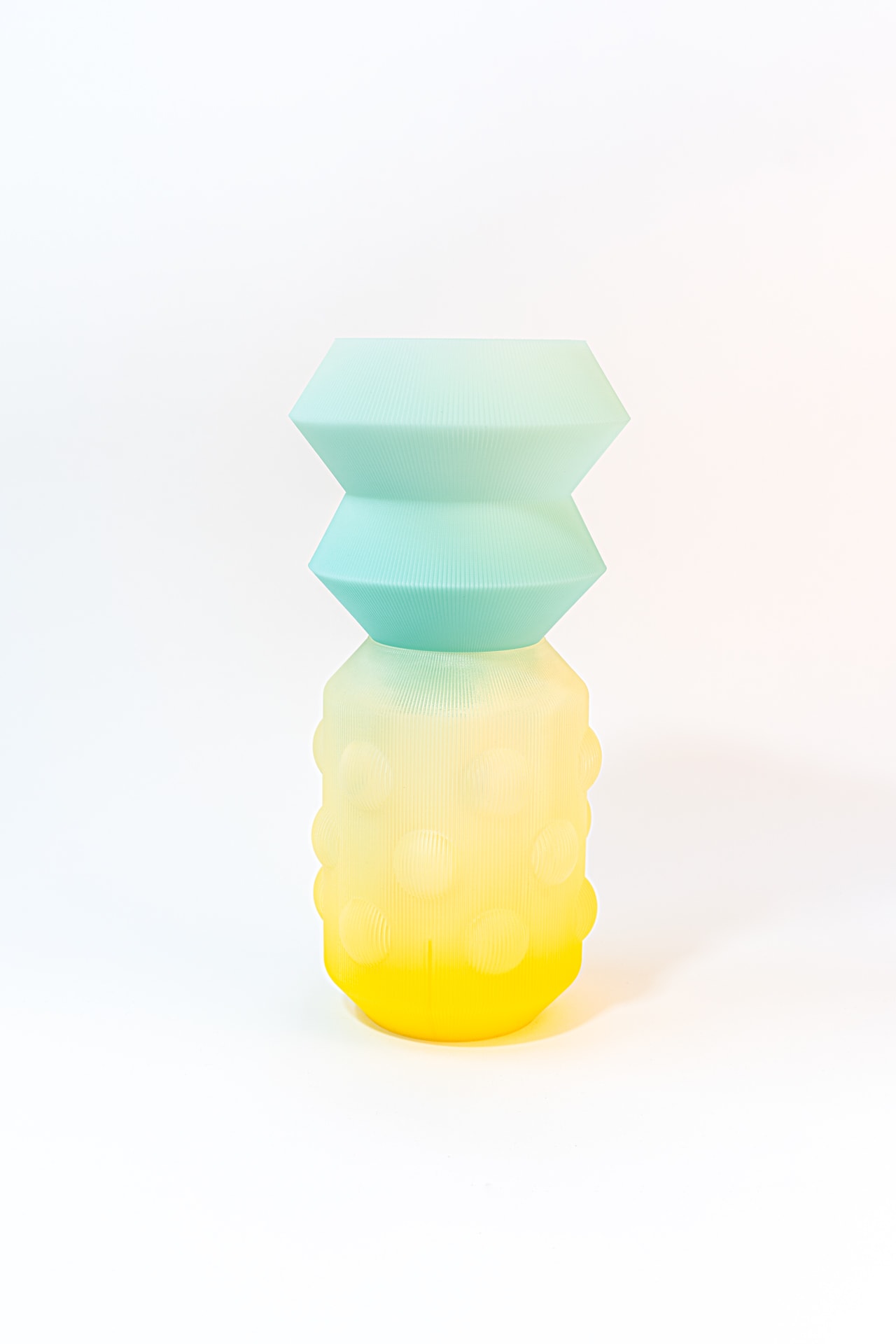
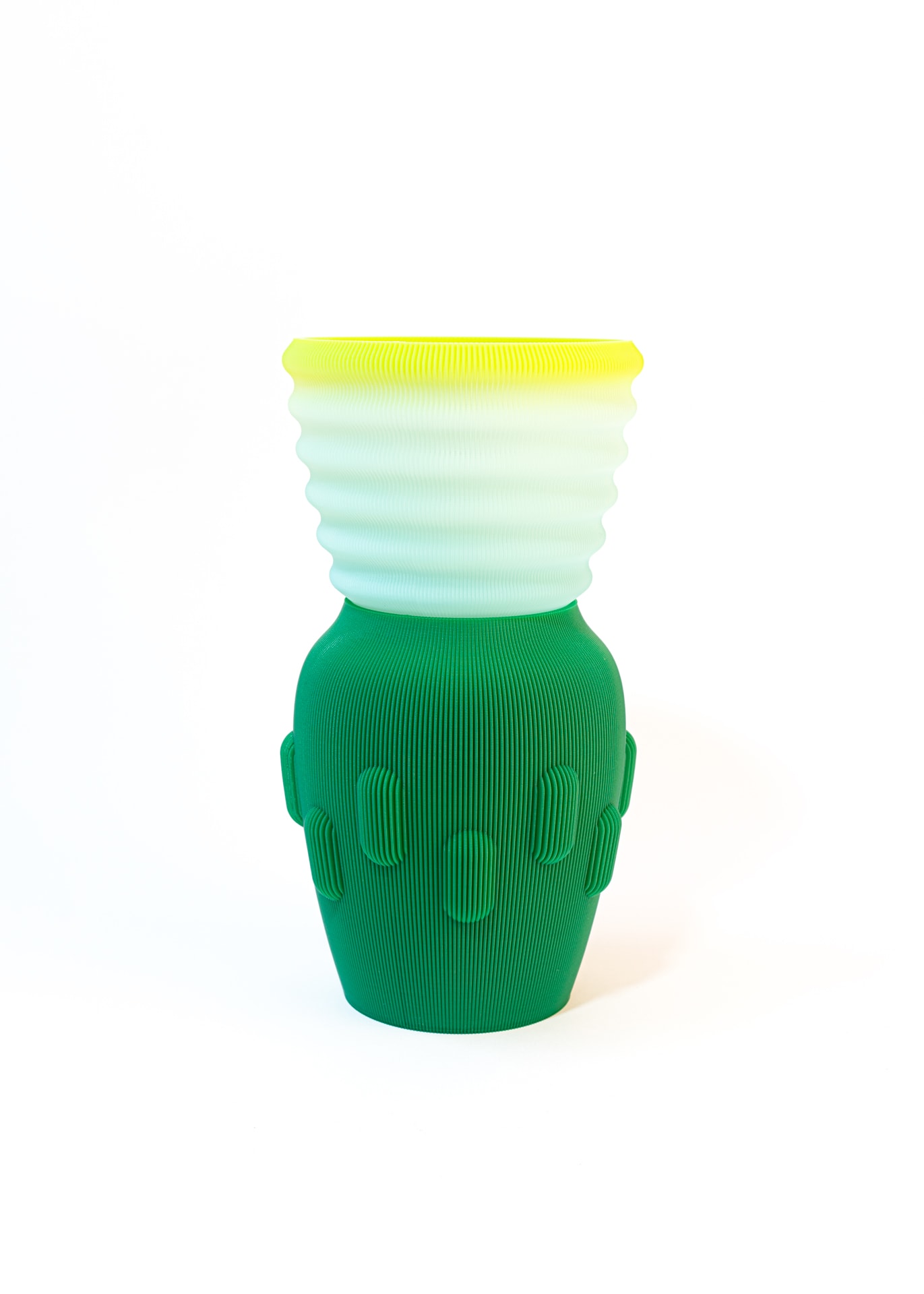
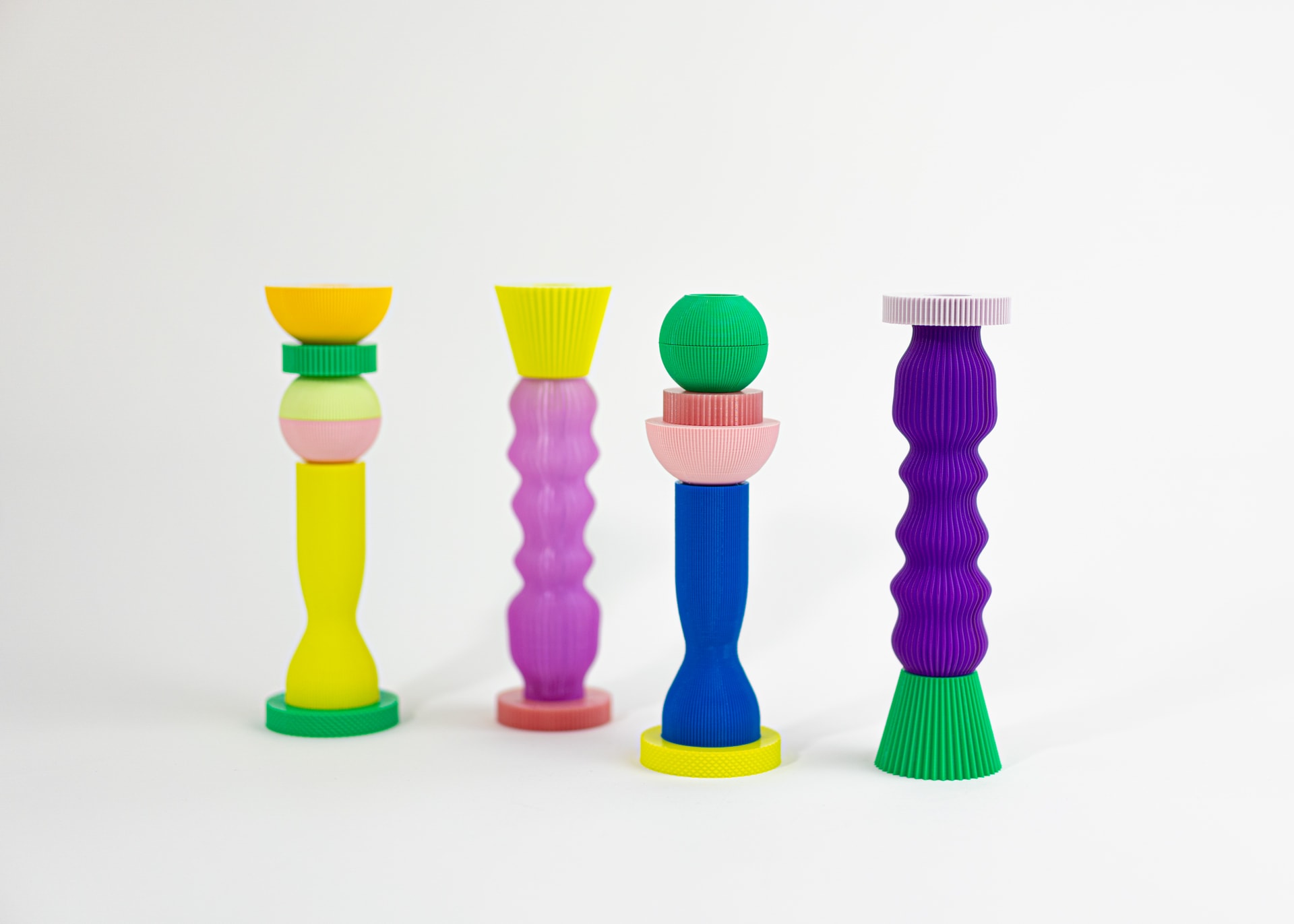
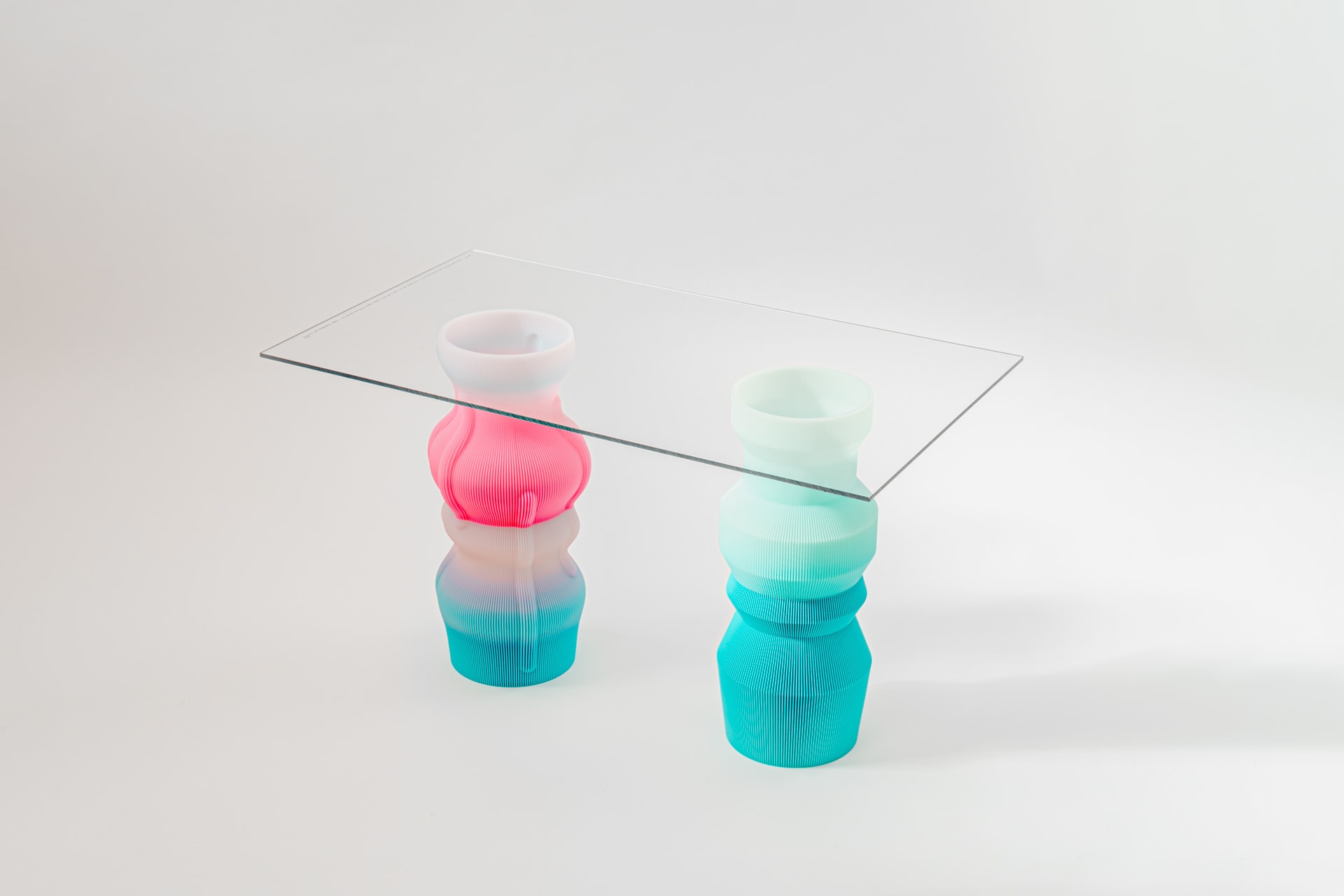
Worn to Wear by Lena Winterink
Design Academy Eindhoven graduate Lena Winterink has designed garments incorporating copper components after being inspired by the beautiful aging process of the material. Each garment is made using a different technique; A knitted sweater and a woven Kimono are made of an uncoated copper and an organic unbleached cotton yarn. A suit is made from an unbleached cotton, which is screen-printed with a special copper-based ink. The flexible qualities of copper allow them to appear sculptural, molding to the wearer and the materials age as the copper oxidises, slowly creating color change. In an age of consumerism when it's "normal" to buy new clothes every time something is worn out, Worn To Wear reconsiders the ways in which we approach materials that interact with our bodies. In emphasizing the beauty of longevity, these pieces restore value in the connection we have to our garments.
