Set on the east side of the Sumida River in downtown Tokyo's industrial Mukojima sector is Bunko-ya OOZEKI, a workshop celebrating its 90th anniversary of producing their Bunkogawa fine artisan Himeji white tanned leather goods.
Leatherworking was a local craft of Banshu Himeji in the Hyogo Prefecture of Japan. The region prospered as a white tanned leather production area for many years and is still famous for their pure white leather, known as Himejigawa, to this day. During the Sengoku period, feudal lords desired the leather due to its lightweight yet strong nature, a material that worked well for armor. Over time, the craft became useful for production of small accessories ideal for everyday use.
Bunko-ya OOZEKI studio uses Himeji leather for its designs, first embossing it with elaborate motifs before hand-painting and crafting it into the final product. Join American photographer and contributor to The Kindcraft, Laura Wheatley, as she visits this respected Tokyo institution.
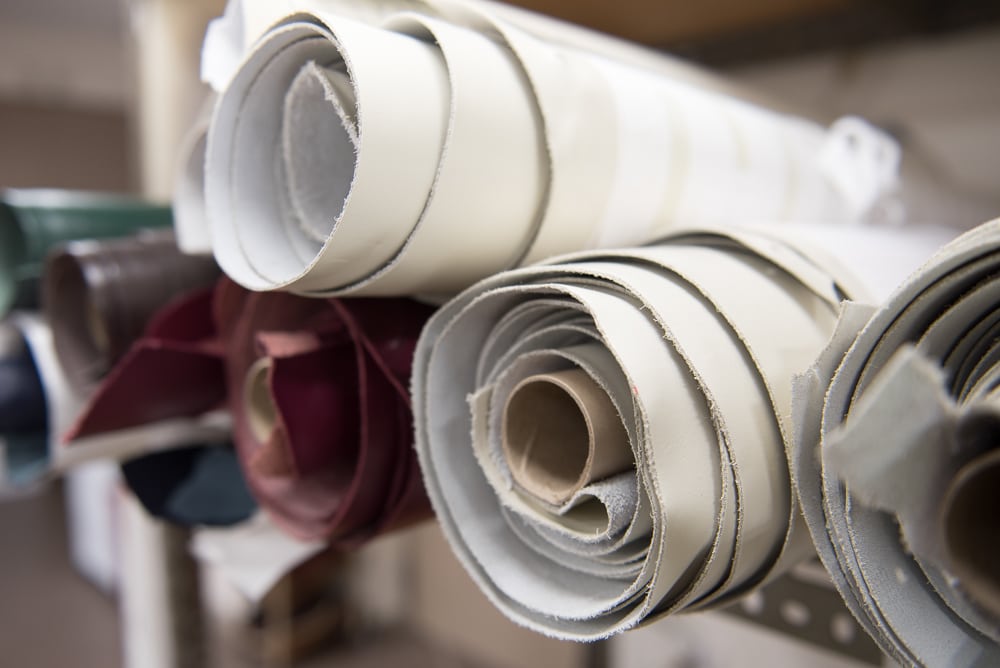
The middle of September had me navigating through the streets of Tokyo's downtown Sumida Ward, the sticky heat not quite ready to surrender to the much-awaited Autumn chill. My destination was a workshop with no signage visible to my eyes but, as I had been given step-by-step directions, I only needed to match each intersection with the corresponding photos on my cell phone.
The first generation of Bunko-ya OOZEKI was lead by Ozeki Uzaburo, who was trained in Yokohama during the early Taisho period. In 1927, he established his workshop in Mukojima, Tokyo after the Great Kanto Earthquake. Despite the disasters of this earthquake and WWII, Bunko-ya OOZEKI went on producing new patterns every year.
Ms. Risako Takahashi, whom I had previously corresponded with to arrange this visit, came to greet me warmly. Once inside the workshop, the intoxicating – slightly sweet and rich – earthy smell of leather flooded my senses.
The workroom was set up as a square surrounding a single island. Each section along the walls seemed to display an impressive heavy-duty machine, ready to be expertly controlled by an artisan's hands.