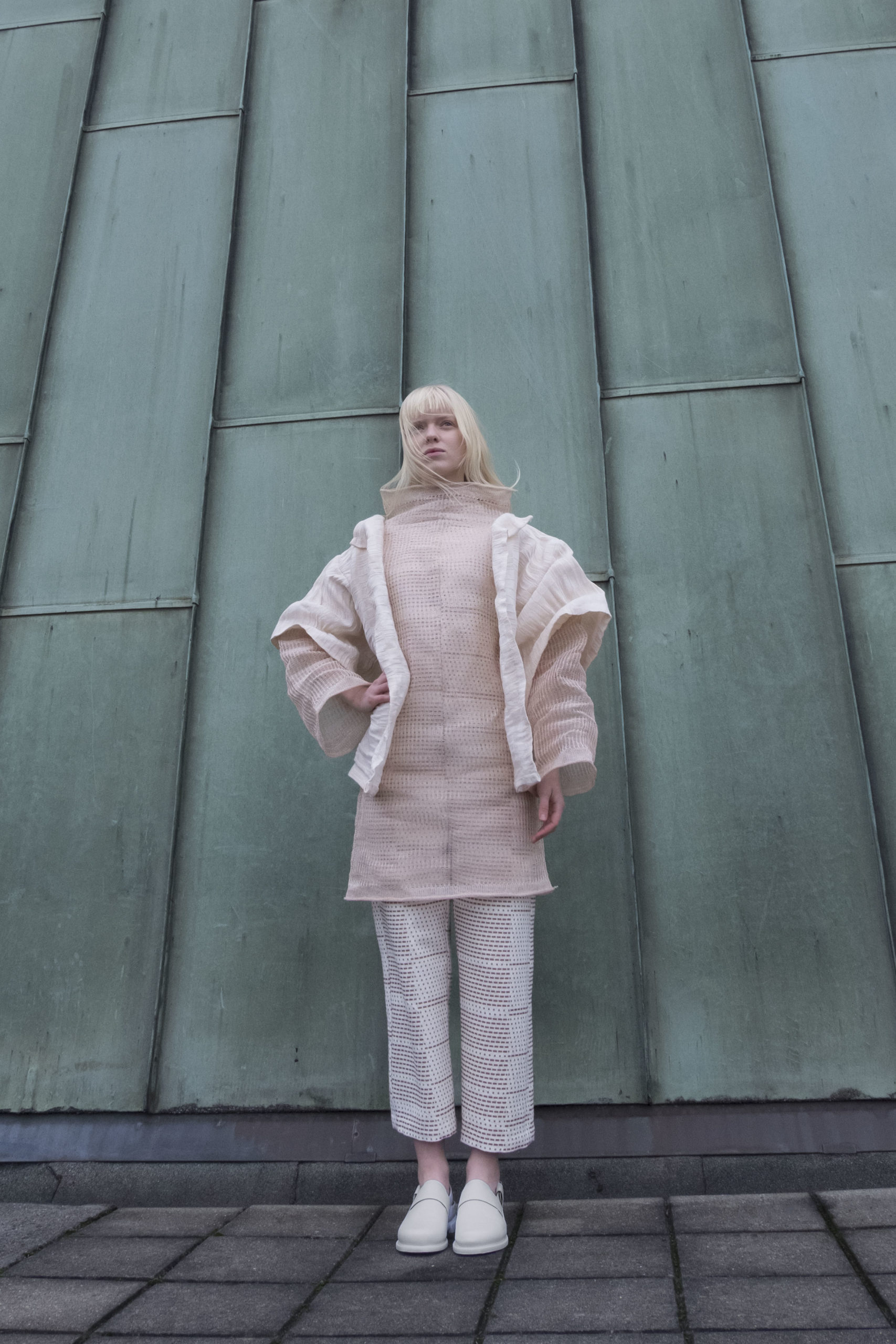
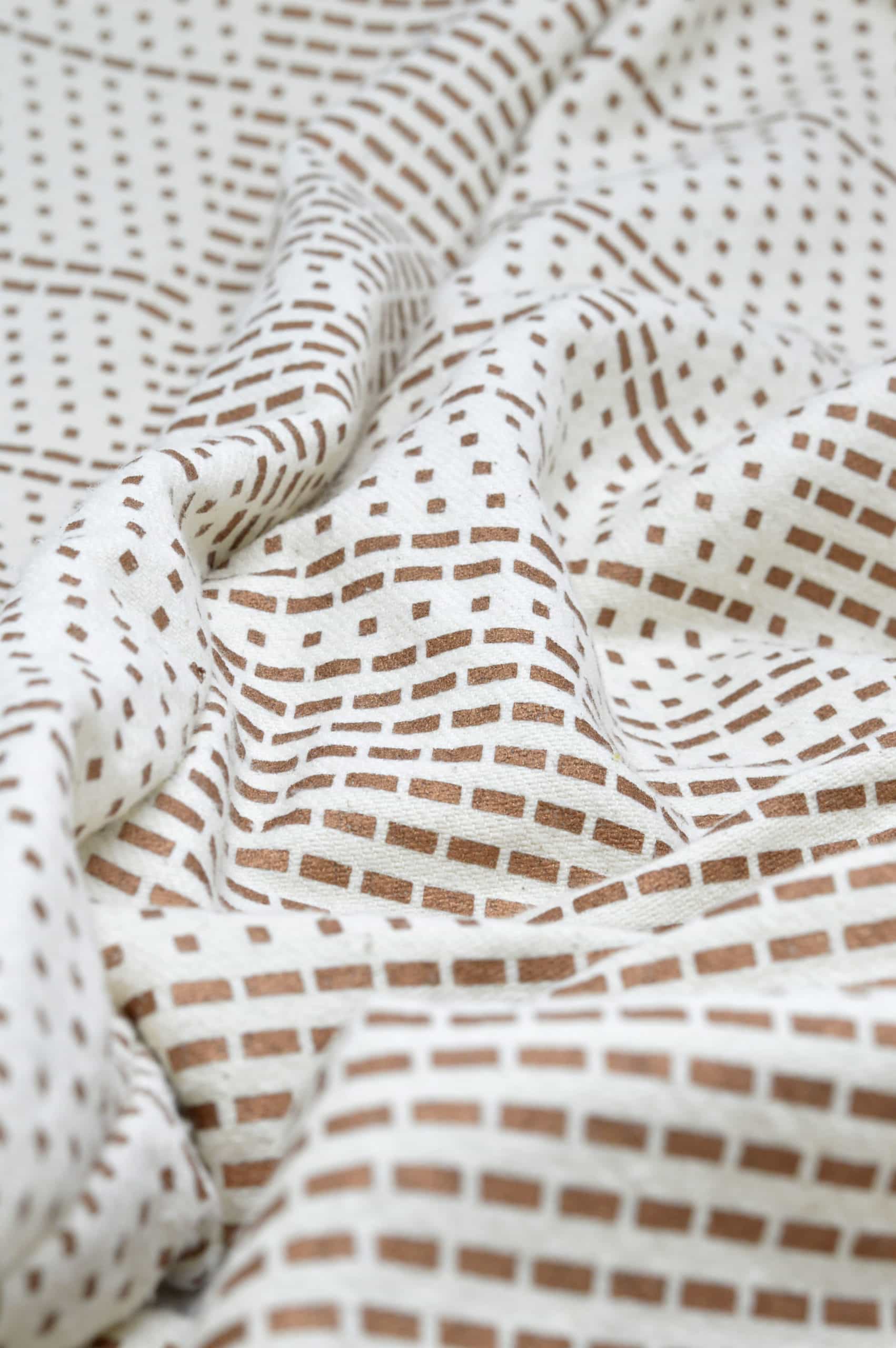
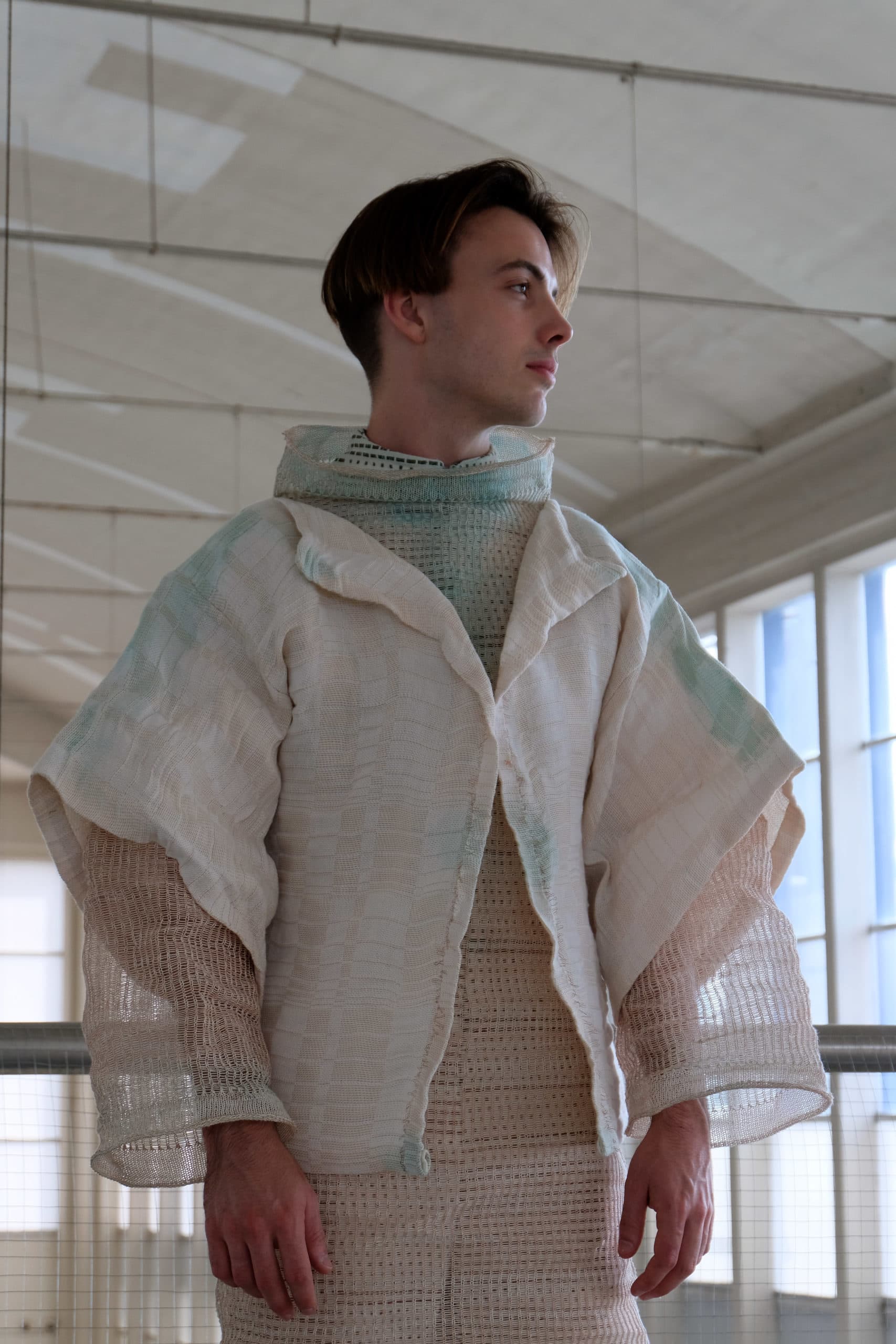
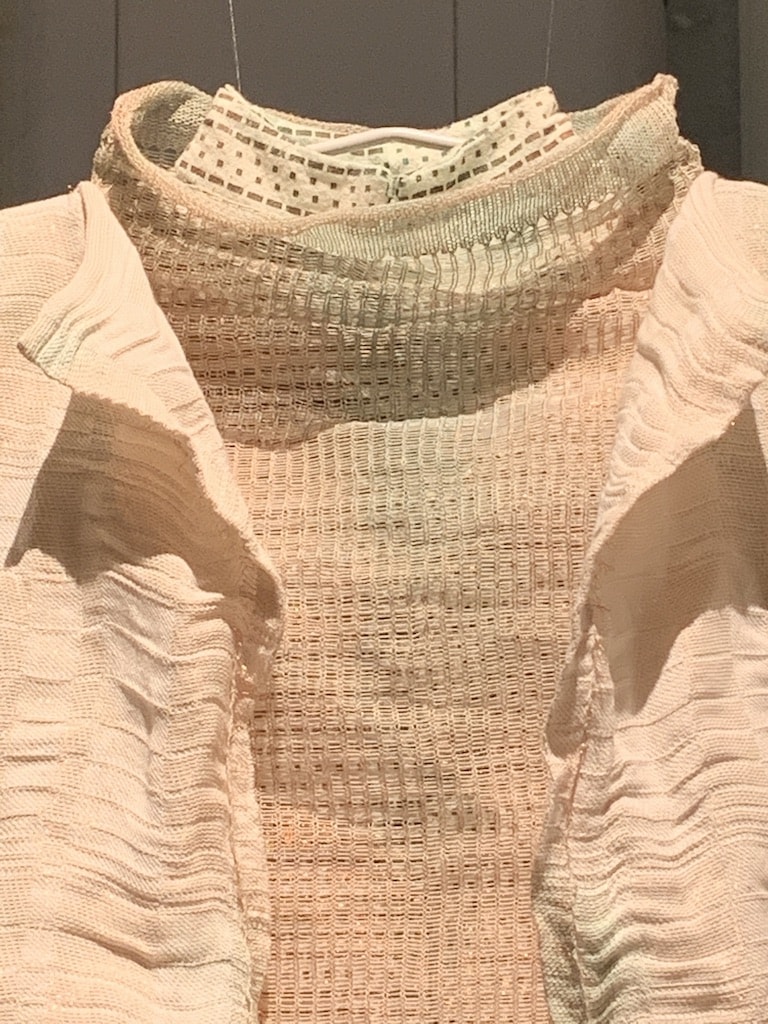
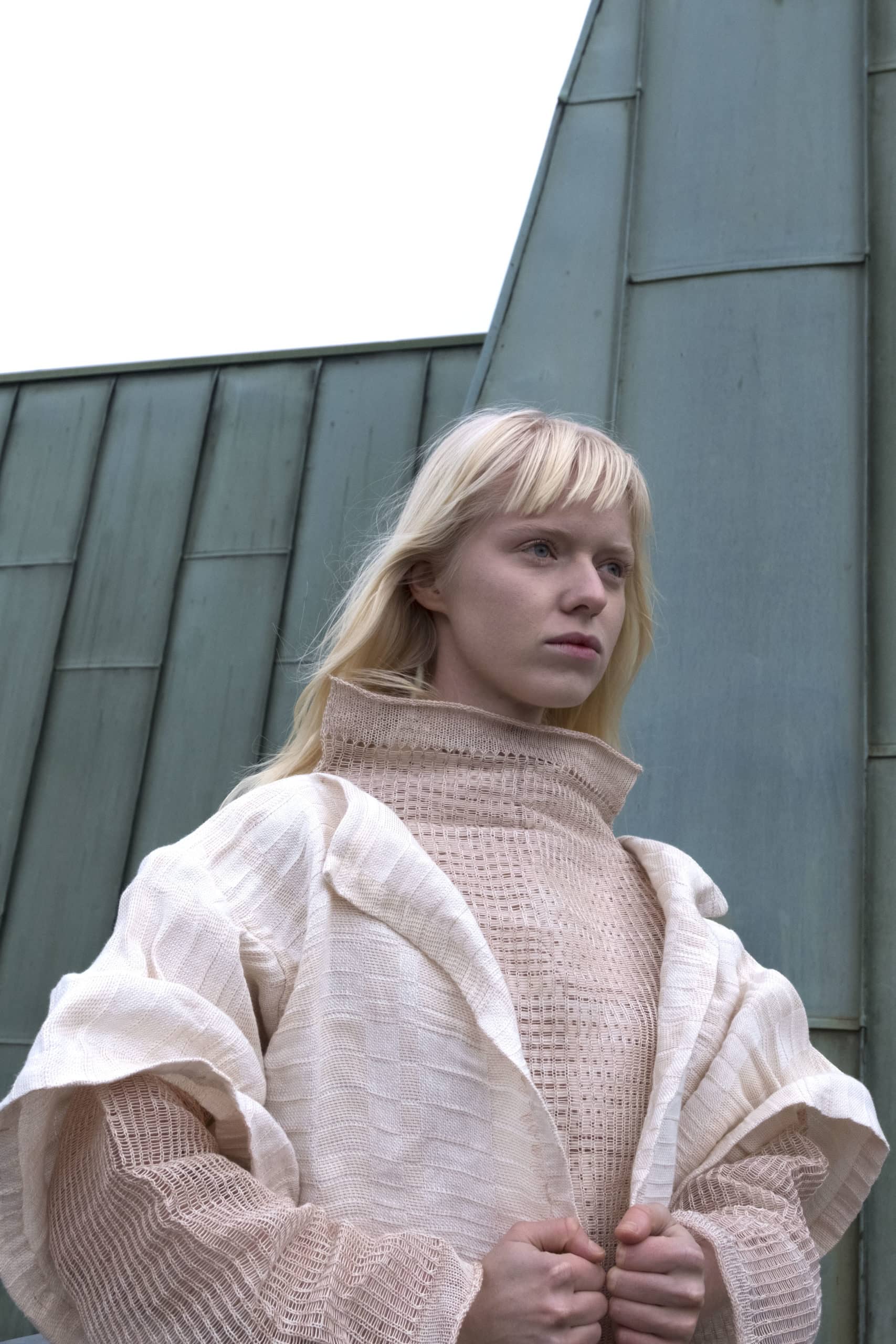
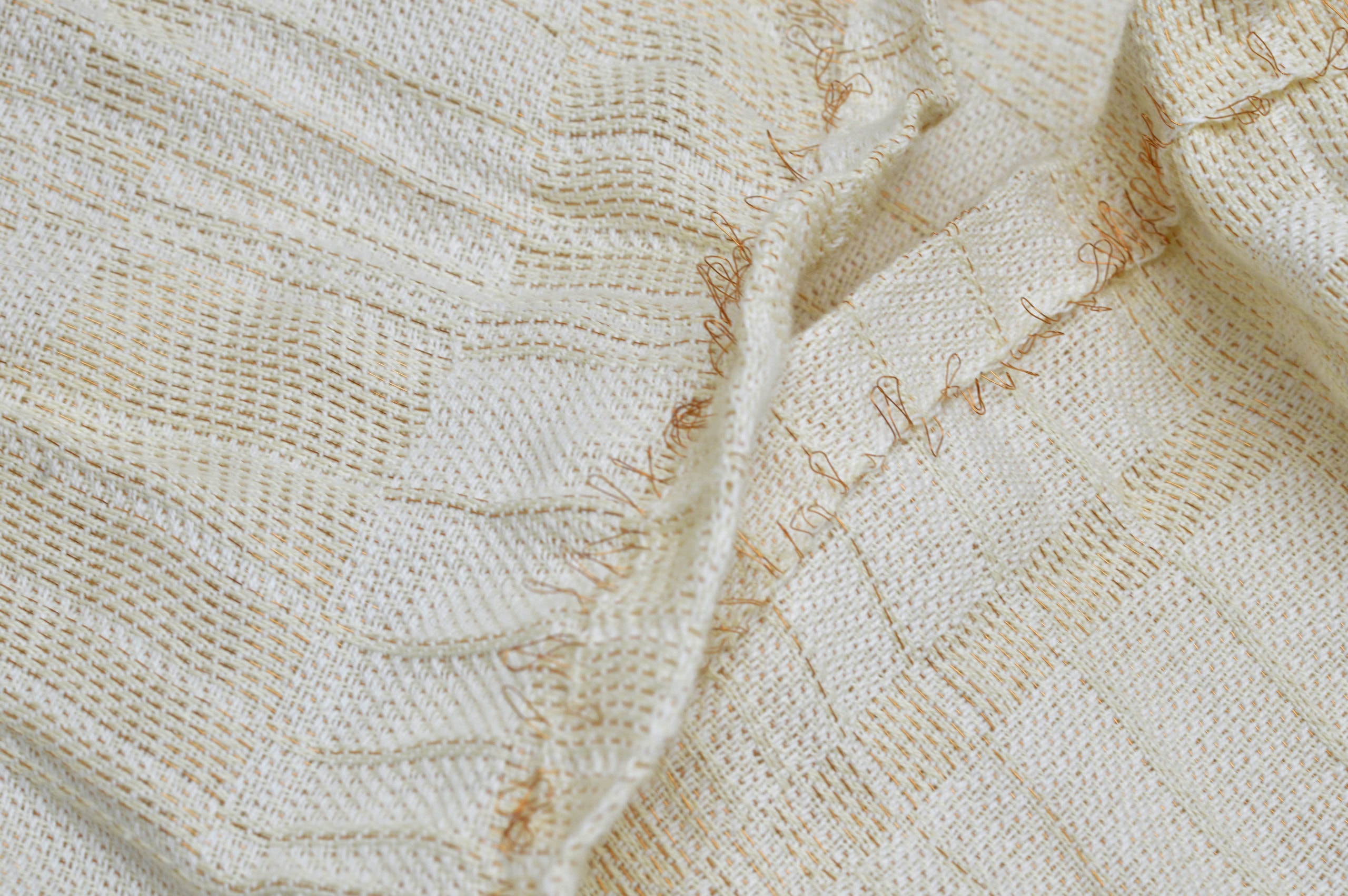
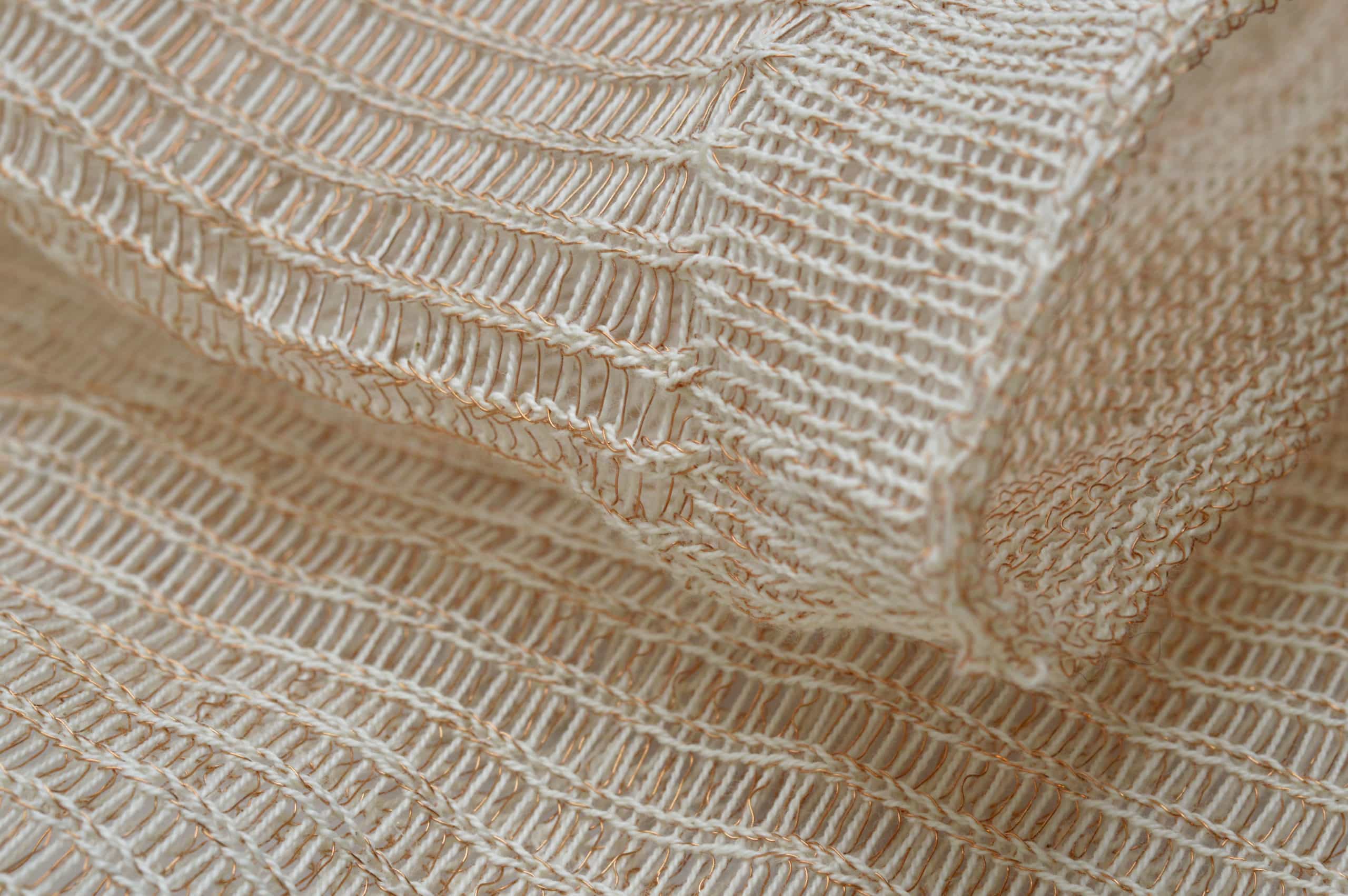
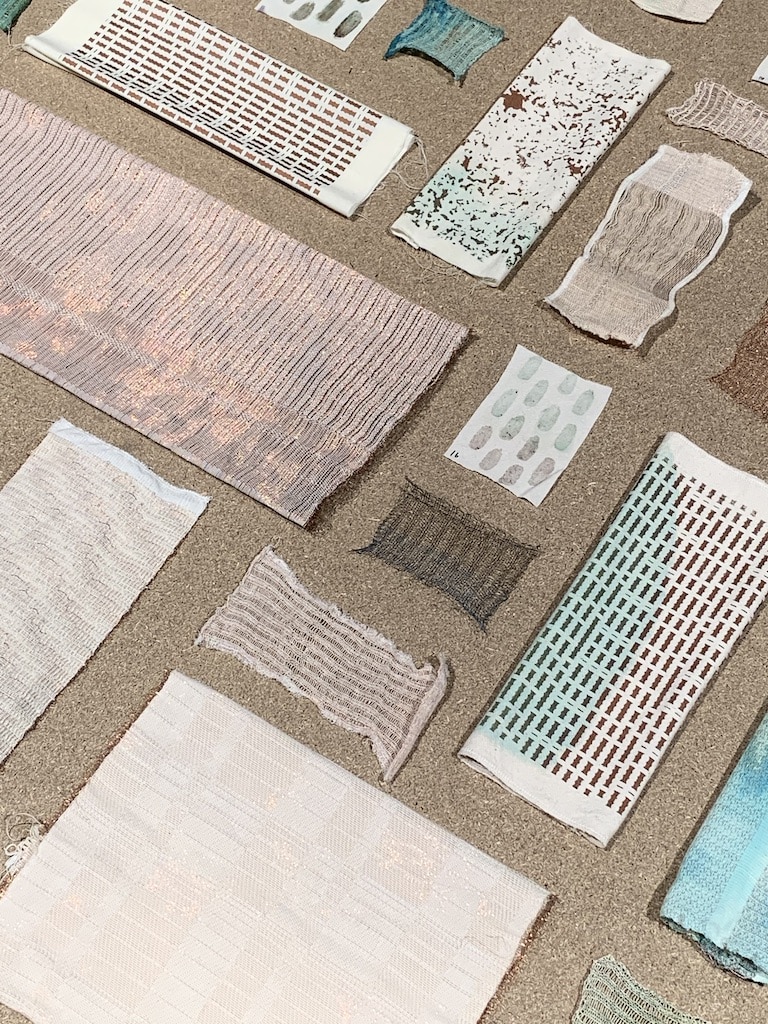
Biophilica by Mira Nameth
Mira Nameth has a background as a botanical illustrator and graphic designer. Her focus has been sustainable design and, as a conceptual but pragmatic designer with a sensibility for beauty, she wants to use this as a motivator for change. Biophilica explores raw material for it’s aesthetic and manufacturing possibilities. There are currently two different materials—flexible and rigid—made from urban plant waste. They are local, biodegradable, and recyclable. The flexible material was created for use in the fashion, accessories, shoe, and upholstery industries. The rigid material has potential applications in many industries: construction, architecture, furniture, and toys.
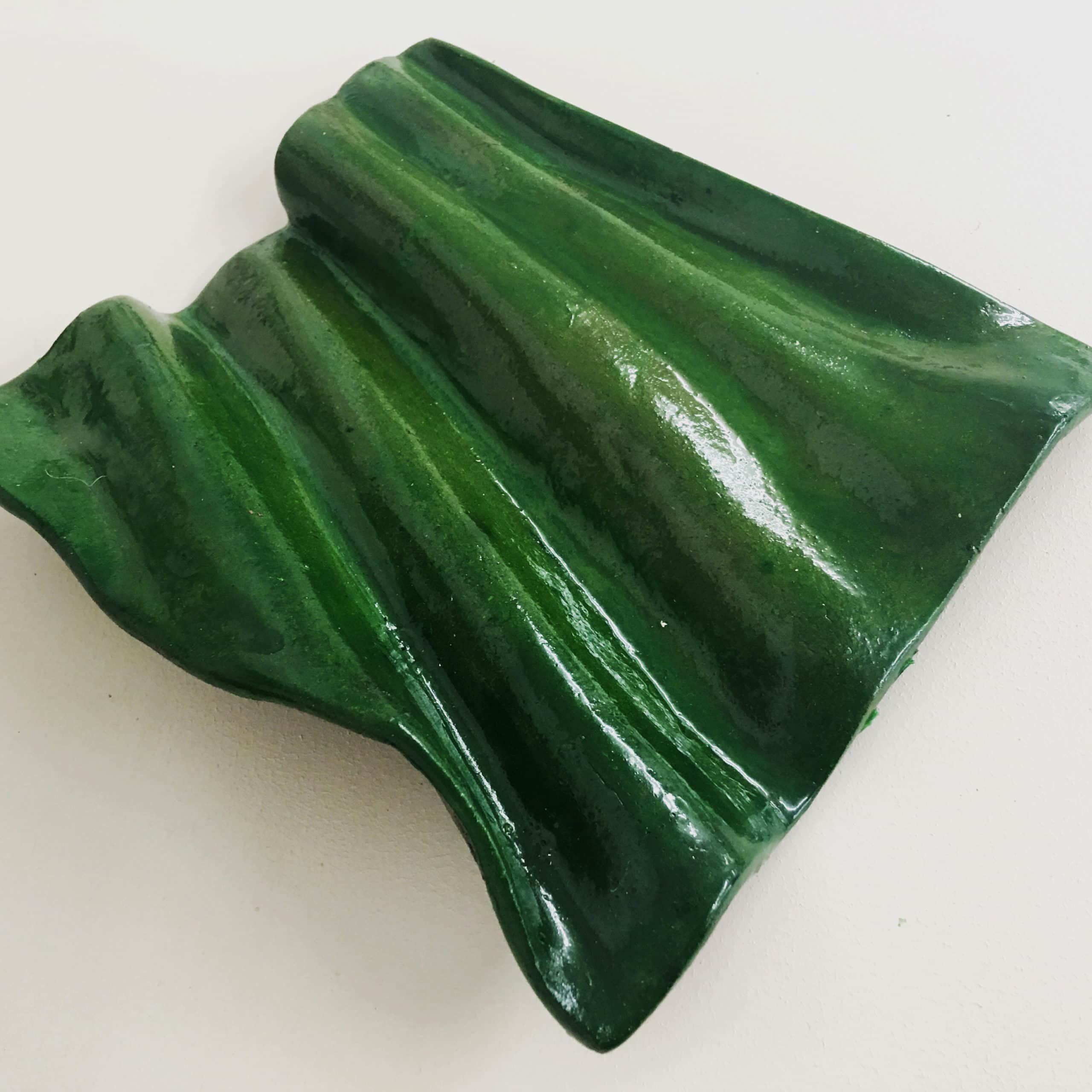
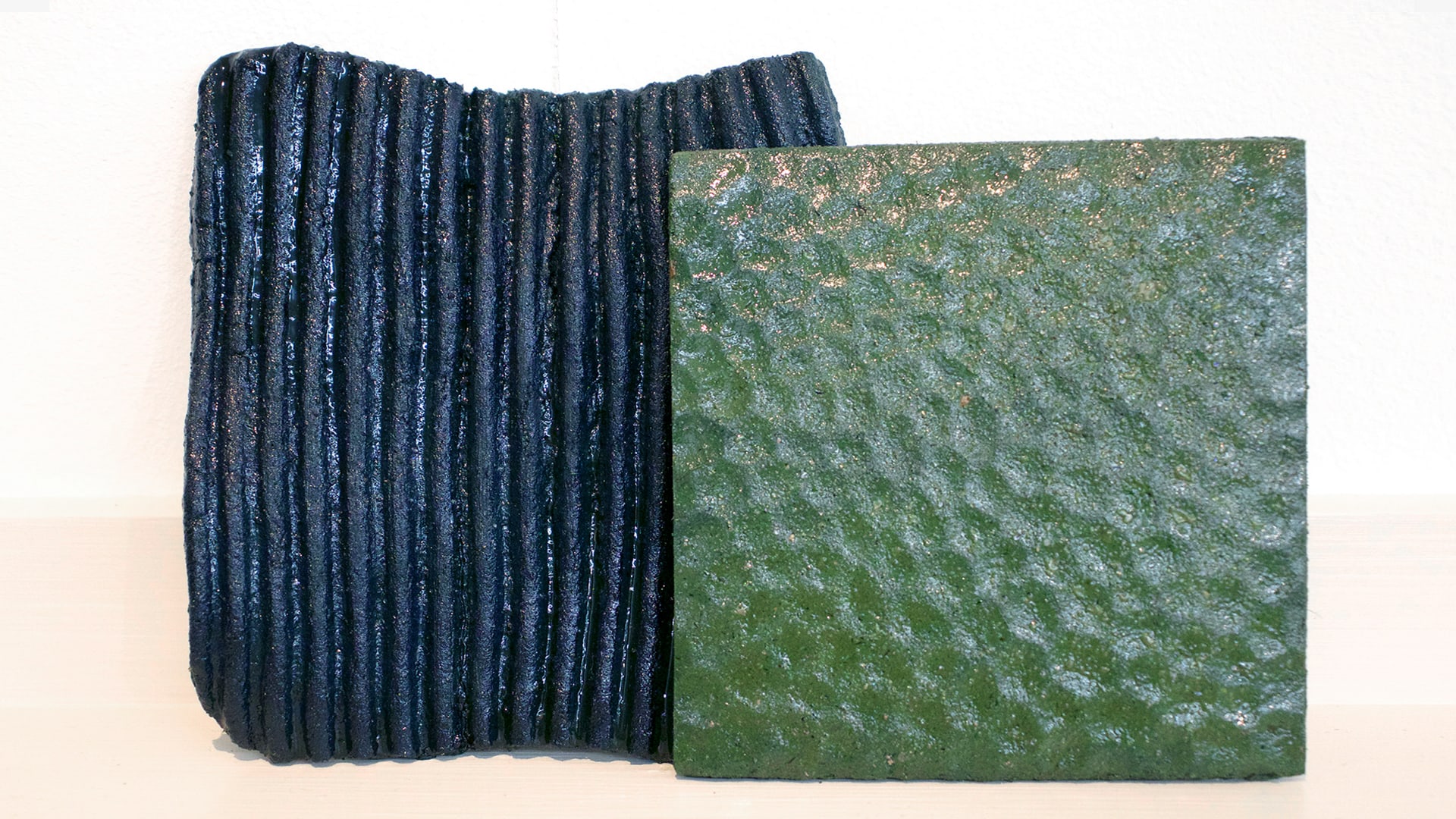
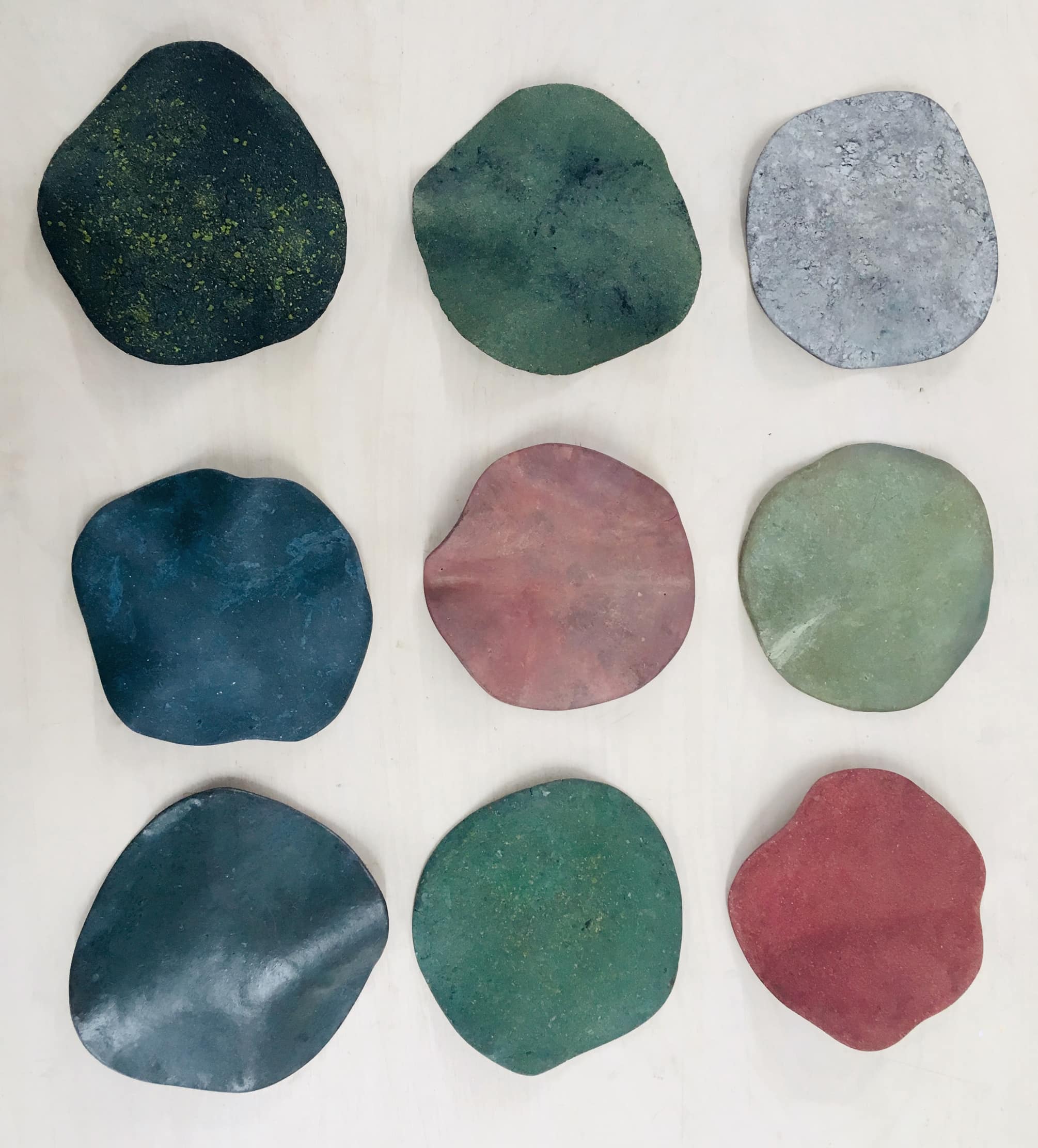
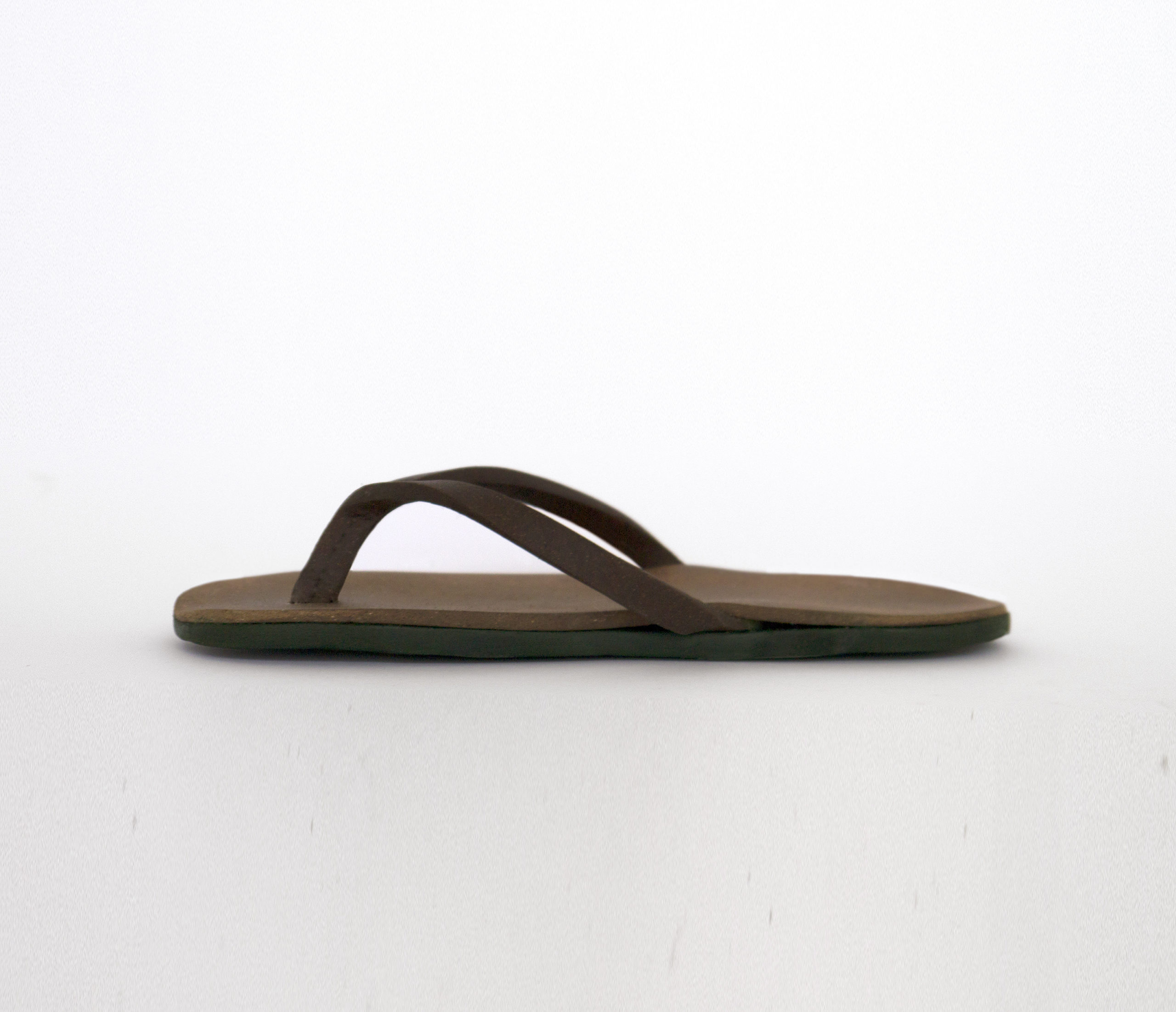
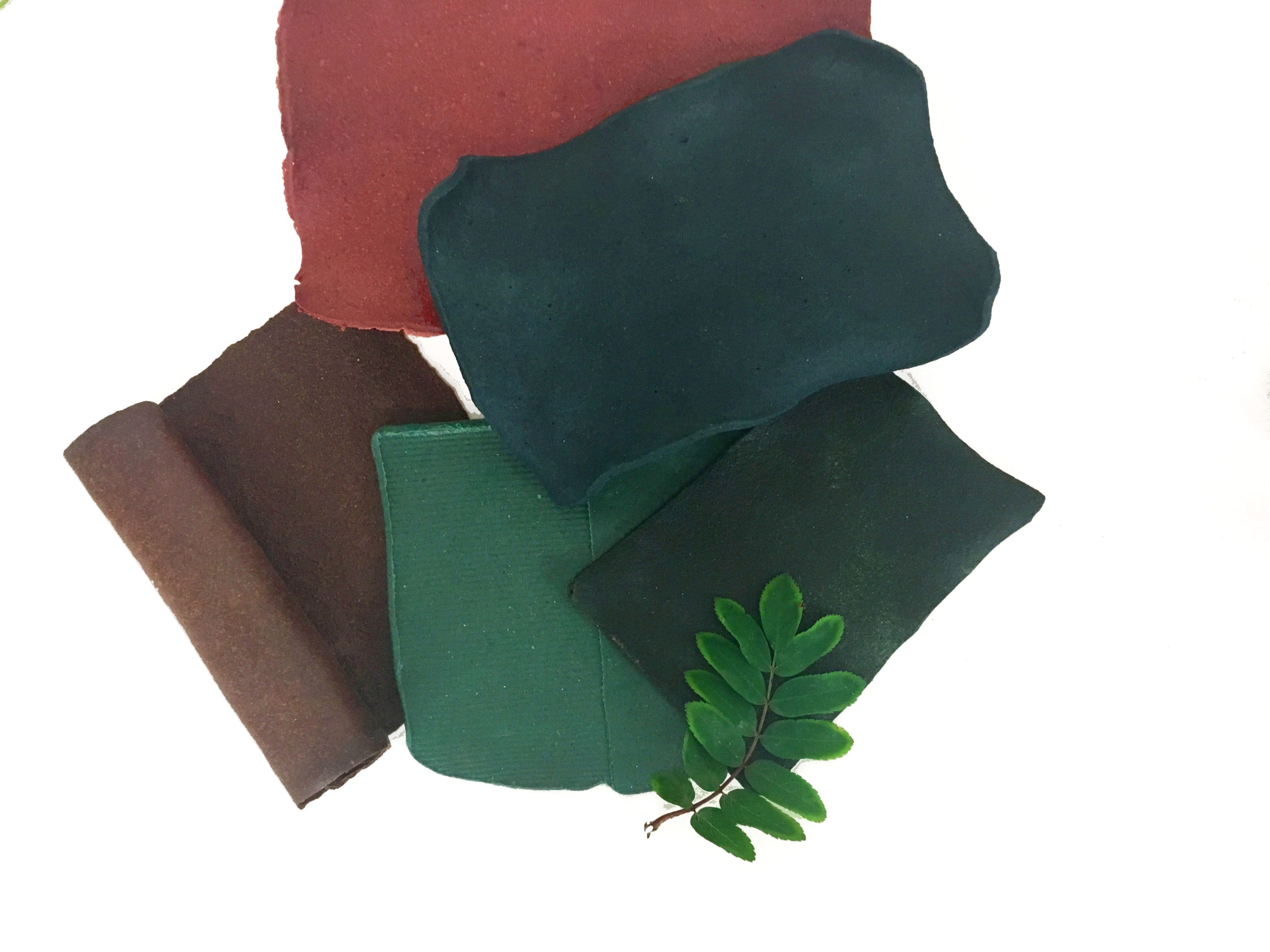
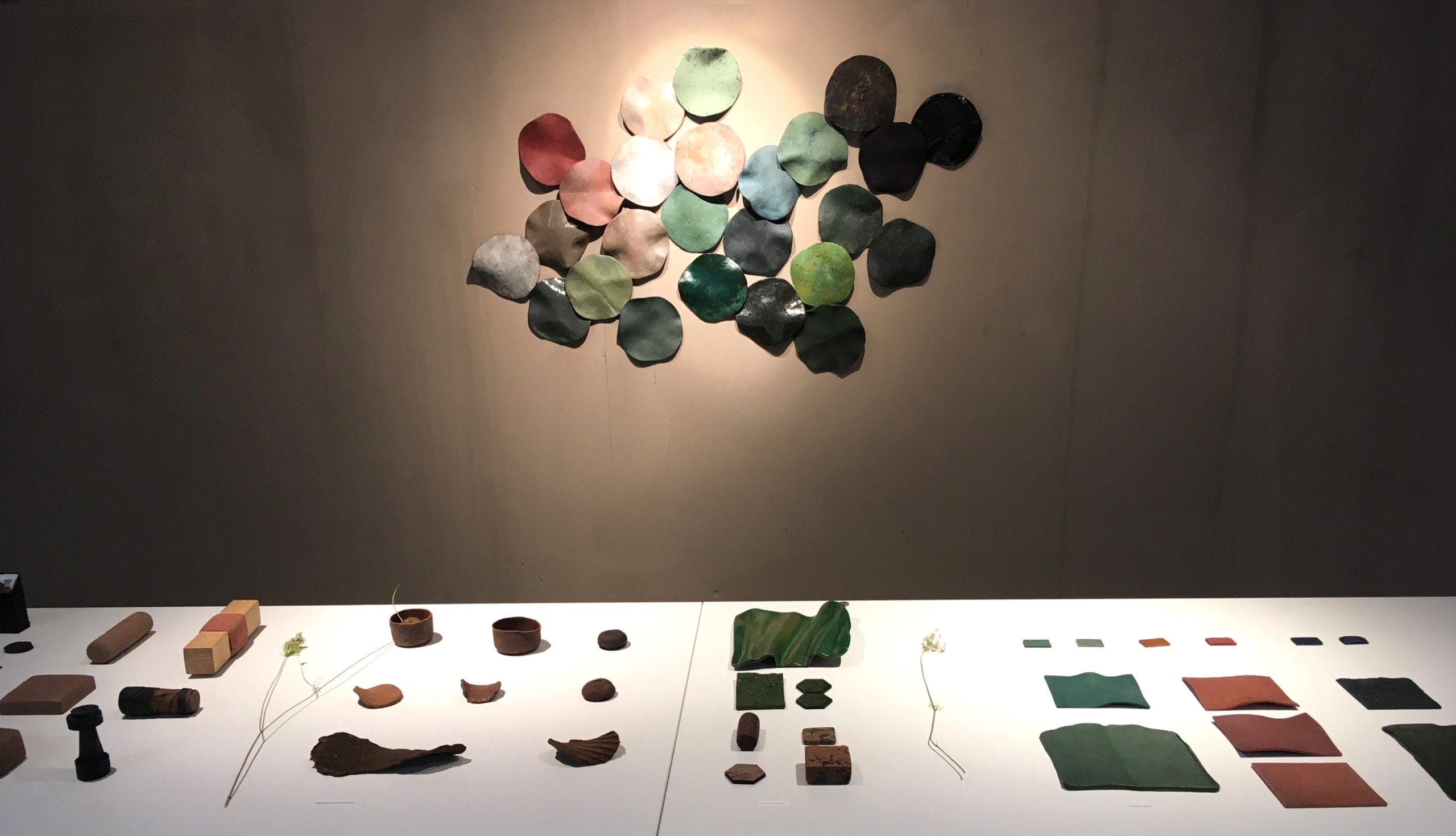
Consumption of Heritage by Sun Lee
Sun Lee is a Korean fashion designer who decided to rethink her process when she realized the scope of how many clothes—hers included—are thrown out once the season passes. Feeling skeptical about the fashion industry, she decided to do an MA in Social Design at the Design Academy Eindhoven and this is her graduation project.