The Embossing Process
I followed behind Ms. Takahashi as she led me to the first workstation in their leathercraft process. She explained that Bunko-ya OOZEKI uses the finest white tanned leather available for their products, which they order from Himeji. They begin by taking the large rolls of leather stacked along the other side of the room and then cut the material into more manageable pieces using a special hand-controlled machine. The newly-cut material is then massaged by hand, softening the surface before making its way to the next step: Pressing.
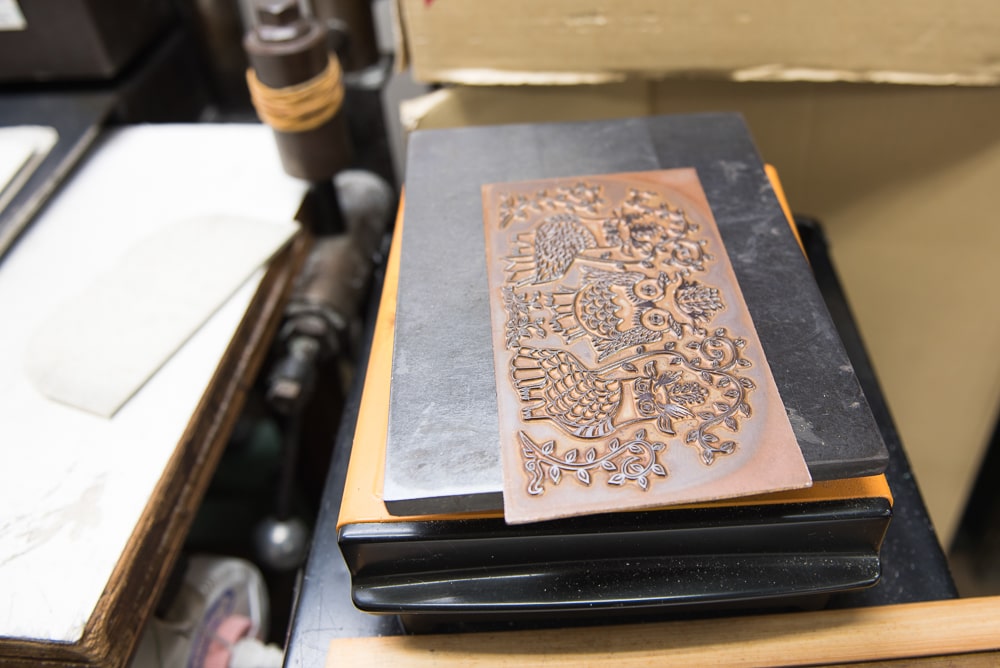
We walked to the other side of the room and we watched in silence as a bespectacled craftsman worked his magic. He focused first on pulling out a patterned copper plate from a library of thin white boxes to his left. I was amazed to realize that each of the boxes held a different pattern, extremely ornate in detail and diverse in style. Some patterns incorporated an art deco design while others resembled Egyptian hieroglyphics. Some have been there since the very beginning - there were perhaps more than one hundred of them!
With one swift and calculated motion, he held the patterned copper plate in his gloved hand up to a heating element on his right. I was told that this would aid in the embossing of the leather as heat changes the pressure level for each type of pattern. This technique puts more emphasis on the artisan knowing which patterns should have more heat applied before the hand-controlled machine presses the pattern into the leather.
The copper plate was then quickly set – pattern-side up – on top of a board and aligned with the guides before the artisan placed the leather delicately and precisely over top. Content with the placement, he slid the three-piece set into the pressing machine. With one glance towards the pressure gauge, he pulled a lever which slowly lowered the weight of the machine onto the leather and the copper plate. After he removed the embossed material, he picked it up and brought it closer to his eyes, inspecting it. When he decided that it met with his approval, he moved it gently aside and began all over again with the next leather square.
Painting the Embossed Leather
Viewing the next step of the process in action required us to take an elevator to the second level. We entered a workspace occupied by various artisans, all deeply immersed in their work. As we passed by, I caught glimpses of different designs being carefully painted, one brushstroke at a time. According to Ms. Takahashi, they are able to create thousands of different hues by mixing only eight colors in small white dishes.