Consumption of Heritage is a balanced and circular collection inspired by Korean heritage, introducting traditional production methods and materials into a contemporary context. These handmade garments are entirely composed of biodegradable Hansan-Mosi fabric and Hanji paper.
Old and new techniques are combined, and modular pieces can be worn in several ways. The result is a layered collection that passes on tradition to a new generation.
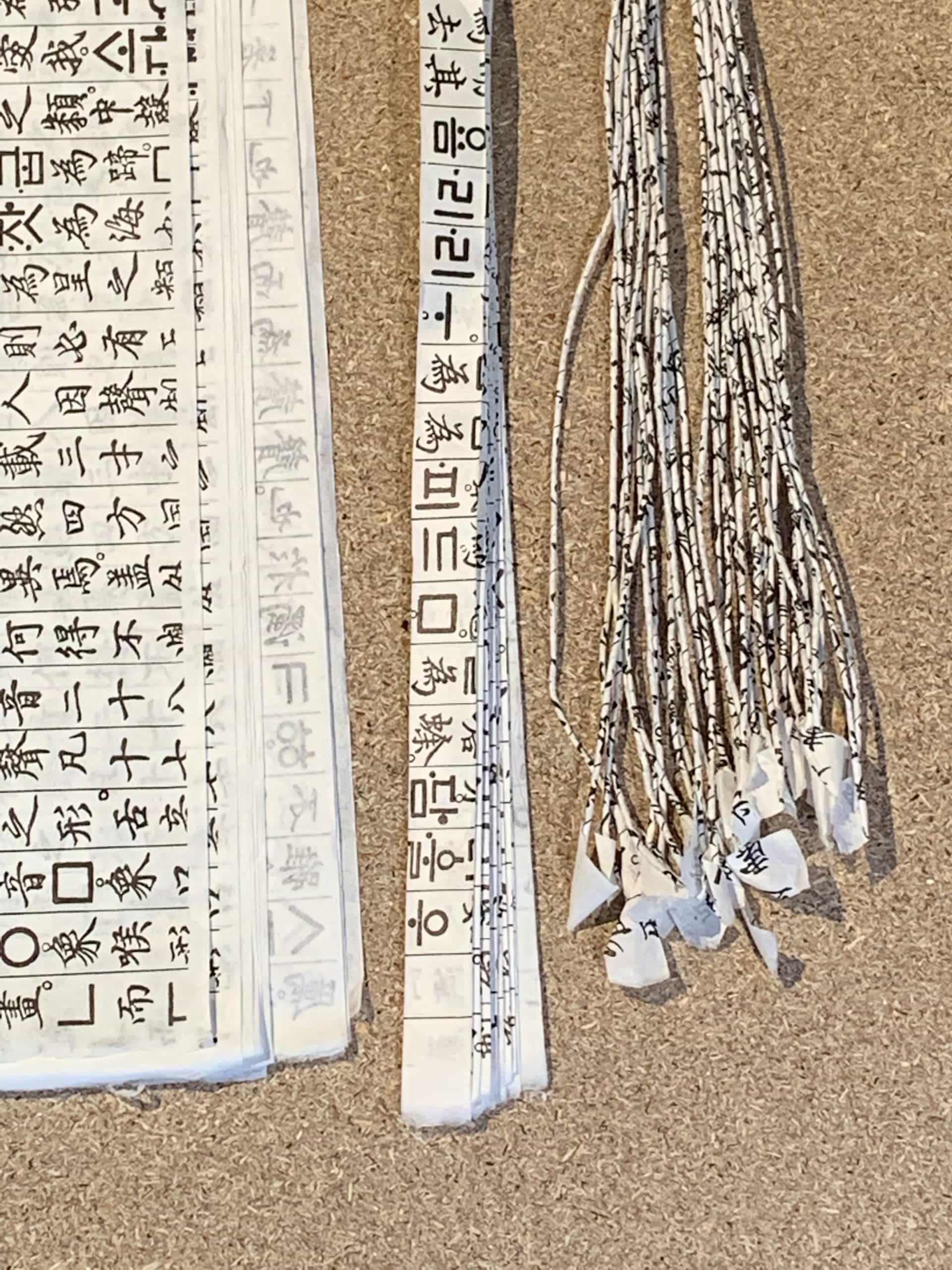
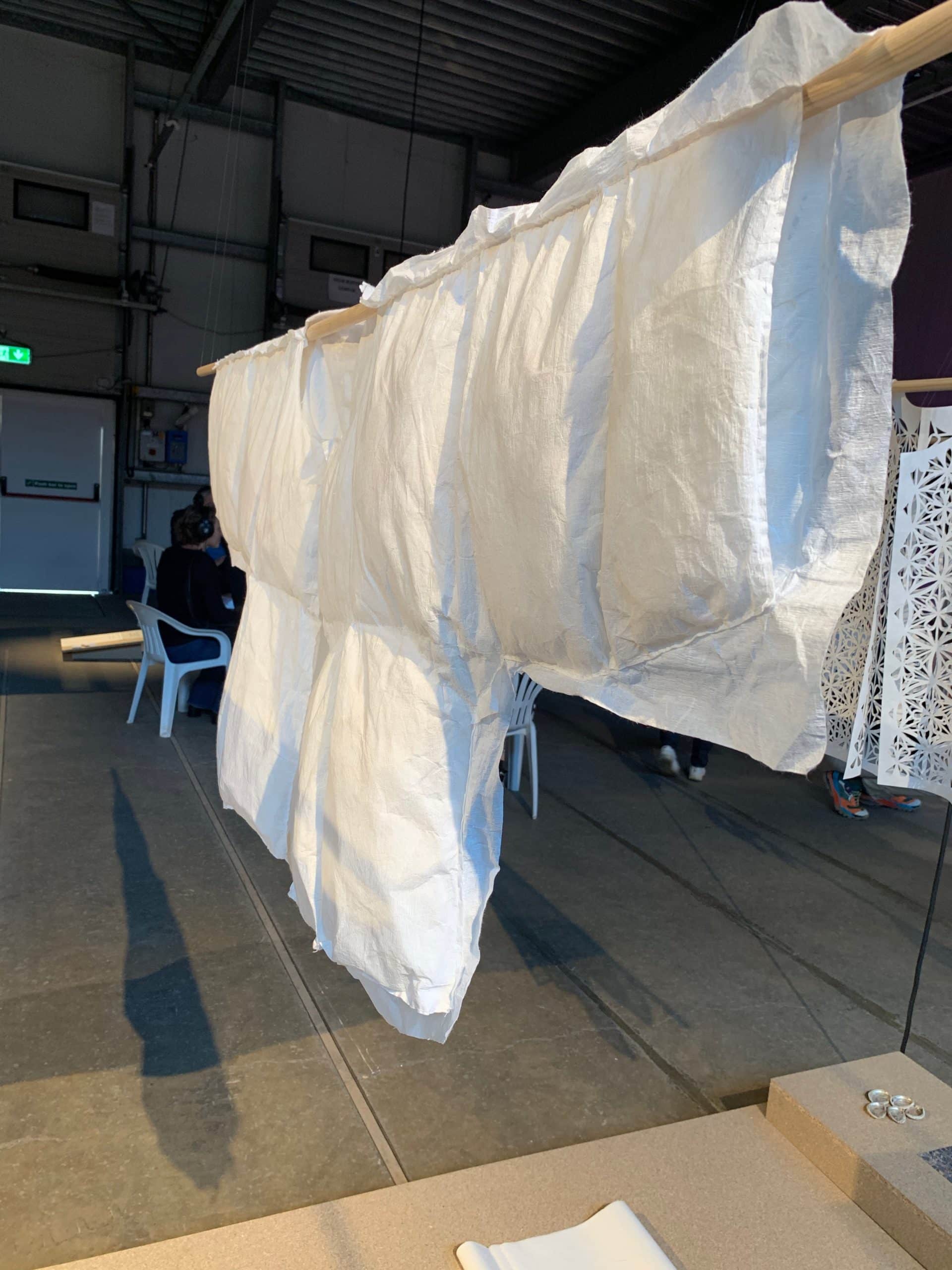
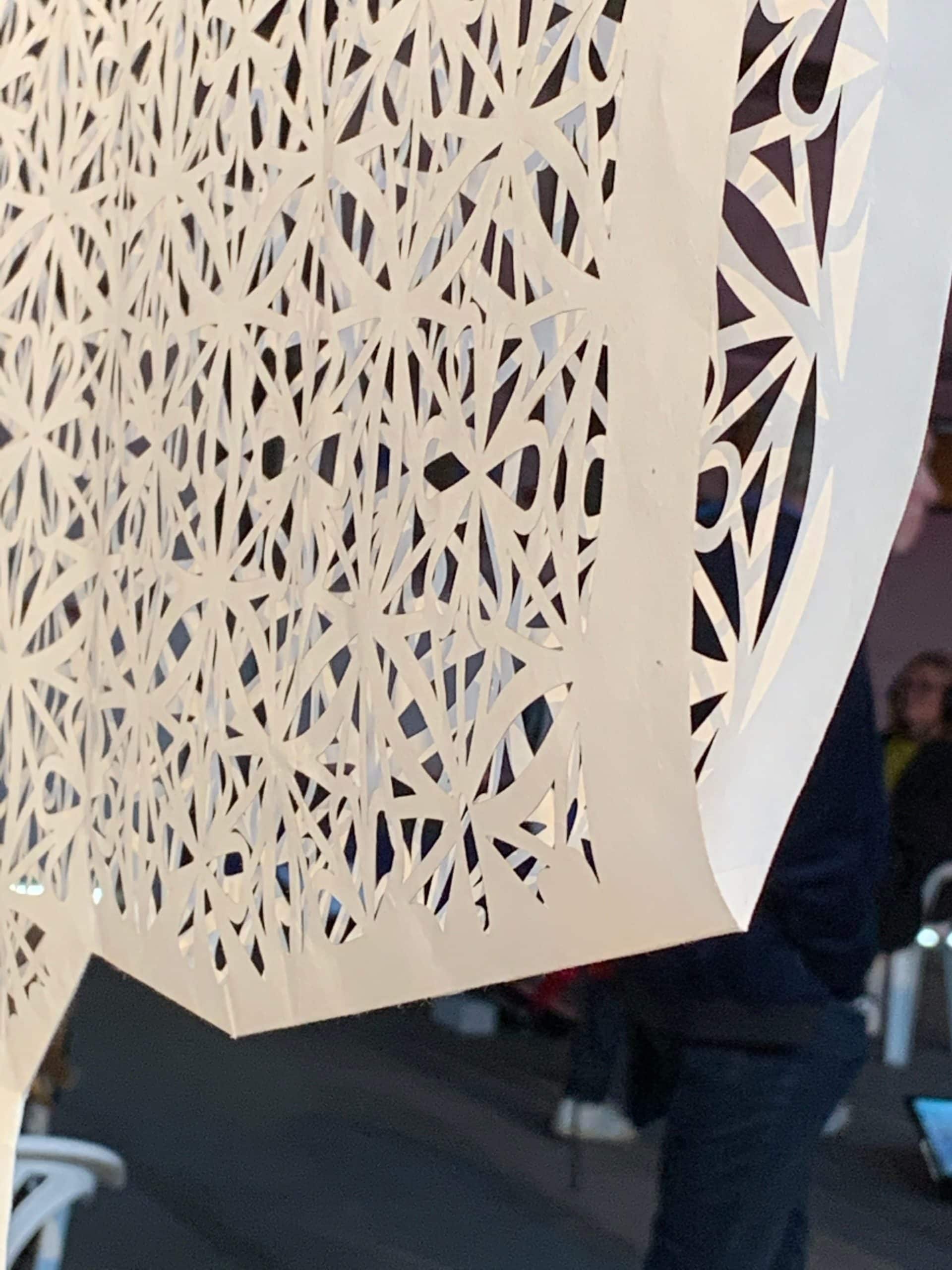
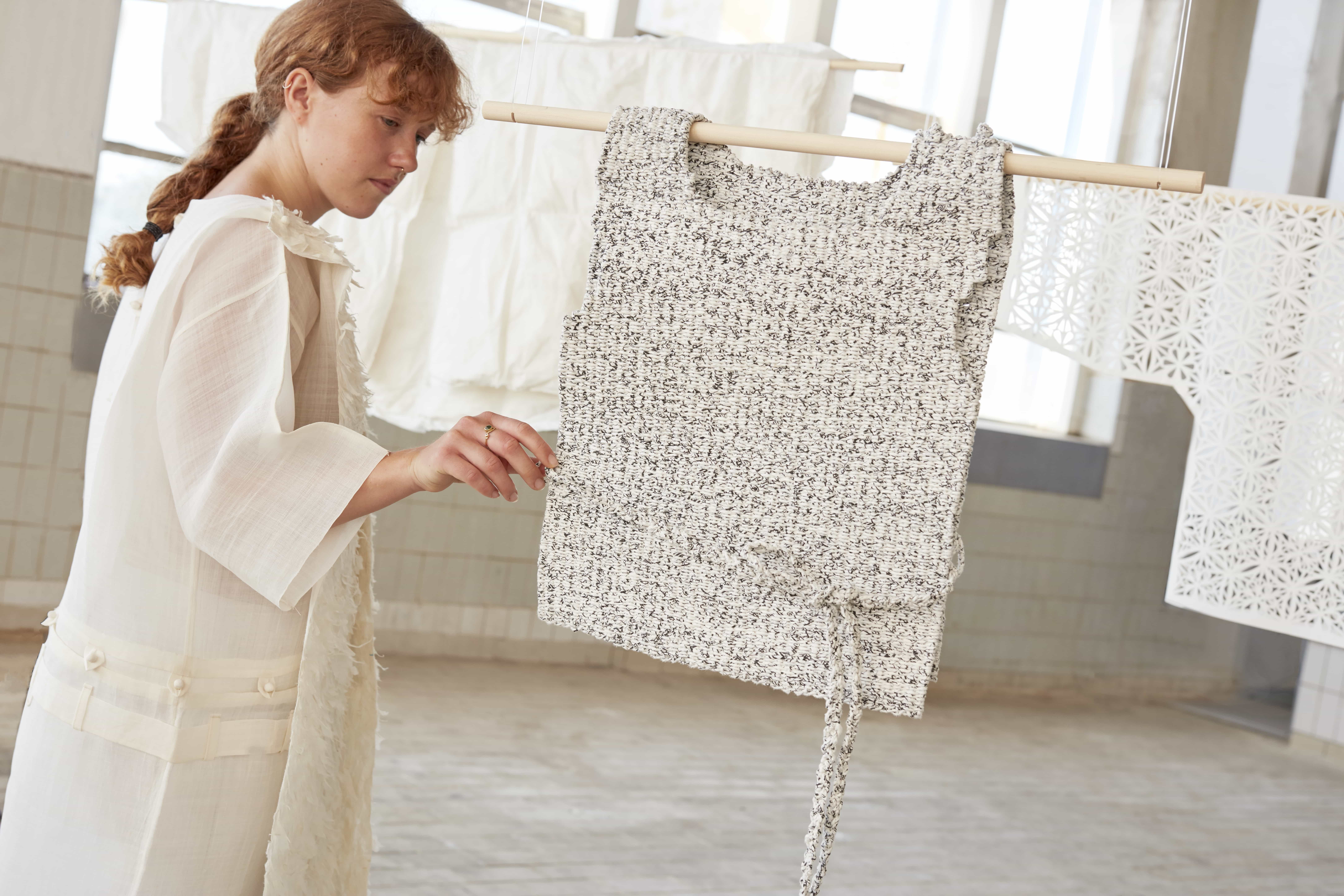
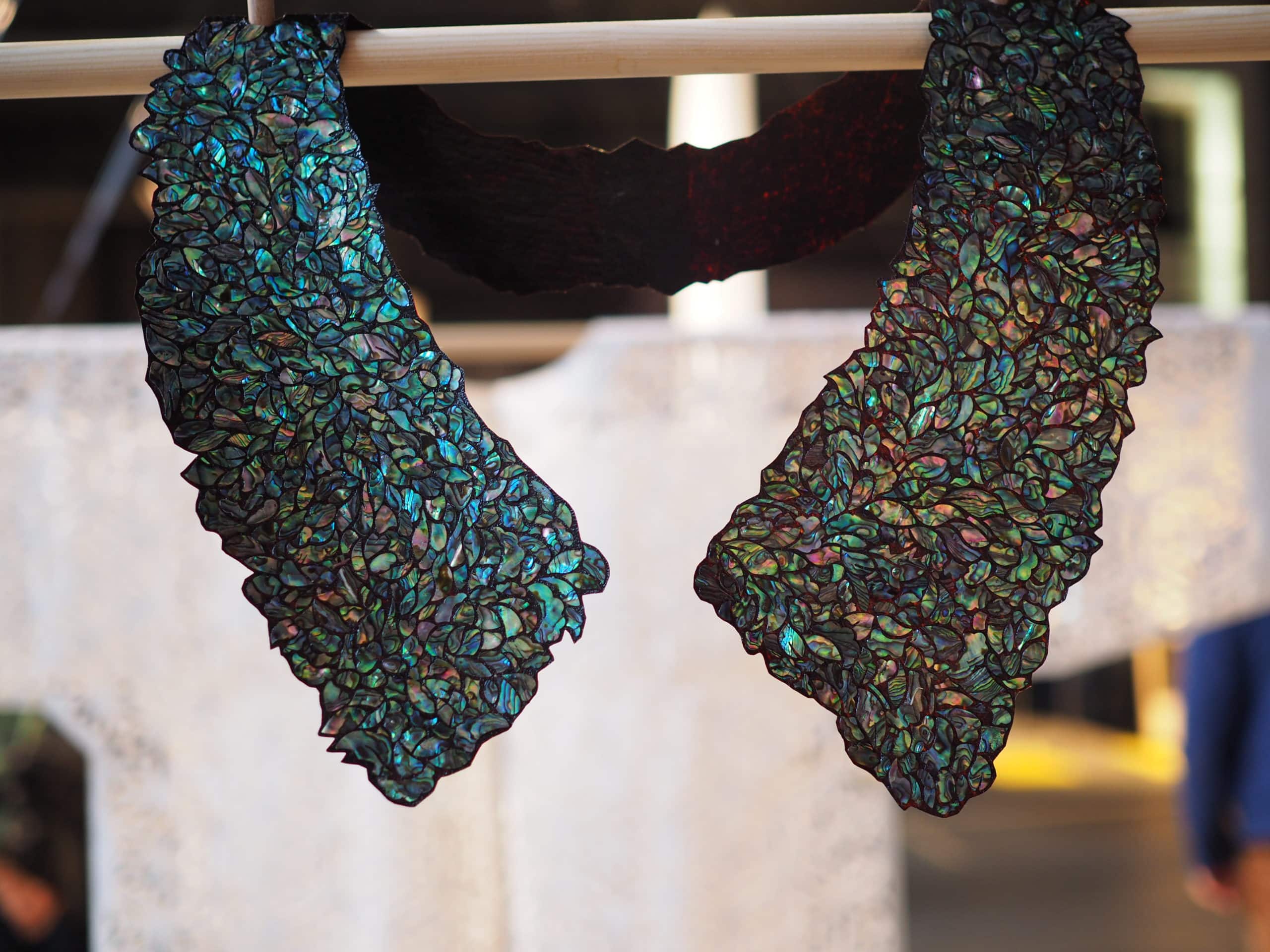
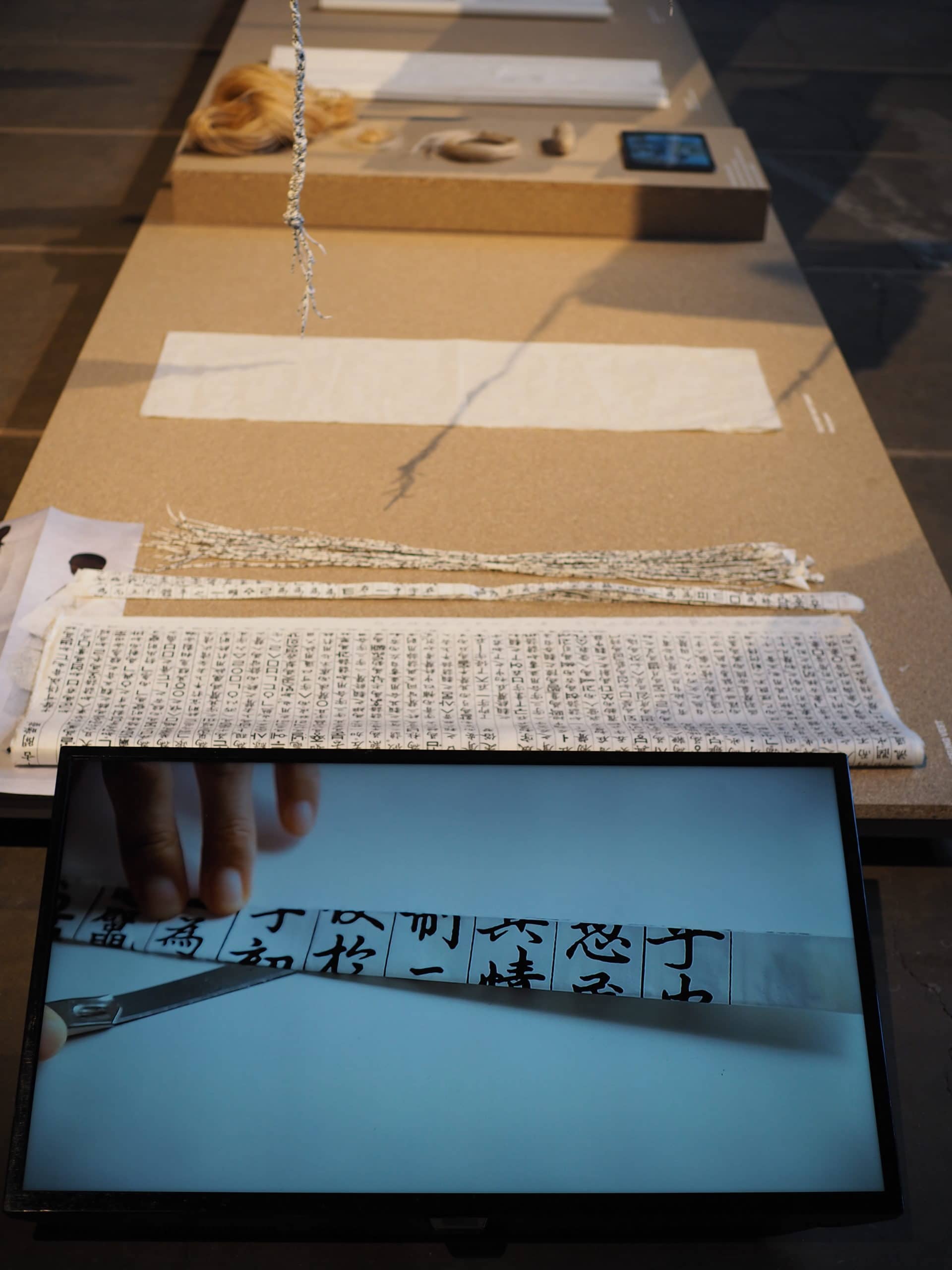
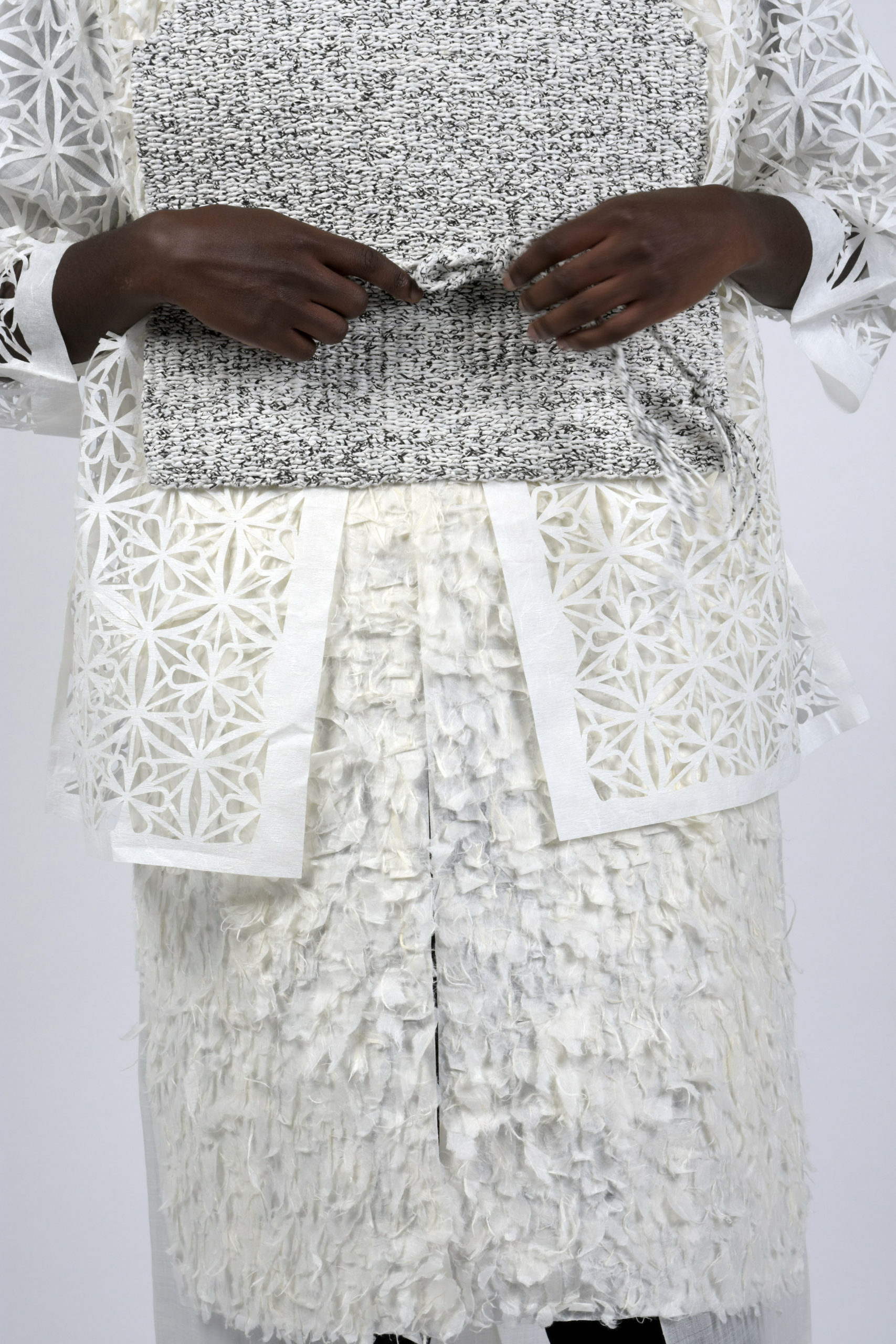
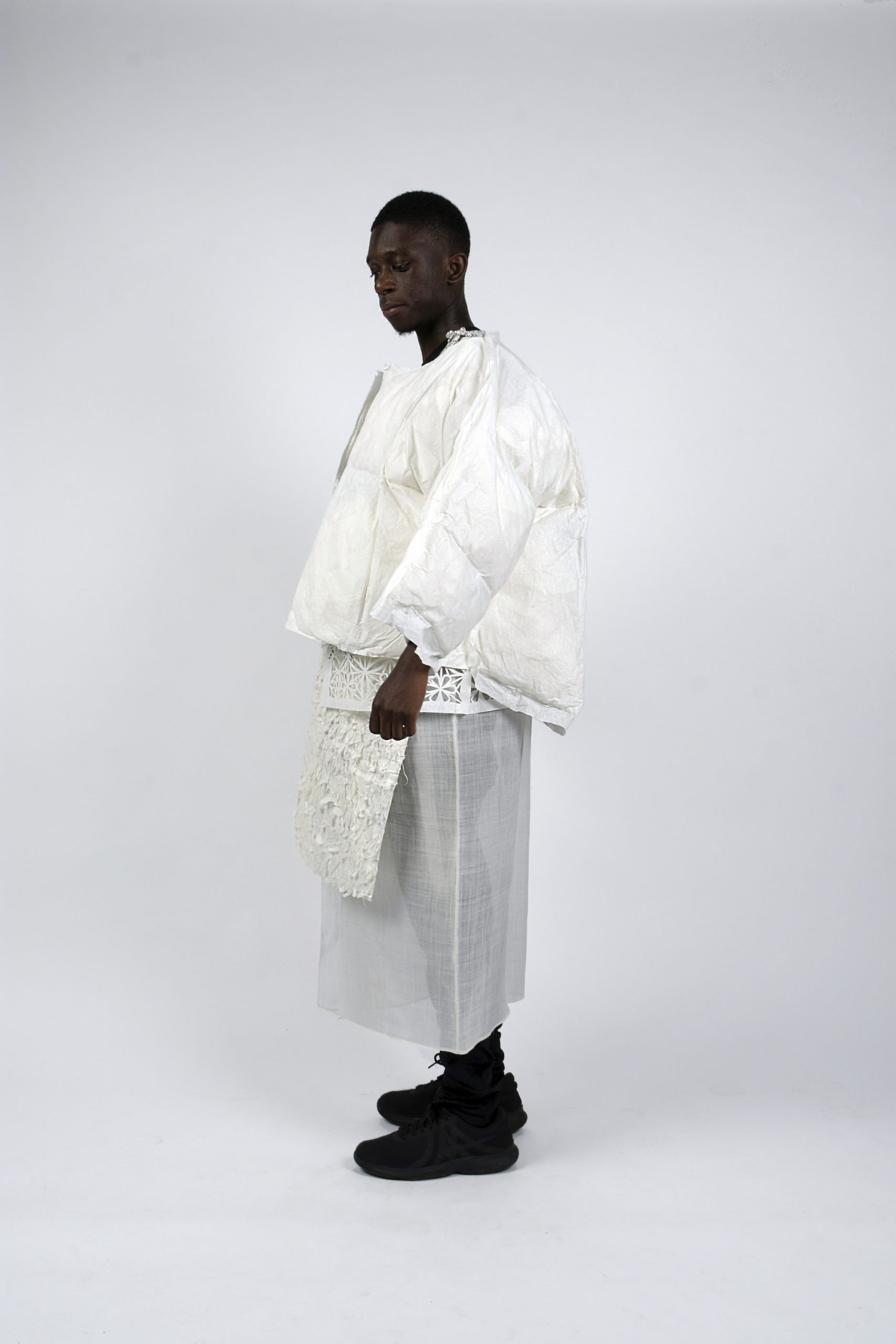
OTT-Another Paradigmatic Ceramic by Seok-Hyeon Yoon
For Seok-Hyeon Yoon’s final project at Design Academy Eindhoven, he created a system for recycling ceramic objects using Ott, a traditional Korean lacquering material made from wood resin. Once widely used in Seok-Hyeon’s native Korea as a glazing for woodenware, he utilized its unique properties for a collection of ceramic tableware (which won him the René Smeets Award). Ceramics are not usually recyclable as the glazes are toxic. They mostly end up in landfill, resulting in environmental pollution and wasting materials. When used for glazing ceramics, Ott doesn’t need to be baked, also evaporating at high temperatures so ceramics can be recolored and redesigned.
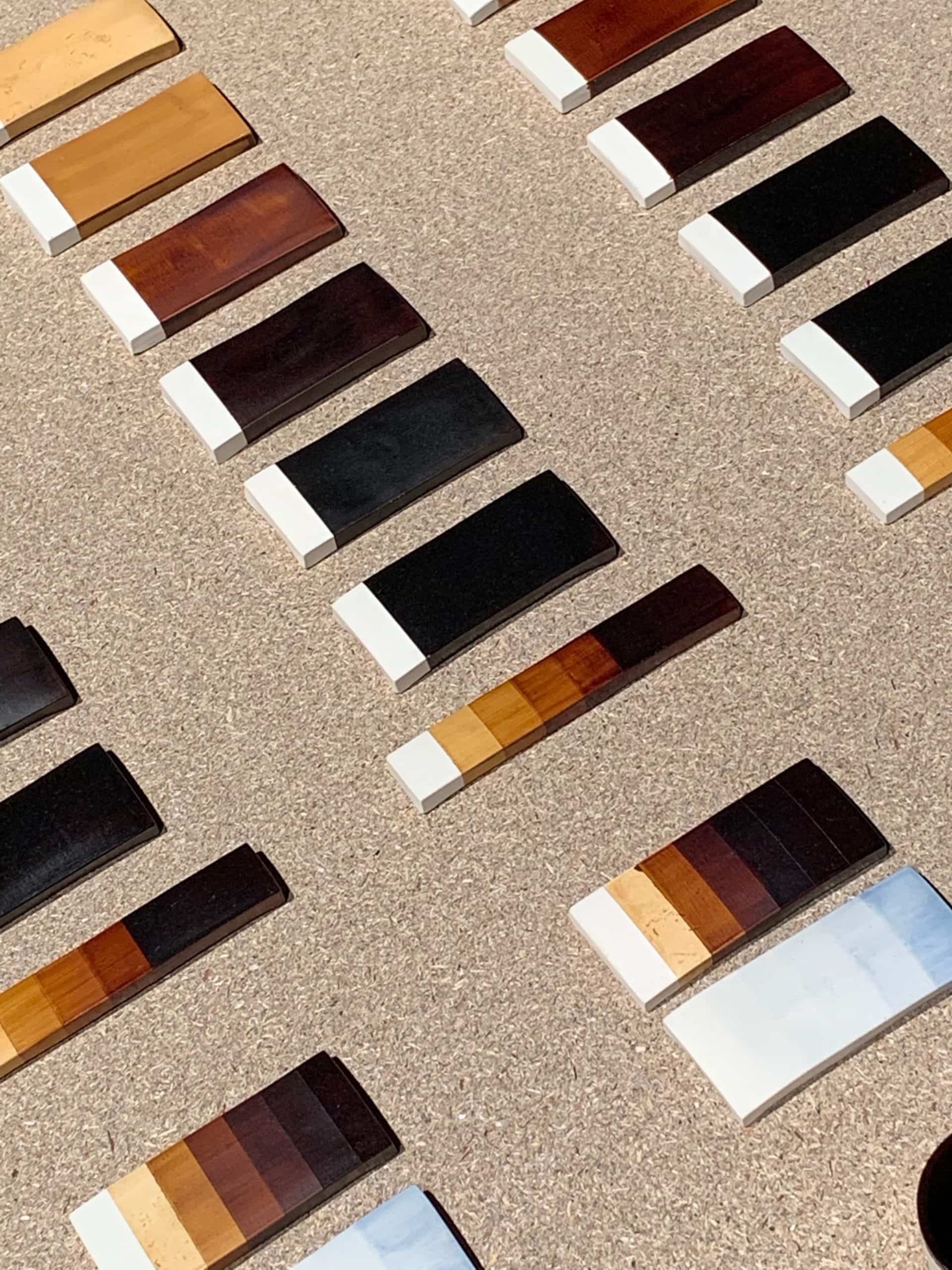
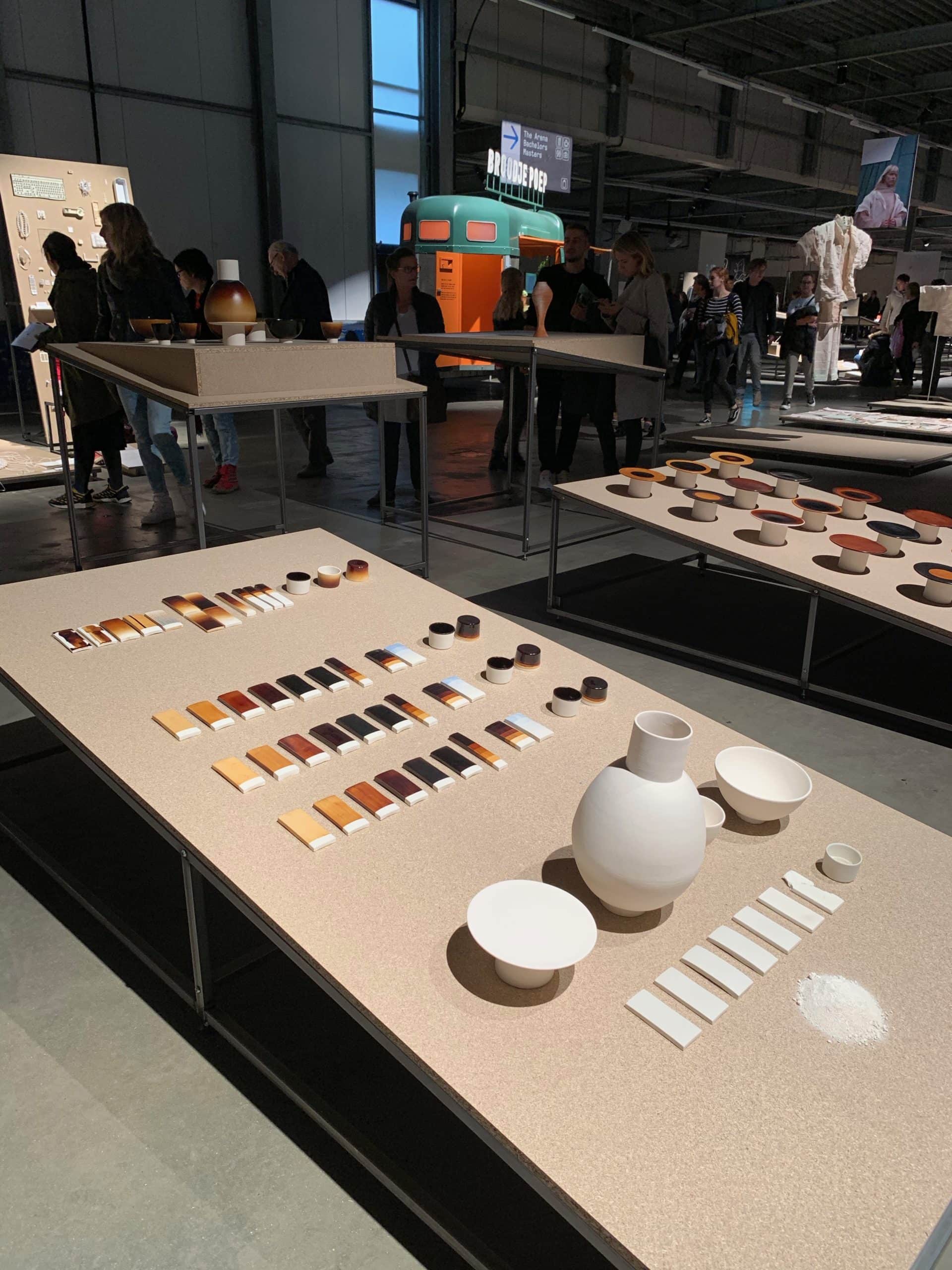