Around a corner we found the head artisan of painting, Haruko Oozeki, expertly painting a truly beautiful design: A depiction of two dragons amidst clouds and what I thought resembled lightning. She allowed me to get a closer look and I was fascinated by the brilliant fuschias flashing back at me, just one of the thousands of color variants that are created in the workshop.
Adding a bit of mystery, Ms. Takahashi tells me that the next step – a "rusting" technique – is a trade secret and therefore she won't be able to show me the process. I observed that, in Japanese culture, there's a certain reverence and charm in old, delicately weathered pieces which I associate with the feeling of a vintage item.
Bunko-ya OOZEKI first paints the surface of the colored leather with a lacquer made from trees called urushi, which serves to protect the material beneath it. Using makomo plant powder, the artisans use their secret technique to apply that "gracefully aged" look that their products are known for. They are the only company in Japan who incorporates this specific method.
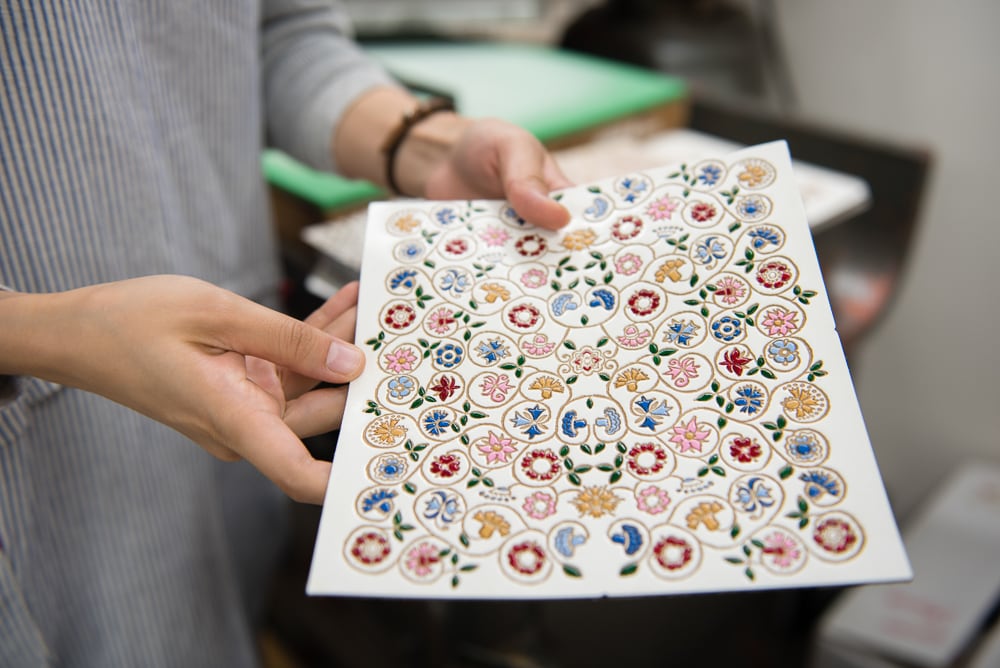
The Cutting Process
We then headed back to the first floor to see what happens next in the process. Ms. Takahashi used a machine to essentially cut the leather into an exact fit for the product it will be made into. She showed me the metal cutting mold as she set it over one of the colored leather pieces, pulling the machine directly over it. Precision is key, she says.
I asked how the final product is created from these pieces. Ms. Takahashi said that they send them off to sewing artisans who, upon completion of the products, will send them back for the final inspection. From there, most of the finished products are brought to their store in Asakusa to be put on display for interested buyers. Currently, there are over 30 types of products being made, ranging from purses and card holders to key-rings and eyeglass cases.
After thanking the artisans for showing me their craft, I was about to head out the door when I heard the bespectacled man say something in Japanese which I didn't quite understand.
Outside the workshop, Ms. Takahashi explained to me that the phrase I just heard, "Otsukare sama deshita", is usually used between co-workers to imply a mutual respect and gratitude for each others' hard work and dedication to their craft and the company. On my journey, it has become even more apparent to me that Japan is unique in the way that their acknowledgment and appreciation of the dedication and care taken in all aspects of their lives are ingrained into their language.