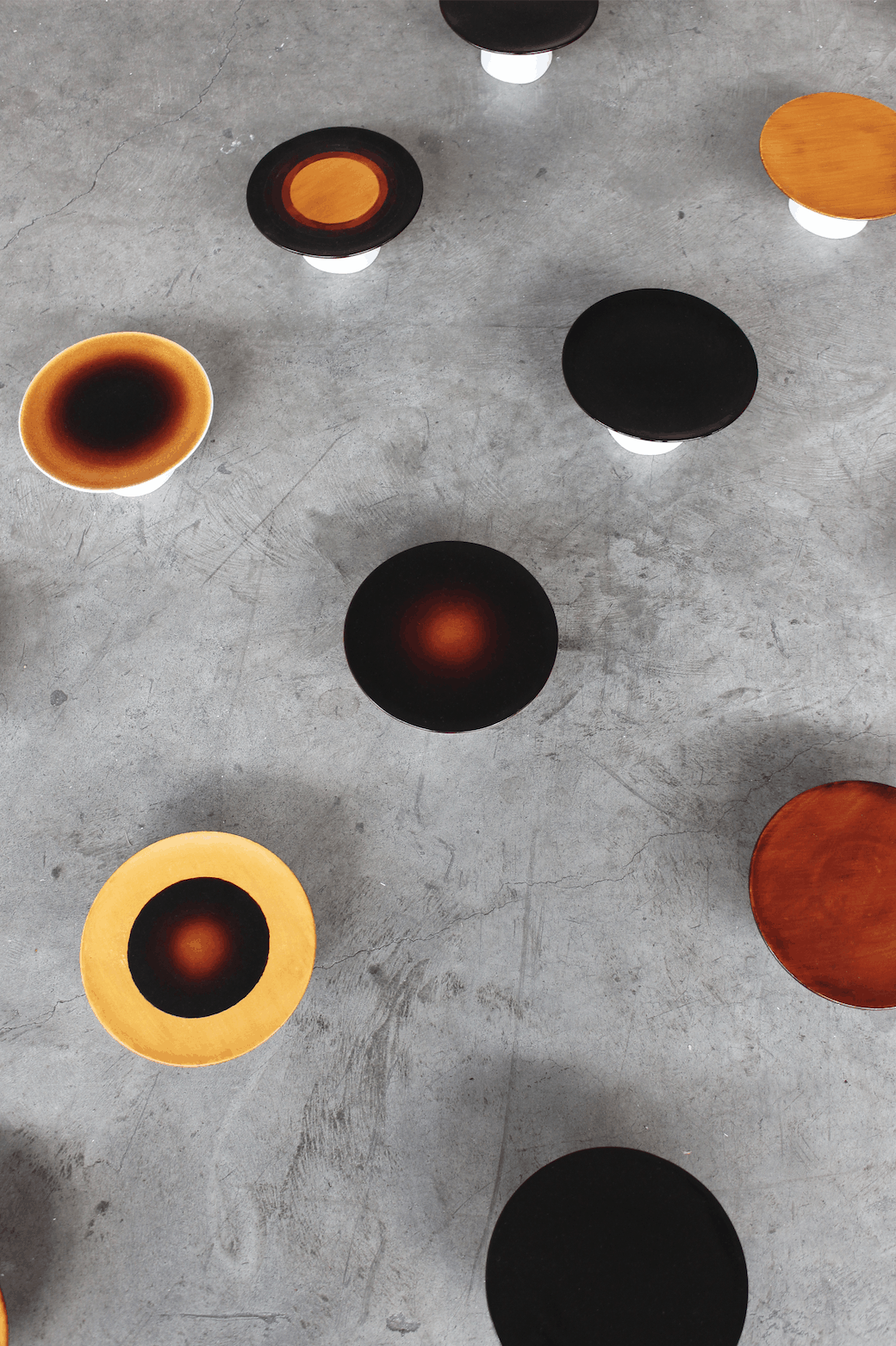
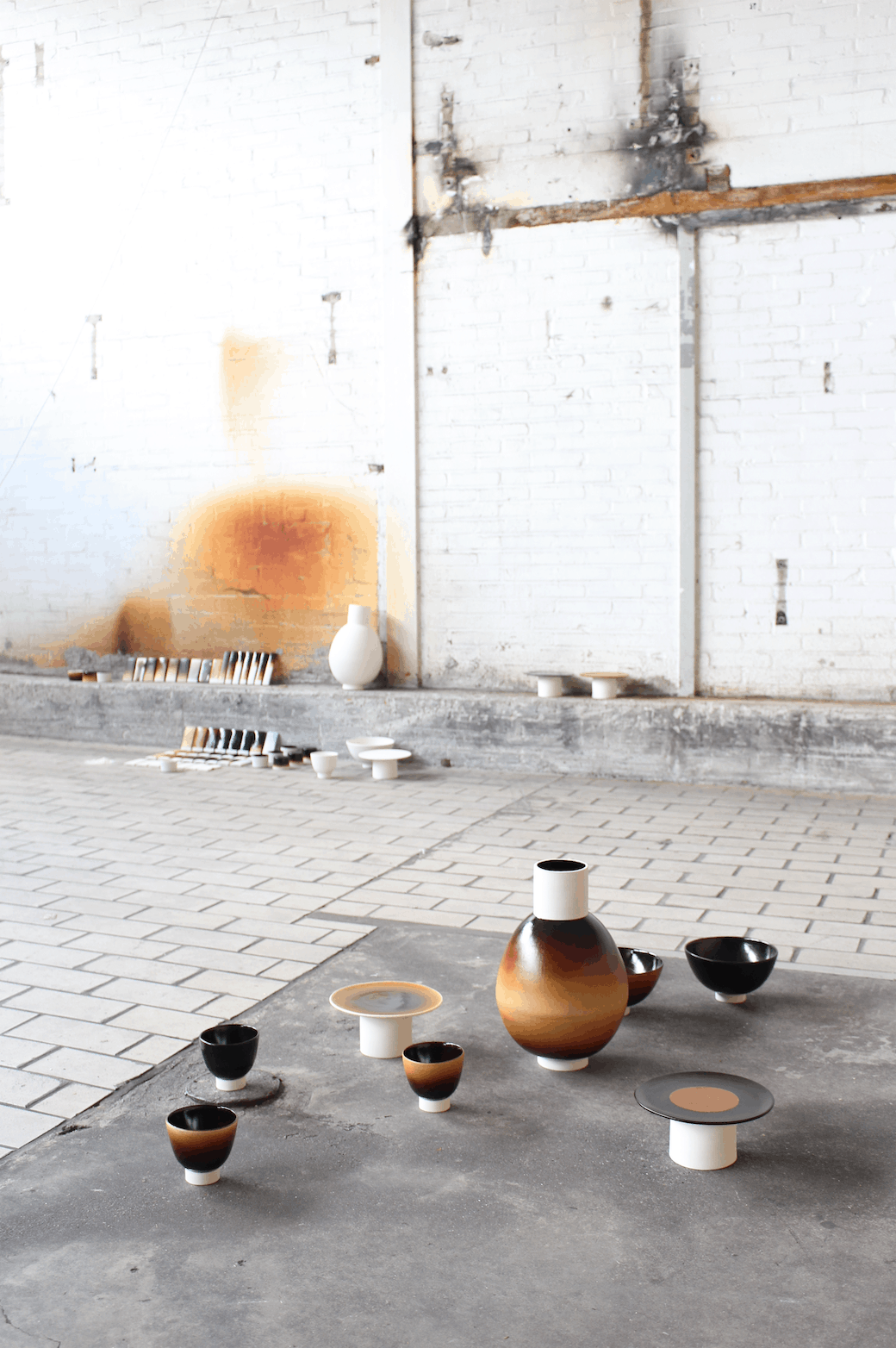
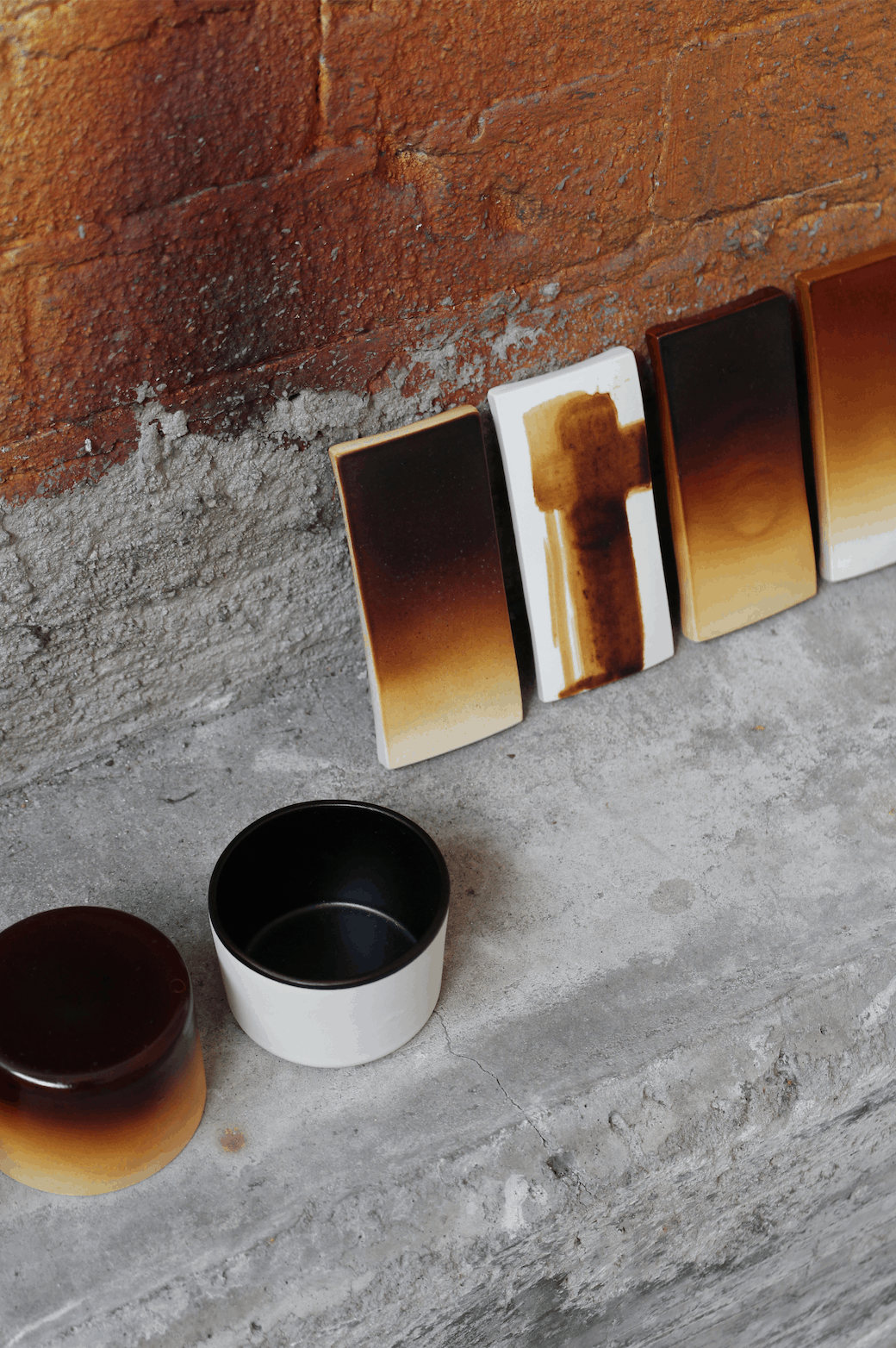
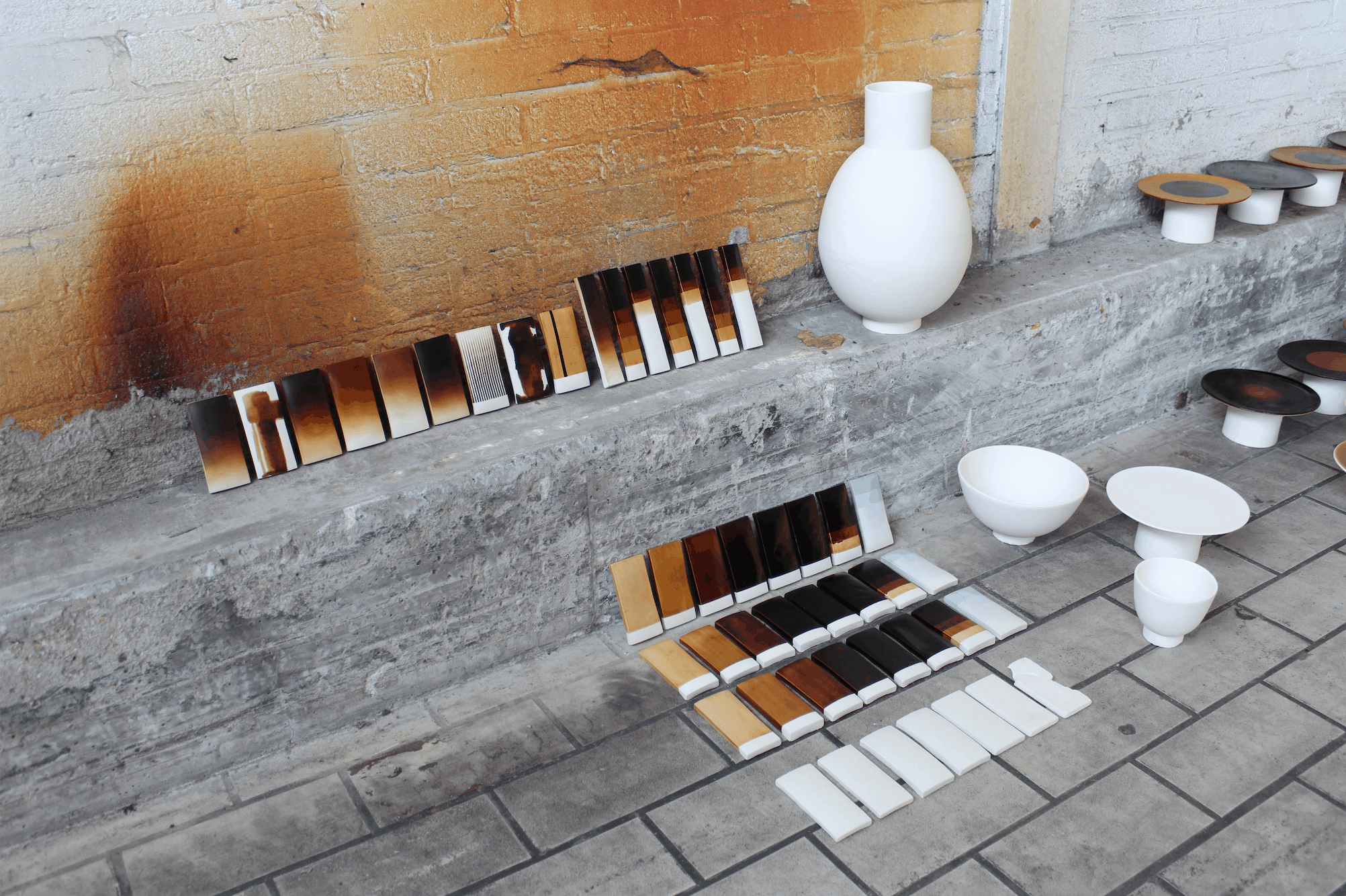
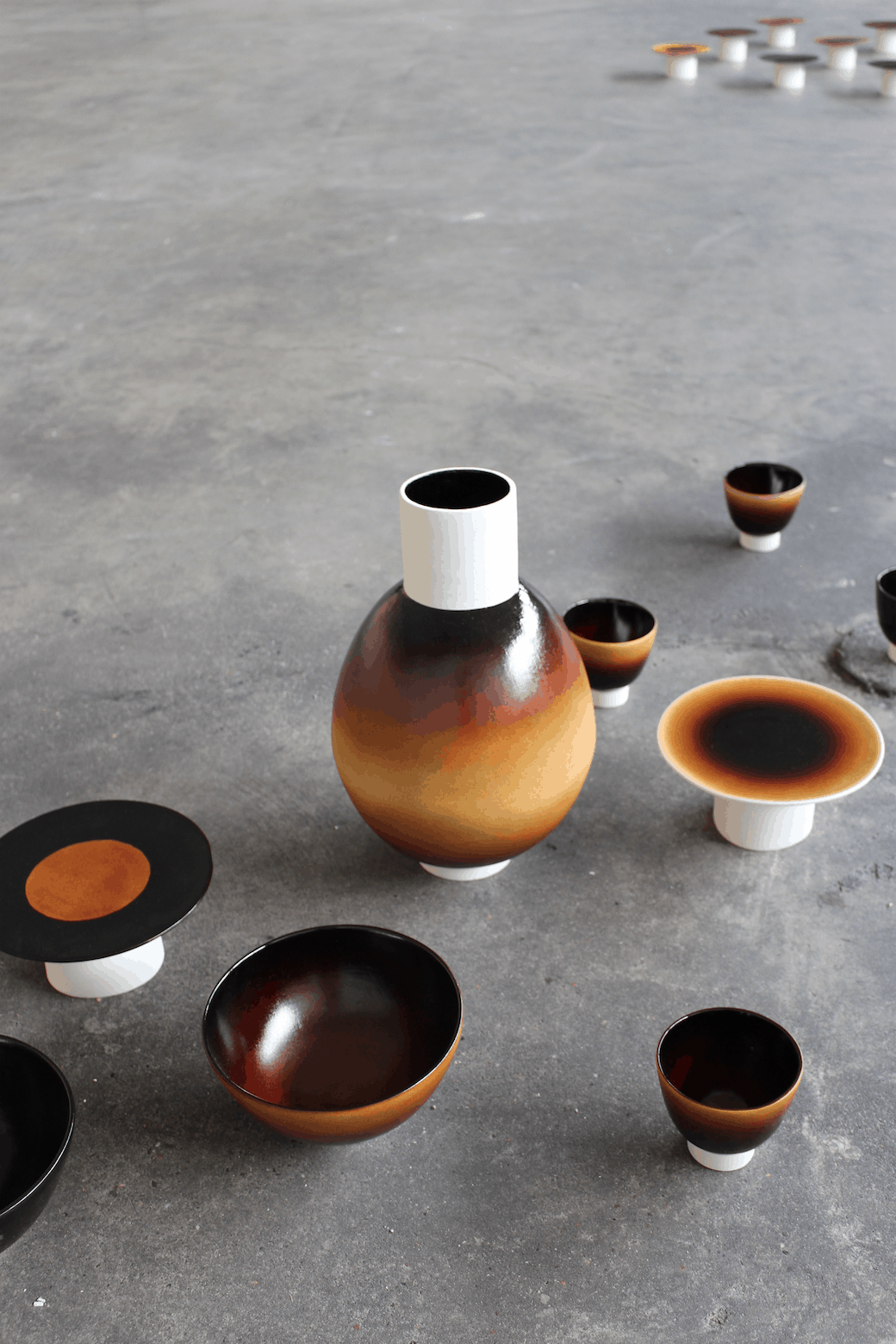
Pulp Fiction by Lab-la-bla
Pulp Fiction is Lab-la-bla's cross-disciplinary collaboration, focused on highlighting the potential for unwanted matter. New bio-composites are manufactured from the waste and by-products sourced from Sweden’s top three industries: mining, agriculture, and forestry.
All objects are produced from materials such as bone ash, pine resin and factory floor dust and are biodegradable and bio-enhancing, adding nutrients to the soil when disposed. What, at first, looks like a playful experiment is based on a very serious idea showing the limitless potential of our industrial waste.
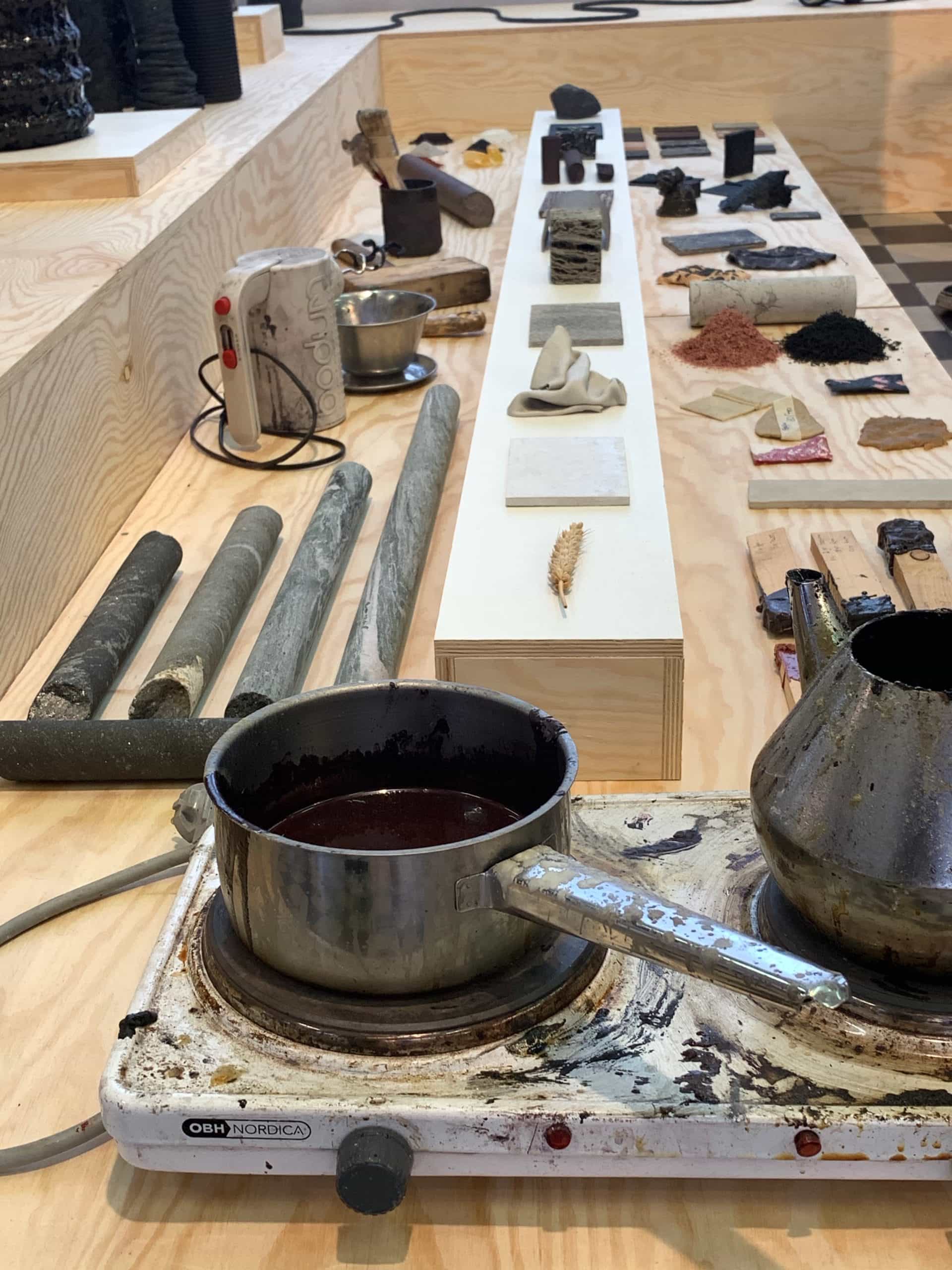
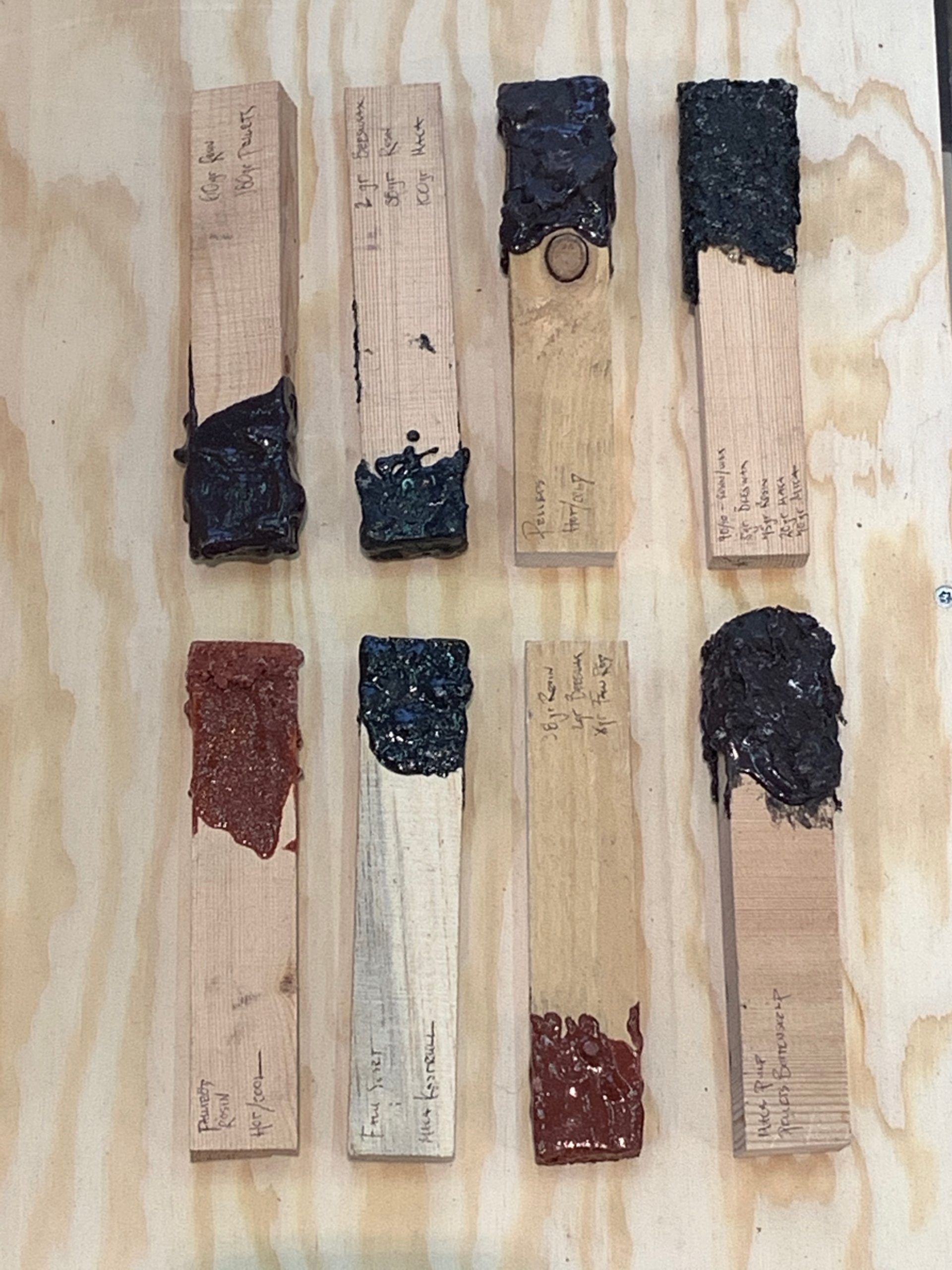
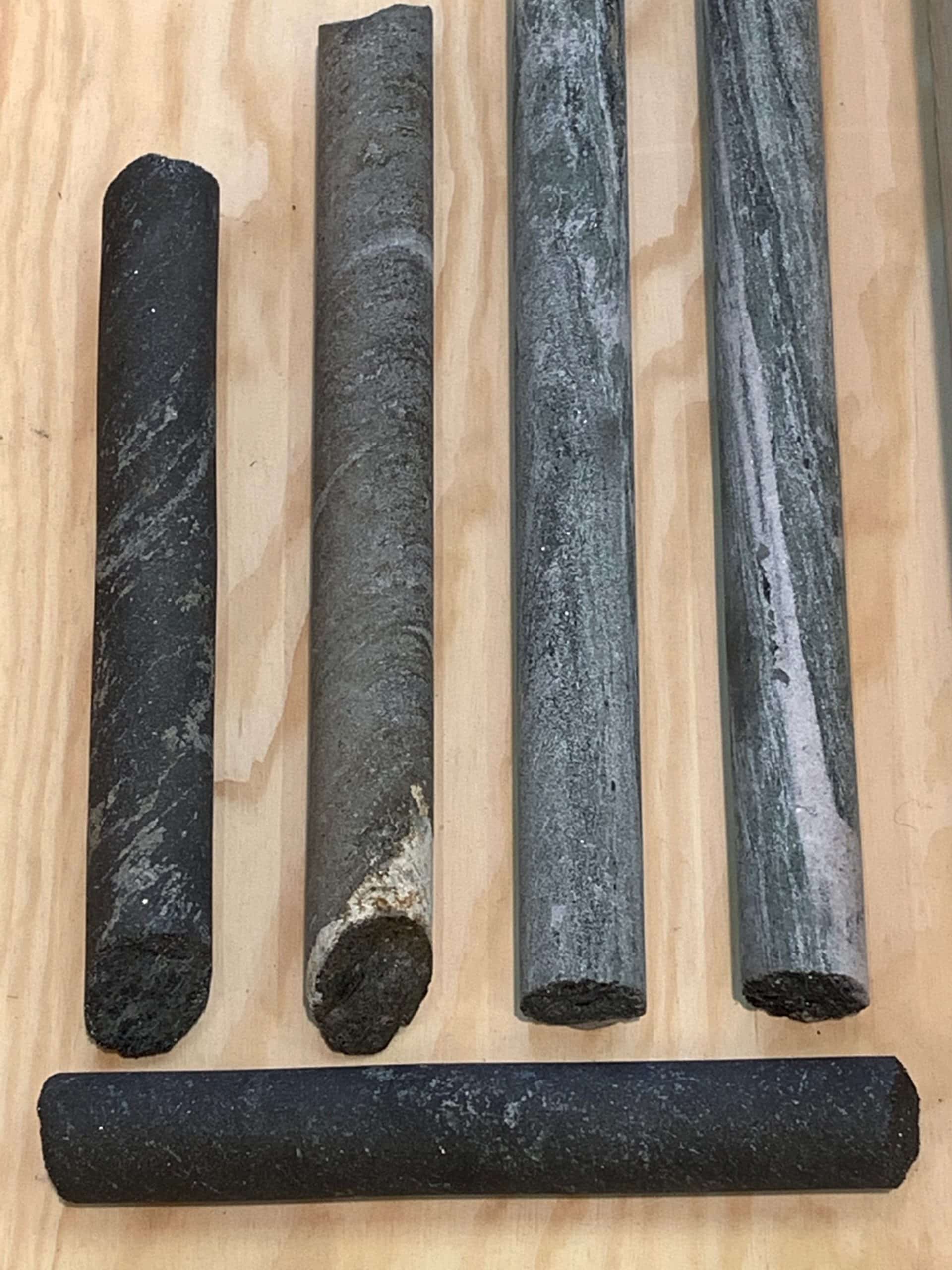
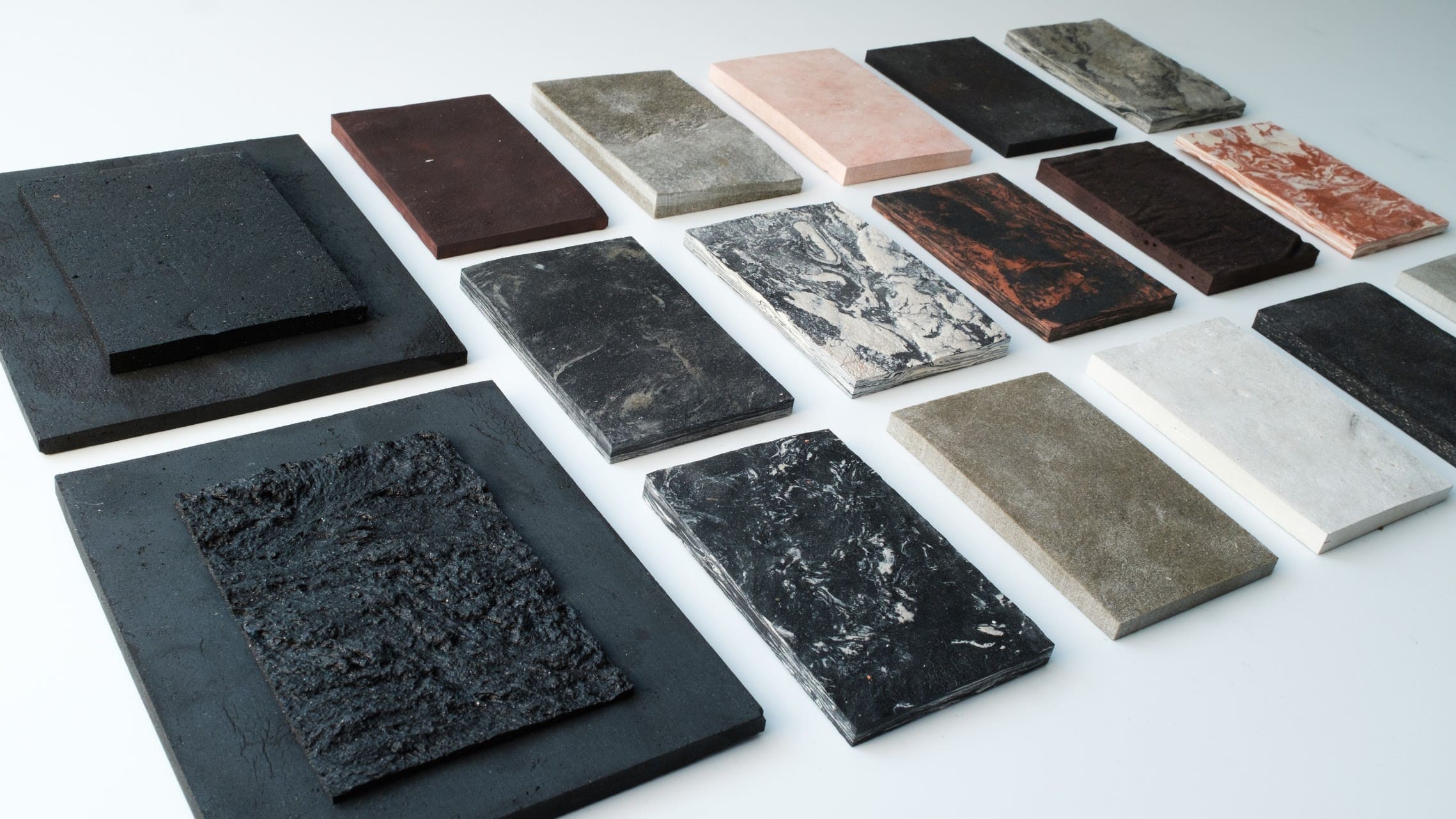
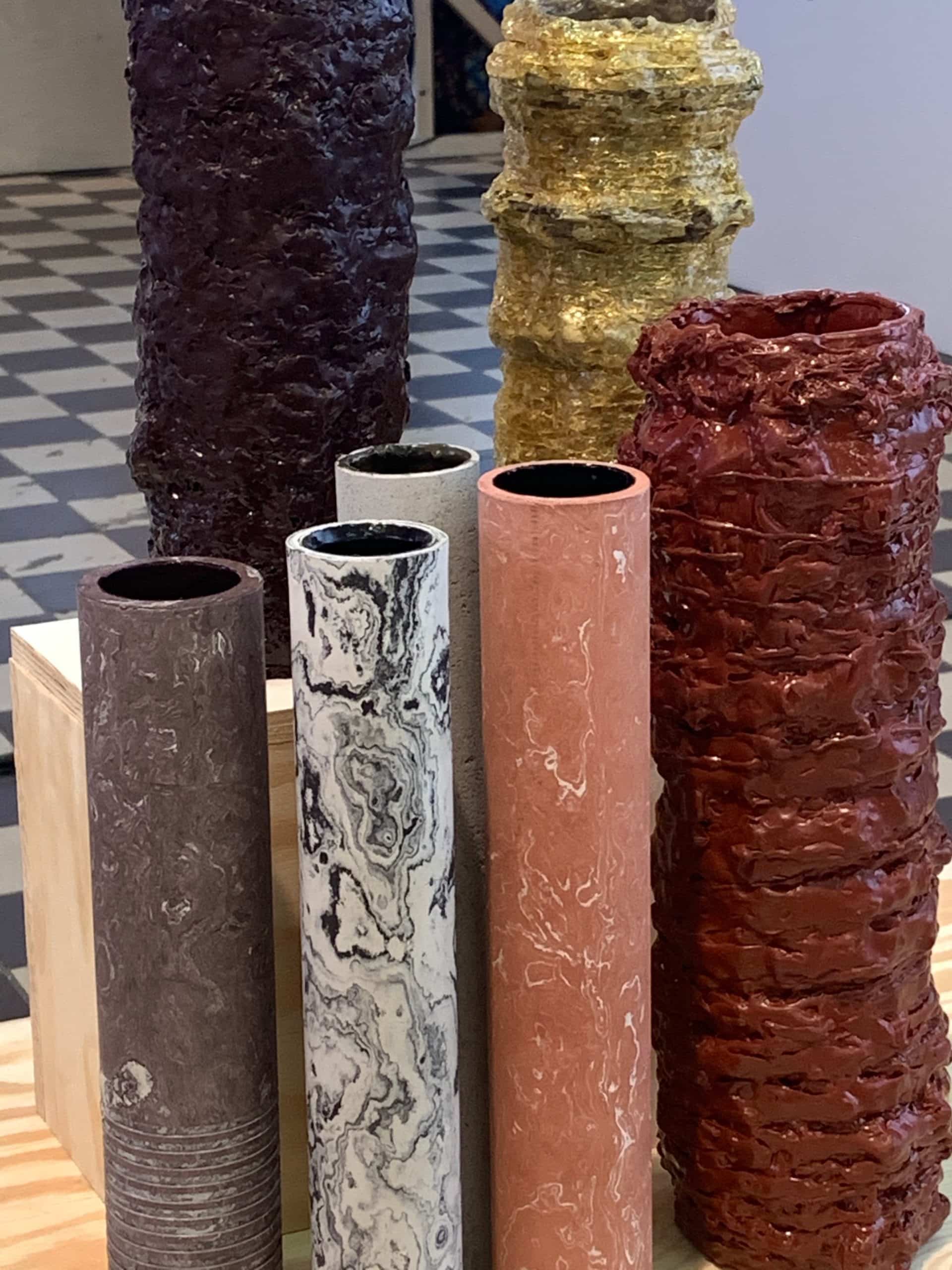

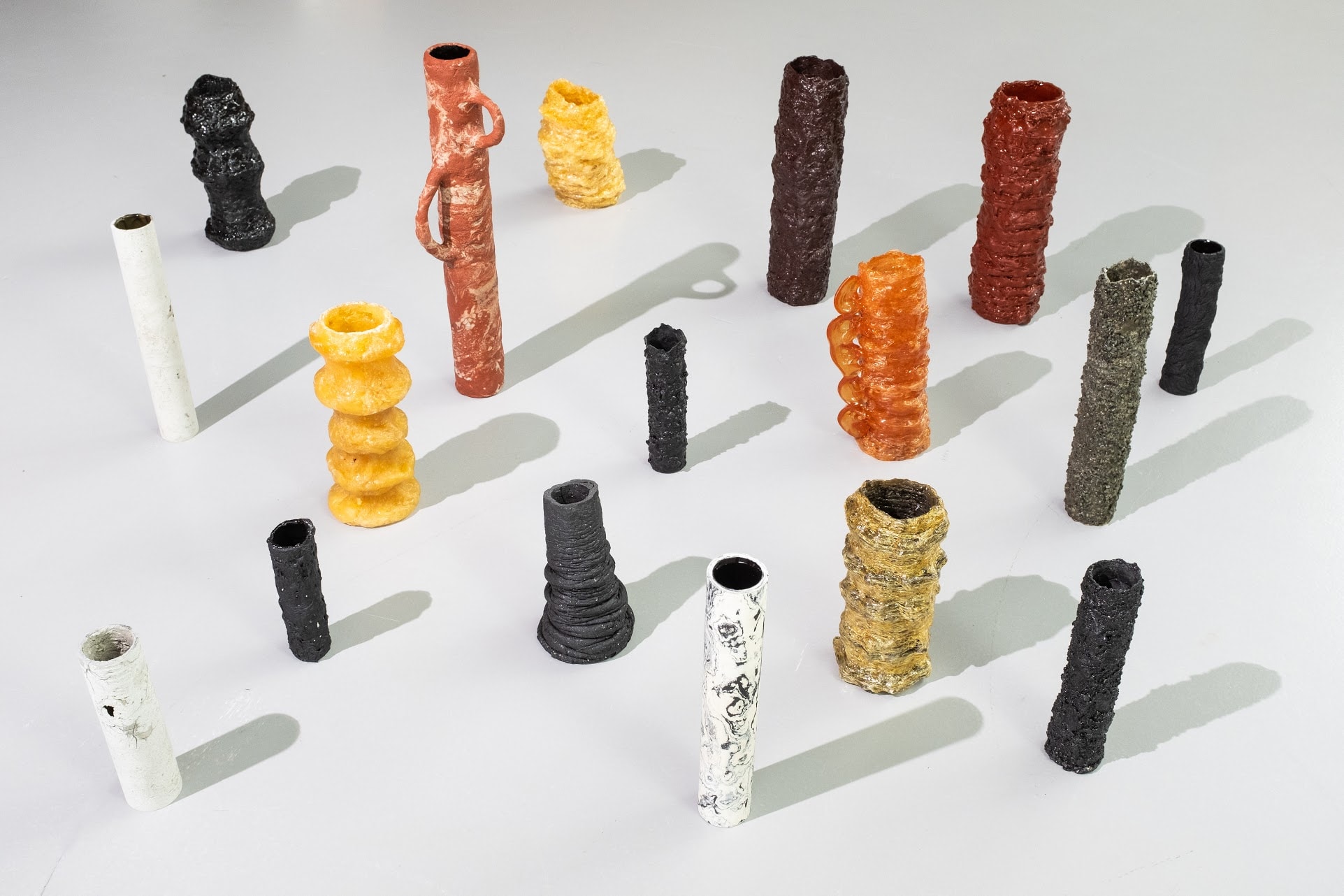
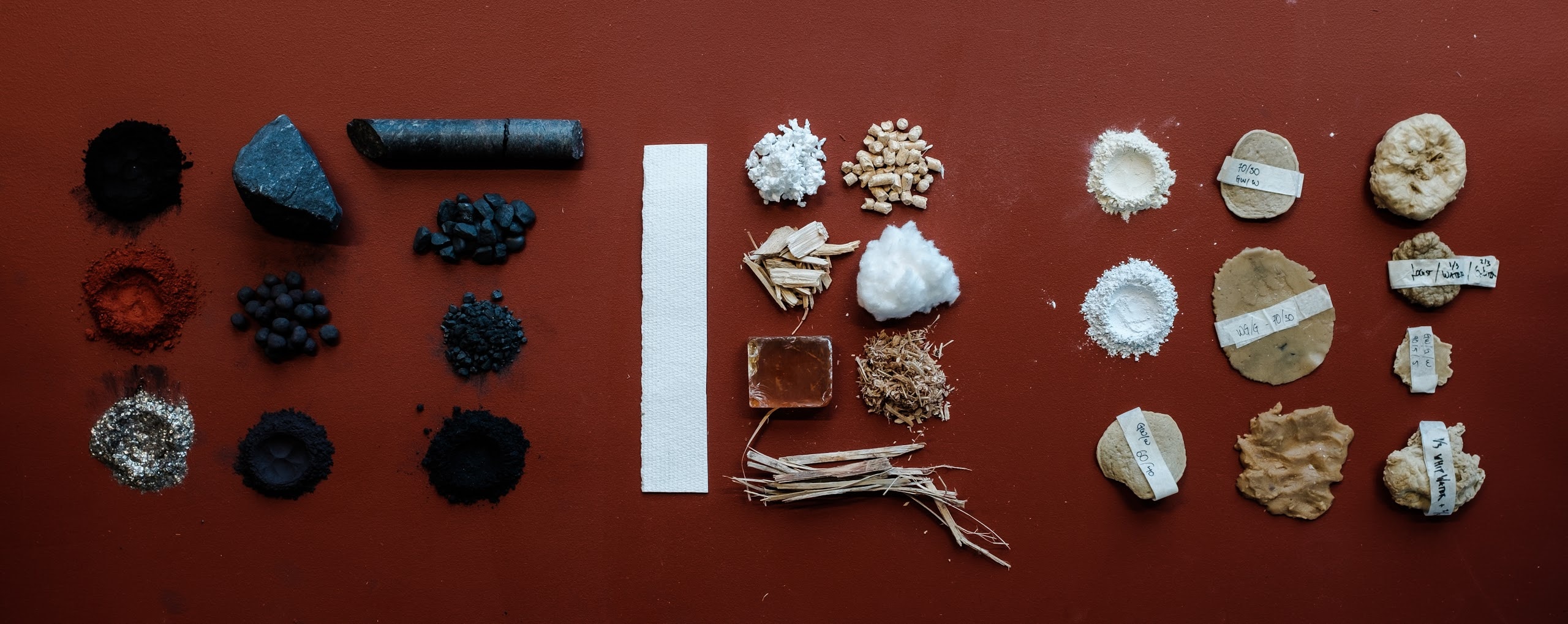
Vlisco Recycled Carpets & Adidas Stripped Down Stripes by Studio Simone Post
The winner of Young Designer at this year’s Dutch Design Awards, Simone Post works with large brands to creatively rework their products and give them a second life. Two of these projects have been for Vlisco and Adidas.
For Vlisco (a Dutch-based textile manufacturer of high-end wax-printed fabrics, mainly exported to Africa), Simone has conducted extensive material research into their leftover textiles. Using these rejected textiles, she developed a line of high quality carpets. Inspired by the side view of the large rolls used to store and transport the textiles, the fabrics are cut into thin strips and then folded and coiled into sturdy carpets. With endless possible color combinations, a unique product is created each and every time. The design shields the original printed surfaces and potential flaws, while the resulting carpets still show off Vlisco’s stunning colors with new and unexpected patterns.