Fascinated, I turned to Ms. Takahashi and asked her what made her wish to learn this craft. With visible pride, she told me about the first time she saw one of Bunko-ya OOZEKI's white leather wallets. There was a feeling in her chest, she said, which made her want to be a part of that creative process. The idea that she could help to make such a beautiful thing, to have a hand in it all, was so compelling to her that she decided to join those artisans. After even just a glimpse into the enchanting world of Bunko-ya OOZEKI, I cannot help but understand that sentiment completely.
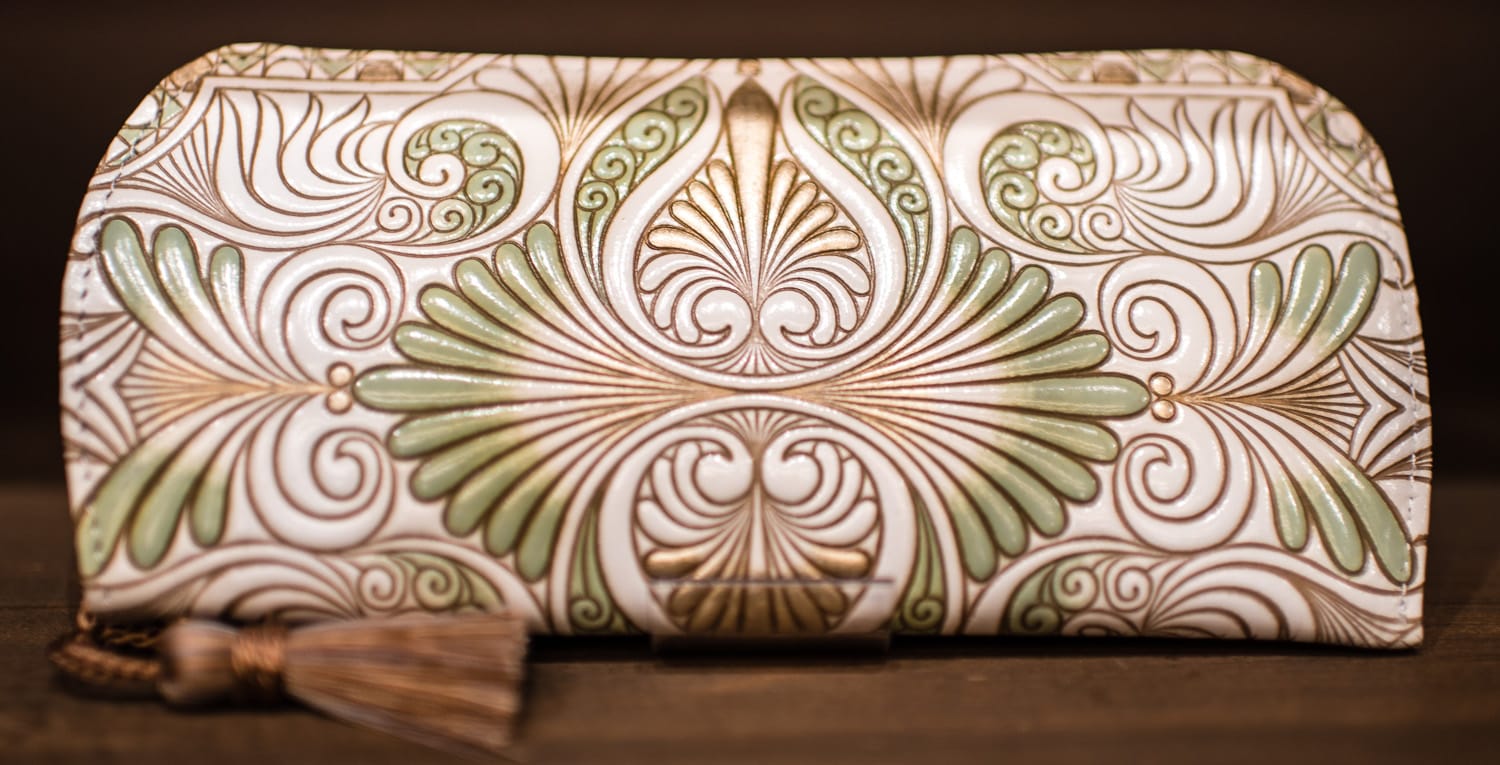