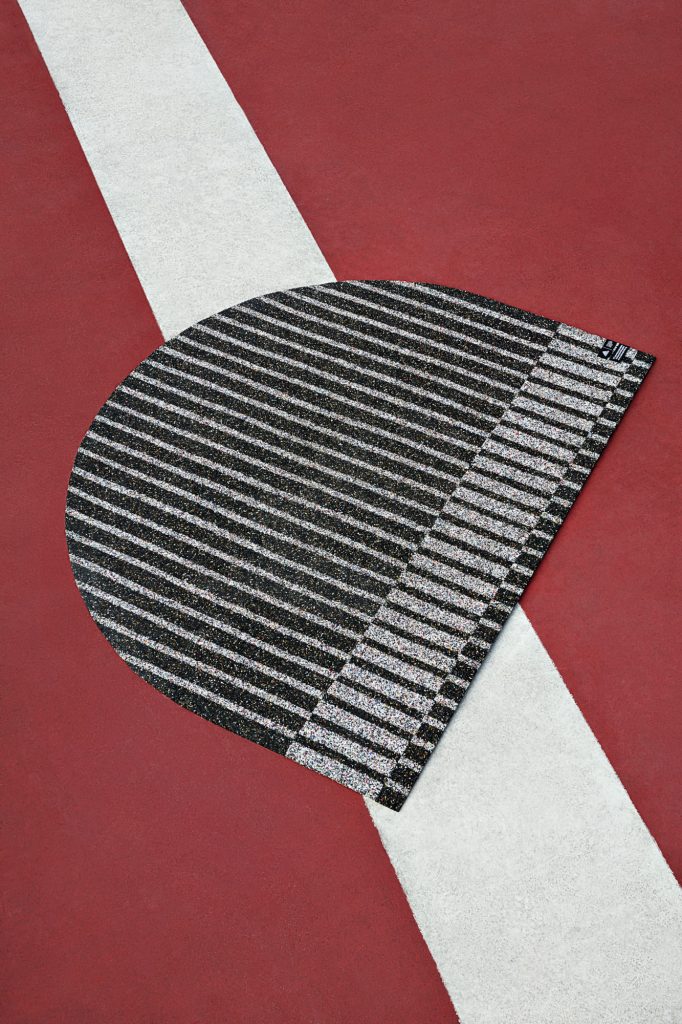
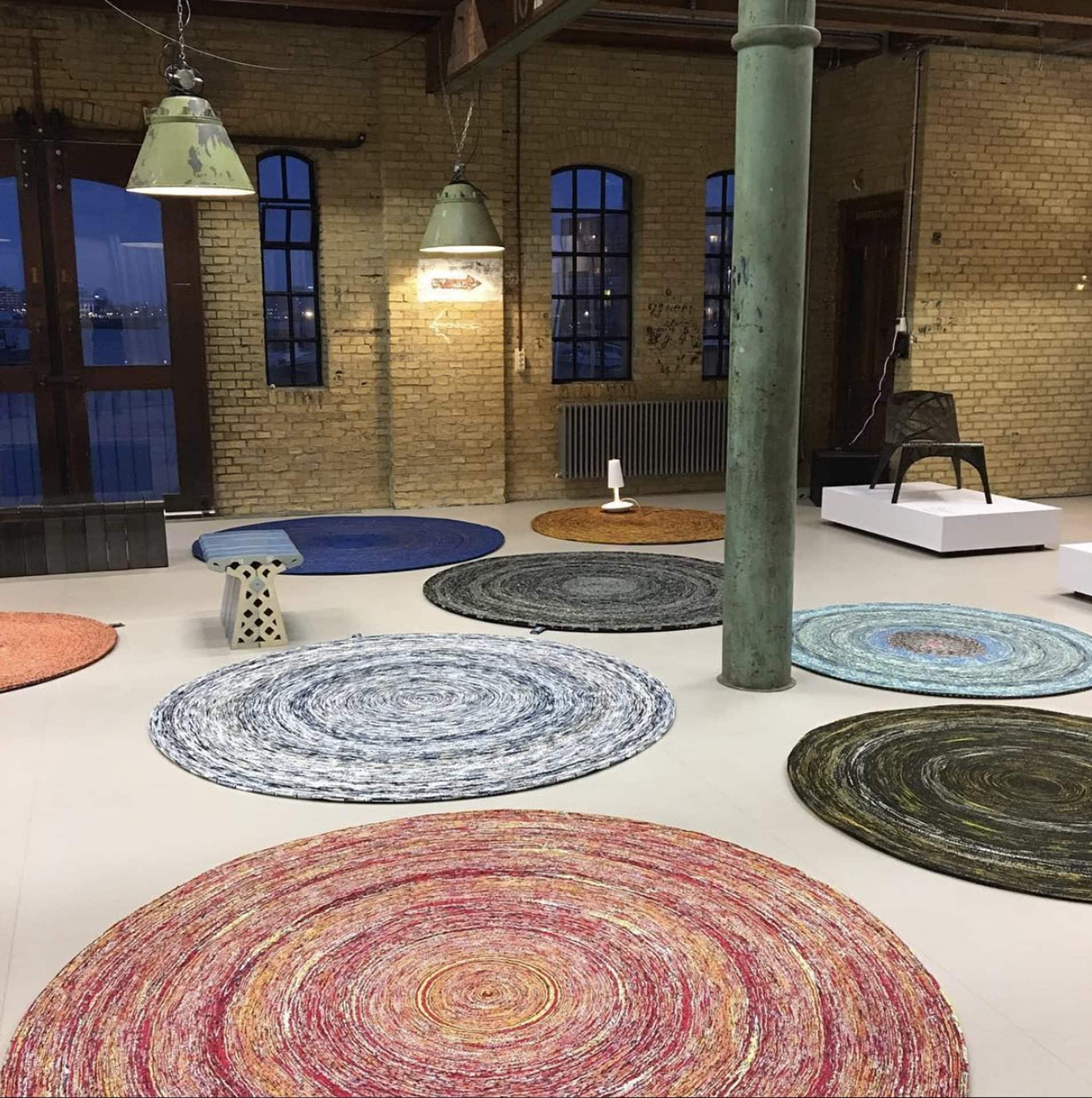
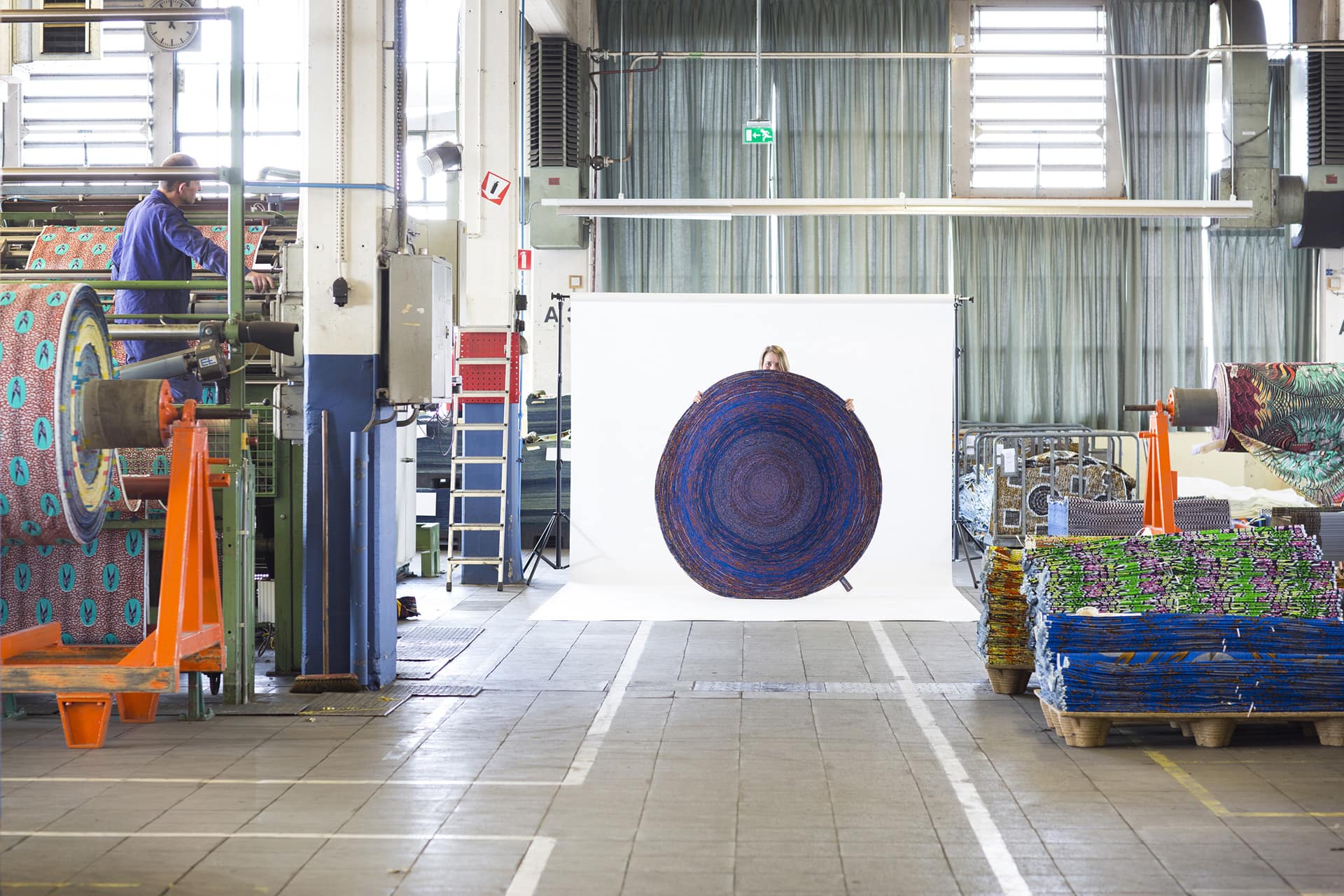
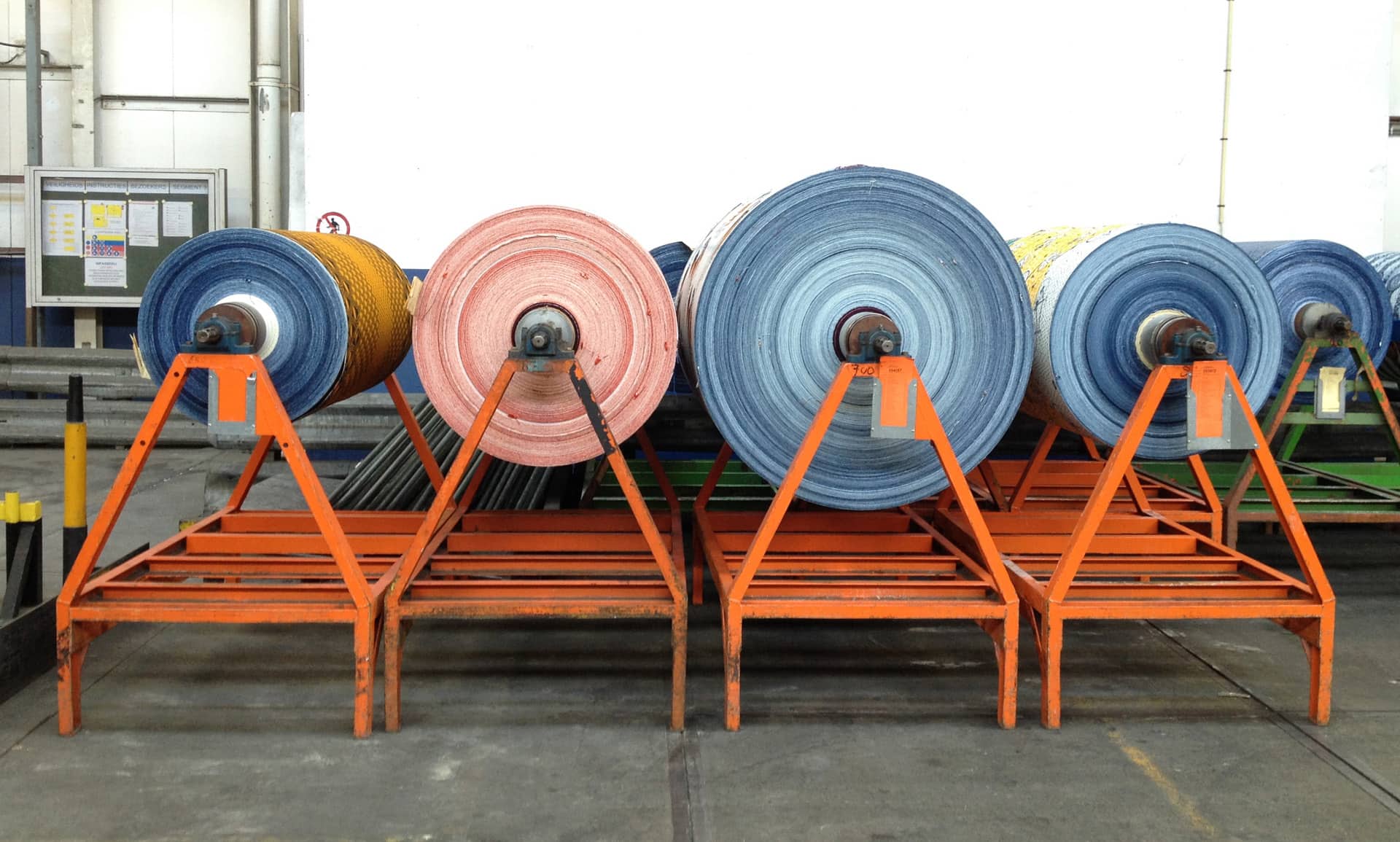
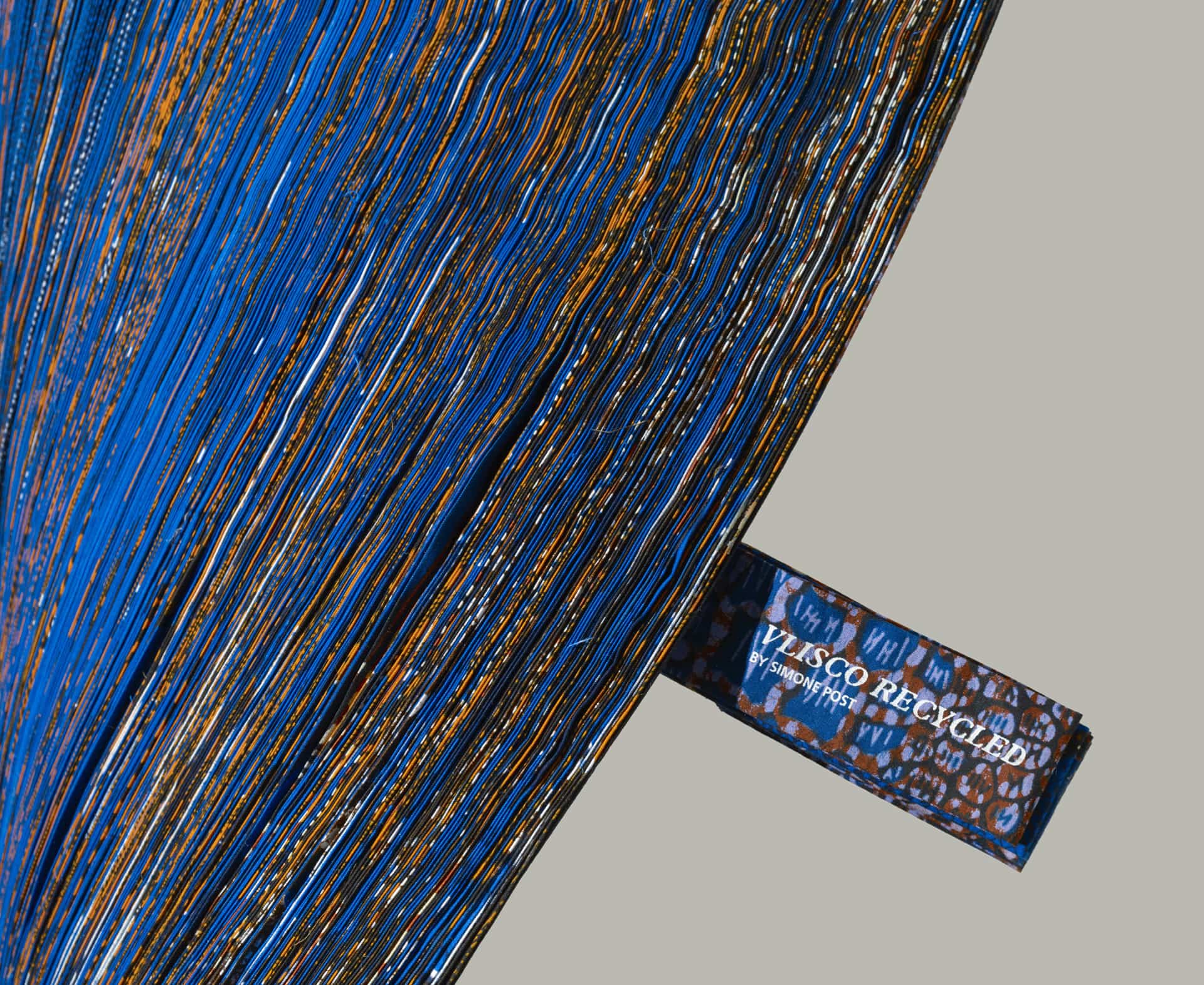
Adidas invited Simone Post to design a rug made from worn sport shoes. The German based company I:CO collects used clothes and shoes worldwide, recycling them into little rubber pallets. Simone experimented with this raw material for the Adidas rugs. On Simone’s request, I:CO divided the rubber pallets in black and white hues. She reinterpreted the distinctive stripes of the brand and turned the rugs into an attractive and fresh looking product—nothing like the old and worn shoes.
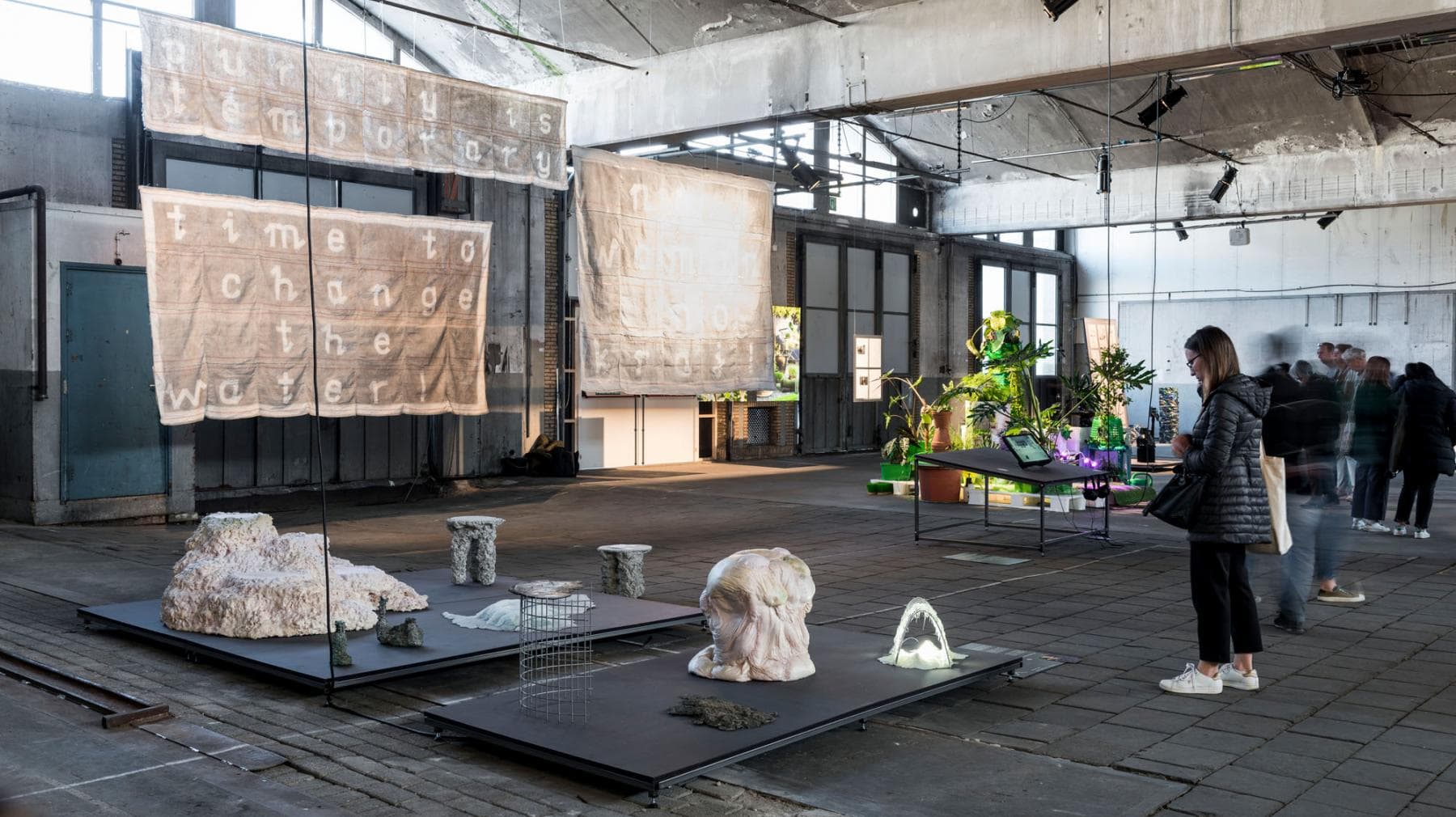